Don’t forget to inspect your valves
It’s easy to leave valves off your outage checklist. There are so many things that must be done and time is limited. Work generated by a seemingly endless stream of advisories from the gas and steam turbine OEMs, generator manufacturers, and regulatory agencies typically gets top priority.
Inspection of main steam stop (MSS) valves, hidden from direct view under a bundle of insulation, is easy to defer. All they do is open and close, no wear and tear from throttling, nothing much to worry about. Don’t be so sure.It’s ironic that there was no time for Ed Sundheim’s presentation on MSS repairs at CTOTF’s Spring Turbine Forum in mid April because sessions were filled with center-stage material on gas turbines. Gas turbines are more important and of greater interest to users than valves, of course. Until there’s a problem.
What Sundheim, the director of engineering services for North American Energy Alliance LLC, Iselin, NJ, was planning to tell the CTOTF members based on his recent experience at NAEA’s Newington Energy LLC: Be proactive regarding inspections of your high-energy valves.
Newington is a 2 × 1 7FA-powered combined cycle engineered and built by Duke-Fluor Daniel with Foster-Wheeler Energy Corp heat-recovery steam generators (HRSGs). The intermediate-duty plant in Newington, NH, began commercial operation in 2003. Original owner was Con Edison Development Inc, which sold off its conventional assets in 2008.
Newington’s MSS valves were inspected during a gas-turbine major in fall 2009 and found to have badly damaged gates and seats, and cracks in the valve bodies as well. Both HRSGs have 16-in. Atwood & Morrill Co (Salem, Mass) parallel-slide gate valves with F91 bodies (Fig 1). A&M is a wholly owned subsidiary of UK-based Weir Group PLC. The valves were manufactured in the UK by another Weir subsidiary, Hopkinson Ltd.
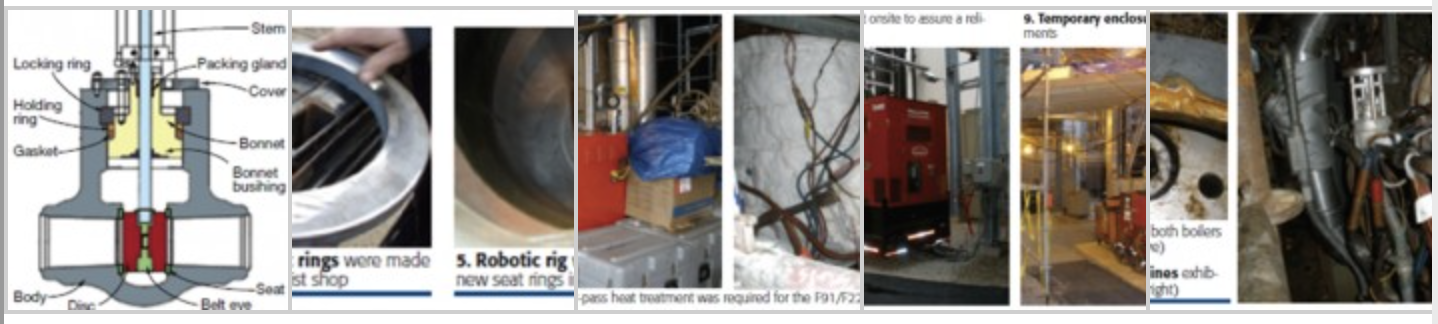
The initial damage assessment was fracturing of the Stellite faces on the gates. Closer inspection revealed that the seat rings on both valves were either loose or nearly so. Plus, weld quality was poor (Fig 2). Close investigation uncovered still more damage—including cracks in the valve bodies. Other plant owner/operators reportedly have experienced the same problems with the same valve.A second problem area concerned the 1-in. MSS warm-up valves and associated piping (Fig 3). Poor fabrication practices and obvious difficulty in making P91/P22 welds was in evidence. Note that MSS and bypass valves were part of the boiler manufacturer’s scope of supply, but the EPC contractor, D-FD, was responsible for QA/QC.
Replacement MSS valves were not readily available from the OEM and the existing valves could not be repaired locally. Next steps included ordering F22 seat rings from United Valve, Houston, and contracting with CFM/VR-TESCO LLC (formerly Continental Field Machining), Elgin, Ill, to weld the new seats in place.
NAEA’s Sundheim said the valves were difficult to access and cracks in the valve bodies particularly challenging to get at. Cracks were ground out to full depth and welded; PT and UT verified the proper job.
Welding of the seat rings to the valve body was a major project. A robotic welding machine (Fig 5) was required because of the extensive heat treatment requirements (pre-weld, inter-pass, and post-weld) associated with 9-chrome material and the welding of dissimilar metals (Figs 6, 7).Metal temperatures extended up to 1300F. Lengthy warm-up and cool-down times were part of the procedure, too. Mannings USA, Dover, NJ, was the contractor for this portion of the work.
Valve repairs were conducted in parallel with high-voltage work in the switchyard and there was a concern that station power could be lost at a critical point in the heat-treatment process. To mitigate that risk, a 400-kW portable generator was brought onsite as a back-up (Fig 8). Temporary shelters also were required to shield the valves from the elements (Fig 9).
The valves have been in service for 18 months since the repairs were made and are working fine, according to Sundheim. CCJ