Don’t fall victim to these precursors of generator failure
by Clyde V Maughan, Maughan Generator Consultants
Generator stator windings usually have a life of 30 years or more, when not exposed to improper operating conditions and if they don’t carry generic design or manufacturing defects. Unfortunately, neither is the case for many units. Numerous mechanical and electrical deterioration mechanisms can shorten winding life.
The nine failure mechanisms described and illustrated here—six mechanical, three electrical—will help you assess the condition of your generators. Although corrective actions are suggested, keep in mind that generators can fail in unpredictable ways and you may need technical assistance from the OEM or experienced consultants. Some of these deterioration mechanisms are fairly aggressive, many are impossible to monitor adequately, and several still are not well understood.
The generator is an electrical machine and its associated failures are usually electrical in nature. The root cause of the failure, though, is likely to be related to mechanical deterioration—vibration caused by electromagnetic forces (EMF), static and cyclic loads caused by centrifugal and differential expansion forces, insulation fracture, and foreign object damage (FOD), to name a few. Even partial discharge (PD), a prevalent generator maintenance issue, is more likely to indicate another failure mode.
The mechanical deterioration mechanisms discussed below are endwinding vibration, circuit ring vibration, slot bar vibration, winding short circuit, contamination, and FOD; the electrical deterioration mechanisms are slot PD, endwinding PD, and vibration sparking.
Endwinding vibration
Local or general vibration may occur in endwindings. Local component looseness is common, but may not be cause for concern if addressed. If the bar groundwall insulation is not damaged, the tie may simply need to be rebounded or replaced.Driving forces causing endwinding vibration (Figs 1-4) are not well understood. Stator-bar current was long assumed to be the main driver, but recent reviews of operating data suggest that core vibration on 2-pole generators is also a significant factor. Today vibration can be monitored in the presence of the high voltages that exist on the endwindings of in-service generators. But until the root causes are better understood, problems will continue to arise.
Resonances usually cause serious vibration levels in endwindings. For this reason, complete rewinds or repaired windings should be bump-tested for resonant frequencies and mobility. Either can, in worst cases, result in a broken bar.
Mobility is the more serious issue, though. The connection in Fig 2 is breaking apart because of inadequate support for the forces involved. If the failure is detected before widespread damage occurs, splicing in new copper strands and repairing groundwall insulation may do the trick.
In Fig 3, one section broke at the series connection on a two parallel-circuit bar—a failure principally caused by high mobility, with contribution from resonance from omitted series connection blocking.
In this particular design, when a connection breaks, current is transferred to the other half of the bar. Immediate and significant insulation damage is unlikely because the insulation is designed to withstand additional heat for extended periods. But the bar in this half-phase will grow longer from differential expansion. The joint probably will fail in the near future from additional mechanical stress and the unit should be shut down immediately for repair.
The fractured series connection in Fig 4 probably results from resonance, but the electrical burning hides much, if not all, of the evidence that could help establish root cause. This damage can be repaired but, in general, damage this extensive requires rewind to remove contamination, plus extensive core, cooler, and frame cleaning.
Circuit ring vibration
Circuit, or connection, ring vibration (Figs 5-8) is closely related to endwinding vibration, and while more common, tends to be less damaging. Drivers are predominantly EMF of the current in the rings and the proximity of the rings to each other. Core and endwinding vibration also may be contributors. Resonance plays a part in fracturing connections when support is inadequate (Fig 5).
The more common circuit-ring problems arise from insulation wear, which is related to inadequate clamping (Fig 6), blocking, and/or tying. Structural integrity has to be increased to support the higher clamping forces necessary to avoid vibration.
The damage in Figs 7 and 8 results from use of a dry tie material in a system designed to rely on bonding rather than clamping. The dry material cannot form a strong enough bond to the surface of the insulation. Repair here involves replacing dry ties and associated clamping with a wet tie system, which gives a stronger bond among the tie, the blocks, and insulation.
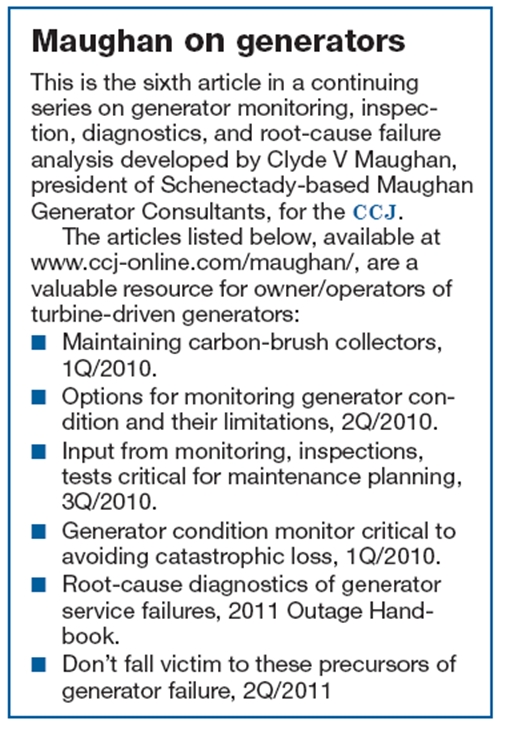
Slot bar vibration
This mechanism includes both bar vibration in the slots and end-of-slot bar vibration (Figs 9, 10). The former has been a problem ever since the first use of hard insulation systems in the late 1950s. Adding side pressure rings and radial pressure springs, as well as improving wedging, have greatly reduced slot bar issues. Yet it is still a constant concern for stator windings.
Assessment of loose wedging should be performed by qualified, experienced personnel. Isolated loose wedges (low concern) or widespread wedge looseness (major concern) may be involved, or wedge looseness may only occur at the ends of the core. Mechanical wedge testing devices must be properly calibrated.
Isolated loose wedges can be corrected by painting a resin in the dovetail region. General wedge looseness can lead to damaging bar vibration, although this is unlikely if side pressure springs are used—unless the bars are not seated in the ends of the slots. General looseness should be addressed by rewedging the entire winding. A word of caution: If the wedge tightness device indicates generally loose wedges, the accuracy of the calibration must be validated by manual tapping of loose wedges.
If bar vibration is indicated only at the ends of the core, root cause is almost certainly not inadequate wedging. Instead, the bars are likely held off the slot bottom by the endwinding support system. The conditions illustrated in Fig 9 may result from bar vibration or from loose end-of-core lamination. You can check the tightness of the core iron by carefully inserting a knife blade between laminations.
Jacking down the bars in the slot, while measuring movement with a dial indicator, will confirm whether or not the bars are seated. If movement of more than about 0.005 in. is found, the end of the slot(s) should be rewedged with special jacking procedures to avoid radial clearance under the bars in the slot.
Winding short circuits
During a winding short circuit or mis-synchronization event, excessive current will flow in the individual phases of the stator winding. The worst conditions for winding damage are synchronizing 180 deg out of phase, or a short circuit before the step-up transformer. Realistically, no generator built today can withstand either of these worst cases without some mechanical damage to stator windings. Most likely location of damage will be the stator bars in the first radius region outside the core.
Shown in Fig 11 is a fracture that has occurred at the end of the core, with forces concentrated at the phase break. Note that the width of the crack gets progressively narrower away from the phase break. The hairline crack in Fig 12 was caused by a sudden short circuit.
Unfortunately, mica, which is used as stator-bar insulation by all OEMs, breaks about like glass. This small crack will have fatally damaged the bar groundwall insulation. Such fatal cracks must be distinguished from the harmless differential expansion cracks that occur in ties and blocks in the endwindings.
Corrective action here includes an over-voltage test, unless the short circuit was minor, or less than about 40% of over-current with no distress indications found. If cracks such as those illustrated are observed, a full stator rewind is necessary.
Contamination
Conductive contaminants—including coal dust, soot, metallic particles, and water—are destructive to the electrical integrity of a stator winding (Fig 13). What’s more, because field windings rely so heavily on clean electrical creepage surfaces (Fig 14), these contaminants can be even more damaging to field insulation.
Sources of contaminants are widespread at powerplants. But the most destructive mechanism of all is plasma resulting from the arc during severe conductor failure (Fig 15, 16). Also, keep in mind the following: (1) Poor ambient conditions do even more damage when the make-up air filters are not maintained, and (2) rain ingress may be a constant source of problems for outdoor units (Figs 17, 18).
Repairs are difficult to generalize for this category. Thorough cleaning may restore windings to acceptable performance when general contamination is observed (Fig 13), but full stator and field rewinds, along with extensive frame and core cleaning, are necessary for the damage in Fig 14. Local repair of the damage exhibited in Fig 17 may be possible, though time consuming. A marginal repair was conducted for the damage in Fig 18 by removing the axial support(s) to allow cleaning of the damaged insulation surfaces and patching of the penetrated groundwall insulation.
Foreign object damage
All reasonable precautions must be taken when the generator casing is open. Otherwise, in the worst case, you get a situation such as that exhibited in Fig 19. But careless work performance (Fig 20) and improper winding cleaning procedures (Fig 21) invite mechanical impact from foreign objects. Unfortunately, if such damage cannot be prevented through meticulous work practices, damage is unique and repairs tend to be unique.
Slot PD
The first electrical deterioration mechanism reviewed here is slot PD (Figs 22-25). Slot discharge refers to PD that occurs on the surface of the bar either within the stator core slot or just outside of it. This class of failure mechanisms came with the introduction of polyester and epoxy mica insulation systems of the 1950s.
PD is a slow-acting deterioration mechanism on mica insulation systems. Failure may not occur for many decades without additional influences, such as bar vibration or bar insulation defects. In air-cooled machines, slot discharges produce ozone which causes other problems and is a health hazard.
Three sources of slot discharge are:
- Loose bars, which lead to vibration of the bar in the slot, and abrading of the slot conductive coating.
- Inadequate slot conductive coatings or poor application of the coating to the groundwall.
- Poor connection of the conductive coating to ground, usually because of an insulating film at the bar surface.
It is difficult to determine which of the three sources initiates the slot discharge. In all cases, however, the energy for the discharge comes from the capacitive energy of the electric field. Thus, this damage occurs only on the bars at the higher voltage end of each phase.
If the problem is widespread, any attempted repairs are likely to be “patches,” not permanently effective. Sometimes adding semi-conductive paint reduces the activity in a particular site, but access to the slot portion of a stator winding is so limited that much of the area will not be treatable in this way. Rewind may be necessary to prevent ozone formation.
Endwinding PD
The predominant endwinding PD is at the phase breaks. Most large 2-pole generators are designed Y-connected, two circuit. These windings will commonly have three locations at 120 deg around the circumference where line-to-line phase breaks occur.
Midway between these three locations are the neutral-to-neutral phase breaks. PD concentrates at the three high-voltage phase breaks (Figs 26, 27). Localized PD patterns are seen on winding bars in operation for long periods (Figs 28, 29). The condition of Fig 29 is of more concern because it suggests that there will be more significant PD inside the slot (which in fact was the case upon closer inspection).
If the deterioration is purely from PD, not accompanied by water contamination or vibration, then it is not likely to result in failure of a mica-based stator insulation system. But if the insulation is other than mica-based, failure can occur in only a few months (Figs 30, 31).
Access for repair in the endwindings is better than in the slots. Painting the endwindings with semi-conductive material may reduce the activity at a PD location, though the repair has to be considered only partially effective. On machines where the phase-bar connections are insulated with non-mica materials, such as potting compounds, remove the potting insulation system and replace with mica-tape materials.
Vibration sparking
While vibration sparking, also called spark erosion, [IT] appears [LF] similar to PD, it is a distinct deterioration process (Figs 32-35). The driver is excitation flux in the core. PD occurs only on higher-voltage bars; vibration sparking can occur at any point on the winding. Like other mechanisms discussed, vibration sparking first occurred in the 1950s with the introduction of the polyester and epoxy insulation systems. Improved wedging systems eliminated the cause: vertical bar movement.
In the 1990s, a form of vibration sparking began to occur globally on vacuum-pressure- impregnated stators (Fig 32). The OEM determined the observed condition was caused by PD, although others believe the problem is related to vibration sparking. More recently, side vibration has been observed on large air-cooled generators with deep, narrow slots.
Low resistance of the slot conductive coating, combined with stator-bar vibration, is believed the root cause of vibration sparking. The current loop is axially along the bar, radially through the core laminations, axially along the keybars at the back of the stator core, and radially up to the bar.
If a bar is allowed to vibrate, the current in this loop will be interrupted at a contact point to the core iron. The interruption of this current will form a tiny arc to the core. If the conductive coating of a bar is low, this current, and the resulting arc, will be sufficient to damage the groundwall insulation by mechanical erosion.
Deterioration is relatively fast with vibration sparking. Fig 33 is a picture taken during a borescope inspection of damage to a modern epoxy-mica groundwall insulation caused by sideways vibration sparking. The stator winding of a similar design failed in service after about four years of operation.
Distinguishing between PD and vibration sparking is difficult, especially for high-voltage bars. Figs 34 and 35 show bars from an air-cooled generator that appear to have both vibration sparking and PD damage. Over-voltage tests may be the only assurance of remaining life of the winding experiencing vibration sparking. But within a few years, a stator rewind will probably be necessary to avoid in-service failure. CCJ




