Four ‘knows’ help identify a viable approach for dealing with casing cracks
By Ron Munson, PE, Ron Munson Associates LLC
A bad day for any plant manager is when a generating unit experiences a failure or circumstance that causes an extended outage. One serious, and increasingly common, issue that can force a unit out of service is cracking of a steam- or gas-turbine casing.
OEMs typically do not have casings in stock and lead times for replacements are long. If the casing can be obtained at all, it will be expensive. Repair of a cracked casing generally is a viable option; however, distortion from potential repair welding and metallurgy issues can make repairs challenging.
Casing knowledge is not widespread among turbine owner/operators, so a cracking issue must be approached deliberately. The four “knows” below will provide much of the information you will need to develop a viable solution.
1. Know casing chemistry and pedigree. Depending on machine age and design, the casing can be made from materials ranging from grey cast iron to low-alloy cast steel. Casing age also is important: It determines pedigree. Keep in mind that steel quality has improved over time, especially regarding the types and amounts of “residuals” in the material.
Casing alloy specifications may specify upper and lower limits for about 10 elements, but there are 15 to 20 or so elements that can adversely impact any type of weld repair. An efficient way to determine the exact composition of your casing is to slice off a small piece from a flange and submit it to a commercial laboratory for a “complete” chemical analysis.
Portable alloy analyzers can tell you what the basic alloy composition is, but they cannot identify some of the deleterious elements that can negatively affect welding-even at ppm concentrations. These analyzers are not useful for characterizing casings for repairability.
2. Know the root cause of the failure, the specific failure mechanism. Here are some of the questions you should ask yourself:
- Is the damage localized-such as in a highly stressed area?
- Is the damage from rotor interaction-such as rubbing, oxidation, etc?
- Is casing deterioration “global,” such that repair at one location will be followed shortly by failures at other locations?
- Is your casing “deceased,” or just “wounded?”
3. Know specifically what to expect from the repair. Will the repair be “permanent” and last the life of the machine, or “temporary,” until you can obtain a new casing? Expectation of the repair life is important-influencing both the economics of power production and personnel safety. Regarding the latter, consider that a repair could change the casing failure mode from progressive-that is, crack elongation and more leakage-to catastrophic-the sudden and damaging release of steam or combustion gases under pressure.
4. Know your repair vendor. You’re almost sure to identify many companies wanting to repair your casing. Be sure to choose the right one. Expect the high bidder to be the OEM, but don’t toss that quote in the circular file at your first opportunity. The turbine supplier probably best understands your casing design and likely has repair experience on a sister unit or one similar to yours. Don’t be surprised if the OEM would prefer to sell you a new casing, assuming one is available; it would have a lower risk profile and higher profit margin than a repair.
Non-OEM repair vendors probably will have the most competitive bids, but one or more might not have the experience to perform the specific repair you require. Thorough due diligence is necessary. The successful bidder should be a company specializing in casing repairs and one having a long and successful performance record. It’s also very important to have the most highly skilled craftsmen assigned to your project; check resumes carefully.
Here’s a checklist to help guide you through a casing repair:
- Photograph the damage.
- Examine nondestructively the balance of the casing. If damage is widespread your choices are (1) live with it, or (2) replace the casing.
- Define the probable failure mechanism and cause. Consider changes to O&M procedures to minimize the recurrence of cracking in the repaired casing.
- Remove samples; a small sliver from an area of low stress is sufficient. Verify composition of the casing material-including carbon level and residuals.
- Review casing history; note the location of previous repairs, if any. Also identify the type of repairs made and the vendor(s) that did them.
- Contact vendors both interested in doing your work and qualified to make the repairs required. Prepare a work scope, making sure to state the expected life you want from the casing. In addition, define post-repair inspection and acceptance criteria for cracks and distortion; clarify the warranty.
- Notify your insurance carrier of your intent to repair the casing. Future insurance coverage may depend on its knowledge that the repair was made.
- Conduct the repair. Have a qualified staff person or a third-party consultant monitor the repair. Your representative must be empowered to halt work if repair practices/procedures are not acceptable.
- Re-inspect the casing for defects both associated with the repair or new defects that came to light during the repair process.
- Return to service. CCJ
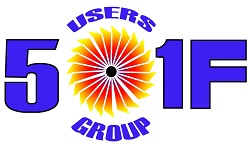
The 501F Users Group was the last of the US-based independent gas-turbine organizations serving owner/operators to conduct in-person conferences in 2020.
That meeting began Monday, February 10, with the group’s annual safety roundtable, followed by live presentations from about 30 third-party suppliers of products and services for the 501F. A vendor fair closed out the first day’s program.
Presentations by users; roundtable discussion forums on the rotor, inlet and exhaust sections, compressor, combustor, hot-gas, and auxiliaries; and special closed sessions for the five OEMs serving this user community (Doosan, GE, Mitsubishi Power, PSM, and Siemens Energy) were sprinkled throughout the three remaining days of the conference.
Featured Solutions Provider

Summaries of the presentations, beginning below, testify to the value of the information disseminated. The complete PowerPoints can be reviewed by registered 501F owner/operators on the user group’s website at https://forum.501fusers.org/login. Non-members who meet the organization’s requirements can gain membership status by completing the online registration.
- 501FUG: Presentations by Owner/Operators
- 501FUG: Special Closed Sessions – Doosan
- 501FUG: Special Closed Sessions – GE
- 501FUG: Special Closed Sessions – Mitsubishi Power Americas
- 501FUG: Special Closed Sessions – PSM
- 501FUG: Special Closed Sessions – Siemens Energy
- 501FUG: Vendorama
- Nord-Lock Group solution mitigates 4-way joint leakage
- PSM Shop Tour for 501F Users