Mitsubishi Power spent a productive four hours with users on the third day of the meeting, discussing and answering questions on a wide range of topics. Presentation segments selected by the editors for coverage here, given their high interest to owner/operators, are the following:
- Safety culture and initiatives to help protect plant and contractor
- Lifecycle experience with critical turbine
- Comprehensive rotor inspections and upgrades—for the air separator and torque tube, in particular—to address fleet issues.
- Exhaust-system
Safety. The Mitsubishi program began with a field-service safety review demonstrating the company’s “safety first” attitude and approach to work. Continuous improvement is the goal of its behavioral-based safety programs.
Similar messages open presentations by virtually all OEMs and contractors these days, but many do not dig into the details like Mitsubishi Power did. The company uses OSHA metrics to benchmark its EHS performance against other manufacturers and service providers serving the electric-power and comparable industries. Example: From 2015 to 2019, its field-service effort grew from 1.1- to 1.7-million man-hours—or by about 50% in just five years.
Over the same period, Mitsubishi Power’s EMR score was stable at 0.6 in round numbers. Not familiar with the acronym EMR? Experience Modification Rates are provided by insurance companies—in Mitsubishi’s case, the National Council on Compensation Insurance (NCCI)— and used by OSHA to evaluate safety standards in the workplace.
The Safety Management Group, which promotes itself as a “nationally recognized” service organization providing workplace safety consulting, training, staffing, and program planning and implementation, says most companies have an EMR of 1.0. Generally speaking, the higher the EMR score, the higher the insurance premium.
Another measure of occupational safety is the Total Recordable Incident Rate (TRIR). It is derived by combining the number of safety incidents and total work hours of all employees in a “standard” employee group—typically 100 employees working 40 hours a week for 50 weeks of the year. Thus, it offers a company the means to benchmark itself against others in its industry, as well as to evaluate its own performance over time.
Mitsubishi Power’s average TRIR for the 2015-2019 period studied was 0.84, well below the benchmark figure of 1.1 reported by a reputable source for the electricity, gas, water, and waste services industry. Manufacturing, by contrast, had a 2.8 incident rate per 100 workers; construction, 2.6.
A goal of continuous improvement means there’s no time off for a good report. Mitsubishi continues to drive its EHS initiatives forward. In 2019, for example, the company was approved for ISO 45001 certification. No findings, major or minor, were revealed during a detailed review of its EHS documentation or during a three-day external audit of its field service safety program. Recall that 45001 is the ISO standard for management systems of occupation health and safety. Its goal is the reduction of occupational injuries—including the promotion and protection of physical and mental health.
Other 2019 highlights of the Mitsubishi safety program included these:
- OSHA safety training—a 30-hr program for site leadership, 10 hours for non-supervisory
- Confined-space, LOTO, fall-protection, scaffold, and hex-chrome courses for all field-service
- An increase in full-time safety staffing by 20%. Highlights of 2020 initiatives are the following:
- Review of recent EHS performance and actions taken, including analysis of behavioral trends to identify deficiencies. One example: Inconsistent PSA (Planning and Safety Assistant) quality was identified as an issue. Deficiencies were addressed in a training
- Pre-outage safety training, one Some of the topics reviewed include site safety plan, proper tool usage, and incident reporting.
- Measurement of training effectiveness and procedure Service and operations managers perform joint site EHS audits—at least one per outage—and share results with executives and staff.
- Improve vendor management through an EHS review and evaluation of key craft vendors, including a follow-on plan for training, safety, etc, to correct deficiencies.
- Increase training in the use of support devices for knees, wrists, elbows, and back, and make more devices available in site safety kits.
Critical turbine parts. Scott Cloyd, chief engineer, gas-turbine service engineering, and his team reviewed product improvements and upgrades for the compressor, turbine, DLN combustion products, liquid-fuel system, and combustion system. In opening remarks, the MHPS engineering team stressed its focus on best-in-class reliability, availability, and lifecycle maintenance cost, suggesting their products are leading the market in these three performance indicators.
To prove the point, inspection results were presented for Rows 1 and 2 vanes and blades— specifically:
R1 vanes. An R1 vane with a service history of 40,020 hours/290 starts (baseload unit) is shown in the left two frames of Fig 6, R1 vane with 14,499 hours/1010 starts (peaking unit) in the two photos to the right. Condition of all airfoils was excellent with TBC intact, no detectable cracks, and no wall thinning attributed to oxidation. Such positive results contributed to MHPS’s decision to validate its R1 vanes for intervals of 32,000 hours/1200 starts.
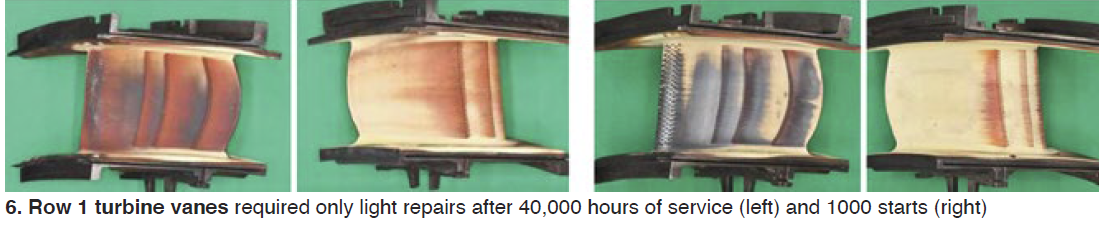
R1 blades in Fig 7 showed similar results with the blade at the left having a service history of 34,676 hours/10 starts and the one in the two images to the right with 6496 hours/1001 starts.
TBC also was intact here. Plus, there was no detectable cracking, or wall thinning attributable to oxidation. Result: R1 blades also were validated for a service life of 32,000 hours/1200 starts.
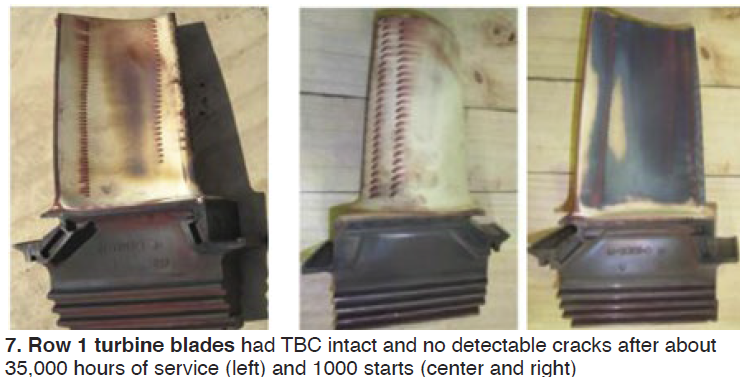
R2 vanes (Fig 8). Experience similar to that for R1 vanes—TBC intact, visible cooling traces, no oxidation-caused wall thinning, no fillet cracking, and only minor cracking on the platform (within the limits of a light-repair scope). Validated for 32,000 hours/1200 starts.
R2 blades also showed TBC intact, no detectable cracks, and no oxidation-caused wall thinning in both baseload and peaking service (Fig 9). Validated for 32,000 hours/1200 starts.
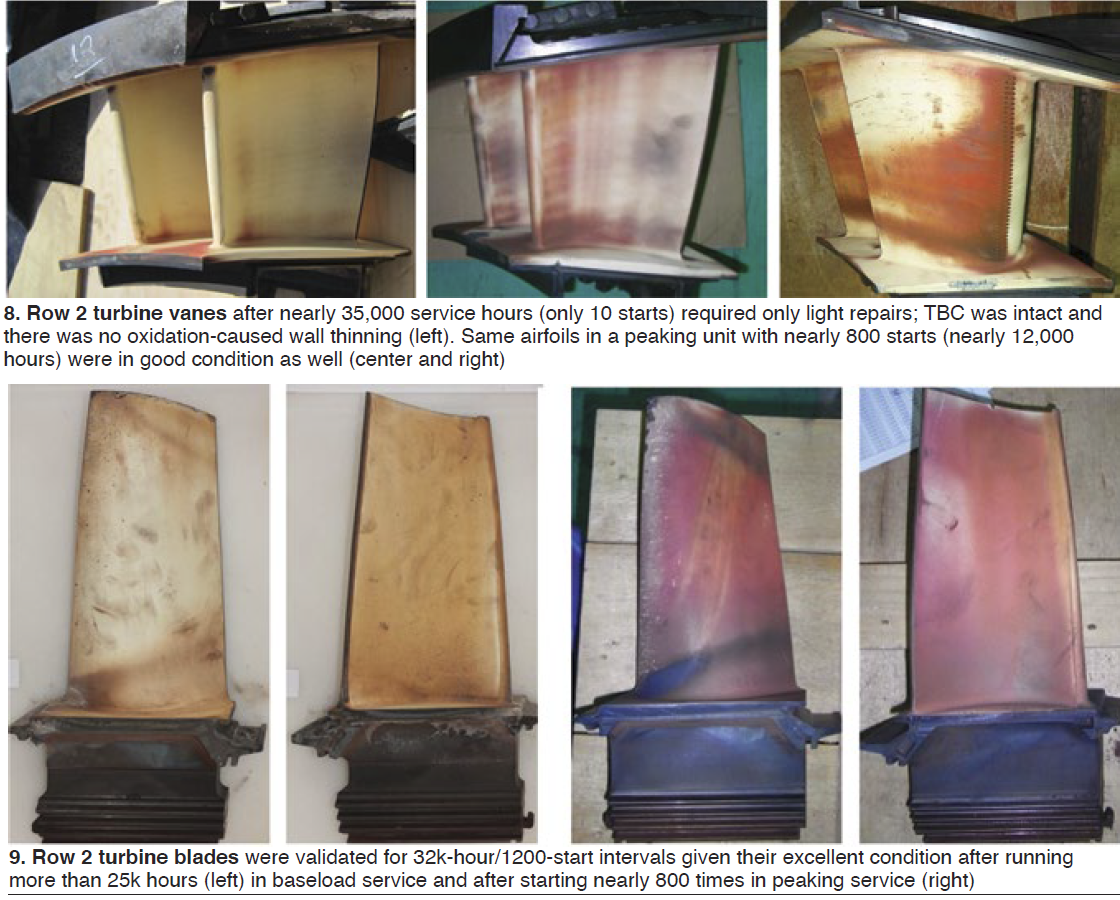
Rotor inspection, upgrades. Mitsubishi Power recommends what it calls a “comprehensive rotor inspection,” or CRI, after 12 years or 100,000 hours of service, whichever comes first. It requires a shop visit and involves complete disassembly of the rotor. All components undergo detailed nondestructive examination; repairs, replacements, and mods/upgrades are performed as necessary to assure performance and reliability goals are achieved (Fig 10).
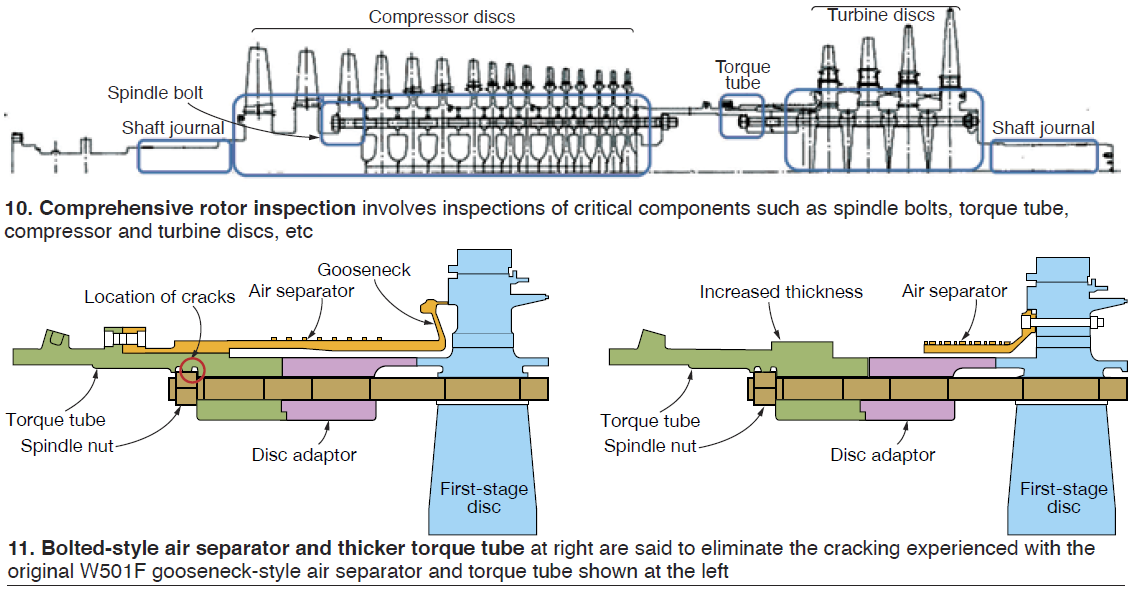
The Mitsubishi speakers touted the experience of the company’s engineers and shop personnel at its Savannah Machinery Works. They also discussed the facility’s state-of-the-art equipment and capability to make complex rotor components, plus the depth of SMW’s material stocking program. Together, the foregoing attributes enable the OEM to provide the flexible solutions to meet customer needs.
While a full CRI is required to qualify a rotor for an additional 12 years or 100,000 hours, Mitsubishi Power often inspects rotors onsite during the turbine inspection (TI) ahead of the CRI to determine its general condition and to develop a risk assessment to guide planning. MHPS calls this a pre-CRI. It reduces the likelihood of emergent work during the CRI by trending data to anticipate refurbishment scope, thereby allowing the owner/operator to source long-lead-time items in advance.
A pre-CRI conducted as part of a TI (so-called Level 1) has no impact on the scheduled outage and includes a disc creep assessment and turbine-blade groove wear and corrosion evaluation.
If the engine owner finds it necessary to postpone a full CRI, Mitsubishi Power recommends a more detailed review of the machine at the major inspection following the TI, one that includes removal of all compressor blades. This Level 2 pre-CRI adds to the Level 1 menu an evaluation of compressor-blade groove wear and corrosion. It also has no impact on outage schedule.
A Level 3 pre-CRI adds cleaning and NDE of all exposed rotor surfaces to the outage scope. Depending on the effort required, this could add to the outage schedule—possibly up to 10 days.
A full CRI in the Mitsubishi Power rotor facility typically takes four weeks, with days added as necessary to accommodate upgrades specified by the owner. A rotor exchange is an option for those requiring a faster turnaround.
Here are some of the important rotor-component inspections conducted during a CRI:
- Spindle bolts, for fatigue or fretting associated with high turning-gear hours and low-speed
- Torque tube, for cracking.
- Turbine-disc cooling-air passages, for clogging attributed to corrosion of the rotor and cooling- air piping and/or foreign material.
- Turbine-disc blade serrations, for wear and fatigue caused by blade rock, pitting corrosion, etc. Curvic clutch, for wear from high hours on turning gear and/or through-bolt relaxation contributing to relative motion between adjacent discs.
- Compressor and turbine discs, for corrosion, cracking, pitting, creep, and/or hardness changes attributed to high operating hours or starts, prolonged exposure to corrosive elements, and abnormal operating conditions.
- Shaft journals, for wear, scoring, and/or cracking attributed to high operating hours, insufficient oil filtration, loss of lube oil, and/or
A focal point of the CRI for most 501Fs is the torque tube, which joins the compressor and turbine sections of the rotor, and its companion air separator. A long-term fleet issue on gas turbines of Westinghouse design (up to and including the Model FD3) has been cracking of torque tubes configured for gooseneck-type air separators, a problem concealed by the air separator (Fig 11).
An indicator of torque-tube cracking is a vibration event, one that can’t otherwise be explained. Although visual confirmation of a crack at this location is not possible, it can be confirmed with an ultrasound scan. If a crack is present, it’s important to implement a solution quickly. Experts say a crack capable of initiating a vibration event propagates slowly at first but then accelerates through a high-cycle fatigue phase to failure.
Mitsubishi Power solutions for a failed W501F torque tube and air separator are rotor replacement (exchanging with a new or refurbished rotor), in-kind torque-tube replacement, and an upgrade option. The last includes a replacement torque tube of additional thickness where cracks have occurred and a bolted air separator (elimination of the gooseneck design). The upgraded components offered by Mitsubishi are said to have operated failure-free for about 3- million hours and 30,000 starts (round numbers) on its M501F engines.
The first Mitsubishi Power torque tube/bolted air separator was retrofitted on a W501F peaker more than two years ago and reportedly is meeting expectations. Several retrofits have been completed in the interim, with others in the pipeline. Mitsubishi recommends replacement of the torque tubes and air separators on all W501F rotors going through its Savannah shop as a risk- mitigation measure.
Exhaust solutions. Mitsubishi’s solutions for the W501F exhaust cylinder and manifold address that model’s recurring durability issues—such as cracking of the diffuser and strut shields. They have been adopted from the successful exhaust systems installed on the OEM’s G and J units (more than 5.3-million hours and 53k starts) which operate at higher temperatures than F engines.
The Mitsubishi Power two-piece exhaust cylinder is a drop-in replacement for the W501F; no changes to auxiliary piping and foundation are necessary. Additional features: no special tooling is required for installation and the journal bearing can be removed with the upper exhaust cylinder casing in place. To date, five W501F exhaust systems have been retrofitted with Mitsubishi’s product.
501FUG: 2020 Conference Review
501FUG: Presentations by Owner/Operators
501FUG: Special Closed Sessions – Doosan
501FUG: Special Closed Sessions – GE
501FUG: Special Closed Sessions – PSM
501FUG: Special Closed Sessions – Siemens Energy
501FUG: Vendorama
Nord-Lock Group solution mitigates 4-way joint leakage
PSM Shop Tour for 501F Users