CONTENTS
Fast start/fast ramp plants
Condenser sparger life limits
Lessons learned: construction
The complexities of flexibility
Safety: a state of mind, a way of life
Water management
Say “combined cycle” and most people affiliated with the electric-power industry think “gas turbines.” These machines produce about two-thirds of plant output (read “revenue”) and get the lion’s share of management’s attention. Steam turbines get the second-most attention—unless they fail to perform when the GTs are running well.
Several user groups managed by volunteers from plant owners and operators serve O&M personnel responsible for gas turbines—at least one organization for virtually every engine type (7F, 501F, LM6000, etc). The Steam Turbine Users Group (STUG, www.stusers.org) covers steam turbines of all makes and models.
Remainder of the equipment in a typical combined-cycle plant was served peripherally and irregularly by some of the GT user groups until the Combined Cycle Users Group (CCUG) grew “legs” under the leadership of Larry Small, director of engineering for Calpine Corp’s Engineering & Construction Dept (photo). His term ended last year.
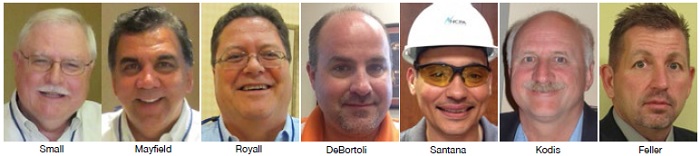
Chair for the 2014 meeting in San Antonio, August 11-13, and the 2015 conference, is Dr Robert Mayfield, plant manager, Tenaska Virginia Generating Station. PG&E’s Steve Royall is vice chair. Other members of the steering committee are listed in the sidebar. This year’s program is robust, with presentations and discussion on heat-recovery steam generators (HRSGs), NERC rules (plant perspective), fast-start/fast-ramp technology, control-system challenges, safety management, plant electric systems, batteries, transformers, plant performance improvement, workforce challenges and changing paradigms, water management, cycle chemistry, corrosion control, diagnostics and prognostics, performance monitoring, etc. For details, access www.ccusers.org.
2013 Conference highlights
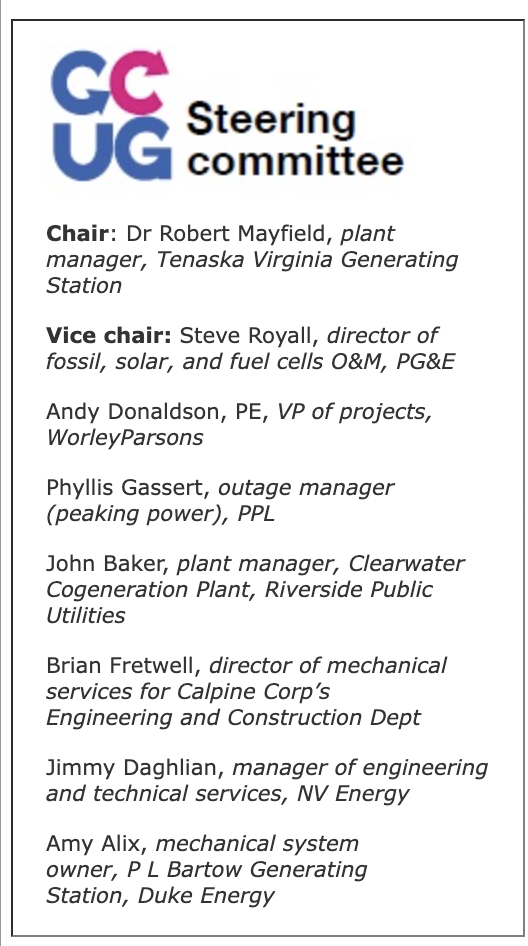
Presentations on critical issues by users and top consultants dominated the CCUG’s 2013 program. There were well over a hundred attendees, including the chairs of the world’s two largest gas-turbine users groups—the 7F’s Ed Fuselier from Direct Energy and Western Turbine’s Chuck Casey from the City of Riverside. In sum, more than 20 members (past and present) of steering committees serving the GT user community participated. The 7F Users Group contributed significantly to the meeting’s success by actively promoting the conference.
Information from some of last year’s sessions has already been published in the CCJ—including Consultant Amy Sieben’s presentation on the mid-life crisis facing many F-class HRSGs and the knowledge shared by several industry experts on generators, major electrical equipment, control systems, performance software, and diagnostic monitoring and assessment. The sidebar identifying these articles includes QR codes to simplify access to material of interest by scanning with your smartphone or tablet.
Fast-start/fast-ramp experience was chaired by Royall. This was the first time a user group had focused on the experience gained in the operation of the nation’s only fast-start (as designed) combined cycles. The dialog on the subject continues in San Antonio.
Participating from the Lodi Energy Center were Plant Manager Michael DeBortoli, PE, and O&M Manager Rafael Santana; NRG Energy Inc’s El Segundo Energy Center was represented by Senior Project Engineer Marc Kodis. Dr Gerald Feller of Siemens Energy Inc, the primary equipment supplier (gas and steam turbines, HRSGs) for both Lodi and El Segundo, was on hand to address any questions related to plant/equipment design.
What sets these new combined cycles apart from others in the fleet are HRSGs equipped with HP sections that permit operating flexibility generally considered not possible with conventional drum-type HRSGs. The ability to bring a unit into service quickly can significantly reduce fuel consumption and emissions of NOx, CO, and VOCs normally associated with startups. There are similar benefits for faster shutdowns as well.
Siemens Energy Inc is the nation’s leader in fast-start technology with Lodi and El Segundo operating in California and two more plants in Texas under construction (Panda Temple Power Project). The Oakley Generating Station under construction in California will be the first fast-start combined cycle using technology from GE Energy.
Feller’s presentation opened the session and focused on the design highlights and benefits of the Flex-Plant™ technology that underpins the Lodi and El Segundo combined cycles. DeBortoli, Santana, and Kodis summarized O&M experience at those facilities from the deck plates. Three of the points made by Feller were these:
- Flex-Plants provide an unrestricted full-ramp-rate gas-turbine start to put power on the grid as quickly as possible.
- Bottoming cycle is capable of fast start/fast ramp. For a hot start, full steam-turbine bypass can be achieved in less than an hour. The plant can load-follow with the gas turbines at maximum ramp rate.
- The OEM’s Clean-Ramp™ system holds NOx and CO emissions out the stack at permit limits while load following at full ramp rate. Feller said that for hot/warm starts, Flex-Plants reduce transient NOx emissions by 87%/91% compared to conventional plants, CO emissions by 93%/96%.
Lodi Energy Center, the nation’s first fast-start combined cycle, is a nominal 300-MW, 1 x 1, F-class unit with a rated efficiency of more than 57%. It has the Siemens designation “Flex-Plant 30” and the ability to deliver 200 MW to the grid 30 minutes after starting the gas turbine (SGT6-5000 FD3). The Lodi boiler is a Nooter/Eriksen triple-pressure HRSG with a Benson® HP section (Fig 1).
Other facts on the Lodi design include the following:
- Cycle chemistry is AVT(O) with oxygen injection, feedwater/condensate pH control is by ammonia injection, condensate polisher assures high-quality demin water. Drum inspections verified that proper cycle chemistry was being maintained.
- Condensate pumps discharge to boiler feedpumps which supply LP and IP drums and the Benson HP section.
- Kettle boilers are installed in the IP and LP circuits.
- Plant is heavily instrumented. It is said to have as many analyzers and system drains as a conventional 3 × 1 combined cycle.
Lodi began commercial operation Nov 27, 2012. Through July 2013 the unit had accumulated 163 starts, averaging 18.9 hours per start. Service factor during the first eight months was 52.8%, in lock-step with the 53.5% compiled by F-class cycling units industry-wide in 2012 as reported in Strategic Power Systems Inc’s ORAP™ database. The plant was operating or on standby 89% of the time from COD through July. Availability numbers were well above 99% for four months, with the cumulative availability since startup at 98.5%; reliability was 99.7%.
Major plant equipment generally met expectations. Relatively minor issues included falling lower acoustic baffles in the HRSG (attributed to cycling and insufficient support), a leaking weld in the lower header of the HRSG preheater, high-temperature trips across the IP exhaust during steam turbine rolls, etc. Apparently, the biggest headaches were associated with the treatment of recycled water; clarifiers were identified as problematic.
As with virtually all new plants, it takes time for a complex combined cycle to find its “groove.” Equipment and controls tuning consumes a significant number of man-hours during the first few months of operation. At Lodi, effort was expended on achieving faster GT ramp rates, reducing CO emissions, and revising steam-turbine control curves to achieve faster starts and loading.
Lodi did an especially good job of reducing CO emissions by making fuel-fraction and IGV adjustments, increasing the ramp rate, operating inlet bleed heat on startup, etc. Thanks to such enhancements, production of CO dropped by 350 lb/start.
Looking ahead, the plant plans to upgrade the gas turbine during the first Hot Gas Path inspection to ramp faster than the 13.4 MW/min now allowed.
El Segundo Energy Center, which was dedicated the week after the CCUG meeting, consists of two intermediate-duty Flex-Plant 10 power blocks with a total installed capacity of 560 MW (Fig 2). The SGT6-5000F gas turbines are designed to ramp at 30 MW/min and provide 300 MW to the grid 10 minutes after pushing the start button. The entire plant must be operating to satisfy AGC control requirements.
The single-pressure non-reheat HRSGs were supplied by NEM and are of the company’s DrumPlus™ design, which combines the advantages of drum-type and once-through HRSGs. The conventional steam drum, which would be susceptible to fatigue damage in a fast-start application, is replaced by a knock-out vessel and external separator bottles (Fig 2).
This smaller-diameter drum has a relatively thin wall to accommodate thermal stresses. Because of the reduced volumes of both steel and water, DrumPlus has the dynamic capabilities of a once-through unit; however, it has considerably more water inventory to provide a higher degree of operational flexibility. Also, DrumPlus does not require the condensate polishing system recommended for a once-through boiler.
A few aspects of plant design of interest are power augmentation capability, an attemperator capacity rated at 25% of full steam flow, and a nitrogen blanketing system that automatically releases the inert gas to the drum when pressure drops below 2 psig. Nitrogen is supplied by an onsite system.
As with Lodi, El Segundo has invested heavily in tuning. The first objective was to tune the gas turbines for fast start. This took several iterations of effort. Valves in the steam bypass system and the steam turbine also were a focal point of the overall tuning effort.
Condenser sparger life limits
The value of a presentation is not related to the length of time the speaker stands at the podium. Chairman Mayfield urges attendees to bring a few pictures illustrating a problem, describing a time-saving procedure or safety solution, etc, to CCUG meetings on a thumb drive; and when time allows, show them to the group with a few explanatory words. These informal “five-minute” descriptions sometimes segue to open-discussion threads of great interest to attendees; others simply are “alerts” or good ideas that colleagues might implement at their plants.
An example of an alert that left many attendees at the last meeting with mouths agape concerned the failure of a condenser sparger pipe at an F-class combined-cycle plant. The speaker set the stage: “Most combined cycles are designed to operate in steam bypass mode during startups to allow the steam turbine and other equipment to warm up at a controlled rate—usually with the gas turbine at part load. Many condensers are ‘designed’ or ‘rated’ for full-flow steam-turbine bypass.”
Sounds like something you want to believe, especially when full bypass is a spec requirement and your company paid for it. But, in practice, the speaker opined, “few condensers actually are capable of frequent or sustained full-steam-bypass operation for long periods at maximum gas-turbine output, without incurring damage.”
The photos he presented show a longitudinal crack in the sparger pipe (Fig 3) and a missing end cap in Fig 4 (it simply blew off). This damage occurred during pre-commissioning tests with the gas turbine at full-speed/no-load. The manufacturer reportedly said something to the effect that the steam was to heavy. More rigorous design specs might be in order.
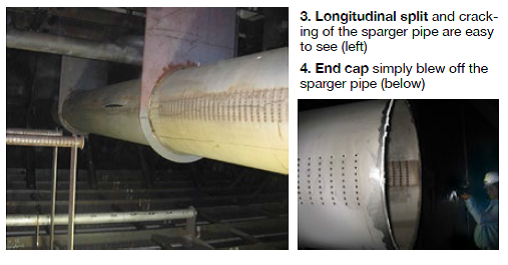
Lessons learned
A user shared lessons learned on recent plant construction projects—always a topic of great interest and one that fuels meaningful discussion. The following are some of the points made by the presenter:
TA cost overruns can eat your lunch. OEM estimates of manpower and hours for commissioning and startup were obtained at the beginning of the combined-cycle project. However, actual time spent by technical advisors, who were paid on a time-and-materials basis, was much more than the budgeted amount. Sorting through records and properly allocating expenses was challenging, significant time having been expended by TAs on OEM-specific issues—such as new product introductions and control software revisions—and on tasks adversely impacted by EPC delays.
The cost overruns were not trivial. Example: One OEM quoted an expectation of 363 field-engineer man-weeks for installation and startup of its equipment. The actual figure submitted was 568 man-weeks, amounting to an additional cost of more than $3 million. That there were arguments over who was responsible for unbudgeted amount (OEM or plant owner) is not surprising. Tighter cost control during project execution was one recommendation from attendees.
Fuel-gas heater: Intended versus actual service. A generating unit’s dewpoint heater was designed to maintain more than 50 deg F of gas superheat, as specified by the gas-turbine OEM. But the ultimate function of the heater became one of maintaining fine control of gas temperature to hold the Wobbe Index value within a narrow band. A single, very large dewpoint heater was not suitable for this purpose across the full gas flow range.
Increasing the percentage of glycol in fuel-gas heater isn’t a casual decision. A manufacturer of fuel-gas heaters pushed the design/capability of its units by increasing the glycol concentration to more than 90%, solely to obtain a higher bath boiling-point temperature. Lesson learned: 50,000 gal of propylene glycol is very expensive.
What’s the best contractual arrangement with an EPC? Fixed-price EPC contracts require more upfront detailed scope definition and engineering work compared to cost-plus contracts. But they have the advantage of keeping the EPC’s “skin in the game,” the speaker said, and with bonus and penalty provisions, a fixed-price arrangement creates the incentive to minimize cost and schedule overruns. The challenge for the owner is to get the EPC to have the end user’s commitment to cost and schedule.
Paint all carbon-steel pipe for corrosion protection, including those sections that will be covered by insulation.
Have a no-smoking policy for the entire site throughout construction. Enforcing no-smoking restrictions after gas is introduced is much more difficult if workers are already used to smoking in certain areas.
Equip boiler feedpumps with fluid couplings or variable-speed drives. Such pumps may be less prone to upsets than fixed-speed units with variable bypass arrangements. Some users have reported significant problems with fixed-speed pumps during transients and flow upsets—including unit trips.
Specify anti-rotation devices on large circulating-water pumps and their motor drivers to prevent the second pump from spinning in the reverse direction when the first is operating.
Insulation spec should distinguish required insulation by system and process temperature. Avoid specifying by insulation effectiveness alone—for example, calcium silicate versus mineral wool for high temperatures. Reason: The combined weight of piping and insulation impact pipe-hanger and structural design.
Provide an 8-in. drain with valve and blank flange at the bottom of all large tanks. This is not a standard tank design feature, but it facilitates draining the tank’s contents if necessary.
Design instrument- and process-air piping systems in sections equipped with isolation valves. This allows O&M personnel to remove individual components from service without taking down the entire system or plant.
Piping design considerations for onsite gas delivery systems. Piping for every redundant fuel-gas system component that might require removal from service should be designed with double-block-and-bleed, vent, and nitrogen purge capability. Consider these features for non-redundant items as well, to avoid having to vent and purge large volumes of gas when only one gas component must be worked on.
Alarm prioritization should be part of the original DCS design, not an afterthought.
Add a “NERC compliance” section to EPS specs. Ensure that the EPC and its plant design comply with the ever-increasing volume of NERC and CIP requirements. This includes timely supply of electrical protective relay settings and other NERC-related documentation. Also, work associated with critical NERC systems—such as battery maintenance—must be done and formally documented as soon as each system is put in service. This may be well before the plant is commissioned.
CCJ articles based on content from CCUG 2013
Control systems
Fleet-wide M&D puts ‘Big Data’ into practice
Heat-recovery steam generators
Prioritization of issues improves reliability, performance
Generators and transformers
Problems experienced with modern generators
Generator inspection first step in avoiding failures attributed
to dry stator-winding ties
Fleet-wide transformer monitoring program reduces losses
Stator connection ring vibration KOs H2-cooled generator
The complexities of flexibility
The utility that owns this plant first installed a diverter damper on a combined cycle to allow for commercial operation in simple cycle while work continued on the Rankine portion of the facility. But the operational advantages experienced convinced the owner to make diverter dampers a standard feature on all of its new combined cycles.CCUG takes an integrated approach to the design, operation, and maintenance of simple- and combined-cycle plants, setting it apart from the traditional user organizations serving gas-turbine owner/operators, which focus on a specific piece of equipment. A short presentation and open discussion concerning the idiosyncrasies of operating a dual-fuel combined cycle also permitted for simple-cycle service illustrates the point.
The damper arrangement is as follows: Between the gas-turbine exhaust outlet and HRSG inlet there’s a flap type damper on the GT side which is included in the engine scope and a downstream guillotine backup which is part of the HRSG scope. These are open when operating in the combined-cycle (CC) mode, closed for simple-cycle (SC) service. A damper in the GT bypass stack is closed for CC operation, open for SC.
A careful review of local/regional emissions standards obviously is required before deciding if a plant capable of both combined- and simple-cycle operation has economic benefit at a given location. SC emissions might be a sticking point, the speaker said, and a deal-breaker.
Review of requirements for the continuous emissions monitoring system (CEMS) is a good place to begin your evaluation. Most air permits in the US require CEMS on each exhaust stack, the speaker noted. So a unit train with separate GT and HRSG stacks requires two sets of CEMS. Listening to the presentation, your initial thought is “that doesn’t seem difficult to deal with.” But it’s never quite that simple. Consider, for example, that air permits generally are written with separate limits on emissions and operating time in the simple-cycle mode and, if dual fuel, also on the secondary fuel.
For transitions between combined- and simple-cycle operation, the user continued, the air permit usually will define each operating mode for CEMS data-logging and emissions reporting purposes. The position of the diverter damper, as indicated by a limit-switch signal, sometimes is used for this purpose. This prevents the need to report simultaneous emissions from both stacks, which might occur if there is zero error on one CEMS system or if there is damper leakage during unit operation.
As the speaker dug into the details, it became apparent that project viability likely hinged on SC emissions requirements. CC NOx emissions wouldn’t be a problem because SCR catalyst is integrated into the HRSG. But that same catalyst is not suitable for use in the SC train because of the high exhaust temperature—up to about 1200F or several hundred degrees hotter than the limit recommended by the catalyst manufacturer. Dilution air is an option for reducing gas temperature, but capital and operating costs probably would make it impractical. The speaker noted that the capital cost of a dilution-air system can be as much as 50% of the cost of the GT.
Another wrinkle: Recent GT design improvements have focused on increasing output and/or efficiency, both dictating higher firing temperatures conducive to increased NOx production. This is not a concern for CCs because more catalyst in the SCR can solve the problem. One way to reduce SC emissions without installing an SCR, the speaker said, is to dial back the firing temperature, which also decreases output somewhat. However, this may be a viable emissions-reduction option in ozone attainment areas.
Operations-related considerations for SC-capable CCs include purge requirements. These may not be as well defined as you might like. The speaker said that for simple-cycle operation, only the SC exhaust system is purged and the damper remains in the bypass position from startup to shutdown. Similarly for CC-only operation, the HRSG and ductwork are purged through the stack to atmosphere and dampers remain in the CC position from startup to shutdown.
Simple enough. However, NFPA 85 says the following in Section 8.9.2.1: “A purge of both the HRSG enclosure and the bypass system shall be completed prior to the admission of combustion turbine exhaust gas into the HRSG.” This is open to interpretation, the speaker indicated, and can be taken to mean that separate purges of the SC exhaust system, and the HRSG and associated ductwork, must be completed prior to any unit operation in which a transition may be made from CC to SC.
The GT OEM takes this as its official position and refuses to control diverter dampers in a manner that would allow a transfer from CC to SC “on the fly” unless separate purges of SC and CC had been performed prior to unit operation—that is, either during startup or from the previous shutdown if purge credit conditions have been met.
A dual-fuel gas turbine further complicates the purging requirements of a diverter-damper arrangement. Reason: the autoignition temperature of distillate fuel is about 410F, or more than 600 deg F lower than that for natural gas. To meet the requirements of NFPA 85, purge air must be at least 100 deg F below the lowest autoignition temperature of either fuel.
This means that to satisfy HRSG purge requirements during operation, diverter-damper transitions usually can be make only from CC to SC mode, not the opposite. More specifically, for CC operation the unit must be started with the damper in the CC position; it cannot be started in the SC mode and transferred to CC with flame in the gas turbine unless all the conditions for purge credit have already been met from the previous shutdown.
Safety: a state of mind, a way of life
How safe is “safe”? Is any work process or personal pursuit ever safe enough? Can “safe” be characterized accurately with numbers? If so, would the number defining “safe” be the same for a mining operation as for an office environment? Why would someone ride to a “safe” workplace on a motorcycle without a helmet, or drive home after having a few beers? Obviously, nothing is or can be 100% safe, but the elimination of controllable accidents in the workplace and home is a big step in the right direction.
Chairman Mayfield is an effervescent champion of safety. He and others on the Tenaska Virginia management team believe you have to elevate the importance of safety in people’s minds to get the desired results. Succinctly, safety must be woven into the fabric of their thinking; it’s not something that can be achieved with slogans and banners, nor is it something you can turn on and off at will.
Achieving VPP Star status is critical to this goal, the Tenaska Virginia team told the editors. The dedicated participation by all employees is necessary to nurture the safety culture required for ongoing success; you don’t want safety to “stop” when management is offsite. Tenaska Virginia received its VPP Star certification in 2009 and it remains the only generating facility powered by gas turbines in Virginia to earn this recognition. In sum, there are only 53 VPP star sites in the state. Nationally, there are but 2300 VPP Star sites among 7.2-million workplace locations.
VPP Star is not a goal, Mayfield stressed, but rather a result of changing everyone’s attitude towards the way safety is handled on a day-to-day basis. It is managed by the employees and supported by management.
VPP Star status must be recertified triennially. Last year, Tenaska Virginia successfully completed its first recertification. Plant personnel regularly share their knowledge on how to develop a safety culture in the workplace with other Virginia businesses and they coach those organizations and other Tenaska plants on preparing for VPP Star inspection and evaluation.
In Virginia, the state’s Dept of Labor and Industry is responsible for administering and enforcing occupational safety and health activities as required by OSHA. Last year, Commissioner Courtney Malveaux visited the plant to thank the staff for being a role model for others. He recognized Tenaska Virginia as one of the safest businesses in the state and discussed the following, among other topics, with plant management:
- Audits by special government employees (SGEs) for businesses that request safety help.
- Fines for OSHA violations and for businesses that are less than truthful in safety reporting.
- The value of SGEs.
- Safety culture and benchmarking.
- OSHA’s willingness to help and the good relationship the plant has with that agency.
VPP Star is the cornerstone of Tenaska Virginia’s robust and highly integrated safety program. Mayfield points to the respect the plant has among contractors because of its safety status. “It sets the tone,” the plant manager says. Contractors think differently when they come to Tenaska Virginia, he continued. Having been the plant manager before VPP Star, Mayfield should know. Plus the recognition motivates plant personnel. It’s not about awards, he says, it’s about the respect they get from the peers for being part of an elite team.
Components of the plant’s safety program include the following:
- Basic safety training which typically requires refresher training on an annual basis. This includes subjects such as lockout/tagout, hearing conservation, confined space entry, first aid, CPR, electrical safety, hazardous chemicals/MSDS, fire protection systems, communications/security, fall protection, personal protective equipment, scaffolding, etc.
- Monthly safety meetings, two hours including breakfast, cover topics the management team thinks plant personnel should have refreshers on. Brief lectures by plant subject-matter experts or outside sources are followed by Q&A/discussion to share experiences, and a hands-on demonstration where appropriate.
- Job hazard analysis identifies specialized safety training required for personnel handling high-risk tasks—such as maintenance of high-voltage equipment in the switchyard. Ergonomics is a consideration in every JHA.
- Unannounced drills are a fundamental part of the plant’s safety awareness program. These exercises rely on realistic props—such as full-body-weight dummies for confined-space rescue. You react the way you are trained, Mayfield says. If the drills are not conducted to management’s expectations, the applicable training modules are modified and practiced thoroughly.
- Contractors and visitors undergo training at virtually all generating stations before they are allowed in the plant. Use of hard hats, hearing and eye protection, waste receptacles, location of showers, and where to muster in an emergency are all part of the normal training regimen. At Tenaska Virginia, any contractor employee who fails to get a perfect score on the written exam must be retrained before retaking the exam. The plant also has specific rules regarding cleanliness, appropriate clothing, and safety for contractors. Work can be stopped at any time for violations. The penalty for use of drugs or alcohol is immediate dismissal.
- Safe work ideas, including protection of personnel and equipment during severe weather events, are communicated during monthly safety meetings and via the quarterly newsletter published by the safety committee, staffed primarily by hourly employees. Mayfield said safety is driven from the bottom up, with management’s role primarily one of review, evaluation, validation, and authorization.
Water management
The CCUG is perhaps the only organization serving gas-turbine owner/operators that covers water treatment for the entire plant—that is, steam/water chemistry, cooling water, makeup and demineralization systems, and wastewater. Other groups with an interest in water, such as the Australasian HRSG and the Air-Cooled Condenser Users, focus on cycle chemistry. Dan Sampson, a highly regarded senior technical consultant for WorleyParsons with more than two decades of experience in powerplant water treatment, conducted a clinic on the subject last year.
Drum internal chemistry, the use of phosphate in particular, was one of Sampson’s first talking points. He said that the only purpose of phosphate feed is to control drum pH, which drops only if contaminants are present. You may be able to stop phosphate feed, the expert continued, if your plant has no history of condenser tube leaks or demineralizer upsets and/or it is an air-cooled plant and equipped with condensate polishers.
However, your decision for or against phosphate should be based on a careful analysis of historical data conducted by a qualified chemist. Caution: Drum pH will drop like a rock if contamination occurs without phosphate.
Drum blowdown was the next topic. The required blowdown rate, Sampson said, depends on the concentration of iron and corrosive ions (chloride/sulfate) in the drum. He suggested measuring iron in the cycle directly, using a suspended iron test, or indirectly, with a particle or turbidity analyzer. Sampson added: “Monitor corrosive ion concentration indirectly (cation conductivity) and adjust blowdown to keep both iron and cation conductivity within limits.”
Amines. The jury is still out on the use of amines, the speaker said; EPRI guidelines don’t endorse their use. However, addition of an amine with a low volatility at the pressure of concern may provide benefit: It will hang along the tube wall to protect against loss of oxygen and ammonia from that space. Absent amine, oxygen and ammonia can migrate into the bulk water, leaving the tube-wall area unprotected. Amine volatilizes later, but after protecting the tube wall.
Bear in mind that amine blends are known to increase cation conductivity and possibly mask more corrosive anions. Their use is influenced by the severity of two-phase flow-accelerated corrosion (FAC) and turbine corrosion. Monitoring of iron transport is highly recommended before introducing amine blends.
Sample panels. As a trouble-shooter, Sampson needs quality information on system chemistry to figure out what caused an upset, what happened during the upset, and what must be done to return the plant to normal operation. So he can get prickly when sample panels are the discussion topic.
Case in point: In introducing the subject, the forensic scientist reminded attendees that the sample panel is their first line of defense, adding “So why don’t you maintain it.” Continuing, he said, CEMS will shut you down now, when stack data are off-spec. By contrast, the sample panel identifies upsets later rather than sooner and will force you out of service longer, but not now.
Sampson understands better than most in the industry the challenges of running a major powerplant with a small staff and no chemistry professional onsite. So he recommended that plants consider seriously the hiring of a contractor to maintain their sample panels. “The driver for the maintenance contract is accuracy, not saving money,” he stressed, “but you should save over time.” An experienced contractor will do the work required in less time than the average plant employee assigned the tasks.
The alternative to a contractor likely will be an under-performing panel and increased wet-test frequency, which translates to higher risk. Sampson recommended that calibrations be checked weekly and that wet-test results be compared to data provided by sample analyzers and trended over time. Statistical analysis will show the deviation between the two and when the analyzer must be recalibrated, fixed, or replaced. Finally, he suggested making sample-panel maintenance a line item on the corporate scorecard.
CCUG sponsors, 2014
The impact of rapid cycling on the condensate/feedwater system was raised as a discussion point. Cycling ages equipment more rapidly than base-load operation, but all-volatile treatment (AVT) eases the chemistry burden, Sampson said. Two suggestions: Add iron traps—especially if air-cooled condensers are installed—and maintain pH high in the target range. A rock-solid corrosion-product transport monitoring program is vital to success.
To provide some perspective for the non-chemists in the room (everyone), Sampson said that each thermal, chemical, or hydraulic shock liberates corrosion products, and that a wide swing in oxygen content during startup or after shutdown causes considerable damage. One startup, he noted, releases about the equivalent amount of iron as 1000 hours of steady-state operation.
To keep air (oxygen) out of the steam system, it is important to inject nitrogen into the steam drum as pressure decreases. This should be done automatically. Sampson reminded that nitrogen is lighter than air, so if the latter gets in the system, nitrogen will not push it out.
Discussion of cooling-water treatment mentioned chlorine dioxide as a preferred oxidizing biocide and provided guidelines on the use of recycled water in the plant. “Chlorine dioxide is an awesome biocide,” Sampson said. It is more efficient than liquid bleach and works well over a wide pH range (bleach does not) and in high ammonia waters characteristic of recycle operations. Chlorine dioxide usually is produced in batches onsite; its volatile nature requires that it be used the same day. Pay close attention to vent location: The telltale green gas can be a public turnoff. Stabilized bromine is a good biocide as well.
There’s increasing pressure to use recycled water at powerplants. It’s acceptable for cooling-tower makeup, Sampson said, but cautioned against its use as a feedstock for demineralized water production. Recycled-water projects are not simple, he stressed; they require an engineered systems approach. Typical limiting constituents include chloride, ammonia, and phosphate, and they may impact project feasibility. One of the big unknowns is water quality over time. There are no guarantees on this and wide variations in quality are possible. Careful analysis and flexible system design are important. Sampson recommended the following project plan:
1. Development and investigation.
- Gather water-quality data from primary and alternative sources.
- Identify potential constituents of concern for cooling tower (CT) and for discharge offsite.
- Calculate wet-bulb and dry-bulb temperatures, and relative humidity, during summer peaks; collect monthly pan evaporation and rainfall data.
- Run a heat balance to determine CT evaporation rates at summer peak and annual average conditions.
- Identify regulatory chemistry limits and liquid volume discharge limits.
2. Initial modeling.
- Use computer models to optimize pretreatment design consistent with CT manufacturer chemistry limits.
- Use computer models to optimize post-treatment design consistent with effluent chemistry limits for discharge offsite.
- Develop a water balance using selected water-treatment components based on primary water source.
- Perform initial cost estimate for water treatment system using the primary water source as the basis.
3. Alternative modeling and optimization.
- Use computer models to optimize pre- and post-treatment systems using alternative water source and discharge limits.
- Develop a water balance using water-treatment components based on the alternative water source.
- Perform an initial cost estimate for the water treatment system using the alternative water source as the basis.
- Perform similar calculations for a heat-rejection system equipped with an air-cooled condenser, if required for comparison purposes.
- Compare capital and O&M costs for all alternatives.
4. Permitting and pilot testing.
- Review with company’s environmental group to determine hazardous-waste characteristics.
- Review permit to ensure waste stream is within discharge limits. If not, change the discharge permit or modify site design and disposal options.
- Perform pilot tests or studies if necessary.
5. Final design.
- Write/review application for certification, if needed.
- Finalize design, heat and water balances, permits, and design drawings.
- Develop equipment specs, issue RFP, evaluate proposals, and select vendors.
- On the subject of makeup water and demineralization systems, Sampson told that group that the latest electrodeionization (EDI) systems are reliable and as good as mixed-bed demin units. Plus, they eliminate all the chemicals required by the latter. Regarding power requirements, EDI and mixed beds (pumps) are about equal.
He regards reverse osmosis/EDI as the “go-to” design for demin water today in terms of cost, modularity, product quality, etc. The typical EDI stack should last between five and seven years, Sampson said. This compares favorably with the need to replace about 10% of the resin annually in mixed-bed units, plus the expense associated with resin handling and disposal.
A user challenged Sampson, saying EDI performance degrades when water is cold because its viscosity increases. At his plant in Wisconsin, it was necessary to add a mixed bed as a wintertime booster. The consultant agreed, adding that he recommends preheating water when its temperature drops below 60F. One way to do this might be to extract heat from at the stack area. CCJ