Learn from long-term experience in burning fuel oil
By Mike Hoy, Tennessee Valley Authority
With the US awash in relatively inexpensive gas, why an article on the storage, handling, and combustion of costly distillate fuel? Simple answer: There are many oil-only gas turbines under contract to support the grid, particularly in areas with large numbers of wind turbines. Most of these machines are relatively old and small by today’s F-class standards.
Plus there are many dual-fuel engines now operating on a steady diet of gas that must be ready to run on oil in an emergency. Distillate degrades in storage and can cause handling and combustion issues if not maintained in good condition. Likewise, liquid fuel systems can adversely impact starting reliability if not exercised regularly and if layup procedures are not followed rigorously.
TVA has a great deal of experience firing oil in its gas turbines, the author told the 7EA Users Group at the organization’s annual meeting in San Antonio last fall. The utility’s oldest engines were installed as oil-only in the 1970s and converted to dual fuel as recently as the late 1990s. Today, the utility has eight sites with 83 dual-fuel machines (mostly GE Frame 5s and Frame 7s) in simple-cycle and combined-cycle configurations. Total dual-fuel capacity is 6255 MW.
Oil storage capability at the eight locations totals 74 million gal. One site alone has 23 million gal of tank capacity to support the operation of that facility’s 16 Frame 7Bs for two weeks with all units at maximum load. Not all tanks at each site are full; oil inventory is maintained to support backup fuel requirements only.
Distillate quality, properties
Distillate sitting in storage tanks for years presents a fuel-quality liability. Water contained in the oil, and that added by condensation of moisture in the vented storage tanks, encourages the formation of bacteria. TVA drains water from its tanks monthly and adds state-approved biocides in the smallest quantities necessary to kill bacteria. Fuel oil is sampled and tested annually for PAD rating and biological fouling.
PAD, which may be a new term for many readers, is a measure of fuel oil decomposition and thermal stability. TVA’s fuel spec requires new oil to have a PAD rating of 3 or less (the lower the number the more stable the oil), but that number will increase as the fuel ages and decomposes. The maximum PAD-scale number is 20; some of the oil fuel in TVA tanks tested as high as 17. The utility has successfully used PRI-D, an additive from Houston-based Power Research Inc, to rejuvenate millions gallons of old oil and significantly reduce its PAD number.
Important to note is that up to 5% biodiesel can be added to petroleum diesel by refiners and distributors without reclassifying the fuel. Problem with storing such blended oils is that biodiesel is hydroscopic and decomposes faster than petroleum oil.
Also, the ultra-low-sulfur (15 ppm sulfur) diesel oil stocked by fuel depots today to meet EPA standards does not inhibit the growth of bacteria as well as the previous low- (500 ppm) and high-sulfur (5000 ppm) fuel oils. No matter; after Dec 1, 2014 all diesel fuel produced in, imported to, and burned in the US must be ULSD. Expect increased bacterial growth in your oil compared with historical levels.
Most ULSD comes from petroleum distillate, but at least one major oil company is said to be developing a synthetic product derived from natural gas. Regarding petroleum-based distillate, important to know is that the refining process used to remove sulfur reduces the aromatic content and density of the ULSD compared to conventional diesel oil. Lower heating value, about—1%—per unit of volume is the result.
However, the biggest user concern with ULSD may be the fuel’s intrinsic lack of lubricity. Fuel oil provides its own “lubricant” when the sulfur it contains combines with nickel to form a low melting point alloy. Poor lubricity can lead to operational problems with critical components—pumps and flow dividers in particular.
Your options are to purchase and install replacement components designed for low-lubricity fuels or have your fuel supplier add lubricating agents to meet industry specs. The latter, if necessary, must be done at the fuel depot/terminal because pipelines usually will not transport ULSD containing additives. Biofuel in small proportions (typically 2% to 5%) also serves as a lubricant.
Raw ULSD has a lubricity of about 640 micrometers, well outside Siemens’ GT limit of 460 um (the higher the number, the less the lubricity); GE does not address lubricity in its fuel spec. You can verify the lubricity of oil received at your plant by having it tested using the high-frequency reciprocating rig described in ASTM D6079.
ASTM D975 is the lubricity standard for diesel fuel in the US and it specifies a limit of 520 um; a comparable European standard specifies 460 um. TVA has adopted the ASTM standard for oil delivered to its GT sites. However, in the company’s experience, ULSD procured for its plants typically has a lubricity value of less than 400 um and there is no need for further treatment before delivery.
Biodiesel for GTs
Interest in biodiesel grew during the days of high gas prices and even higher distillate prices. A few years ago, generous incentives and tax credits available to producers of biofuels, together with government pressure on producing electricity from renewables. had some power generators believing gas turbines powered by green oil might become reality. The availability of inexpensive gas might not be a deal-breaker for biofuels, but it certainly stretches out the commercial timeline.
Successful full-scale operational tests have been conducted on several industrial gas turbines burning biodiesel. This includes combustion of B100 (100% biofuel) at base load in a DLN-1- equipped 7EA at Duke Energy’s Mill Creek site in South Carolina five years ago. The test was conducted on the 2002-vintage engine under the auspices of the OEM and EPRI.
This being a 7EA meeting, the author took the opportunity to review biofuel basics with the attendees. First the definition: Biodiesel refers to a non-petroleum-based diesel fuel consisting of long-chain esters. It typically is made by chemically reacting lipids (usually vegetable oil) and alcohol. It can be burned alone—as the Mill Creek and other tests have confirmed—or blended with conventional petroleum diesel.
Biodiesel can be obtained from a large variety of vegetable resources, but much land is required to produce those resources. For example, corn yields only about 18 gal of biodiesel from each acre in production; soybeans, 48; sunflowers, 102; peanuts, 113. Open-pond algae offers the greatest potential production of biodiesel per acre (10,000 gal), but there’s no large scale production facility anywhere—yet.
Emissions from the combustion of pure biodiesel are significantly lower than those for conventional distillate: unburned hydrocarbons, 67% less; CO and particulate matter, nearly 50% less. However, NOx is higher. When B20 (20% biodiesel/80% petroleum distillate) is burned, the numbers are -20% for unburned HC and -12% for particulate matter. NOx is about the same.
Advantages of biodiesel compared to conventional No. 2 fuel oil are the following:
- Renewable fuel.
- “Soap” content of biodiesel keeps liquid fuel systems clean.
- “Carbon-neutral” emissions. CO2 emissions are about half those released during the combustion of petroleum diesel, but this CO2 originally was absorbed from the atmosphere during the growth phase of the vegetable stock. Thus proponents claim the fuel cycle is “carbon neutral.” The same argument could be made for petroleum and coal, fuel production taking longer because of natural processes.
- Lower CO and particulate emissions.
- High lubricity.
- Pleasant exhaust smell (like French fries).
Disadvantages:
- Hygroscopic: absorbs water from the atmosphere.
- Increased potential for biological fouling.
- Storage time is limited because of hydroscopic action and relatively fast decomposition.
- Higher gel-point temperature.
- Higher pour-point temperature which is conducive to problems at low ambient temperatures.
- Contains about 10% less energy per unit of volume.
- Cleaning action of fuel can cause rapid filter blockage until system piping and components are cleansed of deposits, including varnish, from the previous fuel.
- Possibly higher NOx emissions.
- Attacks and accelerates deterioration of some fuel system materials—such as rubber.
Fuel filtration
TVA’s 7EA fleet, installed between 1999 and 2002, suffered several flow-divider failures relatively soon after commissioning. The primary causes: dirty fuel oil and system debris. Recall that flow dividers have small internal clearances and particles larger than 5 microns can create problems. The original flow dividers were rebuilt with beefier timing gears; later the OEM changed suppliers.
Logically, the filters were checked first. The OEM quoted the filter as “1 micron,” but this fuel-system component was supplied by at least two vendors and filter performance was not consistent among the suppliers. Digging further, engineers found that units with flow-divider problems had filters manufactured from a synthetic material (not pleated paper) and the following characteristics:
- 1 micron, Beta 75.
- 15 micron, Beta 200.
- 19 micron, Beta 1000.
As is often said, the devil is in the details. Sure, these are 1-micron filters, but only at Beta 75. The B15=200 means that the filter will remove 99.5% of all particles 15 microns and larger (filter efficiency equals 1 minus 1 divided by the Beta ratio, or 1 – 1/200 = 0.995). Thus many particles capable of damaging the flow divider can be found in fuel downstream of the filter.
The bottom line: It is impossible to directly compare filter micron ratings unless their micron-size Beta values are the same.
TVA has since standardized on Beta12>1000 filter elements for 7EA liquid fuel systems and Beta22>1000 for its 7B fleet. The older units have larger clearances in their flow dividers and fuel nozzles than the 7EAs and 7Fs. Installing fuel filters that are too fine for the service will develop a high delta P quickly and unnecessarily—particularly with cold fuel. Today, the utility changes oil filters every other year or when the pressure differential across the filter hits 15 psi.
Fuel oil heating
The OEM’s fuel oil spec indicates a maximum allowable viscosity at the fuel nozzles of 10 centistokes (cSt) for light-off. A curve of No. 2 oil viscosity change with temperature indicates that this viscosity requirement is met with fuel oil at 24F (make your own curve by using a straight line through the points 12 cSt/15F and 8 cSt/35F). The relatively mild temperatures experienced at TVA plant locations means oil heating rarely is necessary for viscosity purposes.
However, filter blockage caused by waxing of fuel oil at low temperatures is of ongoing concern. Minimum pour point for TVA fuel is specified as 0F, easily met by ULSD. Cloud point, although not specified by the utility, typically is less than 20F. Low oil temperature caused by unavailable oil heaters was implicated in some unit trips (no 7EAs), but these may have been traceable to water in the fuel or high filter differential pressure that was exacerbated by cold oil.
All TVA gas turbines capable of burning distillate are equipped with GE’s standard 480-V, 20-deg-F-rise fuel-oil heater. Some issues with thick, burned-on crud around the heating elements have been experienced and elements have failed because of overheating attributed to crud buildup, improper installation, and improper valve line-up. Relatively simple controls can prevent most failures.
For example, the heaters serving TVA’s 7EAs are arranged to shut off when oil temperature hits 50F and circuitry prevents heater operation when there is no fuel flow to a unit.
However, no plan is foolproof. One site experienced a problem when electrical transients from auxiliary 480-V power switching caused a fuel heater’s PLC controls to lose its programming. This caused the following chain of events:
- SCR control current output went to maximum.
- Heater operated at full power with no fuel flow.
- Severe overheating was brought to the attention of operators when smoke poured from the heater compartment.
- Fuel oil in the heater and adjacent piping reached several hundred degrees as evidenced by heater distortion and pipe discoloration.
Luckily this occurred during the site’s manned hours and was discovered before a fire started. Keep in mind that the auto-ignition temperature of No. 2 oil is 494F, half that of natural gas and lower than gasoline (Sidebar).
Valves, off- and on-base
The eight 7EAs delivered to TVA in 1999 were supplied with fuel systems that included so-called OCV assemblies—combined stop/pressure-regulating valves arranged in off-base spool pieces. Many problems were experienced, particularly in cold weather, which the OEM attributed to “freezing.” Plant personnel disagreed but heavily heat-traced and insulated all such assemblies, thereby making them “inaccessible.” Extensive insulation re-work was need after valve maintenance.
The OCVs were prone to fail open when fuel oil was first called for. Also, the needle-valve adjustment on their sensing lines was over-sensitive. When the needle valve was open too much, the OCVs hunted wildly, causing pressure swings; when closed too much, pressure feedback and regulating capability were lost. Only a small fraction of a turn on needle valve separated the two extremes and setting at one flow meant the OCV didn’t work at other oil flows.
The needle-valve setting was prone to being “bumped,” especially during repeated insulation work. There always was some oscillation of regulated pressure caused by OCV instability when operating at load, regardless of the OCV setting. GE tried changing the internal orifice size within all OCV devices but that didn’t help. Finally, the OEM admitted the OCV valves were inappropriate for the given application.
Also, the fuel-oil recirculation design arrangement for the spool pieces was counterproductive. Instead of recirculating back to the fuel-oil tank (ideally to the air space at the top of the tank), they recirculated to the discharge side of the fuel forwarding pumps. This did not help prevent hunting/oscillation of the regulating valves for steady operation.
GE tried replacing the OCVs with a combined stop/pressure-regulating valve arrangement from another manufacturer, but experience on a couple of tests at TVA, and experience elsewhere, showed the new set-up was only marginally better than the OCVs. Ultimately, the utility replaced the combined valve arrangement with separate pressure-regulating and stop valves. Important to point out is that TVA normally would not have installed off-base stop valves, which are not required by code, relying solely on the on-base stop valve. However, GE required it.
Fuel-oil safety facts, best practices
Users new to firing oil in gas turbines can benefit from information presented in the bullet points below. Some of the facts will likely surprise you.
- Auto-ignition temperature—the lowest temperature at which a substance will spontaneously combust without an external ignition source—of No. 2 fuel oil is 494F, which is lower than that for both gasoline (535F) and natural gas (more than 1000F). Note that the high-temperature alarm setting for the 7EA turbine compartment usually is about 300F.
The low auto-ignition (AI) temperature of distillate is the reason that the purging requirements for oil-only and dual-fuel units are more stringent than those for gas-only units—particularly in combined-cycle applications.
- Flash point—the minimum temperature at which a liquid will vaporize to form an ignitable mixture in air—of No. 2 fuel oil is 143F. The flash point (FP) of gasoline is -45F. The takeaway: Diesel fuel has high FP/low AI temperatures and gasoline the opposite. This is why diesel is the fuel for reciprocating engines, which use only compression for ignition, while gasoline engines have spark plugs.
- Never try to fix a fuel-oil leak inside the turbine compartment with the unit operating or still very hot. People have burned to death doing this. A virtually invisible spray of fuel oil can drench clothing; excessive tightening of a fitting can make the leak worse or break the fitting.
- Ensure that false-start drain valves always open properly at low turbine speeds.
- Do not try to restart a machine without first allowing fuel oil to drain and purge adequately between starting attempts. Significant damage has been experienced when a false-start drain valve (FSDV) jammed closed and pooled fuel oil. Best practice: Install FSDVs with limit switches that must indicate open before the turbine can start.
Purge, check, three-way valves. The first 16 7EAs installed at TVA, in 1999-2000, were supplied with fuel-oil and purge-air check valves located at the combustion cans (separate sets on primary and secondary systems). These were prone to the same issues that dogged the GE dual-fuel fleet for many years, including the following:
- Liquid-fuel check valves leaking in the reverse direction when operating on gas, thereby allowing combustion gases back into the fuel-oil system—sometimes all the way back to the storage tanks.
- Coking of fuel oil in the check valves and fuel nozzles, creating issues on gas operation.
- Leaking purge-air check valves, which allowed distillate to flow out of the purge-air tell-tale drain.
Later 7EA units, those installed by TVA in 2001-2002, were equipped with the three-way valve arrangement GE had just adopted. These proved problematic when operating on gas. Fuel oil trapped between the on-base stop valve and the three-way valve would heat and expand, causing the spool piece for the latter to move to an intermediate position. Symptoms of this at TVA were high CO readings on gas, caused by improper purge-air flow. GE subsequently retrofitted a complicated fuel-oil pressure-relief arrangement (automatically actuated when operating on gas) to accommodate this.
In the 1970s, GE’s standard design practice (even for oil-only machines) was to have two fuel-oil check valves in series—one set located at the cans, another just downstream of the flow divider in the accessory compartment. This arrangement had proven reliable at TVA, so engineers thought to try it on a couple of check-valved 7EAs. An extra set of check valves, identical to those at the cans, was installed between the flow divider and the fuel-oil splitter valve (Fig 1). That mod solved the problem and it was implemented on all 16 engines equipped with check valves.
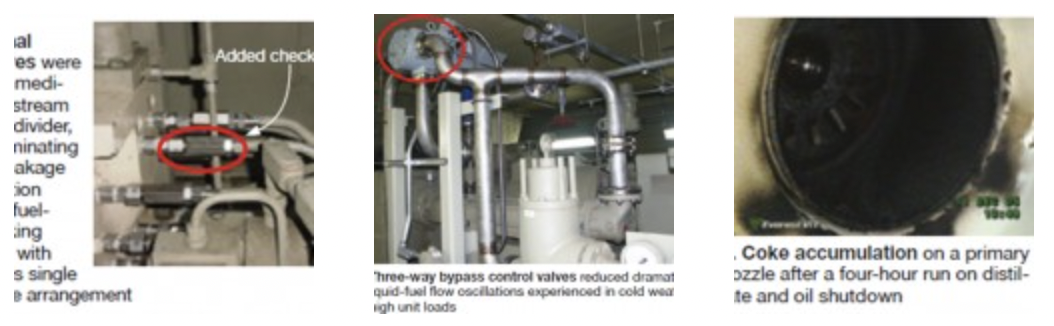
TVA suggested replacing the three-way valve/pressure-relief equipment on the later 7EAs with the dual-check-valve arrangement but the OEM nixed that idea. The units were operating under a long-term service agreement and the decision was GE’s to make.
Bypass control valves were another sticking point. TVA’s 7EAs all were supplied with two-way bypass valves with no valve position feedback, even for indication. All fuel-oil flow control was accomplished via flow-divider speed signals.
Early in the fleet’s history there were extensive and serious problems associated with the liquid fuel system, especially when oil flows were high in cold weather. Issues included large oscillations in flow, causing piping in the accessory compartment to move enough to break welds and tear-up gear-type main oil pumps.
Some problems were attributed to strainer and filter blockage caused by improper flushing, failures of flow dividers, and poor fuel-forwarding stop valve and pressure-regulation control. While all these played a part, TVA engineers believed the main cause was an improperly specified bypass-valve design and control arrangement. Ultimately, GE retrofitted all the units having three-way valves with three-way bypass control valves (Fig 2). The remaining check-valved 7EAs still have their original two-way bypass valves. Issues have been minimal because these units have not had to operate on fuel oil at high loads for many years.
How to reduce coking
An article in the CCJ mentioned using the atomizing-air booster blower to reduce coking in fuel nozzles by purging and cooling during shutdown on oil. TVA investigations showed that this originally was a GE idea, but never implemented at any plant. Trials were promising and the 7EA fleet was arranged for post-combustion air purge. Here are the details:
TVA units suffered coke buildup—most severe on primary fuel nozzles—when its dual-fuel units were repeatedly shut down on oil. Such buildup caused the units to drop out of premix steady state on the first gas start following several oil shutdowns. The OEM recommended transferring to gas during oil shutdowns to reduce coke build-up, which was effective. However, this often was not an option for TVA. When its units ran on oil, it usually was because gas was not available.
TVA got best results by keeping atomizing-air (AA) booster compressors running for nine hours after shutting down on fuel oil. Primary and secondary purge flow paths are open during this period and coke buildup is virtually eliminated. Fig 3 shows primary-nozzle coke accumulation after a four-hour oil run and oil shutdown; Fig 4 shows a primary nozzle after a four-hour oil run and oil shutdown with atomizing-air purge following shutdown.
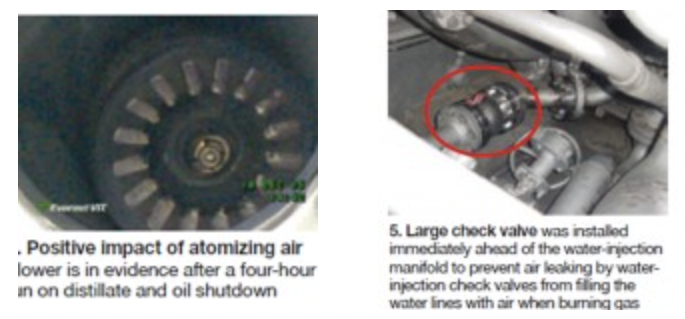
As plant personnel gained experience with the technique they concluded that there was merit to running the booster compressor after all gas and oil shutdowns to prevent coking of oil that burps into the nozzles because of thermal expansion while the unit is shut down. Keep in mind that the TVA 7EA fleet is not manned 24/7 but is available by remote start. Without the AA mod, the unit can be called on for load and fail to stay in premix steady state, thereby initiating an automatic shutdown attributed to high emissions.
Miscellany
- Loud, low-frequency noise (a nominal 25-Hz rumble) is common for water-injected gas turbines operating on fuel oil. The OEM has addressed this by installing orifices in the secondary fuel-oil lines so when the splitter valve is open, 60% of the oil flows to the primary nozzles, 40% to the secondary nozzles (normal fuel split is 50/50). TVA implemented this solution on several 7EAs as an experiment, but has not retrofitted the entire fleet because the noise is not viewed as a major concern.
- A problem associated with dual-fuel units using water injection for emissions control when firing distillate is backflow of combustion air via the water-injection check valves when operating on gas. Filling the water injection system with air creates problems when that system is next needed during oil firing. Issue was addressed by adding a large check valve immediately before the water-injection manifold in the turbine compartment (Fig 5).
- Fuel-pump clutch slippage has been experienced on several dual-fuel Frame 5s and 7Bs. Symptoms usually are load swings at high loads and fuel flows. Problem is easy to diagnose using a strobe light. Remove the clutch covers to gain access to the input and output shafts on each side of the pump clutch.
Slippage rarely is experienced at low loads, and because pump speed is constant, the strobe light frequency is adjusted to “freeze” the image with the unit operating at low load on distillate. As load increases and the clutch starts to slip (often intermittent) the pump shaft image loses its synchronization with the input shaft. Complete clutch replacement usually is the only remedy for this. CCJ