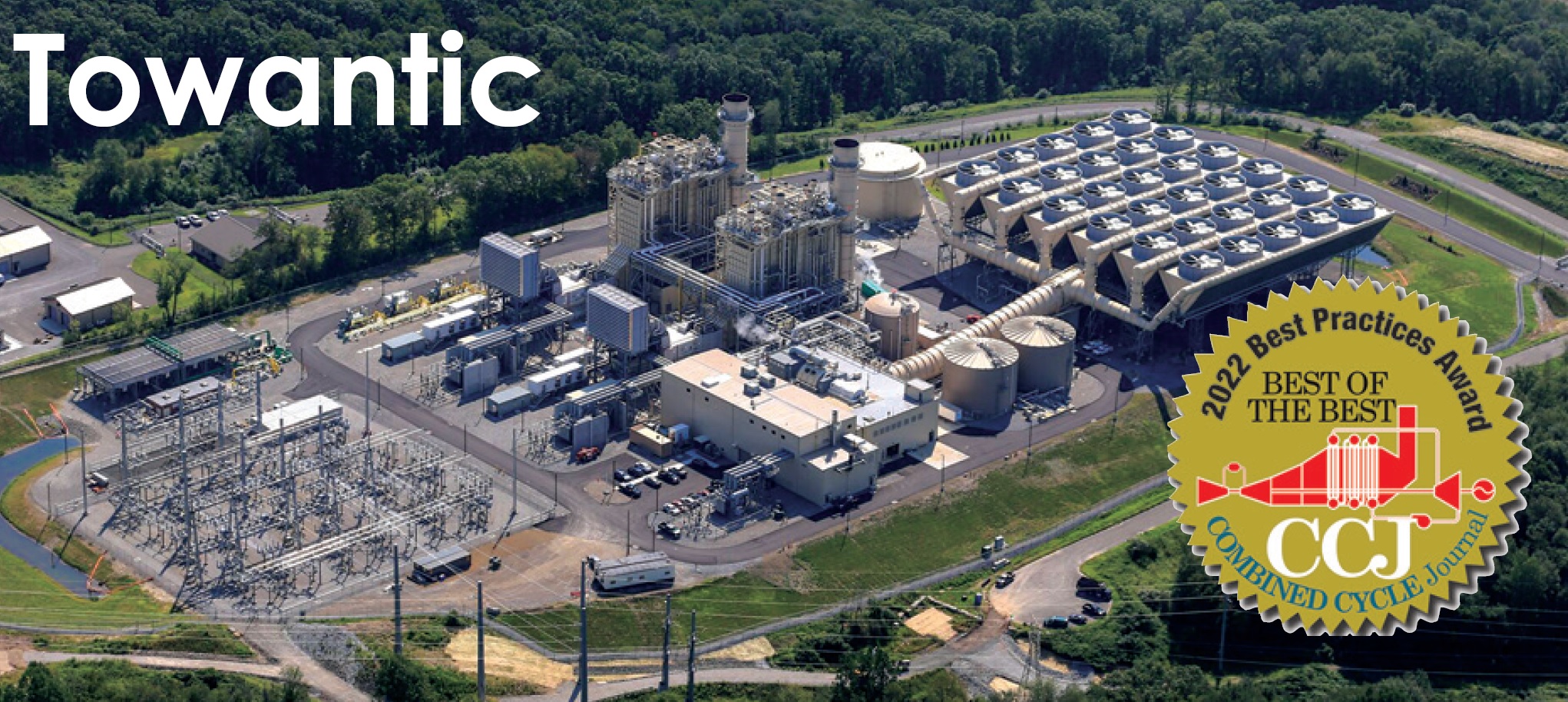
Challenge. Shortly after commissioning, CPV Towantic noticed its oil/water separator (OWS) effluent flowmeter was inaccurate, requiring the outlet valve to remain closed until the instrument could be repaired or replaced and certified.
Primary concern was that the OWS is responsible for removing oil from the wastewater stream prior to its discharge (Fig 1). To keep the plant in service and remain in compliance as a zero-liquid-discharge (ZLD) facility, staff had to figure out what to do with that water. Team Towantic thought outside the box to find a way to be an operating ZLD facility without the availability of the installed infrastructure.
Solution. All departments reviewed drawings, reached out to contractors, and compared notes, focusing plant resources on solving the problem. Management coordinated efforts and tracked progress.
From the onset, the team was committed to selecting the simplest solution with the lowest risk. The outcome that met all requirements was to install a sump pump in the OWS and run a hose from the pump discharge to the blowdown sump for the closest HRSG. It turned out to be the perfect idea, considering that the water from the OWS and the blowdown system are similar in composition and temperature.
A key benefit of this solution was about a 15,000-gal/day reduction in the amount of municipal water required by CPV Towantic. Reason: Blowdown sump water now is pumped to the service- and fire-water tank, which retains 375,000 gallons for fire protection and supplies water to the trailer-mounted demineralizers.
Result. Plant operators and mechanics had the sump pump installed, and the discharge hose safely routed to the blowdown sump, within 24 hours. The new installation worked flawlessly. All other plant parameters, such as chemistry, were unaffected. The facility has been able to run in this mode since commissioning without issue, while meeting all of its power-supply and environmental obligations.