How to improve your water sample panel
By Ken Layton, M&M Engineering Associates Inc, and David Webster, Solutions Inc
PacifiCorp’s Lake Side Power Plant, Vineyard, Utah, completed in 2006, a 545-MW, 2 × 1 combined-cycle facility (Fig 1) was built with an inadequate and unreliable water sample panel. It was difficult to work on, required excessive maintenance, had poor sample-water temperature control, and was poorly arranged.
At any given time, half the sample flows were plugged or analyzers were not operating. Plant personnel had no time to maintain the system and operators lost confidence in what the analyzers were telling them. It is not surprising that the plant had a poor record of maintaining chemistry within established control limits.
Obviously, this situation was untenable. Maintaining steam and water chemistries within prescribed limits is critical to plant performance and maintaining equipment warranties. This article describes the design of a new sample panel and the lessons learned from the project. They apply equally well for water sample panels at any power station.
Background
Monitored water chemistry parameters, for which operating limits are established, include pH, individual chemical contaminant concentrations (for example, sodium, chloride, and silica), conductivity, cation conductivity, degassed cation conductivity, oxygen concentration, oxidizing potential, and corrosion product concentration.
Direct, in-situ measurement—that is, by inserting a probe directly into water or steam at process temperatures and pressures—generally is impossible or impractical. Therefore, continuous samples of water and steam must be drawn from the cycle at locations of interest, transported through sample lines and then conditioned to proper temperatures and pressures before chemical measurements can be made. This is where sample panels come in.
Water sample panels condition the samples to meet the requirements of the analyzers. This sounds simple but it is not. Ideally, the sampling and analysis system does the following:
- Draws representative water and steam samples from designated locations and transports those samples to the panel without affecting the chemistry of the extracted sample.
- Provides for sample-line blowdown to help eliminate pluggage problems and analyzer malfunctions.
- Provides sufficient sample velocity in tubing to ensure turbulent conditions throughout the sampling lines.n Reduces and controls sample temperatures to 25C (77F).
- Reduces and controls sample pressures to approximately 10-15 psig by use of a backpressure valve system specifically designed to provide a constant supply pressure to multiple analyzers fed from the same sample .
- Conditions enough sampled liquid to supply all chemical analyzers and a grab sample.
- Provides sample flow-rate adjustment both for the total flow and the flow to each individual analyzer.
- Assures sample safety relief in the event of excessive sample temperature or pressure.
- Provides flow, temperature, and pressure indication.
- Includes proven and accurate online chemical analyzers that also are low-maintenance, easy to maintain, easily calibrated, and stingy on reagent consumption.
Most importantly, perhaps, the water sample panel achieves the foregoing objectives in a manner that is safe for employees.
Representative samples essentialIf chemical analyzers are to give accurate data, representative samples must be delivered to the sampling panel from the sampling system.
Some water and steam samples are simply drawn from the process pipes through flush-mounted sample tubing—that is, no sampling nozzle penetrates into the flowing stream. However, flush-mounted lines may not draw representative samples from a flowing stream. For extracting water samples from flowing pipes, the ASTM recommends a sampling quill (with a 45-deg beveled end) that penetrates into the flowing stream.
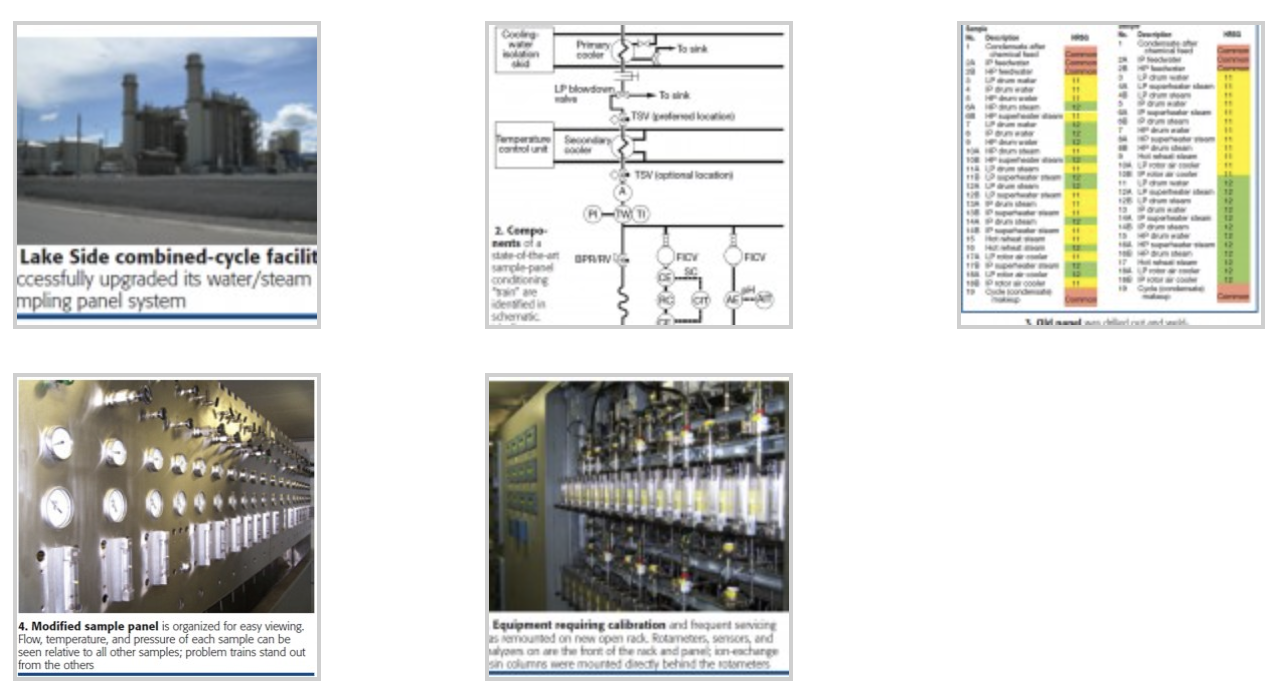
If the fluid that is being sampled is two-phase and if the sample is to be analyzed for particulates or droplets, then samples must be drawn isokinetically. This means that the sample must be drawn through the sample nozzle at the same velocity as the velocity of the fluid in the pipe that is being sampled. The idea is that same-velocity streams don’t bias sampling.
Theoretically, to achieve isokinetic sampling the size of the sample nozzle orifice must be matched to the sample flow rate. In most cases, this is not practical because the flow of the water or steam being sampled is variable, while the orifice size is not. Many isokinetic nozzles have been installed but too often little attention is paid to the correct sample flow rate.
How serious is it if samples are not drawn using recommended sampling methods? It depends on the sample being analyzed, which chemical constituents are being analyzed, and what action is taken based on the analytical results. Remember that whenever droplet or particulate concentration is to be determined with accuracy, the sample must be drawn isokinetically.
Previously, some designs for sampling superheated steam specified that sample desuperheaters be installed close to the sampling location. The idea was that certain chemical species (sodium, for example) that are soluble in superheated steam precipitate from the steam sample as the sample cools on its way to the sample panel, thus biasing the sample. Although a best practice, few of these sample desuperheaters have been installed.
Industry practice is to provide for a 6-ft/sec liquid flow rate through the sample tubing. The reasons for the minimum flow rate are to ensure that the rates of particulate deposition and shedding in the sample line are in equilibrium, as well as to minimize sample lag time. Plus, it prevents particulates from accumulating and plugging sample lines.
However, high sample velocities equate to high volumetric flow rates. For example, using ¼-in. tubing of 0.042 in. wall thickness, about a quart and a half per minute (1500 ml/min) of sample water is required to provide a velocity of 6 ft/sec. That’s more sample flow than is required for one or two analyzers plus the grab sample. And cooling 1500 ml/min may exceed the capacity of sample conditioning systems typically provided with today’s panels.
Larger sample tubing, such as 3?8 and ½ in. diameter, also are common and obviously put an even greater burden on coolers if samples flow at 6 ft/sec. If only the required analyzer flow rates are drawn through these larger sample lines, much lower velocities would result. In such cases, sample-line particulate buildup occurs and the tubing plugs. One solution is to operate all sample lines at the recommended 6 ft/sec, but to divert all sample water not needed for the chemical analyzers (and grab sample) from just ahead of the coolers.
Important to remember is that there are competing considerations when it comes to choosing sample flow rates, sample-line tubing sizes, and sample-panel cooling capacities. Each sample line must be evaluated, together with sample-panel requirements, to determine the optimal tubing size.
The original sample-line sizes at Lake Side ranged from ¼ to ½ in. No sample lines were replaced as a part of the sample-panel upgrade project. The blowdown and filtering capacity added as a part of the project will partially eliminate sample line and sample-panel fouling. The newly installed panel cooling capacity is adequate to cool all samples.
Panel design
A water-sample panel should be located in a temperature-controlled, clean, and well-illuminated environment. That could be a separate room inside an existing building or a separate enclosure or building. The room should have adequate safety exits and should be large enough, and the contents arranged well enough, to allow easy access for maintenance. There should be sufficient space for storage of chemical reagents and spare parts. Specify stainless steel for all sample lines, valves, and components.
Fig 2 shows, schematically, the components of an ideal water-sample-panel conditioning “train.” Ideally, there should be one train for each sample, but each train may supply sample water to multiple analyzers as well as the grab sample. Some of the principal features are described below:Isolation. Occasionally the sampling system must be isolated from the sample panel. One example: Most water and steam samples carry some particulate matter which, over time, will plug sample lines and panel components, and may affect analyzer operation. To eliminate such accumulation, specialized strainers with backwash capability are installed. They can be valved in, when necessary, to purge the sample lines.
The blowdown valves and strainers are relatively new components and are installed in parallel with the isolation valve. In the case of high-pressure samples, such as HP and IP steam-drum water samples, these strainers and quarter-turn nitrided isolation ball valves give reliable service.
Primary coolers typically consist of coiled sample lines inside cylindrical stainless-steel housings. Treated plant cooling water flows through the housing. A pressure relief valve is installed at the cooler inlet to prevent over pressurization of the vessel.
A pressure reduction valve of the rod-in-tube capillary-type generally is included to reduce sample pressure. Pressure drop is controlled by screwing the rod in or out of the capillary flow path. Expect the valve to plug periodically. When it does, the rod can be backed out to purge debris. One company now makes a motorized rod for tube PRVs.
When 6 ft/sec is maintained in large-diameter sample lines, water in excess of what is needed for analyzers and the grab sample is usually is diverted to drain. In such cases, a rotameter would be installed downstream of the PRV to measure total sample flow. A manually operated low-pressure blowdown valve allows periodic sample-line blowdown.An isolation valve of the automatic, temperature-activated type stops sample flow should sample temperature exceed the set point. This valve is located downstream of the PRV. Its purpose is to protect downstream equipment should the primary coolers fail to cool the sample adequately.
The secondary cooling system consists of additional sample coolers, similar in construction to the primary coolers described above. Source of the cooling water for the secondary coolers is a mechanical chiller.The chiller modulates secondary cooling-water temperature as required to maintain sample temperatures at 25C. Downstream of the secondary cooler is a cluster of analog gauge indicators (flow, pressure, and temperature) that give the final report card on how the upstream components have performed in conditioning the sample. All trains should be controlling sample temperature to 25C.
Backpressure relief. Downstream of the cluster of gauges, the sample flow branches into several flow paths. One indispensable branch is the backpressure relief valve (BPRV). This device, and its location in the sample conditioning train, is important for proper operation of the panel.
The BPRV maintains constant sample pressure upstream of the valve, as well as sample pressure to each of the branches where the analytical instruments are located. With this arrangement, constant flow is provided to the analyzers, contributing to their reliability.
The BPRV is a long-lived component that passes whatever flow of sample water is necessary to maintain upstream pressure. The bypassed flow is plumbed to the sink and becomes the “grab sample” flow for that sample.
From this point forward, flow to each branch—that is, to each analyzer—is regulated by individual flow-indicator control valves (rotameters).
- The ideal panel layout should have the following characteristics:
- Locate analyzers, readouts, sensor probe housings on the front of the panel.
- Locate flow adjustment and indication rotameters on the front of the panel.
- Use quick-disconnect fittings with flexible hoses, as required, to facilitate the removal of analyzer sensors and replacement of ion-exchange columns.
- Limit ion-exchange column diameter to approximately 3 in., to eliminate the channeling of flow through the resin. Channeling reduces the capacity of the ion-exchange columns.
- Arrange sample conditioning trains in a logical sequence, with samples from each unit and common support systems grouped together and labeled with descriptive words as well as with sample numbers.
Application at Lake Side
Consistent with the foregoing, the Lake Side sampling panel was modified to include new HP strainers (80 micron) and blowdown valves installed in a new insulated cabinet attached to the outside of the panel enclosure. Flow from the sample-line blowdowns is discharged to a yard drain. Quarter-turn blowdown valves were installed and have given excellent service.
The old panel was drilled out and weld-patched as needed to accommodate the new panel configuration and different components (Fig 3). Because of limited space in the sample-panel room, and limited budget, the panel was modified so that two samples, one critical sample and one less critical sample, share the same conditioning train. One train for each sample would have been ideal, but the new configuration works.
A 10-ton chiller was installed adjacent to, but outside of, the existing water-sampling-panel enclosure. Secondary coolers were added to the existing sampling-panel rack below the existing primary coolers. Sample lines were replumbed from where the lines enter the sample-panel enclosure, to their new locations.
Gauges for each parameter (flow, temperature, pressure) on each sample were arranged vertically, one above the other, such that when the indicators for all samples are viewed horizontally in a row across the sample panel, operators can quickly see which, if any, conditioning train is not working properly (Fig 4).
The sample relocation puts the samples in logical sequence. Each HRSG’s samples are grouped together as are samples from the equipment that is common to both HRSGs. New, durable, easy-to-read labels are affixed to the panel face at each sample train location and at each analyzer and analyzer probe. Previously, in order to read a chemical parameter for a given stream, operators had to look up the sample-line designation on a sheet. Then they had to trace the sample line to know which analyzer the sample went to.
All rotameters, analyzers, and probes were remounted to the front of a new, open rack to make calibration and servicing easier (Fig 5). Ion-exchange columns were mounted directly behind their respective cation conductivity sensors and installed with quick-disconnect fittings, quick-coupling mountings, and flexible hoses. All sensor housings were installed with clamp-type mountings to provide for easy sensor removal, without having to twist the sensor cable as was done previously when unscrewing the sensor for removal.
Online analyzers were located away from their original near-floor-level position. Reagents for the online analyzers, previously located on the floor behind the panel, now are closer to the analyzers, and are elevated.
Additionally, a stainless-steel sink was installed under the new sensor panel on the front of the panel. It receives sample discharge from the sensors. A short extension to the panel face was installed, too, allowing new and repositioned online analyzers to be mounted to it.
Finally, new backpressure control/relief valves were installed in the new location. This was a key modification. The new valves provide consistent flow through the sample conditioning and analytical portions of the panel. All modifications to the sample panel were made without taking the HRSGs out of service. No operational delays occurred because of the modifications.
Real world constraints
Ideally there should be one sample conditioning train for each sample, and analyzers should not be shared among samples. However, to meet financial and space constraints, each conditioning train can be arranged to treat two samples, as described above. For this project, it was decided to share the conditioning train of one highly critical sample with one less critical sample. The highly critical sample normally is valved into service while the less critical sample is valved in as needed.
But before sharing sample conditioning trains or analyzers, give careful thought to which samples and analytical parameters are critical, and therefore deserve the primary, continuous sample, and which may be responsibly shared as the secondary sample. Previous unsatisfactory experience with automated sample sequencers discouraged their use at Lake Side.
Some of the original online chemical analyzers were retained, others replaced. To maximize reliability and accuracy it is vitally important that simple, high-quality analyzers be used. The existing data logging and trending system was adequate. The data points from the analyzers were simply input into the existing system. Reliable chemistry information is now readily available locally as well as in the control room so operators and others can make informed decisions. ccj