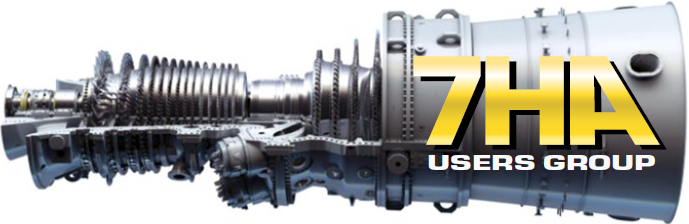
Now in its second year, the 7HA Users Group Conference fosters an open and transparent dialogue among users and the OEM on all aspects of the turbine, so that technical issues can be resolved and best practices shared. Because the 7HA fleet is relatively young, the user group’s steering committee has structured the event to drive strong collaboration with the OEM. For example, this year’s meeting, held in Greenville, SC, August 26–28, included tours of GE’s facilities and a social event for informal user/OEM interaction.
The first day is an open, user-only forum among the fleet leaders and others operating units, as well as users in the installation and commissioning phases. Newer users learn from more experienced HA site representatives.
The agenda for the second day, GE Day, is developed by the steering committee and GE, and covers technical issues, root-cause investigations, solutions for resolving open issues, updates on HA fleet statistics, operating modes, and field performance.
The 7HA community also hosts quarterly webinars to share updates throughout the year.
The steering committee was especially gratified by the overall growth in attendance and greater international participation as new 7HA user sites are added throughout the world. Present at the conference were representatives from five 1 × 1 combined cycles (CC), six 2 × 1 CCs, two 3 × 1 CCs (both outside the US), and one simple-cycle installation representing the first facility with hot selective catalytic reduction. The simple-cycle unit is currently the only one of its type worldwide.
The 60-Hz fleet leader had 17,217 total fired hours at the time of the conference, the 50-Hz leader 20,000+, as well as 340 factored starts. Although the latter site reported numerous trips, it was not possible to distinguish between customer-driven trips and machine-related ones.
GE reported the second day that it had secured orders for 96 HA units, 59 had been shipped, 40+ commissioned, and 39 had achieved commercial operation. By the time of this writing, the order number had grown to 100.
Although forums such as this focus on resolving issues, it is important to remember that the HA machine is breaking records for performance in terms of start times, turndown, output, efficiency, ramp rates, and emissions.
Progress abounds. For reference and context, a review of last year’s report on the inaugural 7HA Users Group conference is necessary, especially around four issues: first-stage bucket (S1B), axial fuel staging (AFS), train vibration, and control hardware and software—especially thermocouples.
Users at this year’s conference added only one significant failure event involving the generator (and a lengthy outage), although it should be noted this is not drive-train related.
Fortunately, based on the 2019 presentations, the AFS failure event appears to be specific to “cold-fuel/ high-starts” CC units and simple-cycle machines (which likely would be in peaking service with high starts), of which there are only a few; the S1B issue appears to be under control, at the time of this writing; and a new thermocouple design, being validated at one user site, seems to be working out, based on initial reports.
As shown below, hardware and control issues persist but these are hardly of the same pedigree because it’s the drive train components which represent the most advanced technology.
Given historical patterns in commercializing advanced gas-turbine technology, this is, actually, good news. Fleet leaders have a year’s worth of additional factored fired hours (FFH) and starts (FFS) and more machines have been commissioned.
But there’s no resting on laurels yet. One nagging conclusion from the “GE Day” portion of the conference (see companion article): The excessive start-to-start vibration issue, which clearly contributes to other O&M issues, is still proceeding towards a thorough root-cause analysis (RCA).
GE experts have identified a primary factor and corrective action for excessive and inconsistent start-to-start vibration, but are still investigating secondary factors. The good news is that when the vibration issue is resolved, other issues may be correspondingly eliminated or reduced in severity.
Users also have observed “distress” at the trailing edge of the first-stage nozzle (S1N), although no “events” have been associated with it.
Several issues with non-drive-train components appear to be rooted in process/organizational gaps between GE, its sub-vendors, and the EPC, though that gives users little comfort. They just want the responsible party to get them back on-line as quickly as possible. Another broad theme from the presented material: Many other technical issues are lacking satisfactory RCA-based explanations.
Other sub-systems, most notably exhaust assemblies and critical valves, are exhibiting technical issues common to multiple users. Keep in mind that non-drive-type issues are common to, and consistent with, most other advanced gas-turbine facilities since the beginning of the “boom period” in the 1990s.
S1B status. Only one site represented at the conference was still operating with the original S1Bs, which the OEM restricted to 6500 FFH; all others have the Gen II S1B replacing the original buckets, or units shipped with the new ones. By contrast, in one 7HA unit, the new buckets have exhibited “no issues during operation,” and will be thoroughly inspected this month after around 6700 FFH. These airfoils will be removed from service and tested; the user community is watching this development closely.
Explanations from GE for the active cracks resulting from the internal oxidation at the shank level “are varied,” according to users.
Start-to-start vibrations. S1B failures aside, the start-to-start train vibration issues may be more insidious. First, they contribute, even if not directly correlated, to less dramatic but still nagging problems which cause unit trips. Second, the OEM has not offered a full RCA explanation. A new load coupling is being tested and validated at a user site to help correct the vibration issue, but no word yet on results. Third, users report there is little consistency in the vibration measurement variations from start to start.
Counter-balancing this reporting, some users noted privately that units experiencing relatively normal vibration levels still exhibit many of the associated issues.
One 9HA user said “the explanation is not yet satisfactory” and the first fix, replacing an inlet plenum cone with a stiffer one, showed a net improvement but still “isn’t good enough.” Vibration is below the alarm point but still significantly higher than expected. The OEM is now “acting on the rotor mass balance to modify rotor excitations at this site.”
Several 7HA users listed some of the secondary consequences of machine vibration: loose wiring in electrical and control cabinets, structural cracks, cut wiring where wiring makes sharp turns against aluminum housing, trips on compressor bypass valves, failures with exhaust thermocouples, fire-protection water-mist nozzles detaching, and generator fixator torque issues.
One user reported that the OEM would soon be coming out with a GEK document addressing vibration through modifications to foundations.
Generator failure. The 2 × 1 CC site which experienced the generator failure on one unit after 8500+ FFH and 105 starts reported that an arc flash occurred at the collector prior to the failure, and endwinding dusting and loose ties observed at this time were addressed. A MAGIC (miniature air gap inspection crawler) inspection had been conducted before the failure. The unit that failed exhibited the least amount of endwinding dust.
There were no leading indicators or alarms prior to the failure, and other users noted privately that the failure may be specific to this model number and/or site.
The site rep asked rhetorically, was it mis-operation, improper reassembly, the fact that the OEM does not do a “bump” test” (frequency response testing on the stator endwindings), out-of-synch phase, or the significantly reduced number of collector brushes recommended by the OEM? The site is still proceeding through the RCA with the OEM, which reportedly had validated the auto-sync process during commissioning.
The generator in question is a 2016-vintage “leads up” with the three phases coming off the top of the unit.
AFS, combustor hardware. GE issued a Technical Information Letter (TIL) on the AFS indicating that cold-fuel/high-start machines are most affected. Cold fuel in this case refers to 80F-120F, although the term can refer to temperatures less than 300F. Two machines at the same site experienced forced outages caused by failure of the AFS fuel delivery pipes.
Modifications for the one site experiencing the most severe AFS failure included a change to a welded design for attaching fuel tubes to the “unibody.” The TIL recommends fuel gas leak detection and haz-gas detectors to indicate an imminent failure situation. One plant is validating the TIL recommendations.
A 9HA site reported issues with fuel nozzles, effusion plate, combustor liner, and the transition piece. The effusion plate cap parts “have been modified because of cracks and liberated pins” and the new design has shown “pretty satisfactory experience” after one year of operation. Cracks have been observed on liners but this was thought to be less of a forced-outage risk.
More than one site has observed spallation on the combustor unibody component. A user reported observing cracks in the transition pieces on the cold side, and a crack at the frame weld on the cold side, of the compressor outlet. This was labeled by the user as “a design flaw, aggravated by abnormal vibration and combustion dynamics.” The user commented about now suspecting the durability of the combustor generally.
Initial, final control elements. Many users are experiencing nagging issues with digital valve positioners (DVP), especially on fuel-gas valves, but also on other critical valves and inlet guide vanes. One user attributed six unit trips to the DVP issue. Several attendees clearly noted that high start-to-start vibrations contribute to the problem. They also noted that each valve has its own configuration.
What appears to be occurring at some sites is that the vibration causes problems with signals and connections, the unit trips, and then site personnel have difficulty performing the online diagnostics. OEM responses to site inquiries involve long lead times, mostly because this is sub-supplied equipment. For one thing, hardware and software reportedly can’t be obtained directly from the hardware supplier, which is responsible for programming of the software while GE is responsible for the valve and its performance, which is proprietary (though a common practice among turbine OEMs).
Another issue across several sites involves temperature control of the fuel-gas DVPs, which are sensitive to extraneous sources of heat. One 9HA site provided details of a forced outage caused by multiple electric gas-control-valve (eGCV) failures. Subsequent analysis upon disassembly showed a powdered metal deposit at the gap between the valve spring seat and shaft resolver link (which provides valve position feedback to the actuator drive), heavy wear of the anti-rotating bearing slot, and coupling-shaft damage (a shaft screw loosened and dropped out).
Oddly, similar symptoms have been observed with other eGCVs at the site, but no symptoms have been observed at this owner/operator’s other sites with similar valves. After this presentation, a user noted from the audience that they had replaced a GCV because motor amps had spiked up to 30-40 amps and the motor was overheating. Operators noted a gas-valve position deviation alarm, which was supposed to fail the valve closed, but instead was observed to be 29% open at shutdown.
The RCA on the matter continues but the cause of the wear is still not known. DVP failures were noted in last year’s conference report.
The story with the GT exhaust thermocouples (TC), also a source of copious discussion last year, is a bit cheerier. One user reported that exhaust TCs broke 11 times in 16 months. Two other sites are now testing the OEM’s upgraded TCs; one noted it has 12 of the new ones installed and they “have been successful so far.”
Exhaust sub-systems. Several users reported “excessive leakage” at the hot gas expansion joint between the exhaust diffuser and the casing. One site implemented the OEM’s new design in October 2018, which was then “corrected” in May 2019. “Long-term reliability needs to be confirmed,” he said.
Another user reported on exhaust-casing insulation defects observed after a full-speed/no-load (FSNL) test. Multiple insulation panel cover plates and washers detached, damaging several of the plates.
Gas leakage in this area also is causing the malfunction of nearby equipment—such as fieldbus cables, cooling-fan cables, and haz-gas detectors.
Myriad other issues. Users brought up a laundry list of control-system issues—including the integrity of flame detectors and combustion dynamics monitoring probes; problems with fieldbus connectors, device ID tags, and communications; and having to add and troubleshoot software logic. Likewise, a punch list of issues were raised with ancillary components like cranes, seals, DC system ratings, igniters and cables, fuel-gas heater, static-starter controllers, a variety of valves, complex insulation arrangements, and several more.
However, while there were detailed discussions around some of these topics, they tend to be one-offs and/or common to installation and commissioning experiences generally.
People and process issues. One reason users groups are invaluable is the collective leverage they provide for users to work more knowledgeably with their suppliers. They also are good reminders that not all root causes are technical in nature.
A user nearing the commissioning of new HA machines reviewed what was discovered during their oversight activities. This owner/operator hired third-party quality inspectors to review things onsite.
One overarching concern was that the OEM has what’s known as “free release” with its sub-vendors. As an example of a consequence, “we won’t have a true history of where our compressor blades come from.” There was general agreement that the OEM needs to improve sub-supplier quality assurance/quality control.
At least one user present intimated that the OEM’s quality processes may not be good enough, and that others should distinguish between parts for which GE does receive complete quality support documentation and those for which the OEM does not.
Seams issues between EPC and OEM also need attention and require diligence and a high level of owner/operator engagement.
One example involves critical valves; a user insisted that “you have to force GE to deliver quality.” Another user outside the US mentioned “many issues with other auxiliaries,” and that working with GE was “difficult.” A third mentioned that “GE does a terrible job with report writing.” A fourth noted that “communications between the OEM and EPC are lacking.” Finally, a fifth exclaimed that, when it comes to work under warranty, “the GE people for the non-GT part of the plant are inadequate.”
Get engaged—early and often. A variant of the old slogan about voting in Chicago applies here. Prospective users and those with units coming on-line or on order are urged to participate in the user-group activities as early as possible and begin developing your own comprehensive checklists for repeated review among owner/operator staff, OEM, EPC, and subsystem suppliers. As one user said, “it’s good to learn from experience, but better to learn from others’ experiences.”