First-rate aero-engine training at virtually no cost
For the latest information on technical and social programs, exhibit space, sponsor-ships, conference and hotel registration, etc, visit www.wtui.com. To reserve exhibit space and sponsorships, contact Bill Lewis or Alvin Boyd
The best deal in the aero sector of the electric power generation business likely is a “ticket” to the Western Turbine Users Inc’s 24th annual conference and exhibition, March 23 – 26, at the Palm Springs Convention Center.
The employee with limited aero experience that you hired to replace a recent retiree will return to the plant with a good sense of what the engine is all about and the problems most likely to occur—a solid educational foundation to build upon. The more experienced people on your staff should attend to continue learning, an incremental process. You grow professionally with every meeting and become more valuable to the organization.
Hundreds of LM2500, LM5000, LM6000, and LMS100 owner/operators participate in WTUI meetings for the updates they receive on fleet issues from the OEM and its licensed repair depots—TransCanada Turbines (TCT), Air New Zealand Gas Turbines (ANZGT), Avio SpA, IHI Corp, and MTU Maintenance Berlin-Brandenburg GmbH. The depots are independent organizations authorized by GE to perform repairs up to Level 4.
The comprehensive technical presentations and open discussion periods conducted during the breakout sessions for each engine contribute to maintaining top performance; they offer sound guidance on how to identify potential issues early and what proactive steps can be taken to prevent unplanned outages.
The closed-door sessions for users run more than nine hours over the two-and-a-half-day meeting. Programs specific to each engine, carefully planned by the depots and the WTUI leadership (Sidebar 1), are detailed in nominal 100-page full-color notebooks given to attendees at their breakout session of choice. At typical depot notebook contains the following material:
- Engine fleet statistics, manuals, and definitions.
- A review of recent service bulletins (SB) and service letters (SL) issued ty the OEM.
- A summary of depot findings since the last meeting, information that’s invaluable for anyone planning an outage.
- Causes of performance loss and how to correct them.
- Lifetime management of critical parts.
- Engine preservation, handling, and transportation.
- Expectations with regard to maintenance intervals.
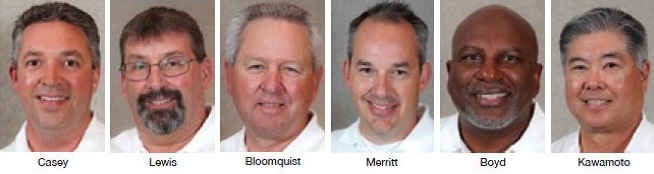
1. WTUI leadership
Officers
President
Chuck Casey
Riverside Public Utilities
Vice Presidents
Bill Lewis
PPL Generation LLC, PPL Ironwood LLC
Jim Bloomquist
Chevron USA Inc
David Merritt
Kings River Conservation District
Secretary
Alvin Boyd
Kings River Conservation District, Malaga Peaking Plant
Treasurer
Wayne Kawamoto
CAMS Juniper CA LLC, Corona Energy Partners
Board of Directors
Dan Arellano
Calpine Outage Services
Charles Byrom
Anaheim Public Utilities Dept
Ed Jackson
Missouri River Energy Services
Andrew Gundershaug
Calpine Corp, Greenleaf
John Baker
Riverside Public Utilities, Clearwater Cogeneration Plant
Bryan Atkisson
Riverside Public Utilities, Riverside Energy Resource Center
Don Stahl
Black Hills Corp, Pueblo Airport Generating Station
Conference Chairpersons
New Users Session
Bob Boozer
Reed Services Inc
LM2500
John Baker
Riverside Public Utilities, Clearwater Cogeneration Plant
LM5000
Perry Leslie
Wellhead Electric Co, Yuba City Cogeneration Plant
LM6000
Andrew Gundershaug
Calpine Corp, Greenleaf
LMS100
Don Haines
Wood Group Power Operations Inc, Panoche Energy Center
Supporting Staff
Webmaster
Wayne Feragen
E I Colton LLC, Agua Mansa Power Plant
Technical Consultant
Mike Raaker
Raaker Services LLC
Registration Coordinator
Charlene Raaker
Raaker Services LLC
Conference Consultants
Joella Hopkins
Simply Mumtaz Events Inc
Jennifer Minzey
Simply Mumtaz Events Inc
Session notebook in hand, it’s easy to follow the depot presentations and jot down additional notes where necessary. And if you step out of the room to take an important call, WTUI has you covered. CEO Sal DellaVilla and his colleagues at Strategic Power Systems Inc, Charlotte, attend every session to take notes, which are then posted in the user-only portion of www.wtui.com. SPS’s notes also form the basis for the summaries of the 2013 breakout sessions below.
Beyond the focused technical sessions, the world’s largest conference on aero engines features the largest exhibition of gas-turbine products and services anywhere. You’re sure to meet at least a few suppliers who can offer suggestions on how to improve plant performance. The exhibit hall will be open during the reception Sunday evening (March 23) and all day Monday and Tuesday (Sidebar 2).
Important for newcomers to note is that WTUI conducts orientation sessions at 3:30 Sunday afternoon, following the optional golf and tennis tournaments. The LM engine familiarization workshop, which runs for about an hour and a half always gets high marks from first-timers. Typically one-third of the users are attending their first Western Turbine meeting, many unfamiliar with one or more engines supported by the group.
The crash course will be taught again this year by Bob Boozer of Reed Services Inc. It is excellent preparation for the breakout sessions beginning Monday morning. Acronyms used in casual conversation by this group are defined in Sidebar 3. Boozer’s workshop will be followed by an SPS presentation explaining the Operational Reliability Analysis Program (ORAP®), an automated system for monitoring and reporting RAM-D (reliability, availability, maintainability, durability) data for gas and steam turbines worldwide.
SPS is an unbiased third party that provides turbine users the means to benchmark their assets against the fleet regarding inspection intervals, time-to-repair statistics, component failure rates, best practices, etc. Unit-specific information also is provided to owners of those assets. SPS works closely with WTUI to support LM users.
Engine breakout sessions
LM2500
Session chair and discussion leader for the 2013 LM2500 breakout sessions was John Baker, who manages the 1 x 1 Clearwater Cogeneration Plant for Riverside Public Utilities and is a member of the WTUI Board of Directors. This was Baker’s fifth year as the LM2500 track chair. He was supported by the following depot representatives: Antonio Errico of Avio, Ralph Reichert of MTU, Brad Downie of TCT, and Sabro Muratbegovic of ANZGT. Cindy Alicea and Karl Maier of SPS were the session secretaries (note-takers).
Case history #1. One of the opening discussions focused on the heavy damage to compressor blades and vanes on a unit with 50,000 service hours. Three 10th stage blades were released and went downstream. Inspection revealed cracks in the dovetails of many blades. Minimal background information was available for the failure analysis because there were no maintenance or inspection records for the engine.
Attendees were reminded that you can’t ignore the compressor during inspections and that accurate record-keeping is important. A depot representative said he was aware of similar failures on other engines in the fleet over the years, but none associated with the 10th stage. This machine was said to have thrown a blade previously, but it was never found.
Case history #2. The top half of a first-stage HP compressor blade released into the air path and caused extensive damage. Machine had only 33,000 operating hours and was overhauled 400 hours before the event. Investigation revealed a small pit on the pressure side of the blade and a small crack on the suction side: The two met in the middle of the airfoil. Damage totaled about $1 million and likely would have been more if the engine were at full speed when the blade separated.
Pits found in other blades were so small they were not visible to the naked eye. Exact cause was unknown but personnel believed they might be related to FOD/DOD (refer to Sidebar 3). Engine was equipped with a sock and FOD screen on the front end; blades were overhauled, not new. At least one tiny piece (? in.) of the stainless steel screen had liberated because of corrosion and gone downstream. Suggestion to attendees: When checking FOD screens, do a careful close-up inspection for tiny discontinuities in the material—they’re important.
A user commented that the FOD screen on one unit at his plant was removed because of compressor airfoil dings caused by bits of wire rope going downstream. He claimed less maintenance for the last 12 years because of this modification.
Case history #3. Engine had operated 32,000 hours since its last overhaul and HPCR vibration had been increasing over time. Operations personnel were baffled by a vibration signature that changed with every start. The unit was shut down when vibration exceeded recommended limits. The owner could not point to an obvious cause of the vibration until that time. An inspection team found the air-duct Vespel® strip completely disintegrated and the majority of blade gaps out of limits.
A depot visit revealed several separate problems that could have caused the vibration, including ones associated with the CFF, HPCS, CRF, HPTR, and TMF. Defects in those areas were repaired. The depot said the entire engine exceeded vibration limits upon receipt, making it difficult to determine the root cause of the problem.
The owner believed the cause might possibly have been package misalignment but the depot thought otherwise. Field service had inspected the unit before it was shipped to the shop, noting that trim balance is not the solution for everything. The technicians said that sometimes the machine must be stripped down and realigned.
Case history #4. Interesting is the wide range of issues you learn about during the user and depot presentations and open discussion sessions at Western Turbine
meetings. Consider the engine that experienced high vibration upon restart after two years of idle time. Among the unknowns were operating hours since COD or last overhaul. A large amount of debris was found in the engine because of its inactive status.
The HPCR air duct was loose and the Vespel strip completely missing. The owner wanted a least-cost return to service; efficiency was not a concern for this rarely used engine. The air duct was removed and Vespel strip replaced. General cleanup was done and the unit returned to operational status. HPC vibration was measured and satisfactory.
Case history #5. Engine was sent to a depot because of high vibration. It had been 32,000 hours since the previous overhaul. Shop personnel found the rear shaft scraped and unrepairable. The shaft was replaced.
Case history #6. The depots reported chipping of the rub coat on three LM2500+ engines in 2012—all operating base-load. Thinking was that perhaps the higher operating temperatures associated with this machine were the underlying cause. Regular borescope inspection was recommended. Rub coat was replaced in the three affected engines.
Case history #7. During removal of an LM2500+ engine, personnel discovered that an air/oil seal had liberated and damaged some stationary parts. Seal loss was attributed to high-cycle fatigue. The seal was replaced with one of newer design. Interestingly, the seal loss did not impact oil consumption; there was no leak to indicate a problem.
Case history #8. Cracks propagating from unused bolt holes, or from holes with loose bolts, have been found in the CRF mid-flange. Cracks may grow inwards toward the case, or go outwards. High-cycle fatigue experienced by startups and shutdowns was said to be one of the main causes. Bolt tightness should be verified periodically and the flange inspected for cracks.
Weld repairs can be made by depots if cracks radiate away from the frame; otherwise the mid-flange must be replaced. The latter is a very complex repair because of the amount of welding and heat treatment involved.
Case history #9. The combustible-gas detector alarm sounded on an LM2500 and the unit, running normally on an oil platform, shut down. Operating hours since COD totaled 122,000, 38,000 since the last overhaul. A 4-in. casing crack in the CRF was found during an inspection to determine the reason for the alarm. Such a crack was considered “out of character” by session participants. The exhaust diffuser was damaged as well.
There was no evidence of temperature rise or unusual vibration. Operations personnel had seen an increase in vibrations, but nothing excessive or over the limits. Experts believed the root cause was high-cycle fatigue and that the crack was probably propagating over time. Increased vigilance during inspections was recommended, but such cracks are difficult to see given all the piping on the engine. The NOx steam ring was removed and mounted off the engine with flexible steel-braided hose for steam delivery. No problems have been reported since.
Case history #10. A user reported several CRF fuel-nozzle pad cracks on a gas-fired unit equipped with steam injection. Crack repairs and replacement of rigid steam piping with appropriate steel-braided hose solved the problem.
Case history #11. One second-stage HPC turbine blade in each of nine compressor drivers (eight LM2500 DLE engines and one G4) owned by a pipeline operator suffered cracking in the dovetail section. This may sound statistically impossible, but it’s true. Owner thinks the cracking, which is under investigation, might be related to the wide range of ambient temperatures (-40F to 80F) experienced at each site. Some units are running with cracks but their propagation is closely monitored by regular inspection. The owner has installed HEPA filters and eliminated water washes.
Case history #12. Wear and tear of water injection nozzles for NOx control was raised as a concern. One user said he sent nozzles out for inspection and all failed; a second opinion from an alternative contractor said they all passed. Whom do you believe? It was said that the delivery time for replacement nozzles ordered through the OEM can take nine months.
Case history #13. An owner with LM2500+ DLE engines said a bolt from the inlet shroud on one machine got loose and wrecked the compressor. Some heat shields also were reported as “missing” and the melted remains found fused to first-stage nozzles in the HP turbine.
Case history #14. DLE combustor dome fretting was experienced on one unit and considered unrepairable. Root-cause investigation was ongoing at the time of the meeting. Investigators thought acoustic vibration might be the gremlin. They said fretting was associated with the older types of DLE combustors. One user in the group said in many cases a bad pre-mixer is the cause, but that the condition was not “normal.” Depot action is to repair or replace as necessary.
Case history #15. DLE heat shields experienced excessive TBC loss, exposing the base material. Condition is conducive to HPT damage and can cause a high temperature spread. Regularly inspect the combustor and replace if cracking of heat shields is identified. Depot suggestion was to keep acoustics low.
Case history #16. HPT first-stage nozzle platform oxidation was experienced on a unit equipped with water injection for NOx reduction. No coating was completely successful in preventing the oxidation, attributed to the higher heat rate consistent with water injection. Regular borescope inspection was suggested, with replacement of blades when necessary.
Case history #17. Breaking of the outer seals on HPT first-stage nozzles was attributed to high-cycle fatigue. This caused an increase in emissions during operation; damage was detected because of the associated temperature spread. Borescope inspection also can identify bad seals. The depot action is to rework or replace the nozzle.
Case history #18. Chip detector alarm in the lube-oil system warned of a TMF bearing failure. Depot found the bearing broken upon arrival at the shop. Debris was found in the pump strainer. Bearing was relatively new; engine had only 4000 operating hours. Contamination was suspected as the root cause based on finding machine chips in the C-sump.
Case history #19. Second-stage blades contacted the TMF multi-piece liner at some point between the 25,000- and 50,000-hr inspections. Original-style leaf seals liberated but this was not considered an issue. Users were reminded that the two-piece liner is meant to expand and contract different rates and this can cause binding. The action urged was to replace the two-piece liner with the one-piece liner/improved leaf springs as recommended by SB-229.
Case history #20. TMF liner rivets can potentially damage the HPT. During engine operation, thermal expansion/contraction cycles may cause rivet heads to liberate. Recommendation is to replace rivets with bolts (see SB-238). If you find five rivets in total, or two in one row, are missing, it’s important to switch to bolts as soon as possible. Replacement can be done in the field in a timely and cost-effective manner.
Case history #21. TMF cast cases have cracked on some units and the depots have replaced them with fabricated cases. This is recommended for engines still equipped with the original cast case. The job, which is expensive, can be done in the field, but it’s easier to do in a depot shop.
Case history #22. Water used for NOx reduction must be of high quality. Hot-section parts on one unit were damaged extensively by chemical attack. Spray nozzles had completely disintegrated. Engine operated for more than two years with poor-quality water; pH was out of limits.
The OEM’s Xtend™ hot-section kit for the LM2500 generated several minutes of discussion. Recall that Xtend contains advanced components developed for the LM2500+G4 and is said to double the lives of combustor and hot-section parts to 50,000 hours when dry gas fuel is burned. A depot representative said that there were 79 units operating with the Xtend upgrade, and some were beyond 50,000 service hours. Here are a couple of takeaways from the discussion:
- A user noted that first-stage nozzle burn was evident at 4500 hour and he did not expect to reach 50,000 hours.
- Nozzles and other components can be overhauled at 50,000 hours, but blades must be scrapped. The high operating temperatures are said to make the blade material brittle.
- An owner/operator asked, “If a LM2500 base engine were operating at its design temperature (lower than the +G4) with Xtend, could it go beyond 50,000 hours between overhauls?” Answer: No, for first-stage blades. Second-stage blades are on a case-by-case basis; some have achieved 75,000-hr intervals.
- Another participant asked if a base engine with an Xtend package could be operated in an under-fire condition. An OEM representative said the company was investigating if under-fire operation were appropriate. Reportedly, cracks found on one or more engines were believed a result of under-firing. Other users said they were running at half load without any issues.
Closely related to this discussion thread was mention of erosion on first-stage HPTR Xtend blades and nozzles on two engines—one with 4000 service hours, the other 7000. Units are close to the sea, burn oil, and use water for NOx control. Owner was told to continue operating and inspect regularly.
Critical-parts life management was another discussion subject. Users were made aware that tracking of parts life is their responsibility and that the information received from the tracking effort is essential for depot repairs. As noted earlier, Strategic Power Systems offers that service to LM owner/operators through its Cycles Tracking™ solution.
2. Conference at a glance
Information current as of January 1; verify at www.wtui.com
Sunday, March 23
Morning
8 to1 pm
Golf tournament, Escena Golf Club
11 to 2 pm
Tennis tournament, Plaza Racquet Club
Afternoon
2 to 7:30
Conference registration
3:30 to 5:30
New-user orientation/SPS introduction
5:30 to 8:30
Welcome hospitality reception
Monday, March 24
Morning
7 to 8
Breakfast
7 to 4 pm
Conference registration
8 to 5 pm
Exhibit hall open
8 to 9
General session
9 to 10:15
Depot presentations
9:30 to 3 pm
Spouse tour, Palm Springs Indian Canyons jeep excursion
10:15 to 10:30
GE Services presentation
10:30 to 10:45
Break
10:45 to noon Breakout sessions for LM2500, LM5000, LM6000, LMS100
Afternoon
Noon to 2:30
Lunch/exhibits
2:30 to 5:30
Breakout sessions for LM2500, LM5000, LM6000, LMS100
6:30 to 8:30
Monday night reception at Palm Springs Air Museum
Tuesday, March 25
Morning
7 to 8
Breakfast
7 to 4 pm
Conference registration
8 to 4:30 pm
Exhibit hall open
8 to 8:50
“Worldwide GT Business Update,” Mark Axford, Axford Consulting
9 to 10
Breakout sessions for LM2500, LM5000, LM6000, LMS100
10 to 10:30
Break
10:30 to noon
Breakout sessions for LM2500, LM5000, LM6000, LMS100
Afternoon
Noon to 3:30
Lunch/exhibits
3:30 to 4:30
“Fuel and Water Valve Maintenance,” Eric Freitag, Woodward Inc
“GHG Market Update,” Jackie Frelita, Elements Markets LLC
“HRSGs in Flexible Operation,” Ned Congdon, HRST Inc
4:30 to 5:30
“Analyzing Complex Vibration Issues,” Maki Onari and Bill Marscher, Mechanical Solutions Inc
“CO, NOx Emissions from LM Turbines,” Ted Heron, Environex Inc
“Control Loop Tuning,” Gary Drew, Metso Corp
Wednesday, March 26
Morning
7 to 8
Breakfast
8 to 10:30
Breakout sessions for LM2500, LM5000, LM6000, LMS100
10:30 to 10:45
Break
10:45 to 11:45
GE new products update
11:45 to noon
Wrap-up and adjourn
Afternoon
1:30 to 3:30
CPV Sentinel Energy Project tour. The 8 x 0 LMS100-powered peaking facility began supplying power to the grid May 16, 2013.
LM5000
Session chair and discussion leader for the LM5000 breakout sessions was Andrew Gundershaug, plant manager of Calpine Corp’s Solano Peakers; session secretary, Tom Christiansen, senior VP, Strategic Power Systems Inc. By show of hands, the majority of users present were from US plants; there was one attendee from Canada and one from South America.
The first of the five LM5000 technical sessions was conducted by Chris Martin of ANZGT and Thomas Benisch of MTU. It focused on issues that these independent depots have encountered on LM5000s recently. There are now 102 engines in the fleet, half STIG and half non-STIG. However, only 56 LM5000s are operating today; half of the remainder are listed as customer spares or GE lease engines.
LPC rotor was the subject of several depot findings, including the following:
- Disc corrosion and resulting seized/locked blades are conducive to vibration issues. Users were urged to review SL5000-09-002. Most engines experiencing corrosion are located on a platform, have fogging systems, or operate in a humid environment. Mitigation recommendations: Use correct water-wash procedures, remove zero-stage blades and clean/lubricate disk slots and blade roots. A similar, but more robust and lasting blade-care procedure is possible at a depot.
- Dealing with high run-outs and incorrect mating fits begins with an accurate vibration monitoring system to check shift and polarity of vibration. If vibration is stable, consistent, and repeatable, the site should consider field-balancing the engine—adding balancing weights under the cone.
- Imbalance is affected significantly by first-stage blade gaps, also by the zero-stage blade’s tang length (viewed back to front). The gap between the spinner and the blades is critical. If the spinner pushes on the blades, they may lock-up and wear prematurely.
- A coupling-nut incident caught many users by surprise. The nut on one engine split and let the LP shaft drop, causing significant internal damage to the unit. The root cause had not been determined at the time of the meeting, but professional opinion was leaning toward hydrogen embrittlement. Interestingly, the LM6000 fleet had experienced several coupling-nut events and migrated to a new design. For now, the experts recommend replacing the LM5000 coupling nut in-kind after each operating cycle.
LPC stator. Excessive fretting wear attributed to high vibration has been observed at the intersection of the third-stage case aft lip and fourth-stage case vane slot. No repair currently is noted in the IRM, but one is now available via CCR at GE authorized vendors. It reportedly will be added to the IRM in the future.
Front frame issues include these:
- Some No. 1 and No. 3 stationary air/oil seals are known to suffer Teflon seal delamination and resultant oil leakage. There is a service bulletin with a fix for the No. 1 seal, which users generally agree meets expectations. No SB yet for No. 3 seal. However, a similar issue on the LM6000 has been addressed effectively by replacing the Teflon seal strip with a metal/thermal spray repair. Depots recommend the Teflon alternative in the LM5000, at least for now.
- Cracking in front-frame weldment areas attributed to “web” remnants from the casting process has been an ongoing battle. There were several incidents in 2009-2010 and an effort was placed on “web” modification/rework that slowed the rate of cracking observed. No incidents observed by the depots in 2011, but three occurred in 2012. Cracks propagation is stopped by using a stop-drill procedure. Users are advised to discuss any cracks identified with the OEM or depot of choice and to inspect the cracks for growth once or twice annually.
- Fretting wear attributed to incorrect seating of the front frame with the air collector has been observed. Recommendations on torqueing and lubrication of bolts, plus other items, are presented in SB-212; increase in bolt size to accommodate higher torque values is discussed in SB-217. A user participant suggested an annual torque check. This involves breaking the lock wire on every bolt, re-torqueing, and installing new lock wire.
- Edge of the sheet-metal skirt sometimes is not machined to the proper limits along the full 360-deg interface, causing incorrect contact and wear. This issue has always existed, but only recently has correction been considered. This requires a one-time machining of the front frame.
HPC rotor issues observed by the depots include these:
- A fourth-stage blade event caused downstream damage. An investigation was ongoing at the time of the 2013 meeting. HPC stator hardware was found severely worn and dirty. Presenter stressed that the VSV hardware must be inspected and cleaned regularly.
A user suggested the following: Each VSV connection should be checked manually; if it wiggles, it is worn. The alternative to this relatively labor intensive task, he continued, is that the blades get off-schedule and the cost to correct that is higher than to keep the area clean in the first place.
- A 12th-stage blade went missing, causing both upstream and downstream damage; blade locking lugs were intact. However, the root cause will remain a mystery because the investigation at the depot was discontinued.
- High oil consumption, high vibration, and Teflon particles in filters add up to degraded O-ring seals that created a leakage path past the adapter retainer. A user suggested replacing seals every time you pull your booster onsite.
- Erosion was reported on the suction side of the mid-span damper, which is classified as a critical area in the IRM. The only known event of this type was found on a platform unit and is believed related to saltwater. Blades were blended to repair the pitted areas.
HPC stator issues focused on VSV hardware damage—including worn lever arm pins, worn pin holes, missing bushings, distorted lever arms, worn links, worn bearing holes and slots on the actuator brackets, and worn trunnion and bearings on the actuation beam. Such wear and tear often is the cause of a severe stall or full-load trip event because of the off-schedule condition. Users were urged to consult O&M manual GEK 72550, Chapter 5-3.11, and to replace all defective components.
Users offered the following advice:
- Perform a manual check of VSV hardware each time your unit comes off an operating run.
- Spray the outside of the VSV with an oil-cutting detergent, wash, and then steam clean. If necessary, use brushes to get the “tough stuff” off.
- Take a day every 18 months to disassemble and check and clean everything in this area. Unless you do this, the user said, you can’t be sure there’s no damage.
CRF wear and tear included the following:
- Cracking has been observed in the mid-flange bolt-hole tabs. Depot visits also have identified bolt-hole elongation to mid-flange, brackets, and stiffeners. Loose bolts in this section of the unit are relatively common. Experts recommended regular inspections for cracking and loose bolts. Interestingly, the depots have not found any flange cracks in the last three years on the LM5000 as they have on the LM2500 (see above).
- Broken bolts have been found on fuel-nozzle pads. One user said he believes at least some broken bolts can be attributed to technician inexperience. The nozzle sits at a slight angle, he continued, and novice techs sometimes break off the bolt heads because they are not properly aligned and too much force is applied. Experienced techs have much greater success. Another user reported that his plant requires all of these bolts to be sprayed with an anti-seize first then broken loose using a box wrench to eliminate excessive force. Once the bolt is loose, the techs can use a socket wrench to remove them.
- Fretting and wear have been observed on tube sleeves at the strut exit areas. Cracks also are in evidence on the oil and vent tubes. Inspect regularly. Consult SL 5000-06-01 regarding replacement of oil tubes. A point made during the discussion: If the B-sump pressurization line is cracked, C-sump temperatures will be 15 to 18 deg F higher than normal. Not everyone agreed. Some users with this problem have not seen a difference in temperature; others said they believed the temperature change was more likely on the supply line than on the sump line.
Combustor. Burning/erosion on the trumpet edges and the combustor dome between the trumpets is seen on 100% of the combustors at 25,000 hours, and at 15,000 hours or less for units running on liquid fuel or with NOx suppression. This is a continuing issue caused by insufficient or missing cooling air, malfunctioning or worn fuel nozzles, and combustor dynamics.
One user said his plant was running at maximum power and getting 50,000 hours on combustors and from 8000 to 12,000 hours on fuel nozzles. He made the following recommendations:
- Pull fuel nozzles as a set, recondition them, and flow-check every nozzle.
- Using a spec developed several years ago (it was handed out to participants and can be accessed by users through WTUI), ensure your fuel nozzles are in the lower one-third of the specification for steam flow and in the upper one-third in terms of fuel flow.
Keep in mind that every nozzle may pass the spec, but the set may vary widely across the spectrum of allowable values defined by the OEM. Tighter tolerances ensure that all nozzles in the set are consistent from a flow perspective, minimizing the probability of issues. A matched set of nozzles is critical for maximizing combustor and nozzle lifetimes.
HPT top issues included these:
- The dirt scoop associated with the first-stage nozzles surfaced as an issue for the first time in WTUI history at the 2013 meeting. This component, spot welded to the nozzle support during manufacture, is used in aircraft engines to filter out airborne particulates. While one could argue that LM2500s in generation service don’t fly and therefore don’t need a dirt scoop, its removal would alter engine design.
Most dirt scoops are found cracked during inspection/overhaul and cracks are not allowed in this area according to IRM guidelines. Experts said the pressure balance in the 4B bearing is impacted by cracking in the nozzle support area where the dirt scoop is located. Three incidents related to the failure of this component have been reported. The bottom line: Crack repair is much less costly than repairs associated with a pressure-balance failure at the 4B bearing.
- Air tubes (a/k/a spoolies), retainers, and washers often are found worn, broken, or missing during inspection. Fragments have been found inside nozzle segments. The damage is believed related to the temperature difference between cooling air and the nozzle, as well as vibration. Users engaged in a brief discussion on the subject noting that even when air tubes are broken they cannot migrate and cause additional damage.
LPT stator discussion focused on case cracking and inner seal wear.
- Axial case cracking has been found during depot inspections, with severe axial cracks observed on the TMF/LPTS flange seal. Because these cracks can be seen only after the LPT stator has been removed, they are thought to be heating/cooling related. There was only one event in 2012, but there were 14 axial cracks on the LPTS. Nozzles were removed to inspect further and the cracks were found to propagate circumferentially. They were outside IRM limits at the time and could not be repaired. A repair has since been developed.
A user mentioned that the metal in his plant’s turbine cases could no longer be repaired because of the number of heating/cooling cycles experienced. Welding was tried, but it just spider-webbed everywhere. The cases had to be re-skinned.
- Wear/grooving was noted on the inner seal. This can adversely impact cooling and may lead to TMF cracking. OEM instructions say no wear is allowed on the 10-14 spool-shaft configuration seals.
LM6000
Session chair and discussion leader for the LM6000 breakout sessions was David Merritt, deputy general manager of power operations for Kings River Conservation District; session secretary was Steven Giaquinto of Strategic Power Systems Inc. Depot presentations were made by TCT, IHI, and MTU. The LM6000 fleet now has more than 1000 engines in service, about three-quarters of those equipped with conventional SAC combustion systems, the remainder DLE.
This was Merritt’s first year at the helm of the LM6000 track. He will not be at the front of the room in 2014 having been elected a vice president of WTUI (refer back to Sidebar 1). Andrew Gundershaug, plant manager of Calpine Corp’s Solano Peakers, will have the gavel this year. He moves up from the LM5000 breakout, his position there filled by Perry Leslie of Wellhead Electric Co’s Yuba City Cogeneration Plant.
A great deal of material was reviewed/discussed during the LM6000 breakout sessions. Some of the topics that generated significant interest include the four identified immediately below:
No. 2R/No. 3R bearing. The root-cause analysis of an inlet gearbox failure on one unit that resulted in oil starvation at the No. 2R/No. 3R bearing was underway at the time of the meeting; first educated guess placed blame on a failed oil supply tube. Bearing surfaces revealed high-temperature discoloration.
Users asked the depot representative how you identify an issue in this area. Response: It’s a tough one and very difficult to monitor by temperature, so look for other signs. The first sign typically is from the chip detector. Also, look for leaks at weep holes, look for wetting, look for oil coming out of the bushings, look at the AGB boot.
Sprint® nozzle tip-shroud erosion in the extreme can surface after only 5000 hours of operation and possibly initiate an HPC event. One incident discussed was thought caused by the wrong droplet size and/or amount of water. Attendees were reminded to verify the recommended calibrations of their water control valves; also, to check the condition of Sprint nozzles during semiannual inspections and overhaul the nozzles at every hot-section or major overhaul.
Compressor bleed-valve durability received significant air time. Currently, Honeywell International Inc is the only supplier for this component; it also has the only approved repair facility. Experience reveals that valves sometimes are being replaced at less than the 10,000 operating hours expected. Reasons include positioning errors from misaligned shafts caused by bearing failures or bushing wear, bearing failures attributed to poorly distributed loading, oil leakage caused by wear on actuator seals, feedback errors, etc. Recommendations made by the depots: Make use of the rotable valve pool to reduce outage time and implement the software change recommended by SB-217 to reduce valve movement. Longer-term, alternative repair options are being evaluated and an improved valve design is scheduled for release next year.
The value of a multi-dimensional user group meeting, such as that conducted by WTUI, is that presentations and discussions identify issues that users might want to know more about and answers sometimes can be found in the exhibit hall.
Serendipitously, the editors stopped at A & I Accessory Ltd’s booth and learned that its engineers had analyzed the root causes of the most common causes of premature bleed-valve failure and had developed what they consider a better bearing for the service—one with increased load-bearing capability and improved durability in the high-temperature service environment. Other enhancements were mentioned as well—all aimed at extended service life. Company representatives also mentioned that A & I offers a rotable exchange program of its own.
Several instances of oil leakage associated with the compressor rear frame were reported with the number of events growing annually—nine in 2012. In three instances, engine removals were warranted. Distortion of the J clamp was the root cause. More specifically, the P clamp bolted to the brazed J clamp “walks” on the wear sleeve, bending the J clamp while doing so. The “walking” was attributed to tube vibration combined with thermal expansion/contraction. Compliance with SB-236 was a suggested solution.
The three depot presenters divided up the published breakout notes that they had helped to prepare and ran through the highlights, taking questions along the way. The following bullet points identify the topics discussed. WTUI members can get more detail in the closed user-only section at www.wtui.com.
- Broken rear bolt on air collector. Look, in particular, at bolts near the 6 o’clock position where stress is highest.
- VBV actuation system failure investigation revealed that when the hinge gets loose, the door can’t close correctly.
- HPT stator impingement-ring spoolie wear typically is associated with high-time engines.
- LPT first-stage nozzle burning and cracking has been observed. Check SB-255 and SB-273. Use of a thermal barrier coating helps mitigate the cracking issue. It was mentioned that owners will be able to purchase coated LPT modules in the future.
- T48 sensor failure is addressed in SB-230. Instruments from one of the two suppliers of the T48 are considered less reliable than the other. Consult the SPS notes on the WTUI website.
- DLE combustor heat-shield separation caused downstream damage but engine trending data revealed no performance loss.
- XNSD speed-sensor failures caused by erratic or lost signals. Causes reported include poor electrical connection between the XNSD sensor and the LP turbine speed electrical harness. Improvements suggested by the OEM are included in SB-262.
- LPC disc corrosion. In general, be sure to dry out your engine before shutting down after a water wash. Note, too, some S0 and S1 discs have been scrapped at the first overhaul because of bolt-hole corrosion and surface pitting. In the near term, recommended graphite grease for coating bolts should be used only on threads because of the product’s strong correlation to galvanic corrosion. Engineering investigations continue.
- Avoiding HP compressor blade events—those caused primarily by FOD/DOD impacts and dovetail separations—usually can be avoided by adhering to recommended O&M practices.
- HPT first-stage shroud distress was identified on units at 6000 and 12,000 hours after hot sections. They were termed “strange” by the depot rep presenting. No conclusions were available at the time of the meeting. Interestingly, a user participant said, “We had this, too.” The cause in his case was that the seal between the shrouds burned.
- HPT second-stage nozzles that had experienced issues and were improved by following the recommendations of SB-238 were said to have been in excellent condition during a shop visit. This led the depot to conclude that SB-238 was a good investment.
- LPT case rail wear can’t be found during a borescope inspection, according to a depot rep. Depots are reporting many incidences, across all engine applications, of second-stage nozzles sagging into the case, caused either by rail wear or shifting shrouds. However, the issue is not as prevalent in the DLE fleet as in the SAC fleet. Repair is not simple if needed; you have to cut the CRF and re-weld it.
- Despite the educational effort, only about one-quarter of the attendees are currently tracking critical parts. However, while slow, progress is being made: Five or six years ago when the requirement was introduced, no one was monitoring critical parts. This program is particularly important for this engine at this time, because depots report scrapping parts because of cycles. Life limits help protect both personnel and the integrity of the engine.
LMS100
Session chair and discussion leader for the LMS100 sessions was Don Haines, plant manager, Panoche Energy Center, Firebaugh, Calif; session secretaries (note-takers) were Sal and Tripp DellaVilla of Strategic Power Systems Inc.
In his opening remarks, Haines said that the LMS100 operating fleet size had nearly doubled since the 2012 meeting, with fewer major issues being experienced. He then stressed the strong commitment LMS100 owner/operators have for information-sharing; its goal is continuous performance improvement across each plant and the overall fleet. To support this commitment, the group has established and strongly endorses the following forums:
- Users group conference call on the first Wednesday of every month at 1 pm Pacific. Contact Haines via www.wtui.com for details.
- Yahoo LMS100 Users Group, facilitated by SPS, to stay current on the various technical and logistical issues faced by owner/operators.
At the time of the 2013 meeting, 28 LMS100 units were in commercial operation; another 23 in the installation/commissioning phase. Of the latter, 19 are located at three sites in California. A tour on the last day of the 2014 meeting will be conducted at one of those facilities—the 800-MW, eight-unit CPV Sentinel Energy Project, located only five miles northwest of Palm Springs.
The high-time LMS100 engine has logged more than 30,000 service hours. Starting reliability for the fleet is nearly 99% according to ORAP data, based on information submitted for more than 80% of the engines.
A big difference between the LMS100 sessions and those for the other GE aeros was that there was no depot involvement. The OEM has staffed up and invested in tooling and facilities to handle the service requirements of this fleet. GE’s status update on product improvement plans focused on the following issues:
- HPC first-stage mid-span shroud wear.
- HPC VSV system wear.
- SAC combustor durability.
- HPT first-stage blades.
- HPT second-stage nozzles.
- IPT strut tubes.
In addition to the GE presentations and open discussion forums, there were was a presentation on battery chargers by Sam Ayoubi of Alpha Technologies Inc, Bellingham, Wash, (available at www.wtui.com) and one on the Bently Nevada vibration system designed for the LMS100 by GE’s William Trevino. CCJ
3. Acronyms to remember
AGB—Accessory gearbox (also called the transfer gearbox)
AVR—Automatic voltage regulator
CCM—Condition maintenance manual
CCR—Customized customer repair
CDP—Compressor discharge port
CFF—Compressor front frame
COD—Commercial operating date
CPLM—Critical-parts life management
CRF—Compressor rear frame
CWC—Customer web center (GE)
DEL—Deleted part
DLE—Dry, low emissions combustor
DOD—Domestic object damage
EM—Engine manual
FFA—Front frame assembly
FOD—Foreign object damage
FPI—Fluorescent penetrant inspection
FSNL—Full speed, no load
GG—Gas generator (consists of the compressor and hot sections only)
GT—Gas turbine (consists of the gas generator pieces with the power turbine attached)
HCF—High-cycle fatigue
HGP—Hot gas path
HPC—High-pressure compressor
HPCR—High-pressure compressor rotor
HPCS—High-pressure compressor stator
HPT—High-pressure turbine
HPTN—High-pressure turbine nozzle
HPTR—High-pressure turbine rotor
IGB—Inlet gearbox
IGV—Inlet guide vane
IPT—Intermediate-pressure turbine (LMS100)
IRM—Industrial repair manual
LM—Land and marine
LCF—Low-cycle fatigue
LO—Lube oil
LPC—Low-pressure compressor (not on LM2500; just LM5000 and LM6000)
LPCR—Low-pressure compressor rotor
LPCS—Low-pressure compressor stator
LPT—Low-pressure turbine
LPTR—Low-pressure turbine rotor
LPTS—Low-pressure turbine stator
NGV—Nozzle guide vane
OEM—Original equipment manufacturer
PN—Part number