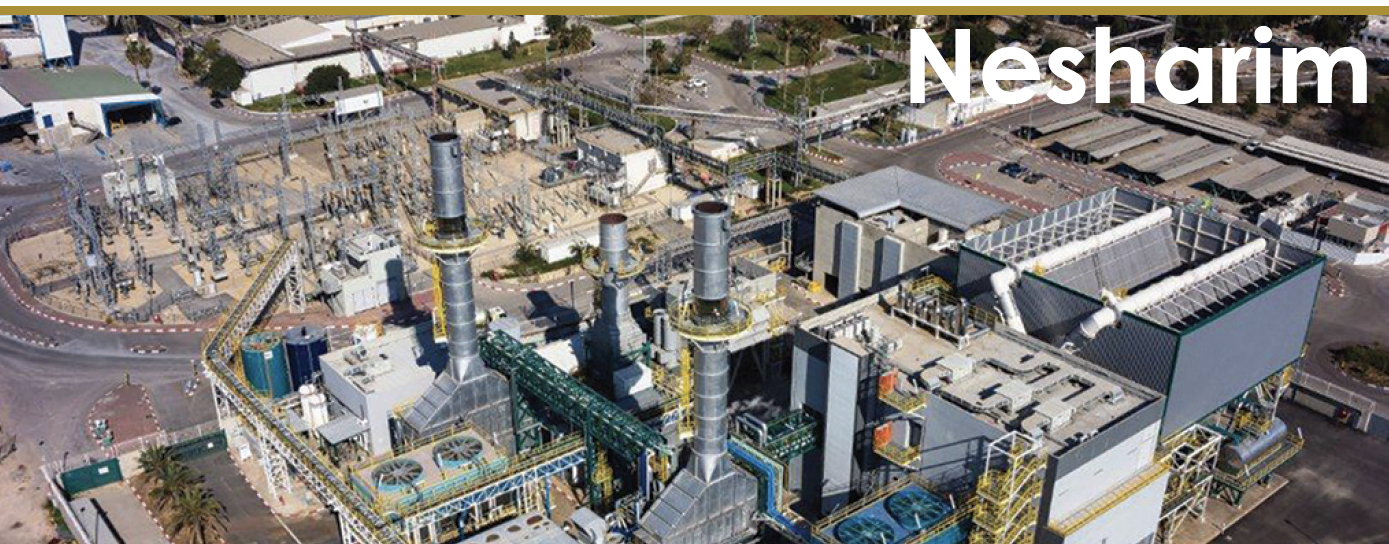
Nesharim Leading Energy
Owned by Clal Industries
Operated by Mashav Initiating and Development
120-MW, gas-fired, 2 × 1 combined cycle located in Ramla, Israel
Plant manager: Kobi Ivenshitz
Insulating filter house roof conserves energy
Challenge. Nesharim’s filter house is installed over its gas turbines and doubles as a roof for the units. The upper portion of the sheet-metal structure is exposed to the sun’s radiation. An electric chiller is used to cool turbine inlet air to 46F the entire year. In summer, solar radiation heats up the filter house to more than 130F, resulting in a loss of cooling energy and a loss of power produced by the turbines.
Solution. A nano-ceramic insulation—in effect, a 0.2-in.-thick coating of “paint”— was applied as a fine layer on top of the cooling area, on the entire upper surface and side walls. By insulating surfaces exposed to the sun’s radiation, less energy is required for cooling inlet air, and air that has been cooled is not reheated by the sun. This fix has increased power generation and reduced parasitic power consumption. Thus turbine efficiency has increased.
Results:
- When comparing the chillers under identical ambient temperature/humidity conditions before and after the insulation was applied, there is a saving of about 60 kW per hour in chiller energy consumption, and a decrease in the inlet air temperature at the turbine entrance of about 3.6 deg
- The chiller’s ability to reduce air inlet temperature is improved and its response time to changes in ambient humidity and temperature is
- The insulation provides an additional layer of protection from corrosion and water penetration into the filter
Project participant: Kobi Ivenshitz, plant manager
Reducing offline water-wash time for gas turbines
Challenge. Compressors are water-washed monthly as part of the plant’s gas-turbine maintenance program and to maintain maximum output. During the offline wash there is a loss in production time of about eight hours, reducing turbine availability by about 1%. The water-wash process involves eight washes of water together with detergent. During the first two wash cycles, the fluid is heated to about 165F. The plant was commissioned with only one wash-water tank, so it took time to warm the water for the second hot wash.
Solution. Plant duplicated the original wash-water tank and added the second tank in series with the first (photo). With this improvement, heating is carried out in the two tanks simultaneously, thereby saving a few hours. In addition, the OEM’s software was modified to shorten ineffective processes, which saved more time.
Results. This improvement has reduced the offline water-wash time by about half, allowing a faster return to production. The second tank heats the water for the second cycle before and during the first cycle, enabling the second rinse cycle to begin just a few minutes after the first rinse ends. Previously there was a waiting period of two and a half hours. The benefits:
- Rinse time reduced from eight hours to four (breaker to breaker).
- Turbine availability increased by 36 hours
Project participant: Kobi Ivenshitz, plant manager
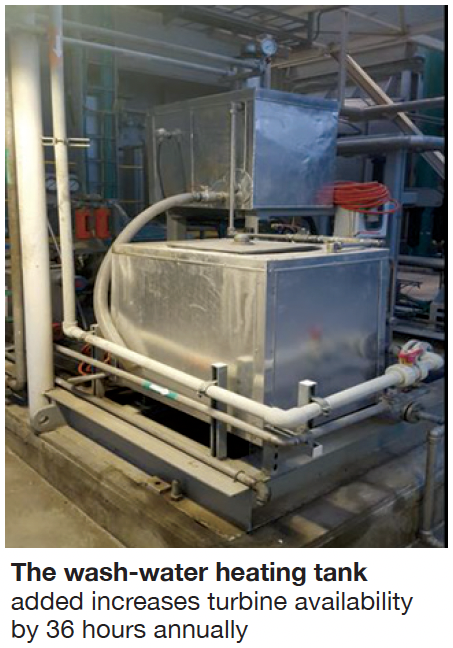