7F users weather a blizzard of information; Fuselier elected chairman
The first full day of the 7F Users Group’s 2013 Conference, started on the double-quick and maintained that pace until the final bell. Chairman Sam Graham, maintenance manager at Tenaska Virginia Generating Station, cracked the whip on a user-only morning session that featured six content-rich compressor-section presentations and a lively open discussion on safety. The meeting broke precisely at noon and resumed 60 minutes later (Graham is navy punctual) with sessions on controls and auxiliaries. Vendor presentations followed the user-only portion of the program and they concluded a couple of minutes before the three-hour vendor fair opened at 5:30.
Steering committee, 2013-14
Chairman: Ed Fuselier, Direct Energy
Vice Chairman: Richard Clark, SCE
Treasurer: Peter So, Calpine Corp
Jeff Gillis, ExxonMobil Chemical
Sam Graham, Tenaska Inc
Art Hamilton, Calpine Corp
Robert Holm, Occidental Chemical Corp
Robert LaRoche, SRP
Ed Maggio, TECO Energy
Justin McDonald, Southern Company
Ben Meissner, Duke Energy Corp
Jim Sellers, Entegra Power Group
David Such, Xcel Energy
Eugene Szpynda, New York Power Authority
Paul Whitlock, Dominion Resources Inc
Graham didn’t spend much time on his opening remarks—perhaps three minutes. There were more important things to do. The first was to thank Paul White of Dominion Resources Inc for his 15 years of service to the 7F Users as a member of the steering committee and one of the group’s guiding lights during its development into a world-class engineering organization.
White has transitioned to an advisory role at Dominion and now spends a significant amount of time mentoring engineers and sharing best practices and lessons learned over his many productive years in the generation business. While some companies complain about the shortage of experienced engineers, Dominion is proactively addressing the issue with its mentoring program. Paul Whitlock of Dominion has replaced White on the 7F steering committee (sidebar).
Graham then passed the microphone to last year’s chairman, Ben Meissner of Duke Energy, who updated attendees on www.7Fusers.org, which went live just before the 2012 meeting. The organization’s electronic headquarters hosts a lively, interactive 7F forum and is equipped with a fully searchable archive.
Both are accessible only by certified users—currently more than 700 from 75 owner/operators. The modern design and user-friendly website got two-thumbs up from attendees. If you are employed by an owner and/or operator of 7F engines and are not yet registered, do so today. This will give you access to presentations from the 2013 conference.
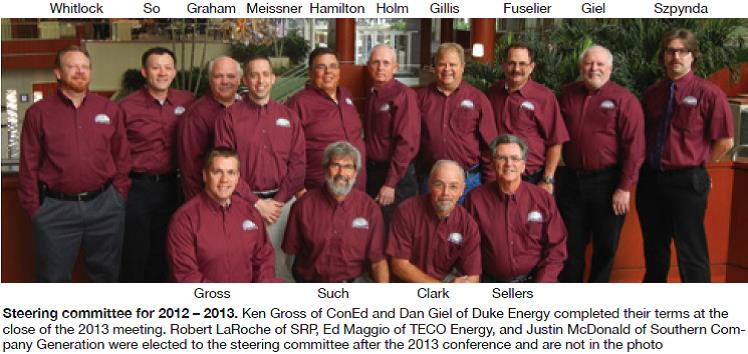
The big chill
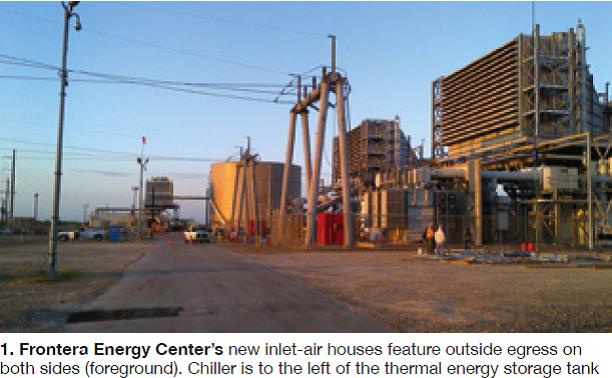
Ed Fuselier of Direct Energy, the 7F Users’ 2013 – 2014 chairman, gave what may have been the day’s most uplifting presentation with an overview of the recently completed inlet-chiller retrofit at Frontera Energy Center, a nominal 500-MW combined cycle located in south Texas. The plant operates in an energy-only market, and with electricity prices generally highest in summer when temperatures are high, replacing the evaporative cooler with a chiller made good financial sense.
Frontera’s inlet chilling system includes a 3.5-million-gal thermal energy storage tank (TES) rated at 70,000 ton-hr; the cylindrical steel vessel stands 65 ft high and measures 90 ft in diameter (photo). The system was designed, procured, manufactured, installed and commissioned by Stellar Energy. TES provides significant operating flexibility (Fuselier called it a 60-MWh storage battery) while minimizing capital and operating costs. Specific benefits of the chiller/TES system include the following:
- Increases plant output by 53 MW on a 100F day.
- Halves auxiliary load during the day (5 MW versus 10) by storing energy overnight.
- Reduces capital cost. The chiller package is 7000 tons; 14,000 tons would have been required absent the TES.
- Allows the chiller auxiliary load to fit on the plant auxiliary bus without an additional transformer.
- Enables the plant to run for two hours—so-called super-peak mode—exclusively on chilled water withdrawn from the TES tank (chillers not operating).
Innovation is evident in the inlet air house arrangement. The original inlet system was scrapped and a new inlet incorporating self-cleaning filters and chiller coils was installed by Donaldson Company Inc. Frontera wanted its new inlet system to fit on the existing structural steel to avoid disturbing the inlet bleed heat system and silencers. Another cost-saving goal was to avoid reconfiguring ductwork. This objective meant Donaldson would have to provide a unit with the same bottom-biased outlet transition that characterized the original inlet house.
But that is not ideal for chiller coils because, with this arrangement, more air would flow through the bottom-most coils than through the upper ones. Result: The uppercoils would produce colder air than the bottom ones and the two temperature regimes would not mix before entering the compressor bellmouth. Such stratification is not permitted by the gas-turbine OEM.
2014 Annual Conference
and Vendor Fair
May 19 – 23
Sheraton Wild Horse. Pass Resort & Spa. Phoenix, Ariz www.7FUsers.org
The solution was Donaldson’s “variable fin-pack density.” Simply put, its engineers used CFD analysis to design the inlet with the optimal number of fins per inch on each coil to produce chilled air of uniform temperature on the downstream side of the chiller section.
Chillers are a competitive necessity for many plants in the Texas market. Given Frontera’s location and the market served, chillers can operate at this facility a significant portion of the year. Temperatures at the plant site typically exceed 80F more than 3500 hours annually.
Although cold snaps are rare (temperatures are 50F and above about 8400 hours annually), their possibility was not overlooked by the owner’s engineers. Should the temperature drop to about 30F, the plan is to circulate water from the cooling-tower basin through the coils to provide the heat necessary to prevent freeze-up. A water/glycol mixture will be circulated through the coils in the unlikely event the temperature drops to 25F.
Compressor session
Compressor presentations and discussion traditionally take most of the first morning at 7F User Group meetings and 2013 was no different. The session ran nearly three hours, including the coffee break. The other sessions—safety, controls, auxiliaries, combustion, turbine, and generator—typically are budgeted half that time or a bit less.
Catastrophic failure. It seems hard to believe, but a corrosion pit, so small that it’s hardly visible, can bring down a large frame gas turbine. That was the sobering message from the first user to address the compressor session. Users may have heard this before, most recently in the CCJ from John Molloy, PE, M&M Engineering Associates Inc, in the 4Q/2012 issue, Minimize the risk of catastrophic failure from contaminated inlet air.
The case history presented to the 7F users described the wreck of a simple-cycle machine with 700 starts while it was at full speed, no load. Borescope inspection revealed extensive damage to the rotating and stationary compressor blades. But that assessment hardly described the damage found when the unit was opened and the rotor removed.
It did not appear that any airfoil was left unscathed. Close examination revealed only one clean fracture surface: An R1 blade was sliced off neatly at the platform. Investigators at the shop identified a second R1 blade with a big crack, perhaps only a few hours or one or two starts from failure.
The area in the lower casing once occupied by S5-S9 was cratered and occupied by slag. No one knew where the base casing material was. There was a deep gouge, about ½ in. deep and 6 in. long, in the mid compressor case which could not be weld-repaired. What to do about that?
There were three options for the rotor: rebuild the existing one, 10 to 12 weeks; buy a refurbished compressor rotor, five to six weeks; buy a fully refurbished unit rotor, four weeks. Casing options were: Repair existing casing, three weeks; buy a used casing, three weeks; order a new casing, 10 months. The casing repair option seemed contradictory because the OEM said welding was not possible. The owner opted for rebuilding the existing rotor and buying a used casing.
But the return to service would prove to be a torturous journey. The used casing was found, upon receipt, to have a patch ring at stage 10—an unpleasant surprise. Plant personnel learned that it was installed to correct a manufacturing error and that the casing had operated its entire life that way. The not-so-perfect casing, though disappointing, was accepted as is.
During re-commissioning operations the unit tripped on high exhaust spread. Debris distributed throughout the fuel system was the cause. It seems like workers “missed a spot” during cleanup. The debris hideout was on the upstream side of the purge valve. All fuel nozzles were removed and sent to a repair shop for cleaning and inspection; debris was collected and analyzed.
Root-cause analysis (RCA) suggested the failure was caused by the coexistence of a local high stress point and a corrosion pit which led to crack initiation and the eventual liberation of a single R1 compressor blade. Corrosion was likely initiated by poor water quality early in the service life of the unit, about the time of the millennium. A check of available records revealed that chlorinated river water was used as makeup for the evap cooler at that time. Today, a reverse osmosis system provides evap-cooler makeup and water quality is monitored.
One final note: Borescope inspections had been done regularly, the last one only a dozen starts before the wreck, but telltale pits and cracks had never been noticed because they were not in a “hot area” for inspection.
“Forced Forward Stator Replacement,” well presented and well received, featured a valuable review of compressor issues and OEM responses (Technical Information Letters and product changes) that owner/operators have endured since the unit profiled began operating in spring 2005.
The historical perspective was of particular value to the first-timers in attendance—about half of the registrants. If you didn’t absorb all that the speaker had to say, access the presentation at www.7Fusers.org. The archives section of the organization’s website is for owner/operators only and requires a “library card.” Register today online; it’s simple to do.
The two 7FAs for this combined cycle were commissioned with the so-called “original” compressor blades and the OEM’s modified water washing system. Given the many design iterations for these components it is difficult to understand from this summary exactly what was installed in this user’s engines at the time. However, he did say that the airfoils in the R0 and R1 rows of his units were susceptible to erosion, foreign object damage, and associated cracking.
One of the reasons to attend user-group meetings is that you can query the speaker to learn exactly what components his or her case history is referencing. With all the OEM’s design changes over the years, and the wide variety of third-party parts available, there probably are more than a hundred unique engines in the fleet.
Back to the case history. The plant began inspections recommended in TIL 1509 for R0 and R1 in fall 2005. A crack was found in an R0 blade on one unit in spring 2008 and blades were replaced with the “original” airfoils. The owner implemented the OEM’s recommendations based on fleet and user experience, including the following:
- No R0 upgrade.
- No online water washing.
- Aggressive semiannual inspection schedule.
- Monitor the OEM’s upgrade progress through the 7FA Users Group and the GE sales team.
- Evaluate third-party solutions.
In planning for the fall 2011 major inspection, the owner’s engineers fully evaluated all upgrade options, including the OEM’s “enhanced compressor” upgrades—such as Package 3 to address R0 and stator failures, Package 5, marketed as a “proactive enhancement” to address R1 cracking and other issues.
In conducting its assessments, the outage team focused its analysis on issues presenting the highest operational risks—including R0/R1 cracking, stator cracking, aft stator rocking. Analyses complete, the owner, a transactional customer, opted to wait until it had adequate time to evaluate field experience with both OEM and third-party alternatives before deciding on the specific upgrades to install.
When Unit 1 was opened for the fall 2011 major, extensive corrosion pitting from contaminated air was in evidence on blades in R1-R3, R6, and S1-S4; some pits exceeded the maximum allowable depth after prescribed corrective blending. The pitting photos shown by the speaker were very similar to those presented by M&M Engineering’s Molloy in the article referenced above.
The user presenting said his 18-stage compressors suck in air heavily contaminated by vehicular emissions and salt. He also mentioned a four-month shutdown in spring 2009 to address problems with the HRSGs. During that time there was considerable air flow (natural draft) through the gas turbines. Experience of others suggests that air curtains and portable dehumidification systems are beneficial. The owner also believes that ineffective water washing contributed to the pitting attack.
The poor condition of the compressor air path required a significant increase in scope for the major inspection. Re-blading was necessary. Plant personnel considered themselves lucky because no blades were liberated despite the extensive pitting. GE was selected to destack and overhaul the rotor and rebuild it with new blades, a job that took six weeks. The speaker said there was not adequate time to evaluate the capabilities of third-party services providers and invite them to bid on the work.
The plant had a spare rotor (with an enhanced R0), so it was inserted into Unit 1 and that engine’s rotor overhauled for Unit 2 during its major inspection in late fall 2011. Unit 2’s compressor also had extensive pitting damage. Interestingly, the plant is now operating two GTs with rotors having different features: One has a Package 5, the other a Package 3.
Follow-on corrective action includes the following:
- Increased frequency of water washing to multiple times weekly. R0 erosion is being monitored.
- Inlet inspections are characterized by greater vigilance for oil, dirt, grease, moisture, etc.
- An air-filter upgrade program will be complete by year-end.
- Upgraded water washing system is being evaluated. Investigation of erosion potential is part of the evaluation.
A second presentation by this user described “Aft Stator Replacement” for the same gas turbines. Since 2006, he said, semiannual inspections have been conducted for compressor rubs and shim migration; TILs 1502, 1562, and 1769 were mentioned. In 2008, a “cases-off” hot-gas-path (HGP) inspection included aft blade tip blending, installation of third-party S17 vanes and exit guide vanes, and pinning of shims by a third party.
The first significant finding of stator rock was during the fall 2009 borescope inspection. Rocking of from 30 to 50 mils was in evidence. The following spring, rocking of up to 67 mils was found. Inspection intervals were reduced to between 1000 and 2000 hours from that point on. Vane rock increased to as high as 95 mils. Owner was concerned because at 120 mils the gas turbine must be shut down.
Engineers set about evaluating upgrade options for the aft stator section of the compressor for possible implementation during the fall 2011 major inspection. The first option, replace in-kind, really was not a viable alternative: It doesn’t solve the problem because the case was already damaged and the likelihood of shim migration was good.
The OEM’s so-called Bigfoot mod/ Package 4 was an alternative, but that was viewed as an extremely intrusive and permanent machining procedure that would become the critical path for the major. It also involved a significant upfront commitment for parts and labor for a procedure with limited operational experience (fleet leader at 13,000 hours at the time). Plus, there were emerging stator twist concerns.
A fallback position would be to wait until the 2014 HGP to implement a solution, as was the strategy described earlier for the forward stator section. But a third-party was offering multiple-vane segments using field-validated airfoils that were viewed positively. Fleet leader had 24,000 hours at the time and these parts and their installation were much less costly than the OEM’s solution. Deal! The new parts have since passed the 12,000-hr mark and are said to look like new.
Another compressor presentation that got high marks, “17th-Stage Compressor Wheel Dovetail Cracking,” provided attendees several lessons learned/best practices. When preparing for a major inspection, an owner’s engineers were warned about the possibility of finding dovetail cracking on the 17th-stage wheel. Rotor out, cracks ranging from about 125 to 155 mils radial and 60 to 220 mils axial were illuminated by red dye on the aft side of every flat-bottom blade slot. The rotor had experienced 2025 actual starts and had recorded 44,365 hours of service at that point in its life.
The OEM told the owner to blend-out cracks up to a depth of 100 mils; also, to smooth all blunt edges and transitions of the blend and dye-pen the affected area to be sure the indication is gone. If a crack remains after blending 100 mils, the OEM said, take a picture, estimate the size of the crack, and submit a PAC (Power Answer Center) case. One crack was known to exceed 100 mils, so the owner leveraged EPRI research and decided that blending to 125 mils was acceptable.
Caution: At the 2012 meeting, an attendee told the group it was his understanding that if you blend and can’t remove the crack it will propagate faster than if no blending had been done.
The forward sides of all slots also were dye-penned; all of those were cracked as well—from about 60 to 155 mils axial. EPRI’s stress analysis concluded that 7FA discs with flat-bottom dovetail slots will crack somewhere in the neighborhood of 1000 to 1500 actual starts. The disk examined was considered good for another 900 factored starts.
A field service team from Sulzer Turbo Services was dispatched to the plant to blend out the cracks. This is a difficult job to do in the field, the speaker said, but Sulzer successfully removed all cracks. The owner’s plan is to order the new 17th stage wheel/stub shaft with round-bottom blade slots and install it during the next HGP, which becomes a major because the rotor must be unstacked.
An RCA revealed that rim dovetail cracking is caused by thermal transient stresses associated with cyclic operation. Hot restarts are the most damaging operating scenario; during a shutdown, the rotor rim cools quickly and the wheel center stays hot. One user in the audience commented that rim cracks are not self-arresting. He added while round-bottom disc slots avoid stress concentrations characteristic of flat-bottom slots, they also will crack, but are expected to last twice as long as discs with flat-bottom slots.
There were two brief compressor-section presentations, one with the speaker talking through a series of photos of S17 vane segments from the time they were removed from the engine for repair of the bolted shroud until they were reinstalled in the unit. A hiccup was reported on final fit-up. A poll of attendees revealed about half a dozen users operating with shrouded S17 vane segments provided by a third-party supplier—one engine having more than 25,000 hours on those parts.
A user who presented last year on the difficulty in extracting damaged R0 blades using a come-along and air hammer, and the galling of the blade slots experienced with that method of extraction, was back at the podium again this year. He reported success (no galling) on another gas turbine by using a cutting wheel to remove the airfoil and then a milling tool to evacuate the blade slots. He said it took about three shifts to mill out all of the R0s. Outside California, he added, you can use a plasma torch and probably get the job done in one shift. The first rotor goes to the shop this fall to replace the stub shaft and integral wheel with the galled slots.
By show of hands during the open discussion period, about 80% of the group has done a compressor upgrade of some sort—most with the OEM. Other talking points included ice damage on R0 and how to avoid it. This has been a discussion subject at several user group meetings over the years. Use the search function at www.ccj-online.com to access more information. There also was mention of systems for compressor-blade health monitoring—both OEM and third-party—but relatively few attendees had experience with these promising diagnostics.
Safety
Fall protection was a major topic of discussion because many serious injuries result from falls of only a few feet. One fatality reportedly was caused by a 12-ft fall. Lifelines, suggested tie-off points, etc, were included in the give-and-take.
The pros and cons of enclosure entry while the GT is in operation also were debated. Some attendees see the benefits of periodically inspecting the inside of the turbine enclosure to identify leaks, catch other developing concerns, and to facilitate troubleshooting.
Others argued that opening compartment doors could put individuals at risk should unexpected conditions inside the compartment expose personnel to hot gas, a combustible environment, fire, or other acute hazards. They do not allow operators to enter the package with the GT in service. One case history noted involved an operator who opened the compartment door and saw something glowing in the combustion section (caused by the failure of a dual-fuel nozzle), narrowly avoiding injury.
An attendee said operators at his plant periodically open the compartment door for a 30-sec look-see to identify possible issues using the senses of sight, smell, and hearing. But they are not allowed to break the plane of the package with equipment in service. Another user said his plant allows operators to enter the package but they must be wearing a long-sleeved shirt and gloves, and inform the CRO before entering and after leaving.
The dangers of CO2 fire extinguishing systems were discussed as well. One user’s experience was that when CO2 dumps into the No. 2 bearing compartment it spills out and floods the surrounding area. This can be dangerous because low-lying areas can take considerable time to ventilate properly. He recommended conducting a CO2 test and tracking its migration to develop appropriate safety procedures. A recommendation from another user was to install hazardous gas detectors outside the package to improve their reliability.
Two more safety topics discussed: (1) Emergency exits and fire breaks in air-inlet filter houses, and (2) extraction of injured workers from confined spaces. The latter can be particularly challenging if the people who must be rescued are overweight. Regular practice with first responders was suggested.
Combustion session
An owner reported that one of its 7FA.03s, with a DLN2.6 operating on LNG, tripped on high exhaust spread as the combustion system transferred from Mode 4 to Mode 6. A restart was attempted with the same result. First thought was that the root cause was in the fuel system, not the combustion hardware. Reason: Nitrogen in the LNG boils at -320F, lower than the -258F for methane, and engineers surmised that nitrogen vaporized first, rapidly diluting the boil-off gas (that is, the surge in nitrogen reduced the calorific value of the fuel at the burner tip).
Engineers believed this was the cause of the lean blowout (LBO) event, but because the Modified Wobbe Index was in the flammable regime at the burner tip, they predicted a DLN issue in addition to low MWI. The OEM was consulted and what sounded like a trial-and-error approach to a solution was initiated. The PM3 split was increased at the mode change and this was effective in avoiding LBO, but peak-2 dynamics increased as a result. Engineers also learned that peak-1 dynamics increased with MWI and peak-2 dynamics decreased with MWI.
Finally, engineers were able to tune the combustion system to hold dynamics under 2 psi, maintain NOx between 10 and 15 ppm as allowed by the plant’s permit, eliminate the LBO threat, and permit turndown to about 50% load. The editors spoke with the presenter afterward and learned his employer—a gas company that also produces electric power—saves the highest-value LNG for its gas customers.
The owner receives LNG from many sources worldwide and product variability can be significant in terms of its use in finely tuned combustion systems. A review of CCJ’s EcoElectrica LP plant report, published in 4Q/2012, shows the highly reliable operation of that plant depends significantly on its high-quality LNG with minimal variation in composition.
Another presentation focused on the conversion of an early (Serial No. 1) 17-in. DLN2.6 combustion system to an 18-in. system. This was done to enable parts compatibility with other units and the ability to use 24K hardware offered by the third-party supplier with which it has a long-term parts agreement. The speaker attributed much of the challenging project’s success to fellow 7F users who shared lessons learned from their conversion experiences. The presentation triggered significant open discussion on experience with 24K and 32K hardware.
Turbine session
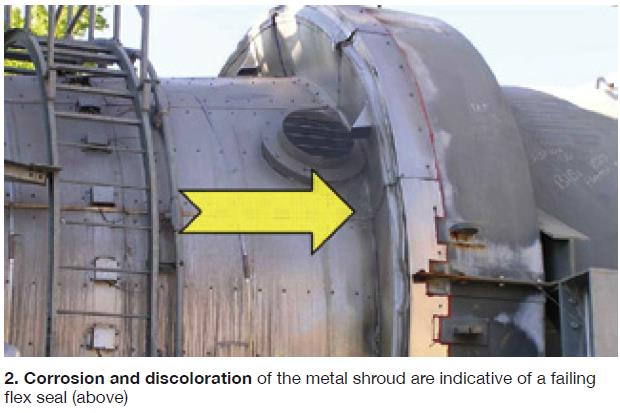
Several discussion topics gained traction in the turbine session. Cracks in gas rings received some air time. One user said the OEM got involved the second time the PM3 header cracked on one of his units in the same location the occurred the first time. First thought was that vibration was the root cause of the problem because the upper section of the header was not supported to allow for expansion. But the gremlin turned out to be pigtail lockup. Upper-half pigtails were swapped out for ones an inch longer and the problem went away.
As the fleet ages, owner/operators are experiencing exhaust-frame deterioration as earlier frames had in the past. Condition-based maintenance was batted around and the general conclusion is that it’s not there yet. A user described the scenario where the contractor decides what repairs to make by virtue of the contract. Your equipment might not be returned to as-new condition, he said, it might just be “good enough.” Then the contractor loses the paperwork on what was done, what parts were used, etc. The owner is at risk then, he concluded.
The subject of exhaust-section flex-seal failures was brought to the floor. In four years of operation, one user’s 7FA.03 had suffered several flex-seal failures. Another owner confirmed that failures do occur frequently. Yet another recommended changing the flex seal at every HGP inspection because, he said, “it will fail” and you don’t want that to happen during the summer run. Proactive replacement is a viable strategy, he added.
That the vendor fair is a valuable adjunct to user group meetings was in evidence again as a stop at the EagleBurgmann booth revealed an OEM-approved flex-seal upgrade that seemed to address the needs of a couple of users discussing the challenges they faced during the closed session. Discoloration and corrosion of the metal shroud that covers the flex seal—located between the turbine manifold and exhaust diffuser—is indicative of a failing seal, the editors were told (Fig 2).
He said that the harsh cycling conditions experienced by many engines in the fleet cause flex seals to lose their flexibility and sealing capability over time. A leaking flex seal can allow exhaust gas to bypass the downstream SCR and contribute unnecessarily to NOx emissions. The upgrade described in Fig 3 provides a gas-tight seal over the 7FA’s existing metal flex seal (Fig 4).
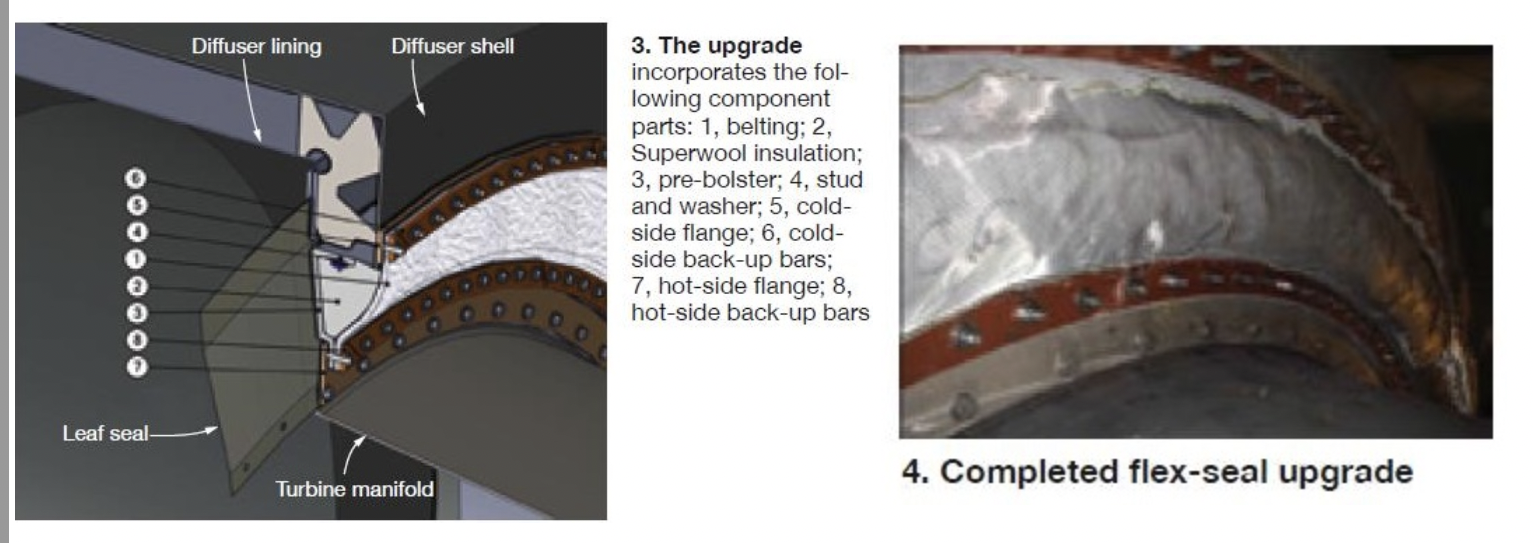
Generator session
Floating hydrogen seals were a topic during the open discussion period. A few users were puzzled by the problems experienced on GT generators that had not been identified with generators at conventional steam plants. Recommendation: When you receive new hydrogen seals, make sure you check for roundness before putting them on a shelf in the warehouse. One plant went through six sets before finding one that met spec.
To pull the field periodically or not—at each major, for example—also was discussed, with no definitive conclusion being reached. The hands-on people in the room were for periodic field removal, saying an up close and personal inspection provides better information than GE’s Magic (the acronym for miniature air-gap inspection crawler) or alternative remote inspection devices.
After the session, an attendee stopped the editors to say his plant had been quoted about the same price for Magic as for pulling the rotor, so they pulled the rotor. That was not the experience at a plant recently visited by the editors during its generator inspections. There the cost of remote inspection (not GE) was half the cost of pulling the field.
Controls session
The controls component of the 7F Users Group meeting has expanded in scope over the last couple of years to help owner/operators address multiple challenges—including diminished OEM support of legacy control systems and the need for tighter operational control to accommodate renewables, satisfy NERC CIP requirements, reduce emissions, etc. Several recent additions to the steering committee with controls experience have contributed significantly to the more robust program.
There were several user presenters in this portion of the 2013 conference. One focused on frequency response for combined cycles using the DCS. The speaker said the DCS emulates the governor and the preselected load set point is biased in proportion to the change in frequency. Critical to success is a high-resolution frequency measurement; the SFL1 in the Mark V or Mark VI via PI is not satisfactory. The solution here was to hard-wire a frequency meter to the DCS.
Another user presented on the value proposition of PI ProcessBook™, which makes it possible to efficiently display real-time and historical data residing in the PI system and other sources. He views ProcessBook as an efficient method for getting the most out of PI. Its advanced features are real simple to use, he said, and demonstrated this. Example: Scatter plots, good for identifying highly correlated items and for revealing when a process is off-track, are easier to build in ProcessBook than in Excel. If you’re unfamiliar with ProcessBook, there’s plenty of material up on the Web.
Upgrades. It seems that the most popular controls presentations at user group meetings concern system upgrades and replacements. One user presented on an HMI replacement for a combined cycle that began commercial operation in 2004. The original arrangement featured six GE HMIs and three screens in the control room. There was no HMI for use as an engineering work station (EWS). The new set-up features three of the OEM’s HMIs: two in the control room and one EWS. All machines are quad-monitor capable, the speaker said. There are still three monitors in the control room; the EWS has two monitors.
Another upgrade to the original system was the addition of a Wyse terminal (thin client) to the Packaged Electrical and Electronic Control Compartment for each gas turbine. The PEECC, sometimes shortened to PECC, is where the Mark VI and the motor control center for the GT reside. The inexpensive Wyse terminal is connected to the Ethernet loop for the HMI and Mark VI. The reconfigured and upgraded system has been in service for more than a year; no negatives were reported.
The replacement of Mark V control systems on two gas turbines serving a combined cycle that started up in mid-2005 was the subject of another presentation. Interestingly, the Mark V had reached end of life (EOL), according to the OEM, in March 2004—more than a year before plant’s commercial start; the announced end-of-service (EOS) date is March 2014. The owner felt compelled to upgrade. By way of background, the Mark V TMR system has four processors (referred to as cores) R, S, T, and C and a protective core P. It was initially provided with an IDOS <I> operator system and subsequently with a Windows/Cimplicity-based operator interface system and uses an ARCnet-based communications protocol to communicate with the operator interface system.
The owner’s engineers reviewed many options, including the following:
- Upgrade to Mark VI with its 32-bit computer system, Windows interface and better software tools, and Ethernet-based communications. However, this system reached EOL four years ago and EOS is expected in only six more years.
- Replace the Mark V with a Mark VIe. Advantages of the latter include (1) OEM’s current offering, (2) support expected until 2025 or beyond, (3) Windows HMI interface, and (4) Ethernet communications. Another benefit of a new Mark VIe is that it can be expanded to provide total plant control.
- Mark VIe migration (Mark V retrofit). This option involves installing a Mark VIe controller inside the Mark V cabinet and retrofitting it to the Mark V core. All boards are upgraded to supportable versions.
- Third-party DCS. The plant has Ovation™ for its balance-of-plant platform.
- Third-party solution with PLC-based controllers.
What to do? Perhaps the most obvious option would be to do nothing. Reasons include these: There are many Mark V systems operating in the electric power industry, the OEM will support the platform until parts run out, the OEM does offer field-service options (if you have the money, the OEM has a service team ready to support you), there is robust third-party support for control system components, and there’s access to support from other owner/operators via the 7F Users Group.
A replacement Mark VIe apparently was on the pricey side, although the speaker did not talk about dollars or contract terms and conditions, as is the rule at user-group meetings. One assumed cost was a concern because he said field I/O work was required for a new Mark VIe and outage time would be a week or two, possibly more.
Ovation was a serious consideration, but, in the end, the lack of experience of that platform on 7F engines was the deal breaker—this despite excellent reviews from the one customer based on two years of service. Little was said about the PLC-based option.
The preferred solution for this application was a Mark VIe migration because of the speed and economy of implementation, and OEM controls reliability and compatibility. Regarding the second point, minimal control system management was required, the OEM support network was already established, and there were multiple third-party options for control systems, automatic tuning, flame monitoring, etc.
Value of the vendor fair. The editors stopped by CSE Engineering Inc’s booth on the exhibition floor to ask what its team of experts would recommend to a critical generating facility having legacy Mark V controls on its GTs and then compare that solution with the one selected by the owner who had presented earlier in the day. Perfect question for Chairman Craig Corzine, a former GE employee having a deep background in Speedtronic® control systems and gas turbines, but he was out in the field. VP/GM Steve Morton was patrolling the company’s 8 x 10 ft territory. Like many 7F attendees, he had served in the US Navy and managed shore-side generation facilities.
Morton said CSE, which celebrated its 20th anniversary in 2013, had decided not to develop a retrofit control system package for the gas turbines but to continue development of CSE’s technology to extend the commercial viability of the existing Speedtronic control system with specific emphasis on the Mark Vs. Asked about CIP compliance, Morton said the concern with CIP standard compliancy is not related to the Mark V itself but to the HMI interfacing with the Mark V and it is one of the areas that the California company has focused on.
Corzine was patched into the conversation by cell phone and he said that scrapping the Mark V on a controls refurbishment project was akin to throwing out the proverbial baby with the bathwater. If it was installed, commissioned, and has been maintained properly, it’s an exceptionally reliable system, the controls expert said. Spare parts and technical support are available and will be for several years to come. The only reasons to replace a Mark V in his view probably would be to accommodate a technological upgrade of the turbine—such as a DLN retrofit—or to transition to a fleet platform to reduce spare-parts inventory and to facilitate maintenance.
Corzine said CSE’s <ITC>® HMI is a CIP-compliant industrial monitoring and control software platform designed specifically to replace the functionality of the IDOS based Mark V <I> and Windows/Cimplicity-based Mark V HMI. The <ITC> system also is used to interface with the Mark IV and Mark V LM, and soon for the Mark VI and Mark VIe as well.
The system communicates with the Mark IVs and Mark Vs using its native protocol over ARCnet and is provided with USB, PCI, PCIe, and Ethernet communications drivers. Plus, it can support up to four individual ARCnet networks and can be used to integrate Mark IVs and Mark Vs within the same system.
For the Mark V, <ITC> incorporates all the functionality of the legacy <I> and current Cimplicity-based HMI systems, inclusive of Logic Forcing, Control Constant Editor, I/O Configuration, Control Sequence Editor, EEPROM Utilities, Diag_C, View Tools, and Auto-Calibrate. Additional features not available with the standard <I> or Cimplicity-based HMI system include Automatic F Drive Synchronization across all <ITC> systems, fully animated Real-Time Rung Display with sophisticated search and navigation tools, Multi-generator Tie-Line Control, Integrated Data Historian, Integrated Time-Sync Manager for all Mark Vs and balance-of-plant individual controllers, and integrated offsite remote monitoring and control.
Additionally, the <ITC> system is used extensively as a data historian and gateway between the Mark V and other computers or control systems, providing a direct read/write data exchange path between the devices for monitoring and control. Communications protocols include OSI PI, OPC (server and client), GE FANUC Series 90 (Serial and Ethernet), Allen-Bradley DF1 (Serial, DH+, and Ethernet), DNP 3.0 (Serial and Ethernet), Modbus (Serial, Ethernet TCP, Ethernet UDP, and Modbus Plus), Siemens S7-200, S7-300, and S7-400 (Serial and Ethernet), Westinghouse WDPF, and many more. CCJ