There’s nothing generic about generator failures
By Clyde V Maughan, Maughan Generator Consultants
Root cause analysis is never easy, but the dearth of true field expertise with generators has led to improper diagnoses, incorrect responses, and significant costs to owners and OEMs, much of which could have been avoided.
Original equipment manufacturers (OEMs), which used to send out their factory engineers to diagnose plant failures, now have fewer such experts and they are usually needed elsewhere. Generator service firms may have one or two experts with the skill levels required.
Also, generator failures are more difficult to diagnose than failures in other major powerplant components, such as boilers and turbines. Typically, no one at the plant site knows much about the generator. Finally, even records from state-of-the-art monitoring devices may not shed light on failure causes, and such records are often disorganized or not retained. Diagnostic
errors often are expensive (sidebar).
As a checklist, owner/operators should (1) monitor their generators with state-of-the-art equipment and keep that equipment in good working condition; (2) record, retain, and organize all monitoring data; (3) assure that the failure investigation is thorough and the conclusions are plausible and reasonable; (4) bring in additional technical support as early as possible if you are not comfortable with the information being presented to you; and (5) if qualified OEM diagnostics personnel are not available, find other sources of technical support.
The failures described below, as well as many other failure modes, point to an over-arching conclusion: While there may be common generator failure modes, it can be costly to generalize about specific failure incidents. Root cause analysis (RCA) tends to be unique except to the most common failure modes.
Pretty soon it’s real money
Each of the five diagnostic errors described below cost between a few hundred thousand dollars and many millions
of dollars.n A “ring of fire” type stator winding failure on a 900-MW water-cooled winding was incorrectly pegged to the piping. The correct failure mode was identified after further investigation, avoiding a repeat of the massive failure.
- A 200-MW unit failed twice within several months because corrective action was taken the first time based on a misdiagnosis of “lightning” striking the stator winding.
- Contamination of a core end-package was attributed to minor stator-bar vibration. No corrective action was taken. The root cause proved to be local core looseness and the winding failed to ground a few weeks after the unit was returned to service.
- Core discoloration was overlooked at the location of a stator winding failure in an 80-MW unit. The stator was rewound without correcting a core-iron condition, and the replacement winding failed shortly after the unit was returned to service.
- When an asphalt stator winding was incorrectly diagnosed as exhibiting rapid migration of the ground wall, the recommendation was to immediately rewind the stator. In fact, migration had long ceased and the machine needed no repair.
Stator RCA
Endwinding looseness. Local or general vibration distress is often found on large generators. Problems are occasionally associated with vibration in the entire endwinding (Fig 1), but usually the effects are localized (Fig 2). Note the characteristic white dust generated by endwinding looseness in the first photo (an oil-mist free generator) and local “greasing” in the second (with the common minor oil internal contamination). Possible root causes are resonances, insufficient ties and blocks, lack of bonding, loosening of clamping forces, and loosening caused by short-circuit forces.Stator RCAWinding failures—endwindings, connectionsStator winding failures are one of the most frequent causes of generator forced outages, and windings can fail in numerous ways.
Electrical connection failure. Exposure to connection failure is significant because stators have many electrical connections. In Fig 3, local resonance is likely responsible for the burned connection ring, though given the extent of burning (note that 12 in. of the lead is gone), identifying a root cause is probably futile. But after repair, the natural frequency must be confirmed to be at least 15-20 Hz above double the operating frequency.
A series connection failure is shown in Fig 4. Again, the extent of burning has made accurate root-cause identification next to impossible, but resonant vibration is more likely than an inadequate electrical joint or phase-to-phase electrical failure.Fig 5 shows one section broken on a unit with a 28 parallel-circuit series connection. The photo is of a broken braze on a top-to-bottom bar series connection. The current lost in the broken section is easily carried by the remaining 27 circuits with about a 4% increase in temperature. Arc damage is minor and the root cause—vibration of the joint—can be established with confidence. However, all corrective actions are not equally reliable.
In Fig 6, half of a series connection is broken. When this happens, the current is transferred to the other half of the bar, doubling its temperature rise, but arc damage isn’t significant. The evidence of root cause is clear—omitted series-connection blocking permitting resonant vibration.The most common root cause of these types of failures is local resonances, although general endwinding resonance may also occur. Testing the failed winding’s natural frequencies can assist in the RCA since the overall natural frequencies may not have been significantly affected by the failure.
Running-frequency resonances tend to be associated with insufficient blocking and tying, occasionally because the OEM is trying to shave costs. Bump testing of the winding can identify resonant frequencies. Keep in mind that natural frequencies will be lower when the winding is hot after being placed in service and will be further reduced over time by operating duties. It also is helpful to review operating experience on duplicate generators or ones of similar design.
Foreign object damage. Evidence of FOD is usually visible (Fig 7), such as when something is lodged between bars in an endwinding. Sometimes, the foreign object is hidden or embedded between layers, or burns up during the failure.
FOD may also result from generator components becoming loose and lodging in vulnerable areas. Fig 8 shows a loose stator-winding blocking component that has worn completely through the insulation on a connection ring. Fortunately, the ring was at neutral voltage and winding failure did not occur.
Maughan on generators
This is the fifth article in a continuing series on generator monitoring, inspection, diagnostics, and root-cause failure analysis developed by Clyde V Maughan, president of Schenectady-based Maughan Generator Consultants, for the CCJ.
The articles listed below, available at www.ccj-online.com/maughan/, are a valuable resource for owner/operators of turbine-driven generators:
- Maintaining carbon-brush collectors, 1Q/2010.
- Options for monitoring generator condition and their limitations, 2Q/2010.
- Input from monitoring, inspections, tests critical for maintenance planning, 3Q/2010.n Generator condition monitor critical to avoiding catastrophic loss, 1Q/2010.
- Root-cause diagnostics of generator service failures, 2011 Outage Handbook.
Turn shorts. The arc damage shown in Fig 9 may completely eliminate the possibility of determining root cause, although the three most probable root causes are: (1) strand or turn shorts in one of the involved stator bars, which could be identified by overheat damage of the strand insulation in the full length of the bar; (2) fractured strands in a bar (unidentifiable); and (3) foreign object (possibly identified).
Inadequate connection insulation. Generators designed with exposed copper at the connections rely on physical spacing to hold the high voltage. The spacing must remain uncontaminated for safe operation. If conductive plasma occurs from a connection failure, or other source of contamination, the phase joints and series joints may flash over. The result has been termed a “ring of fire” (Fig 10).Winding failures—slot portion.
Commonly, older units with inadequate wedging, as well as large direct-cooled machines, experience bar vibration in the slots. Root cause may not be obvious but primary diagnostic actions would be to assess the severity of vibration and establish its root cause. Indications throughout the entire core are likely related to general looseness of wedges. But if indications are only located at the ends, the root cause is almost certainly bars held off the slot bottom by the endwinding support (Fig 11), not inadequate wedging.
If red oxide is visible on the wedges and the iron, the likely root cause is simply individual wedges vibrating, not bar vibration (Fig 12). It is important to distinguish between bar and wedge vibration, because the former is always serious, the latter is not.Vibration sparking. Distinguishing between partial discharge (PD) and vibration sparking isn’t easy. The indications are similar in appearance (although evidence of vibration sparking tends to be dark in appearance and PD tends to leave a whitish appearance). But the pattern is different—that is, PD can only occur on the higher voltage bars while vibration sparking can occur on all bars.
PD represents slow deterioration, while vibration sparking may fail a winding in a year or two of operation. Indications of damage may be seen at the ends of the slots (Fig 13a), and through the ducts (Fig 13b) on machines with radial ventilation ducts. Assessment of severity of damage cannot be made short of a hipot test. OEM recommendations for frequency of inspections and repair should be followed.
Partial dischargeIndications of PD may be widespread in the slot and endwindings (Figs 14-17). The Y-connected, two-circuit, two-pole windings shown in the photos have three locations of phase-to-phase voltage break at 120 deg in the endwinding. The initial assessment of the damage in Figs 16 and 17 was that lightning striking was the root cause. The correct analysis was clearly PD in the presence of non-mica insulation.
Note that in Fig 14, PD is in close proximity of bar ties at a line-to-line phase break; in Fig 15 there are heavy PD indications at a line-to-line phase break; in Fig 16, PD is at a phase connection location where there was no failure; in Fig 17, the failed connection was in evidence after removing insulation.
More generally, root causes of endwinding PD are inadequate endwinding grading paint/tape materials or application and/or inadequate physical space. Until a failure actually occurs, assessing the extent of PD damage to the groundwall insulation is difficult, short of conducting a hipot test. While there may also be damaging burning between the endwinding grading and slot grounding systems because of inadequate connection, this is not true PD.PD shows up in the slot portion of the winding somewhat differently (Figs 18, 19). In the first photo, PD activity can be seen on a bar surface beyond the wedging; in the second, wedges have been burned away by severe PD on a stator bar. Even though an accurate assessment of root cause cannot be made in either case, clearly the semi-conducting tapes/paints are inadequate.While PD may be widespread in a stator winding, failure of a winding caused by pure PD acting on mica insulation is rare, if non-existent. Nevertheless, because of fundamental uncertainties relating to the progress rate of PD attack, rewind is sometimes the preferred option. Furthermore, on air-cooled generators, high levels of ozone can be generated by the PD. The associated hazards may force a stator rewind since it is impossible to repair the damaged grading paints in all locations of the slot and endwindings.
Strand header leaks
Strand header leaks are an on-going problem with some water-cooled stator windings. Capacitance and Wet Insulation Detector (WID) tests are available to assess water contamination of the insulation. Also over-voltage testing will detect wet insulation. If a bar is confirmed to be wet, the root cause almost certainly is leaking in the braze between the strands in the electrical clip (Fig 20). Wet insulation cannot be reconstituted, and it is necessary to remove the bar with damaged insulation.
Tape migration
As old as this problem is, it is still poorly understood. Currently associated only with asphalt insulation systems (Fig 21), tape migration is mostly confined to very old generators from one OEM, but it has also been seen on some small coil-winding generators made up to 1990.Little can be done to control future tape migration in these windings. The nature of the insulation system in the old, pre-1960 windings is such that the insulation became much less prone to migration as the winding aged and will have ceased after a few years of operation. On the newer units, migration will continue until failure occurs or the winding is replaced. Obtaining an accurate assessment of winding condition by inspection alone is nearly impossible. Hipot tests are required.
Contamination
General contamination can be seen at a glance (Fig 22). Common contaminants are water, oil, outside ambient dirt, and internal dust from inadequate cleaning or wearing parts. While actual source and impact may be difficult to ascertain, if the source can be identified, corrective actions are usually obvious. Unfortunately, elimination of on-going contamination may be very difficult and costly, for example water penetration on an outdoor installation.
Stator core failures
Cores failures are many and varied, and root cause may be difficult to establish. However, because repairs of core failures are usually extensive and costly, it is particularly important that the correct root cause be established.
Core looseness. A loose core should be readily apparent. Normally, dust generation occurs at the area of looseness. Inserting a knife into the core where looseness is suspected will confirm local or general looseness (Fig 23). If you assume that the dust on the core (Fig 24) results from bar or wedge vibration, core looseness may be overlooked. In such a case recently, the incorrect diagnosis resulted in winding failure a few weeks after the unit was returned to service.
Local core overheating. Core overheating shows up as local hot spots, bands of discoloration, local burn spots, and massive meltdown. In Fig 25, the damage is minor and appears to have been caused by physical damage to the core laminations. The damage in Fig 26 appears to be the result of lamination insulation failure, a far greater concern.
In both cases, the actual root cause may be impossible to determine but the likely causes are (1) minor nick caused by workman error or foreign object damage, and (2) core lamination insulation breakdown. The former is inconsequential (although correction is necessary), but the latter calls into question core integrity.
In the case of a shorted iron test and inspection failure (Fig 27), the inspectors noticed the indications, but an ElCid test, probably conducted with an inadequate sensing coil, gave satisfactory values. A new winding was installed but after a few hours of operation, the core iron melted and the winding failed (Fig 28).
General core melting. Occasionally, massive core meltdown occurs with large amounts of molten metal deposited in the endwinding and elsewhere (Fig 29). In these situations, evidence of root cause has probably been destroyed. A likely failure root cause for this class of core is: (1) very thin lamination insulation, (2) through-bolt location, and (3) slight crown of lamination material resulting in high clamping forces at the radial midpoint of the core.
Over-flux damage. In this uncommon failure mode (Figs 30, 31), damage may not be obvious until the stator winding is removed. However, damage can be extensive and repair costs high—for example, the stator core and winding may have to be replaced, along with extensive field and frame cleaning.
The root cause is operation with excessively high field current while the generator is offline. In this particular case, after the severe over-flux incident the unit ran for several months before extensive core melting caused the stator winding to fail. However, the rate of damage of a typical over-flux incident normally would be so great that failure would be expected concurrent with the over-flux incident.
Field RCA
Windings
Field windings may have low to zero resistance to ground from general contamination, localized contamination, broken turns, and/or arcing between coils. Finding the actual ground location is usually easy, ground may not be (Figs 32-34).In Fig 32, the root cause of contamination was defective shaft oil seals coupled with inadequate filter maintenance. Fig 33 shows forging burn attributed to a double field winding ground; old, worn-out insulation was the cause. Cause of winding ground from coil-to-coil short circuit in Fig 34 remains unknown.
Turn shorts can be benign, or lead to hazardous operation. If less than 3% to 4% of the turns in a field are shorted, and the shorts are randomly distributed circumferentially among the field coils, the machine may be operable, assuming acceptable field excitation current.
However, if the shorts are concentrated on the smaller coils, and on one pole, then an unacceptable thermal vector may exist. If the shorts indicate progressive insulation breakdown, the situation may become hazardous.
Open circuits. Windings with open circuits are not common. Typical contributors to root cause include: start/stop operation, cyclic loading, inadequate blocking, incorrect copper hardness, inadequate flexibility in connections, and improper friction planes (Figs 35-37).
Fig 35 illustrates a fractured turn; root cause was cyclic duty combined with braze location, reduced copper area, and stress risers. A cracked top turn is in Fig 36, caused by a non-body-mounted retaining ring. Open circuit in Fig 37 was caused by the fracture of an 18/5 retaining ring.
Load-related mechanical vibration
There are at least a dozen potential root causes of load-related vibration in generators: field copper bonded to slot liners, uneven end-turn blocking, turn shorts, broken turns, cracked field forging, uneven ventilation in slot region or under retaining rings, displaced slot liners or turn insulation, uneven coefficients of friction, wedges fitted incorrectly, overlapping retaining ring insulation, turns bonded to slot liners, cocking/shifting of retaining rings, and shifting of end-turn blocks. Thus, it may be difficult to identify the root cause and appropriate corrective actions.
Forgings
Flow of body current is the root cause of localized hot areas on the field forging. The current comes from excessively unbalanced stator currents or asynchronous operation, the latter resulting from a broad spectrum of operating conditions. These include across-the-line connection at standstill, minor mis-synchronizing errors, and loss of field current while carrying light or heavy loads.
If good plant records are available, root cause of forging burns (Figs 38-40) almost always can be identified. Local wedge burns are shown in the first photo; severe burning of field, wedge, and retaining ring in the second; and melted field and retaining-ring forgings from asynchronous currents in the third photo (probably single phase across-the-line breaker closure).Field forging cracking. Cracks tend to appear on field forgings in two locations: under the retaining-ring shrink fit and at the edges of the pole faces near the body centerline. OEMs understand these types of cracks. They are serious, and vulnerable designs should be checked for cracks as recommended by the manufacturer.
Retaining rings. Cracking of retaining rings can lead to forging failure, making the unit vulnerable to catastrophic failure, injury, and loss of life. You must adhere to OEM recommendations for care and inspection of retaining rings. The predominant issue today relates to stress-corrosion cracking of 18/5 retaining ring material. These rings can fail in a very short time (months or a few years) if exposed to significant moisture. A few years ago, one of these 18/5 rings failed catastrophically only 18 months after both rings on the field were removed and passed full non-destructive examination (NDE) tests (Figs 37, 41). ccj




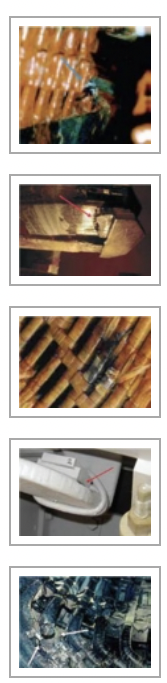