Spare-parts strategy critical to asset availability
The EUCG Fall Workshop, held the first week of October in Indianapolis, featured a panel of experts on gas-turbine (GT) spare-parts strategies who offered valuable insights on how to assure timely availability of spares to maintain high engine productivity without going broke. It was clear from the discussion that a “one size fits all” strategy doesn’t exist. The program that best meets a given plant’s needs most likely will be a unique arrangement of proven ideas unique to the asset’s O&M schedule and balance-sheet requirements.
Perhaps the first question that comes to readers’ minds: What is EUCG? Unless you’ve been in the electric power industry for more than 30 years and have some nuclear blood, you may not know. The Electric Utility Cost Group was formed in 1972 by several utilities building nuclear plants to share information. Goal was simple: Improve the performance of engineering/construction activities to reduce costs.
Today the group is known simply as EUCG Inc and its global membership includes both regulated and unregulated power producers. Participants are focused on improving their competitiveness by sharing information through cost and performance databases, networking, and benchmarking. Strategic planning, maintenance practices, outage management, and other aspects of plant operations are the subjects that underlie most group discussions. Workshops are conducted each spring and fall. For more information, visit www.eucg.org.
The editors were invited to participate in the CC/CT session of the Fossil Forum (the other forums are nuclear, IT, T&D, and hydro), chaired by SRP’s Barry Drost. Vice Chair is NV Energy’s Tom Price, who manages combined-cycle and peaking assets totaling 1900 MW at the utility’s Clark, Sunrise, and Walter M Higgins Generating Stations in theLas Vegas area.
This group’s program included the spare-parts roundtable mentioned above, progress on a survey of 7FA outage experience being conducted by Russ Arlotta of Public Service Electric & Gas Co (PSEG), an update on an SCR benchmarking study directed by Price, and a review of Drost’s ongoing efforts to develop a comprehensive CC/CT database for identifying best performers.
Drost and Price selected for the spare-parts panel managers representing companies with many, several, and few GTs, to get a diversity of approaches to spares management.
Large fleet
The first speaker’s company has about 9000 MW of frame GTs in combined- and simple-cycle arrangements at more than a dozen locations. Nearly 30% of the 100-plus engine fleet is F-class machines operating under an OEM LTSA. Some of those assets were purchased from the original owner with a condition of sale being the acceptance of the LTSA in force. The presenter said the following three tactics were employed for managing parts, depending in large measure on equipment age and the number of like engines in the company’s fleet and at a given plant:
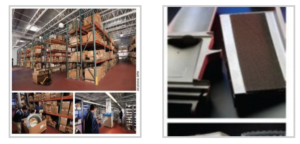
Plant ownership. Maintain parts onsite sufficient to support a given plant’s operations. This is a relatively simple and effective approach for mature assets with known parts histories; hardware purchases are controlled and managed to meet the plant’s specific needs. A benefit of this method is that parts are available when you need them—or at least they should be. Risks include high upfront costs for parts purchases and no cost sharing for parts replacements.
Fleet ownership. Fleet spares are retained in a central warehouse and shared among units at multiple locations. Advantage for large fleets: Fewer spares are needed per unit. Risks: (1) Plants with a high operational profile may get priority over others, (2) cost of central warehousing can be significant, (3) probably less knowledge of parts history than if the plant owned the parts, and (4) repair pedigree is more difficult to maintain.
Group ownership. In some instances, the sharing of parts among multiple generators with third-party management of those spares can make sense. Big benefit is the shared upfront cost for parts, which may make most sense for big-ticket items—such as a compressor, generator rotor, etc. Parts replacement costs are shared as well. Another benefit is having personnel to track parts and their repair pedigree.
Risks include parts controlled and managed specifically to meet contractual obligations of specific partners, as well as routine fees associated with parts management and warehouse operations. Perhaps the biggest risk is the defection of participants over time because of asset sales, changes in generation-company ownership, etc. If you start with five or six partners and the number drops down to two or three over time, it might become cost-prohibitive to continue the group relationship.
Small fleet
The second speaker represented a company with half a dozen F-class GTs and four 7B-E engines serving in combined cycles, plus another six early frames in simple-cycle arrangements. Here’s a thumbnail sketch of the parts strategies being used:
- For its four 7FAs, the utility has a non-exclusive MMP (multi-year maintenance program) contract with the OEM. It has no non-OEM parts at present but such parts are not ruled out for the future. Two complete sets of HGP (hot gas path) spares are retained; outage work is self-performed with a GE technical advisor to guide the effort. Repairs typically are bid competitively.
- The utility maintains either one or two sets of spares for its two 501FD2s. One engine is under a short-term CSA (contractual service agreement), the other is totally self-perform. Third-party transitions and first-stage blades, vanes, and ring segments are in use.
- For the four 7B-E machines, the company maintains one set of spare combustion hardware and first-stage buckets, nozzles, and shrouds. It is willing to take longer outages to make R2 and R3 repairs during the outage and return the repaired components to service. With proper planning, the speaker said, R2 and R3 buckets typically can be removed, repaired, and returned within three weeks. Repairs are bid competitively on a case-by-case basis. Regarding spares purchases, mainly GE, but the company has some third-party buckets and combustion liners. Overhauls are self-performed with an OEM technical advisor.
Generally speaking, the presenter continued, his company looks to work with vendors having extensive experience that are willing to negotiate master terms and conditions. An approved-vendor list is maintained by component; repair specifications generally are based on EPRI guidelines. Being selective, he said, is conducive to reducing repair turn times and can forego the need to buy spare parts.
Looking ahead to 2012, the speaker noted, the company is looking at three 7FA HGP outages in a six-month period with two sets of spares. Plan is that one set of parts from the first two units must be repaired for the last unit to avoid buying new parts. This means that a turn time of less than 16 weeks is required, which the speaker did not see as a problem—at least for third-party shops. He believed that three to six months of lead time is sufficient to line up such a contract.
In wrapping up, the speaker said his company was pursuing the opportunity to save money by extending parts life. Internal due diligence on a component basis is being conducted it see if going beyond OEM recommendations is possible and, if so, by how much in terms of hours and/or starts. EUCG workshops give the company the opportunity to talk to owner/operators at the “leading edge” to benefit from their experience.
Engineers currently are investigating life limits on DLN2.6 liners, transitions, and fuel nozzles, he added. Such stationary hardware are viewed as a lower risk for life extension than rotating parts. For some components, the speaker continued, the cost differential between repair and replace can be as much as a factor of 10.
Single-plant entity
The third speaker represented a single-plant entity operated by a third party. The 2 x 1 7FA-powered combined cycle is covered by a turbine-only LTSA. He described a pragmatic approach for arriving at spare-parts requirements. It was a particularly valuable lesson for someone trying to develop a parts plan for the first time. Asset management philosophy was an important consideration, he said, and suggested the answers to the following questions were a prerequisite for decision-making:
- How do you expect your plant to operate?
- What’s your company’s appetite for risk? Specifically, what components will be covered by a service agreement and how will the agreement be constructed? What’s your company’s philosophy on levels of taxable inventory?
- What’s your spare-parts budget; what parts can be charged to plant construction?
- What do you expect your operating budget to look like?
- How will your plant be staffed?
Next, conduct a failure analysis on each plant system and rank the necessity of each component. Then do a component-by-component failure analysis in priority order. Follow that analysis with an evaluation of maintenance requirements for top-priority components. The goal of this evaluation is to determine the level and frequency of maintenance, and the impact of the repair evolution with or without spares.
The next critical item is a cost/lead time evaluation. Here the goal is to determine repair costs and times for priority components and compare that information against the lead times and costs for new parts. Don’t forget to evaluate space, climate-control, and other special requirements into your analysis. Output from this study will be valuable perspective on the specific spares necessary as well as stocking requirements.
Critical for the future is the development of an obsolescence migitation plan. Routinely spot-check parts on a progressive timeline with the goal of identifying obsolescence before it bites you.
The EUCG databases under development promise to compile valuable benchmarking information that might not be readily available from any other source. But to participate, your company must join the organization. To learn more about the 7FA outage survey and the database being populated to identify best CC/CT performers, contact Drost at barry.drost@srpnet.com.
The SCR benchmarking study aims to gather information on intervals between catalyst cleaning, rejuvenation, and replacement; the time and costs associated with those activities, etc. Price already has information on 39 SCRs and is looking for datafrom many more installations. You can contact him at tprice@nvenergy.com. CCJ
Latest generation stats presented to EUCG members show new wind capacity well below expectations
It wasn’t long ago that capacity additions for the electric-power industry were so easy to predict accurately that a neophyte could look like a genius. Installed capacity simply doubled every 10 years from about the end of WWII through the 1970s, when American industry was booming and the economy was expanding.
Today, predicting future capacity requirements is a crapshoot. Project financial viability hinges in part on flexibility—the ability to move project completion dates forward with minimum penalty if demand doesn’t increase as expected. Gas turbines (GTs) fit the indecision model well because they are the least expensive “big-power” option and can be built in the least amount of time.
Gas turbines also are the “best bet” technology because they are “least offensive” big-power option environmentally. In the mid 1970s, not many would have bet against nuclear as the dominant generation resource for the future. But thenThree Mile Islandhappened and more nuclear capacity was cancelled than was ever built. In the 1980s and 1990s it didn’t look like anything could slow the construction of coal-fired plants. But EPA has. Most recently, the nuclear renaissance that promised to pick up where coal left off appears to have been washed away by the Japanese tsunami—at least for the near term.
Nuclear and coal conveniently cast aside, renewable resources—wind and solar, in particular—have been promoted as the nation’s energy future. The sales pitch: Essentially free energy with little or no environmental impact, rolled up with jobs creation. This cast renewables as an instant success story—at least in the minds of politicians.
But because wind and solar are intermittent, these assets must be backed up by generation that can operate at night, in high wind, in no wind, etc—a “detail” in the minds of the promoters. However, there’s a positive here for several OEMs: Increased sales of GTs, the preferred generation resource for backup duty.
Looking at the type and amount of capacity added in the first seven months of 2011, one has to wonder if the nation’s love affair with renewables might be over, or nearly so. According to data published by the Energy Information Administration (EIA), only 3010 MW of wind generation was added during that period, slightly more capacity than the five large coal-fired facilities that began commercial operation (2673 MW) and less than half the 7013 MW of simple- and combined-cycle gas turbines.
A reasonable question is “What does that prove?” Not much, except that at the end of last year, the expectation was that 45,000 MW of wind would be added in 2011, based on information provided by that industry sector to Energy Ventures Analysis Inc (EVA), the respectedArlington(Va) energy forecasting firm. There was only 42,300 MW of wind-turbine capability installed in theUSat the end of September, according to PlattsUDI, a division of the McGraw-Hill Companies.
GT additions. There has been an uptick in new GT installations; some industry experts are calling it a mini-boom. Note that the new capacity predicted for 2011—11,400 MW—is well within reach with 7013 MW already in operation at the end of July. But if wind goes south, one has to wonder how much of the GT capacity planned for the next few years will be needed.
The big picture. Total US generating capability at the end of September was 1135 GW, according to Platts UDI. Generating facilities powered by gas turbines today can produce 390 GW, or more than one-third of the country’s total capacity. The breakdown: combined cycles, 218.2 GW; simple-cycle GTs 150.4 GW, GTs in cogeneration service 13.2 GW, and combined heat and power (CHP) facilities 8.3 GW. To putAmerica’s GT capacity in perspective, consider that it exceeds the [IT] total [RM] generating capability of every nation other thanChina.
Primary energy. The declining price of natural gas is an important reason gas turbines are operating more and equipment orders are on the upswing. The Henry Hub spot price on September 21 was $3.78/million Btu, 28 cents lower than it was a year earlier. One of the big unknowns is how long the price of gas will remain at the current level. Some experts put gas reserves at about 100 years for the current consumption rate of 24 trillion ft3/yr. You may recall that 40 years ago, the “experts” said we had a seven-year supply and consumption was less than one-third of what it is today.