Hazardous gas detection system
Armstrong Energy
International Power America Inc
625-MW, dual-fuel, simple-cycle peaking facility located in Shelocta, Pa
Plant manager: Matthew Denver
Key project participants: Wes Crawford, Jim Mandella, Peter Margliotti, Bryan Miller, and Dexter Cox, plant combustion turbine specialists
Challenge.
Armstrong Energy is a four-unit, GE 7FA simple-cycle facility. As part of the original installation, hazardous gas detection sensors were located in the turbine and gas-valve compartments. During a TIL upgrade, additional sensors were installed in the collector cabinet and generator terminal enclosure (GTE).
All eight sensors installed were connected to two General Monitor four-channel combustible gas monitors and wired into the Speedtronic Mark VI controls as alarms only. A single composite alarm was issued for any of the four sensors connected to the CGM via a set of contacts located within the CGM itself with no remote monitoring available.
To compound the danger, the sensors were grouped together for the turbine, the gas valve, collector, and GTE so that if the CGM malfunctioned, no alarm or indication would be available for the affected compartment.
Solution.
In order to correct this and provide the operator the ability to constantly monitor the combustible gas levels inside each affected area, the analog signals which were originally omitted from the configuration were used. These analog signals were connected to the Mark VI analog inputs within the same enclosure as the CGMs and terminated in such a way as to provide redundant indication and prevent the complete loss of protection because of the malfunction of one CGM.Logic was created to alert the operator if combustible gases were present in a specific location so appropriate action can be initiated. Additionally, after consultation with our corporate engineering department, a matrix of automatic logic controls was developed and implemented (Fig 40). This provided increased personnel and equipment protection.
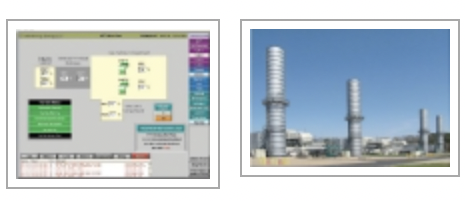
Results.
While the OEM upgrade could be viewed as expensive and complicated, with just a few materials, some locally developed logic, and a few man-hours, Armstrong Energy was able to develop an adequate detection and protection system. This system also provides the operator with real-time monitoring and display via a new screen. The increased ability to accurately detect and pinpoint areas of concern improve safety and reliability and system upgrade is being implemented throughout IPA’s fleet of 7FAs.
Improved ladder cages reduce fall risk
Challenge.
We have a small but safety-oriented workforce that takes pride in maintaining an excellent safety program. One of the most important parts of establishing and maintaining a safe workplace is the ability to improve areas that have the possibility of causing a hazard to personnel.
A fatal accident at another plant brought on the realization that Armstrong could be improved to avoid a similar incident and better protect our staff from fall hazards. While descending a fixed ladder an individual lost three-point contact and fell backwards onto an unprotected section of the ladder. The handrail was too close to the ladder and as he was falling backwards he pivoted over the handrail and fell 30 ft to the ground and died.
An investigation showed that the fatality could have been avoided if a barrier had been installed between the lowest ladder loop and the highest barrier handrail to eliminate or minimize the possibility of a fall from a more elevated position.
Solution.
A site inspection determined that the possibility of injury existed with the fixed ladders installed at our plant. The landing area of 16 ladders (four per turbine) and the handrail was relatively close to the opening of the ladder cage and imposed a fall hazard.
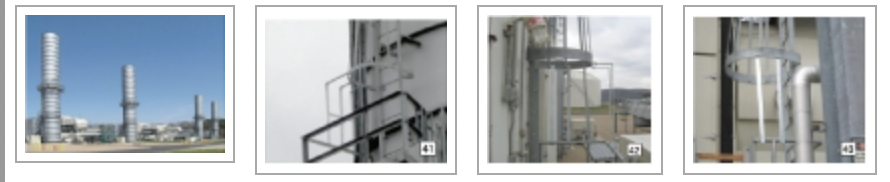
Results.
With the help of an outside contractor, we installed ladder-cage extensions to act as a barrier between the ladder cage and handrail (Figs 41-44). While this does not eliminate the risk completely, it significantly reduces the risk to the individual and may even save a life.