LOTO system improvements
Blackhawk Station
Owned by Borger EnergyAssociates LP, Operated by NAES Corp
230-MW, gas-fired, 2 × 1 combined-cycle cogeneration facility located in Borger, Tex
Plant manager: Craig Courter
Key project participants: Steve Nelson, operations supervisor; Bryan Stout, maintenance supervisor; Alan Bull, project manager
Challenge.
Blackhawk Station’s LOTO system was very time consuming and cumbersome. The system had very little congruency between shifts because the paperwork and tagging were performed manually. The system utilized lock boxes that were hard to keep maintained in an organized manner and created other issues with identifying which system was assigned to boxes during large scale outages.
Solution.
Steve Nelson, operations supervisor, noticed immediately when he started at Blackhawk that an excessive amount of time and energy was being spent on the LOTO program. The LOTO system being used employed the use of the red lock boxes and a ring full of locks and keys (no locks keyed alike). The outside operator would take his ring of keys and fumble through each one for each lock in the field. The red lock boxes would be piled on a desk in the control room and were very cumbersome to work with.
Nelson redesigned the LOTO program to avoid the pitfalls associated with individual lock boxes. The cabinet he built kept all the lockboxes in one location (Fig 81). The lock out cabinet was equipped with lock sets from six locks to 20. The individual lock sets are keyed alike, eliminating the wasted time operators would spend trying to match keys to locks in the field. Next step was to automate the tagging system.
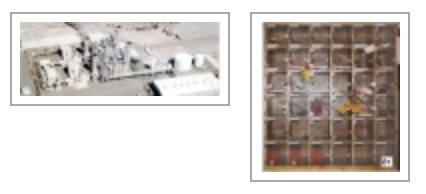
The legacy system at Blackhawk required every LOTO to be hand-written, which was tedious and time-consuming. Using the same format as the handwritten LOTO, he copied each LOTO from the LOTO history to an Excel® spreadsheet. The operator writing a LOTO now chooses the equipment to be locked out from a list, then inputs the data required on a cover page.
A “tag” page was then designed and formatted to pull data from the cover page. Once all the information is input into the cover page the operator can print to a printer dedicated to the LOTO program. The cover page will print first. Then the operator inserts a tag sheet and hits print again and the tags are printed on the tag sticker sheet. The tags can now be peeled off the sheet and attached to tags to be hung in the field.
Results.
The system has proven effective not only in time saving but also in congruency of the LOTO program. Nelson works closely with the O&M staff to ensure that proper procedures are followed and all isolation is done in accordance with corporate procedures. The system locking procedures are identified and reviewed by several team members and then documented in the Excel® spreadsheet creating a valuable database for future use.