Flow dividers are used on gas turbines to maintain equal flows of liquid fuel to all combustors. They are passive devices that derive their motive power from the energy contained in the fuel delivered by the main fuel pump. Although designs and layouts vary, the fundamental principle of flow-divider operation is the same.
Flow dividers are little more than an array of virtually identical, high-precision, spur-gear hydraulic motors (think of them as flow elements) that are mechanically coupled to run at equal rotational speeds. When liquid fuel enters the flow divider, it simultaneously exerts a pressure on the inlet side of all these hydraulic motors, which causes them to rotate and meter oil at virtually identical discharge rates.
To maintain relatively equal discharge flows under varying pressure conditions, the running clearances inside each flow element must be extremely small. This characteristic also makes flow dividers very susceptible to fouling if particulate matter is allowed to enter the clearance areas. Particles larger than about 20 microns must be filtered out.
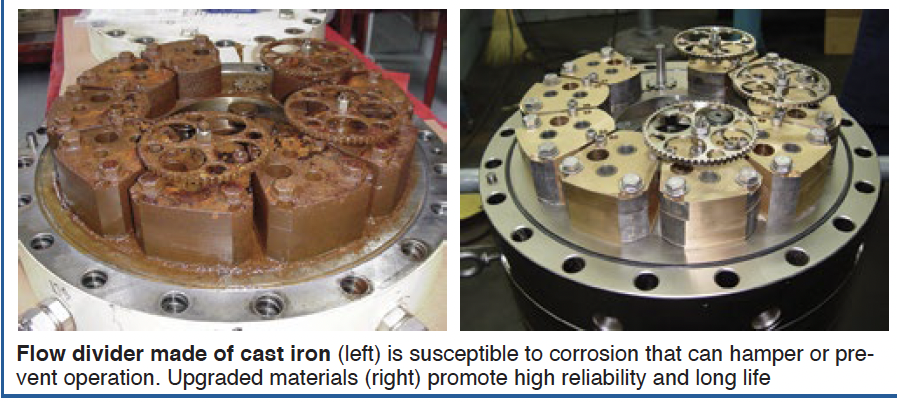
Certain non-particulate fuel impurities that cannot be filtered out are another potential source of problems. Liquid fuels may contain various corrosion-causing contaminants—water is most common—capable of attacking materials that many legacy flow dividers traditionally were made from—such as cast iron. Water corrodes the cast iron and the resulting iron oxides can quickly consume the small clearances between the gears and housings and prevent their rotation.
New flow dividers have for many years been made of aluminum bronze or a similar material to assure top performance and long life. At least one manufacturer supports a program aimed at improving the reliability of legacy equipment with corrosion-resistant replacement parts.