A better plant today than when new
(Scroll to the bottom for photos and graphics.)
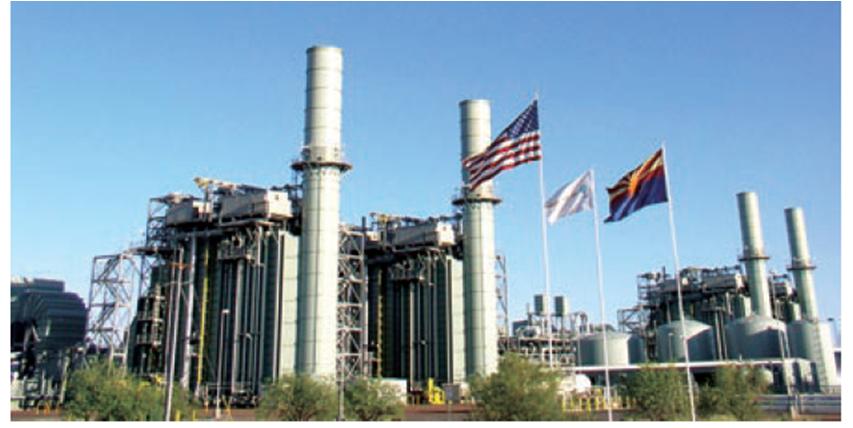
The editors first visited Mesquite Power in summer 2004, about six months after the plant’s second 2 x 1 power block began commercial operation (sidebar). Focus of the resulting article was the state-of-the-art knowledge management system put in place to enable fast, accurate decision-making—this to maximize revenue, minimize downtime and emissions, and maintain the highest level of safety in the workplace.
Mesquite was designed to operate as a standalone merchant generator. In addition to a robust DCS (Ovation™)—customized to accommodate both power blocks and also interface with the facility’s critical water treatment plant, natural-gas conditioning system, and the 500-kV substation that receives the plant’s electricity—it has its own purchasing, HR, and payroll systems.
When the Arizona combined-cycle went into service it was among industry leaders for its ability to cull intelligence from data collected by the plant’s PI system (OSI Software Inc, San Leandro,Calif). One example: alarming and notification of significant deviations from normal operating limits delivered via the Internet to anyone with a password and Web-enabled device. Sounds “ho hum” today, but eight years ago in the electric-power industry such capability was leading-edge.
This illustrates how quickly new technologies are adopted once proven and why continual investment in generating-plant infrastructure is required to remain competitive in the merchant power market. And reinvest regularly is what Mesquite has done to maintain equipment reliability and plant availability at levels that support the nominal 8000 hr/yr the plant has operated since COD.
It also has invested significantly in safety improvements that have earned the plant OSHA VPP Star status. This is the highest level of recognition for safety in the workplace offered under the federal agency’s Voluntary Protection Program. Mesquite and Yuma Cogeneration Associates are the only two power producers inArizonaat the Star level.
The editors’ June visit to Mesquite focused on upgrades and safety initiatives implemented by the plant since first start and the benefits accrued. They met with Jeff Zaifert, O&M manager; Mark Joy, senior gas turbine technician; and Joe Washington, site safety sponsor.
Zaifert, whom the editors met on their first visit when he was a gas-turbine technician, invited the participation of Greg Livingstone, CLS, executive VP, Fluitec International, St. Petersburg, Fla, and Ryan Sachetti, project engineer, Industrial Air Flow Dynamics Inc (IAFD), Glastonbury, Ct, who were deeply involved in two of the initiatives discussed.
The primary discussion topics were:
- How Mesquite maintains lube oil in top condition.
- Upgrade of lower penetration seals for the reheater 1, 2, and 3 and HP superheater 1 sections in all four heat-recovery steam generators (HRSGs).
- Conversion of lube-oil pumps from grease-packed upper thrust bearings to circulating turbine oil.
- Safety improvements—including new exciter brush gear to permit online inspection and maintenance, replacement of the OEM’s shaft grounding system, upgrade of the cooling-tower fire protection system, etc.
Turbine oil: Aiming for 100,000 hr
Lube-oil degradation and varnish have been a nuisance for many owner/operators of large frame gas turbines, to the point of compromising unit reliability in some instances.Mesquitehas taken a proactive approach to lube-oil lifetime management to avoid issues experienced by others, and plant personnel expect to reach at least 100,000 hr with the initial charge of lubricant by benchmarking against industry standards, periodic oil analysis, and thorough investigation of fluid degradation mechanisms.
Mesquitealways has used oil analysis as part of its predictive maintenance program. Joy mentioned that the OEM suggested usingASTMD4378, “Standard Practice for In-Service Monitoring of Mineral Turbine Oils for Steam and Gas Turbines,” as a guideline. However, it does not include any test for varnish-potential—a possible shortcoming.
Joy consulted with the plant’s laboratory partners and implemented a varnish-potential test called Membrane Patch Colorimetry (MPC), currently a draftASTMstandard. Oil samples fromMesquite’s four gas and two steam turbines revealed varnish potentials at the “critical” level.
The GT tech implemented a root cause analysis program. First goal was to identify the degradation mechanisms that might be causing elevated varnish potentials. Analysis of lube-oil filters revealed spark discharge, which adversely impacted the plant’s efforts to keep oil clean and caused its premature deterioration. Joy also learned that the filters were incapable of removing the soft contaminants associated with elevated varnish potential.
Here’s a summary of the actions Mesquite took to address these issues:
Eliminate spark discharge. The main lube-oil filters for 7FAs are in a duplex arrangement, allowing operators to quickly switch to a clean filter should the one in service become fouled (Fig 1).
However, because experience indicates that online plugging rarely occurs, the operations team decided to run both filters in parallel. Halving the flow rate across each filter, said Fluitec’s Livingstone, quoting industry research, would reduce the chance of spark discharge by a factor of eight.
To further improve fluid cleanliness, Joy switched from the 24-micon OEM filters to non-sparking, 12-micron filters. Both actions lowered the stress on the turbine oil and provided a cleaner fluid.
Lower varnish potential. Mesquite personnel researched the available technologies designed to remove the sub-micron soft contaminants conducive to elevated varnish-potential ratings, opting for a technology that accomplishes this objective when the turbines are offline and the fluid is cool and the soft contaminants are insoluble (Fig 2).
In addition, Mesquite deployed a resin-based technology capable of removing soluble soft contaminants when equipment is operating and the oil is warm. Both technologies operate on a slipstream off the lube-oil reservoir drain line and return the clean fluid to the oil fill line. The resin-based technology has been particularly effective for removing varnish precursors. Today, the oil circulating through all six ofMesquite’s gas and steam turbines has a normal varnish potential rating (Fig 3).
Improve the plant’s oil analysis program. The plant purchased equipment to perform MPC varnish-potential testing onsite. The in-house analytical program is augmented by additional tests conducted by a leading laboratory, including: RULER® (Remaining Useful Life Evaluation Routine) for determining antioxidant health, RPVOT (ASTMD2272, Rotation Pressure Vessel Oxidation Test) for measuring oxidative stability, and particle count (ISO Cleanliness Code 4406) for determining the number of particles of a given size in the oil sample.
The bottom line: Joy reports that the lube-oil conditioning plan described above has maintained the plant’s turbine oil in excellent condition. The antioxidants have at least 75% of their remaining life and the fluid’s lifetime is projected at more than 100,000 hours. Participants in the roundtable interview believed the average life of oil in a 7FA is five to six years;Mesquite’s oil already has been in service eight and a half years.
Other proactive lubrication initiatives include the following:
- Lube-oil pumps for each turbine were converted from grease-packed upper bearings to forced lubrication by filtered turbine oil to improve reliability and eliminate removing, cleaning, and repacking the bearings every 8000 hr as recommended by GE (more on this below).
- Filter carts were purchased to facilitate the maintenance of cooling-tower gearbox oils in pristine condition.
- Training. Joy attended Fluitec’s Lubrication Academy at the urging of Plant Manager Bob Ellis to expand his knowledge of tribology and turbine-oil chemistry.
The penetration-seal conundrum
Who’s the best pitcher in baseball? Who’s the best shooter in basketball in clutch situations? What’s the best type of penetration seal: mechanical, metal, or fabric? The answers to each of these questions can be debated into the wee hours without coming up with a definitive answer.
Recent hires at gas-turbine-based cogeneration and combined-cycle plants may not be aware that penetration seals are used to prevent the leakage of hot gases where pipes intersect the casings of heat-recovery steam generators—thereby minimizing energy loss and emissions, reducing noise, and protecting equipment and personnel. These components are designed to accept axial, lateral, and angular movements, thereby minimizing the stresses on the pipes to which they are attached.
Many HRSG users worldwide would like to know the optimal time to modify, upgrade, or replace failed penetration seals. Questions typically asked on the deck plates: How long can you run with a leaking seal? How much leakage is too much? Should you replace in kind or change the type of seal? Will leakage cause collateral damage (to adjacent seals, instrumentation, structural members, etc) and/or be a personnel hazard? How long might repairs or replacement take? What are the costs involved?
Mesquite O&M personnel asked themselves and prospective solutions providers these and other questions when the penetration seals on their four triple-pressure HRSGs exhibited excessive wear and tear. Joy said that after evaluating alternatives, plant staff decided to partner with IAFD on the design and installation of lower penetration seals for three reheater and the HP superheater sections in each of its steam generators. A total of 84 seals were involved, ranging in size from 4 to 14 in.
One of the toughest questions facing Zaifert and his colleagues: What would be the best type of seal forMesquite? They knew each has its advantages and disadvantages. To illustrate:
- A metal-bellows solution would require cutting of pressure piping and code welding to allow installation (read expensive). Longevity is the benefit.
- Mechanical seals will prevent most of the gas from escaping between a pipe and the casing, and they can be repacked or replaced when required—generally at acceptable cost. However, there always will be some leakage.
- Fabric inevitably will have to be replaced with new material, but this is relatively simple to do and generally affordable. But hiring just any local contractor to replace fabric is not recommended. Poor material selection and poor workmanship can lead to failures in short order.
Life of a fabric joint depends on the temperature of gas contacting the material. Example: A typical polymer fabric rated for 500F-600F might last 10-20 years if the material is kept at 250F or less. By contrast, one week to two months at 600F could put it at or near end of life.
The seal selected forMesquiteis of a hybrid mechanical/fabric design that IAFD said it has had good experience with—based on 350 units installed. To implement this solution, the original penetration seal (any type) is upgraded with a new frame that has a mechanical slip seal and a set-up to bolt on a fabric cover. Direct heat is blocked by steel and any remaining heat is sealed off with a fabric bolted-tight.
The bolted fabric clamping bars allow tightening and retightening of the fabric to assure the seal maintains its integrity (Fig 4). Plant’s experience with seals that used metal banding around the fabric to seal off leakage of hot gas was that expansion and contraction over time “worked” the banding loose and it lost some sealing effectiveness.
Mesquite hired IAFD to design, manufacture, and install all 84 penetration seals using only permanent employees of IAFD. This took finger-pointing out of the equation, which might have occurred had the plant contracted separately for installation and a problem cropped up.
The first 34 seals were installed in back-to-back power-block outages of six days each. The remaining 50 seals were installed during a later single outage which required the supplier’s craftsmen to work around-the-clock for 16 consecutive shifts.
Performance. The penetration seals experience the toughest duty are those for the first reheater module and the HP superheater. Temperatures in those sections can reach 1150F and pipe movement can be 6 in. After 18 months of service, the seals still are operating at near 180F on the outside of the fabric and show little wear and tear. Expectations are that they will last more than 36 months at these conditions.
Lube-oil pump mod
O&M personnel must scratch their heads from time to time wondering what was on the minds of designers when they made some of the decisions they did. At Mesquite, one of those times occurred every 8000 hours of operation until Ellis, O&M manager at the time, and his team decided that if they didn’t redesign the lubrication system for the upper thrust bearings on the lube-oil pumps supplied with the gas and steam turbines nothing was going to change.
At issue was the grease-packed, upper thrust bearing on all 12 pumps (two pumps each for the four gas and two steam turbines). According to the OEM’s manual, quarterly greasing was required via the grease cup. Every 8000 hours, the pumps had to be removed and disassembled to clean the thrust bearings and repack them with fresh grease.
This is a labor-intensive job, one requiring about a week’s effort for each power block. The effort normally would not impact availability because it fits within the outage schedule. But not many plants have unassigned personnel available for this effort and contracting-out the work is expensive. What to do?
The OEM undoubtedly received complaints, because it issued a technical information letter that suggested swapping-out the supplied pump with one that can operate 16,000 hours before repacking. Many would consider this option a non solution, considering the expense involved.
Mesquite’s solution—with an assist from Bob Jelley, recently retired from ExxonMobil and now in private practice—was to modify the lube-oil pumps to accept about 1 gpm of cooled, filtered turbine oil at about 7 psig for lubricating the upper thrust bearings (Fig 5). Joy led the conversion effort.
This involved removing the lower grease seal, changing the upper seal to an ISOMAG® mechanical seal, and installing Type-316 stainless steel tubing to supply the oil (follow the steps in Figs 6, 7). The nominal $2500 investment per turbine (two pumps) quadruples expected bearing life with no more pump disassemblies and re-packs.
Safety initiatives earn plant VPP Star status
Mesquitehas invested significantly over the last several years to nurture a proactive safety culture and to make physical improvements that lessen the chance of an accident occurring. Making safetyMesquite’s top priority earned the plant VPP Star status in 2009. According to Safety Sponsor Joe Washington, the facility has operated more than 3500 consecutive days without a lost-time accident.
Many of the thingsMesquitehas done others also have done. For example, install inspection and work platforms; eliminate ladders to the degree possible; quickly correct deficiencies; empower staff to address any unsafe situation identified; replace standard bolted HRSG casing doors with quick-latch doors, etc.
Major programs/projects that illustrate the commitmentMesquitehas made to make the facility a safer workplace include the following:
Contractor qualification program. All contractors undergo stringent safety background checks. One of the first things thatWashingtonverifies is reported accident rates. Companies that do not have accident rates below averages compiled by the Dept of Labor, if selected to work at the plant, must have additional onsite supervision or provide dedicated safety personnel to monitor their work. A qualification form thatMesquiteuses is shown in Fig 8.
Contractors also must submit for plant approval job safety analyses before work can begin. Every specific job is assigned a plant employee as Assistant Safety Sponsor.
Mesquite commissioned during the bubble
Sempra Generation’s Mesquite Power LLC was commissioned in 2003 when simple-cycle gas turbines and combined-cycle plants totaling 46,100 MW were connected to theUSgrid. The first 625-MW, 2 x 1 power block began operating in June, the second 7FA-powered combined cycle in December.
GE Energy,Atlanta, supplied the steam turbine/generators as well as the gas turbines. Nooter/Eriksen Inc,Fenton,Mo, provided the heat-recovery steam generators.Black&Veatch,KansasCity, was the EPC contractor.
The plant is located about 40 miles west of Phoenix in Arlington, Ariz, just two miles south of the nation’s largest generating facility—the three-unit 3800-MW Palo Verde Nuclear Generating Station.
Generators. High availability is critical toMesquite’s bottom line and generator exciters are monitored daily for arcing. Recall that the first sign of an impending problem is arcing caused by a progressive loss of contact between the ring and one or more brushes. Preserving the intimate connection between slip rings and brushes is critical to preventing ring fires, which can damage the collector system. Fires can occur virtually in a heartbeat once conditions reach the “tipping point.”
It is important for O&M personnel to address arcing in timely fashion and most understand that. However, close quarters in the doghouse and arcing can be intimidating to almost all but the experienced operator when it comes to adjusting or changing-out brushes. Simply put, brush systems that are not perceived as personnel-friendly often militate against taking the required corrective action.
Ellis understands operators and their concerns as well as any seasoned manager and he championed the idea of swapping-out the OEM-supplied brush system with the user-friendly EASY-change offering from Cutsforth Inc, Bloomington, Minn. Senior Electrician Jim Griesenhauer played a major role in the upgrade evaluation and implementation. Exciter brush systems installed on all of Mesquite’s gas and steam turbines were replaced during an outage in 2010.
For background on the topic, access the COMBINED CYCLE Journal’s editorial archives at www.ccj-online.com and read “Is your exciter brush system meeting expectations?” in the 7F Users Group report published as part of the 3Q/2009 issue, and “How to prevent collector-ring fires,” in the 2011 Outage Handbook.
The plant also changed out the original shaft grounding systems on all turbine/generators with Cutsforth’s new system, which uses copper rope and carbon brushes for maximum effectiveness. Safety benefits include the ability to replace brushes, rope, and wipers while the generator is in service.
The Cutsforth grounding system is said to maintain a lower shaft voltage than OEM solutions, offering a higher level of bearing protection (Fig 9).
Cooling towers. Fires in cooling towers do happen periodically and protection systems must be maintained in top condition. Joy told the editors that Mesquite’s very aggressive tower water had corroded away, in only six years, the exterior of the galvanized steel pipes supplying the spray nozzles.
Solution was to retain galvanized steel for the above-deck mains but replace the galvanized branch lines located within the wet tower environment with Type-304 stainless steel (Fig 10). This project required both engineering and fire department approvals. CCJ
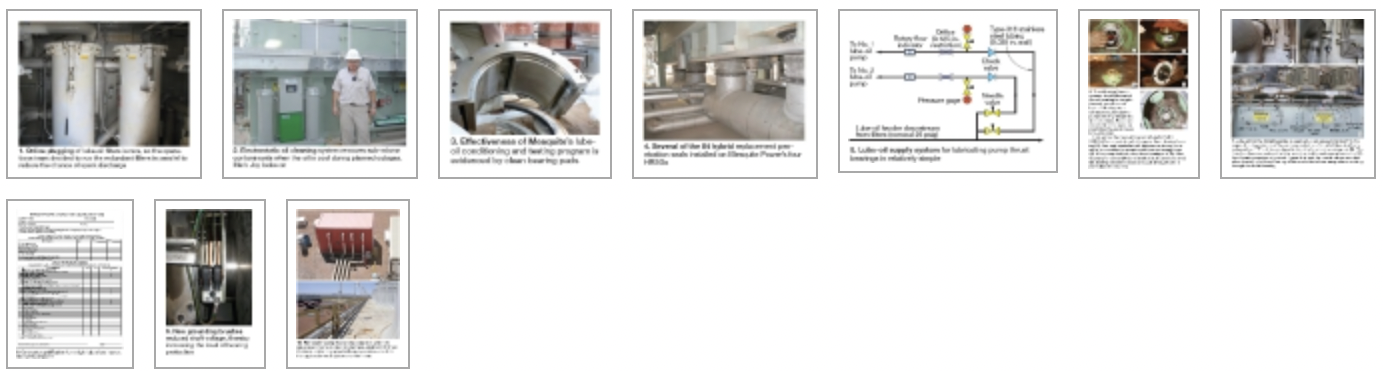