Revised “close-call” program improves safety
Rathdrum Power Plant
Owned by Rathdrum Power LLC
Managed by Power Plant Management Services LLC, Operated by NAES Corp
275-MW, gas-fired, combined cycle located in Rathdrum, Idaho
Plant manager: Gary Allard
Key project participants: Dale Miller, compliance supervisor Rusty Whiteley, division director Alan Bull, project manager, Entire Rathdrum staff
Challenge.
Rathdrum Power Plantis an OSHA VPP site that experiencesvery few accidents. Even still, nearmissevents were not always beingreported. Only one near-miss eventwas reported in 2008, none in 2009.
The near miss event that occurredin 2008 happened while plant staffwas lifting a turbine coupling guardwith a crane. The rigging caught on afire protection pipe that was mounted directly over the coupling, and then the mounting bracket clamp holding the pipe pulled free and the pipe broke. The clamp that pulled free struck an employee on the chest, hard hat, and safety glasses. The employee’s shirt pocket was torn and the employee received a small abrasion on the face. Luckily, no medical attention was required.
This was a potentially very serious accident, and the near miss was recorded. The near-miss programthat was in place during 2008 and2009 was a complex electronic reportingsystem that discouraged the input of less serious events and issues. The purpose of any near-miss program is to prevent accidents and other recordable incidents.
Solution.
To improve near-miss reporting, compliance supervisor Dale Miller revised the near-miss program in 2010 to encourage safer working conditions at the plant. As pointed out by a former OSHA VPP inspector, near-miss events can be successfully used to measure unsafe conditions at the plant and to make improvements. First, the electronic near-miss program was replaced with a manual, anonymous close-call program. This way, plant staff can report anything that appears to be of concern simply by filling out a ‘close-call card’ (Fig 49), and anonymously placing it in the nearest ‘close-call box’ (Fig 50).
The card openly states: “Please no names, just explain what happened so others will know how to prevent a repeat close call or better yet prevent an accident.” There isn’t even any requirement to be an actual near miss. The plant safety motto is also printed on each card: “Don’t Learn Safety by Accident.”
Second, a graphic “near miss” photograph or illustration was placed above each close-call box to encourage the use of the close-call cards and program. The close-call boxes are located throughout the plant for easy access.
Third, Miller collects the cards and the plant safety committee reviews each one to determine if the report is indeed a near miss. For each near miss, the committee then submits a near-miss report and takes the necessary action to mitigate the near-miss potential. This may require training, hiring a vendor to provide onsite inspections and corrections, or simply a reminder at a regularly scheduled safety meeting.
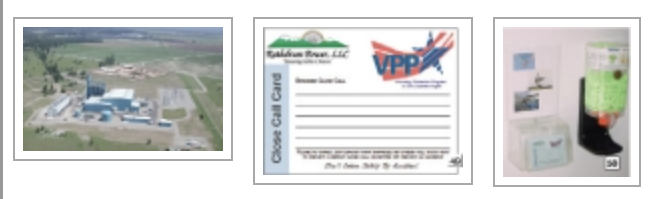
Results.
During 2010, a vast improvement in the program was noticed; 11 close calls were reported. Every close call was investigated, and appropriate action was taken in each case. Not only has plant safety improved, but employees have enthusiastically embraced the revised program because of its ease of use and anonymity. Here are some examples of near misses and actions taken at Rathdrum:
- An employee caught a foot on the stairs and fell forward onto his hands, but sustained no injuries. This was used as a safety awareness topic.
- While sliding a heavy box across the floor with a toe, the employee felt stress in the back and stopped, realizing how close they had come to an injury. This topic was used at a safety meeting wherein an expert doctor on back injuries was invited onsite to train employees on back safety and proper lifting techniques.
- An employee observed what he thought were protruding steel deck grading joints, presenting potential fall hazards. After an investigation, it was determined to be a normal condition that presented no real trip hazard.
- When opening a cabinet to take readings from gages located in the cabinet, an employee almost slammed the door on his hand. This was discussed, and it was determined that no real solution was required. Employee safety awareness and care was stressed.
- A delivery truck making a U-turn on the plant site struck a garbage dumpster, moving a Jersey wall 12 in. This near miss was reviewed by plant personnel, and it was agreed that plant staff must provide a spotter for trucks while they maneuver onsite.
- An employee noticed a dripping valve on a chemical delivery truck during a transfer of aqueous ammonia. The delivery was shut down, and the valve was examined. It was discovered that the valve was improperly assembled and could have easily blown out causing a reportable issue. Fortunately, the quick call by the employee prevented this from happening.
- An employee pushed a button to open a large roll-up door, and a wire from the safety strip located at the bottom of the door struck him in the face. The employee was not injured. Later it was discovered that the wire was energized. All door strips were inspected and replaced with a pneumatic system.
- During a “permit-required confined space entry,” the door watch noticed small spikes of carbon monoxide on the meter, and reported it. The job was shut down, and staff discovered that gas-fired welding machines located nearby were the source of the CO. The welding machines were relocated, and the CO problem was resolved.
- An employee observed a subcontractor building a block wall onsite without proper footwear. The job was shut down, and it was discovered that the subcontractor had not received orientation to the plant safety programs.