Rx for compressor fouling: proper ingestive cleaning
When the performance of your gas-turbine compressor degrades because of fouling, don’t just assume an “over the counter” compressor cleaning will do. Get a prescription that accounts for the specifics of your machine and its operating characteristics. Here’s what you need to know about cleaning fluids, delivery systems, and economics so that you can discuss your situation intelligently with turbine care providers.
The diagnosis
Gas-turbine operators know that engine efficiency deteriorates progressively with compressor fouling (Fig 1). Under typical running conditions, about 70% of the loss in efficiency and power can be attributed to compressor fouling. But fouling can also accelerate the aging of components and lead to forced outages if thermal limits are breached or vibration levels fall out of normal range.
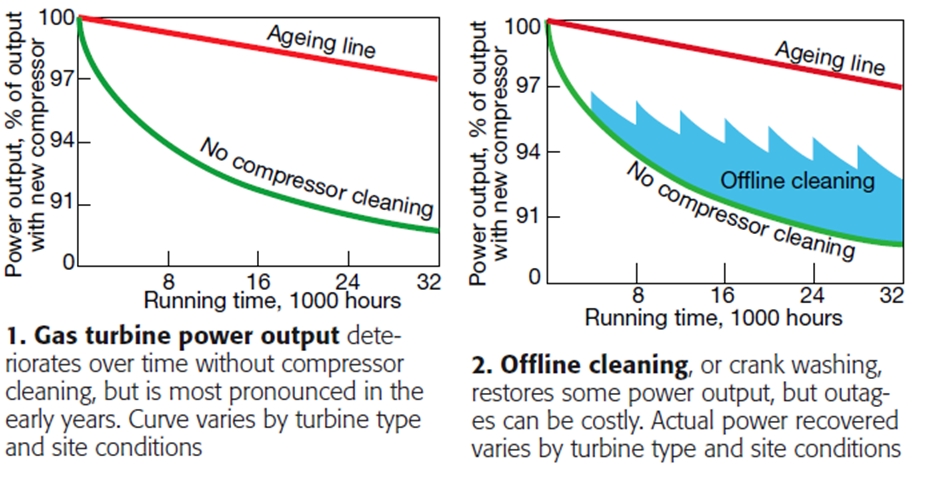
Fouling airborne contaminants can be organic or inorganic—soils, fibers, insects, herbicides, insecticides, soot, pollutants, corrosive chemicals, etc. They combine with moisture from the air and internally emitted lubricants and vapors, which cannot be prevented altogether in even the best maintained engines.
In the back stages of the compressor, the contaminants are baked, and then tend to migrate through to the combustor where they are burned. Contaminants on the forward stages tend to undergo physical state changes. They come to resemble a varnish-like layer on the surfaces. Removing this material requires proper selection of cleaning substance and delivery system.
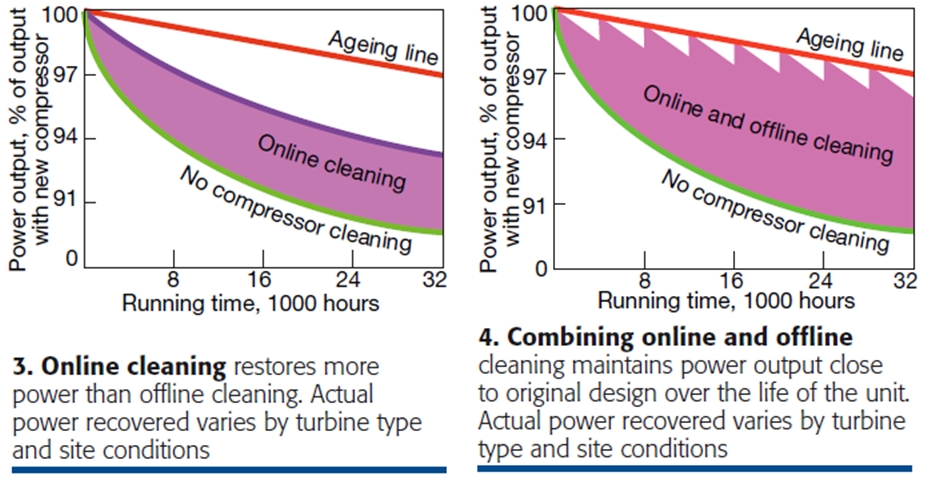
Your options
Although mechanical cleaning, the use of abrasives to “scrub” contaminants off blade surfaces, once was prevalent for gas turbine compressors, newer machine designs are essentially too complex for their use. Pieces of abrasives, nuts, rice hulls, aluminum oxide, and others, can lodge in variable-pitch blade apparatus, impairing their use, or clog cooling-air ducts. OEMs that do approve abrasive mechanical cleaning typically impose limits on particle size, stone content, and residual ash. For this reason, chemical cleaning agents are the focus here.
Crank washing, or offline cleaning, is the most effective and most commonly used method. The procedure is straightforward. The compressor section is flooded with the chemical cleaning agent; the blades, immersed in the fluid, are rotated, and then the unit is allowed to soak. Afterward, the compressor is thoroughly rinsed with demineralized water (some call it deionized water, same thing). While its ability to restore performance is unquestioned (Fig 2), offline cleaning requires downtime, which sacrifices revenue.
Starting and stopping the unit also affects component life. Thus, the time between outages for offline cleaning is extended with online cleaning techniques (Fig 3). When online and offline cleaning techniques are combined, almost all of the lost power output can be restored (Fig 4).
Although water, known as the “universal solvent,” can be used as a cleaning agent, it is an inefficient and risky choice. For one thing, it cannot combine chemically with hydrocarbons, the largest fraction of fouling substances. Heating water can assist in the physical removal of hydrocarbons, but that also means it will evaporate before it achieves the proper depth of droplet migration.
Standard tests show that the effectiveness of water-based cleaning is 10-20%, compared to 80-100% for chemical agents. Water can disperse and dislodge soils and salts but these contaminants are often embedded in the hydrocarbon material. To be effective, water has to be applied at high pressures, exposing compressor surfaces to erosion.
Under no circumstances should you use water that has not been demineralized. Alkali and alkali earth compounds and chlorides and fluorides (that is, salts) present in untreated water can cause severe damage to turbine hot section components. But even demin water, because of its extremely low level of electrical resistance, can establish galvanic cells in areas where dissimilar metals are joined. Finally, water has a surface tension about 30%-50% higher than chemical solvents, making it more erosive.
In nature, a substance only can be dissolved by a like substance. Therefore, chemical cleaning is based on the interaction of “fat loving” lipophiles and “water loving” hydrophiles. Oil, greases, fats, and other hydrocarbon-based substances are lipophilic. Such compounds can be solubilized and dispersed into a stable aqueous medium through emulsification with a “surface active agent,” better known as a detergent. All aqueous cleaning fluids rely on this principle.
Chemical cleaning agents are strongly preferred, for the reasons stated above. They fall into two categories: petroleum distillates and detergents.Distillates are strongly lipophilic. They dissolve into the hydrocarbon contaminants, loosening and softening them, and making them easier to dislodge by the action of centrifugal force (from the spinning of the blades). Solvents are most frequently used for crank washes, but are not as effective for online washing.
Reason is the solvent “flashes” in the elevated-temperature sections of the casing, and the contaminants dislodged from earlier stages readily accumulate on later stages. Uneven deposition leads to vibration issues and even combustion in the compressor, which in turn can lead to overheating, over speed, and unit trips. Finally, solvents are intrinsically toxic (high level of benzene-based compounds), and require special handling and storage.
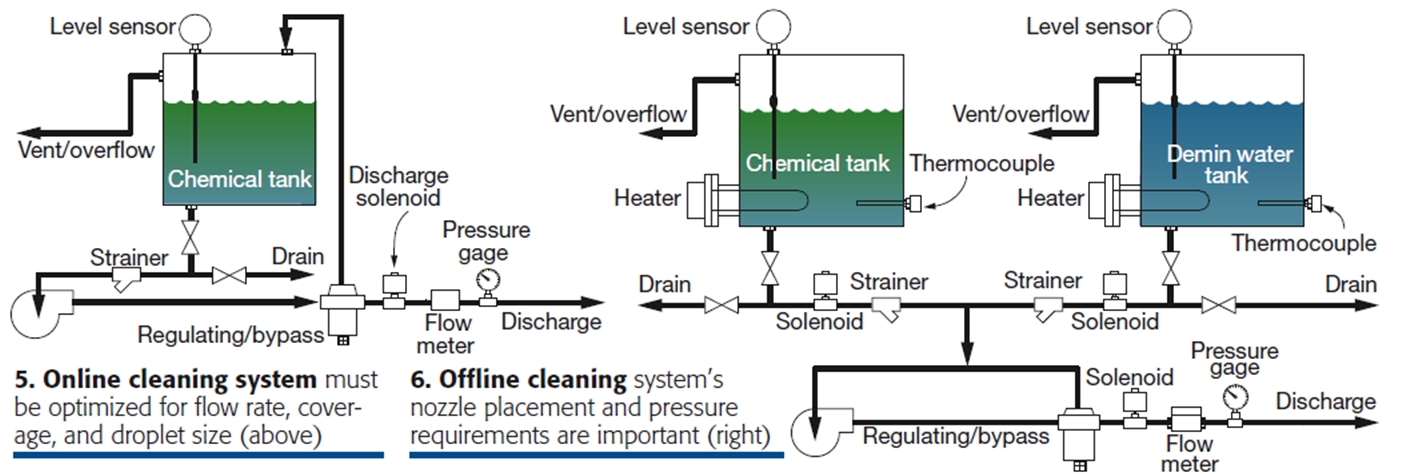
Surfactant-based fluids clean by lowering the surface tension of the aqueous carrier. As the wet fluid contacts the fouled surface, the solution readily penetrates the porous matrix and dissolves into, or combines chemically, with the contaminants. The material is then dislodged permanently as the blades rotate, and is burned in the hot section.
Surfactants typically have high vapor points, exceeding 400F, allowing them to migrate as liquid well into the compressor. They also exhibit low surface tension and better wetting capability, which means they produce larger droplets, increasing the contact area with the contaminants. Finally, they are less erosive than water.
Important to consider with surfactants for online cleaning is the purity of the mix water. If the surfactant is being diluted from a concentrated state, then demin water should be used. This ensures that the active ingredients in the cleaner will not combine with solids in the mix water and degrade cleaning ability. Deionized water used for mixing and rinsing should conform to the requirements of ASTM D1193.
Choices of surfactants fall into the three categories: linear alkyl sulfonates (LAS), ethoxylated alcohols (EOA), and ethoxylated tertiary amines. All of them have low levels of heavy metals and chlorine to meet OEM specifications, are nonflammable, and biodegradable. However, LAS surfactants typically exhibit high pH before mixing with water and alkali metals—primarily sodium, potassium, calcium, and magnesium. Such strongly basic compounds will attack aluminum alloys and aluminides present in ceramic/metallic coatings, VSB bushings, and other components. EOA and tertiary amine-based products are usually neutral or only slightly basic.
LAS surfactants comprise large molecules of at least 10 aromatic and aliphatic alcohol hydrocarbons. They are bound with a hydrophilic group, such as sulfonates, in an aqueous carrier with a wetting agent, commonly a glycol-ether-type compound. These compounds can be toxic and combustible. They must be stored, handled, and used in accordance with their associated regulations.
EOA surfactants are selected based on the anticipated temperature during the cleaning period. They don’t remove carbon-based fouling agents as efficiently as ethoxylated tertiary amines, and exhibit lower boiling and flash points. If these surfactants contain volatile organic compounds (VOC), then local environmental restrictions must be considered.
The ethoxylated tertiary amine surfactants combine long-chain cationic amines, bound with several [nonionic] molecules of ethylene oxide, into a more compact molecule. These surfactants are both lipophilic and hydrophilic, so they readily combine with both organic and inorganic contaminants. They tend to persist longer in a liquid state at high temperatures. Thus the duration of contact is longer, so lower injection rates are possible. Biodegradable, amine-based detergents avoid excessive environmental and safety regulations.
Delivery systems
Space precludes a complete discussion of cleaning-fluid delivery systems. However, a few points are useful to know.
- Online and offline delivery systems differ somewhat (Figs 5, 6). The systems are designed to deliver a cleaning agent at the desired flow rate and design particle size and spray characteristics. Offline systems are typically designed to OEM specifications.
- Heaters should be considered in offline systems to increase efficiency and reduce risk of thermal shock.n The preferable location for offline-system wash nozzles is outside the plenum, although this isn’t always possible.
- Only low foaming cleaning products should be used in offline systems.
- Flow rates for online injection should not exceed 0.2% to 0.4% of engine mass flow. In practice, OEM recommendations vary.
- Nozzles have fixed capacity at a specific pressure. They should to be selected to deliver a sufficient volume of fluid, provide full and uniform coverage of contaminated surfaces, and maintain injection long enough to remove the foulants. Nozzles that deliver more than the optimum flow waste money.
- Nozzle spray angles—whether the nozzles are of the cone or flat-fan variety—may vary with the physical properties of the cleaning fluid. Equipment for delivering solvent-based agents is seldom suitable for detergent-based products.
- Droplet size is a critical parameter for cleaning effectiveness. A rule of thumb is that droplet size should be around 150 to 200 microns for online cleaning, and 500 to 700 microns for offline cleaning.
Cost/benefit
Effective compressor cleaning saves money three ways. First, for a typical machine, the time between major overhauls can often be extended from five to seven years if cleaned regularly. Second, the gain in efficiency and output reduces direct costs for fuel, consumables, labor, etc. This is the primary saving, and the one most easily calculated. Third, regular cleaning will extend component life, largely attributed to avoiding higher-than-desired operating temperatures.
For a typical GE Frame 6 firing natural gas, the rated output is 42.1 MW at ISO conditions. Heat rate is approximately 10,642 Btu/kWh and typically deteriorates from 2% to 4% over the first 2000 hours of operation.
Assumptions taken to calculate the saving associated with washing: recovery in performance of three percentage points; fuel lower heating value of 1010 Btu/ft3; cost of fuel, $3.98/1000 ft3; load factor, 50%; cleaning fluid dosage, 60 gal; cleaning frequency, once per week; cleaning fluid cost, $3.95/gal.
“Doing the math” suggests that, for a $12,324 annual investment, the saving is close to $220,000. ccj