Borescope safety, practices
Armstrong Energy
International Power America Inc
625-MW, dual-fuel, simple-cycle peaking facility located in Shelocta, Pa
Plant manager: Matthew Denver
Key project participants: Wes Crawford, Jim Mandella, Peter Margliotti, Bryan Miller, and Dexter Cox, plant combustion turbine specialists
Challenge.
Armstrong Energy performs an annual borescope inspection on each of the four 7FA gas turbines onsite. The task of prepping a unit for inspection can be very tedious, especially if the job is not planned well and preventive maintenance actions are not taken to ensure the unit can be opened without any mishaps.
Before the job can be started a LOTO has to be performed to ensure the safety of personnel and equipment. During this process, the inlet guide vanes (IGV) are opened, the actuator arm pin pulled, and a safety block put in place to prevent the vanes from accidentally closing. A few processes were developed to accomplish this task in a safe manner.
Solution.
A ladder attaches to the platform next to the IGVs to allow easy access to remove the pin (Fig 71). Secondly, an IGV block, made from a heavy duty bolt and a handle, is attached to the threads (Fig 72). This prevents personnel’s hands from entering the path where the block is placed. Thirdly, a tool was made to force the IGV pin out of the dog bone eye without hammering out the pin and causing damage to the equipment (Fig 73). Once the IGVs are put into the correct angle, personnel can set the tool in position and remove the pin safely.
Ensuring the proper tools are present for the job is a key ingredient to a successful outage. This saves a lot of time and heartache. The best way to ensure this is to provide two pre-staged job boxes with all necessary tools needed for the job (Fig 74). One box is staged on the upper level, the other on the lower level of the unit receiving the borescope.
Each job box is equipped with two toolboxes which house the different size of sockets, wrenches, adapters, and extensions to remove the necessary bolts. In addition, there is an air impact gun, hose, and lifting chain to remove the manway covers located on the gas turbine engines (Fig 75).
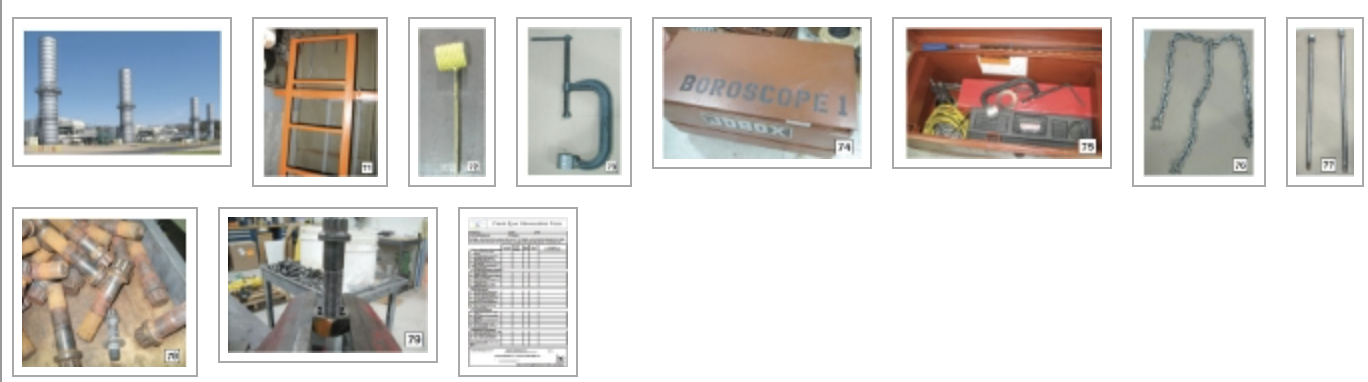
Removal of the manway covers may appear to be an easy task but it’s not always as easy as it looks. The top cover can be lifted off with the use of the overhead chain fall (Fig 76), but the bottom cover is a challenge in itself. To combat the problems with lowering the bottom manway cover the plant decided to make three guide rods which are threaded on each end (Fig 77). Utilizing three chain falls in coordination with the guide rods and the gas turbine eye bolts, the man way cover can be lowered easier and safer.
Bolt maintenance is an important key in this process. It ensures the bolts will be removed safely and without damage (Fig 78). Removal of bolts the first year was a horrendous task. A few bolts broke, damage occurred to threads and slugging wrenches had to be used when the pneumatic impact guns couldn’t perform the job.
To prevent that from recurring a maintenance program was implemented to have all bolts cleaned using a die, cutting oil, and a wire wheel buffer (Fig 79). The bolt holes are also tapped; thereby the bolts come out easier and without any damage.
During the evolution of opening the turbine for maintenance, a member of the management team observes and records findings on a “Fresh Eyes Observation Form” (Fig 80). This program allows another set of eyes to observe the task being performed, highlighting what was done wellt, what can be improved, and to ensure the overall safety of the job.
Results.
When all these practices are put together, the resulting borescope preparation and inspection is a much safer and efficient task. With plant staff pulling together, focusing on an assigned task, and constantly searching for safe and effective ways to improve the process, we feel this qualifies as a best practice.