Challenge. The operation of a frame-size combustion turbine creates an environment that does not allow the installation of lighting and power fixtures. During outages, when work in the turbine compartment begins, there are a number of difficulties to supplying sufficient light for the more detailed work and power to operate electric hand tools in the compartment. Workers utilized the sparse outside receptacles for lighting and hand tools via extension cords pulled through the open doors.
Solution. The safety committee had a clear set of objectives to solve the problem:
- The original thought was to build a custom product that would meet all the needed criteria, but the discussion of parts and labor costs seemed added up to more than it would cost to purchase a system.Lightweight, modular, and universal: The system had to be easy enough to unpack and install so it would be used.
- Cost effective for power distribution.
- Minimal manpower for setup.
- GFCI protected.
- A method to enter the turbine compartment without going through a door.
We started by installing 480/240-V transformers in each turbine electrical control building (Fig 1). Conduit was run from the transformer to a fusible disconnect that powers the 50-amp receptacle. A sealable penetration was placed near the wall of the enclosure and the receptacle to provide a short run for the power cord to be connected to the skid.
If an additional skid is needed, workers can simply connect a cord to the outlet of the first box outlet to the inlet of the second skid which is clearly marked (Fig 2). Each individual circuit is GFCI protected and has individual over-current protection. In this configuration, a single fault does not interrupt the work of everyone else.
This system includes fixtures in the compartment that allows for use string lights rated at 150 W per fixture. These are used in the upper and lower sections to provide a well-lit workspace. Each fixture is attached to the wall of the enclosure using a magnetic plate attached by a stainless steel “S” hook which makes them easy to install and to relocate (Fig 3).
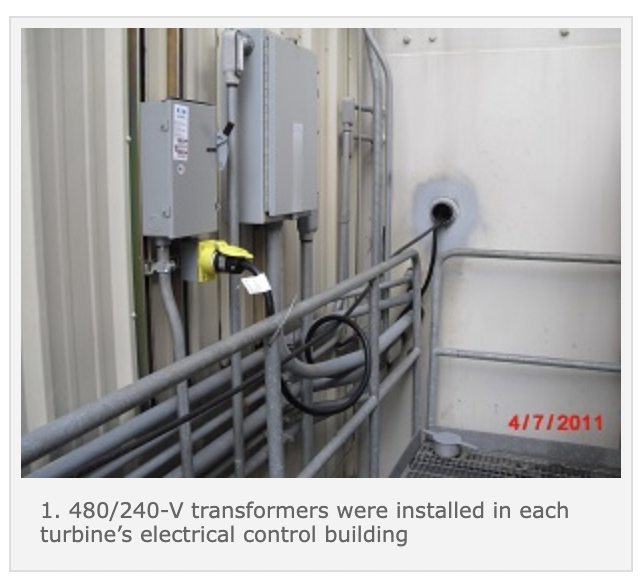
Results. We have eliminated the need for multiple extension cords, reducing tripping hazards as a result. This system provides a safe source of power for multiple users with GFCI and over-current protection on each circuit. The workers have an abundant power source in a short distance from the work area. All of the components are lightweight and can easily be carried by a single person and installed in a matter of minutes.
During a recent outage when an unplanned hot gas path (HGP) started on an additional unit, the contractors asked for and installed the power boxes and lights because the convenience during work and ease of installation exceeded expectations. This system has also proven itself useful in working in the different sections of our HRSGs by providing the ability to supply independent power to individual modules quickly.
Key project participants:
Sam Graham, maintenance manager
Neil Pierce, I&C technician
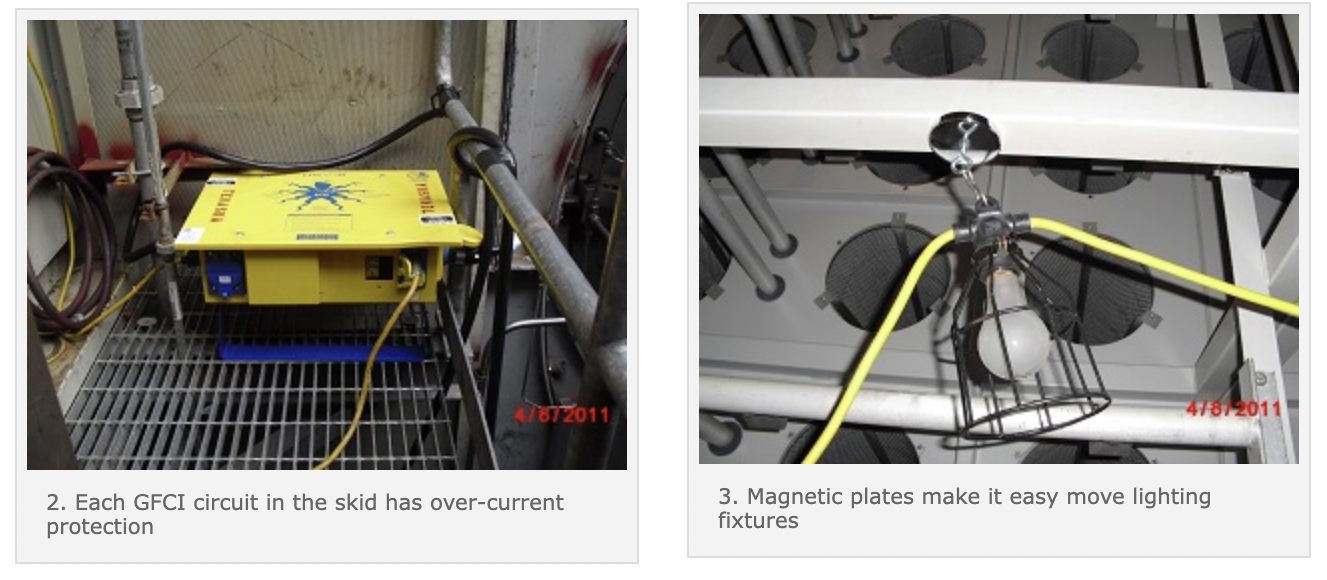