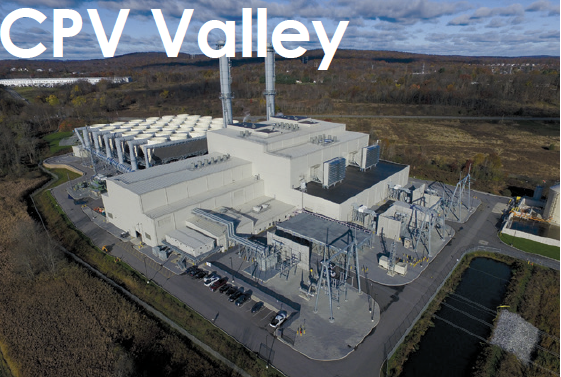
CPV Valley Energy Center
Owned by Competitive Power Ventures and Diamond Generating Corp
Operated by DGC Operations LLC
680-MW, gas-fired, 2 × 1 combined cycle located in Middletown, NY
Plant manager: Ben Stanley
Planning, collaboration key to outage management process
Challenge. IPPs with minimal staffing must be flexible and tactical when planning all outages. Utilizing a standardized (but adaptable) process for planning and execution helps keep employees and contractors safe and surprises to a minimum.
Solution. The plant’s O&M team works closely with asset-management staff, third-party support, and equipment OEMs to plan and execute outages. Key elements to the program are:
- An outage planning procedure that outlines the process for the team. This procedure is reviewed by the team before any upcoming outages.
- An outage summary document that states the purpose of the outage, the intended worklist, EHS planning, third-party participation, logistics, training, cranes and rigging, etc. It provides a narrative or “story” of the outage and evolves over time as the team refines the plan and gathers more detailed specifics around the work needed.
A checklist that details the main components of the outage. Starting with the type of outage (routine, minor, CI, HGP, major) and expected duration, the planning checklist includes the following:
- Internal meeting schedules—including those for LTP/LTSA service planning, EHS planning, budget reviews, and meetings with third-party vendors.
- Outage-date requests and approvals to energy managers and ISO organizations.
- Outage project list, which comes from the work-management process in the CMMS. Work orders and PMs are appropriately identified, prioritized, and classified for each type of outage. This list is reviewed continuously during the routine work-management process (backlog and work planning meetings).
- A preliminary outage schedule is developed and shared with stakeholders early in the process. Critical-path items are identified and highlighted.
- Work schedules. Operator/maintenance crew shift schedules are reviewed and updated. Shifts are added where needed to support plant evolutions, EHS activities, operator training, etc.
- Special compliance inspections needed (pressure vessels, insurance/risk inspections, compliance metering).
- Rigging and lifting. A review of the need for lift plans and special rigging certifications is performed. In some cases, rigging/crane certifications require long lead times with third parties.
- Safety planning and third-party support (confined-space rescue, audit support, and site security).
- An EHS plan for the outage details items such as hazardous waste generated, inspection and audit planning, potentials for high-risk environmental issues, etc.
- Logistics. Parking, laydown, deliveries, additional office space, etc, are reviewed and an updated site map is generated.
- Budget and procurement. The business-administration and asset-management teams are fully integrated into the process with a detailed list of parts/inventory needed, executed contracts, purchase orders, and appropriate delegation of financial authorities. The team also maintains awareness of the potential for additional discovery work and prepares to communicate variances as they occur during the outage.
- In-house parts inventory is reviewed. Long-lead-time items identified should be ordered well in advance.
- Severe-weather contingency planning includes a review of forecasts, historical weather patterns, and lessons learned. Focus is increased on personnel safety during severe weather. Consideration is also given for activities such as water washes during freezing ambient temperatures, delays in deliveries during extreme weather events or snowstorms, emergency lodging/hotels, etc.
- Plans are developed for pre-, in-, and post-outage testing. Bear in mind that several tests are best performed during shutdown to minimize reliability risks (turbine auxiliaries, overspeed testing, fuel swapping, etc). There are other tests that should be performed only when the plant is offline. Finally, certain validation testing is performed during the restart process.
- NERC task review of the required compliance testing items is performed for NERC applicability.
- An integrated checklist is developed for critical site and contractor contacts. Since this changes for each outage, it’s important for staff to update the list specifically for each outage.
- External notifications. Regulators, emergency management organizations, and in some cases local government agencies, require notifications. Best practices have been adopted to make courtesy notifications to town supervisors, boards, mayors, etc. This prepares them for increased traffic in the area, additional vehicles parked onsite and potential inquiries from the public/media.
- Scope freeze. The O&M and asset managers determine the appropriate date for scope freeze so that no additional work items are planned for unless they fall under a higher amount of scrutiny by plant management. This helps to minimize schedule impacts.
- A lessons-learned meeting is conducted shortly after outage completion. Focus is on both when and where improvement is needed. As many stakeholders as possible are invited to the session. The list generated helps to create corrective actions and items to consider for the next outage. Continuous improvement is the goal.
- Final outage report includes the outage summary, detailed schedule, facility outage map, detailed costs and variance report, and final results of the work list.
Results. The collaborative efforts of the team lead to safe, well-planned, cost-effective, and well-documented outages. Utilizing the procedures and tools developed by the team helps to ensure that the outages are completed on schedule and on budget with minimal surprises.
Project participants: The entire O&M staff, including Donald Atwood, Ben Stanley, Ed Peters, Dave Engelman, Tanya Rovner, Josh Zimmer