Identify, address potential weaknesses to mitigate cycling impacts
By Jonathan D Aurand, HRST Inc
Most combined-cycle plants were designed for base-load service. But must-take generation from renewable energy projects is forcing many gas-turbine assets to cycle and/or to follow load for a large portion of their fired hours. More cycles and faster ramps are known to adversely affect the health of your heat-recovery steam generator (HRSG). An engineering assessment is recommended to identify at-risk components and to suggest equipment mods and changes to O&M and inspection procedures to mitigate cycling impacts.
There are six primary areas to evaluate when conducting an HRSG cycling assessment. They are:
1. Desuperheater overspray. Most HRSGs were designed to use little or no spray water to control final steam temperature at full load. During startup and when operating at part load, conditions often require considerable spray water, reducing the temperature of the mixture to near saturation—particularly for the popular GE 7FA gas turbine. Desuperheater performance depends on the arrangement of heat-transfer surface, process conditions, and gas-turbine load.
Each desuperheater system is unique and must be evaluated based on the type of spray nozzle, lengths of straight pipe before and after the attemperator, and the ratio of spray to steam flows. If overspray occurs and remains unchecked, damage to interconnecting piping and downstream tube bundles will occur (Figs 1-3).
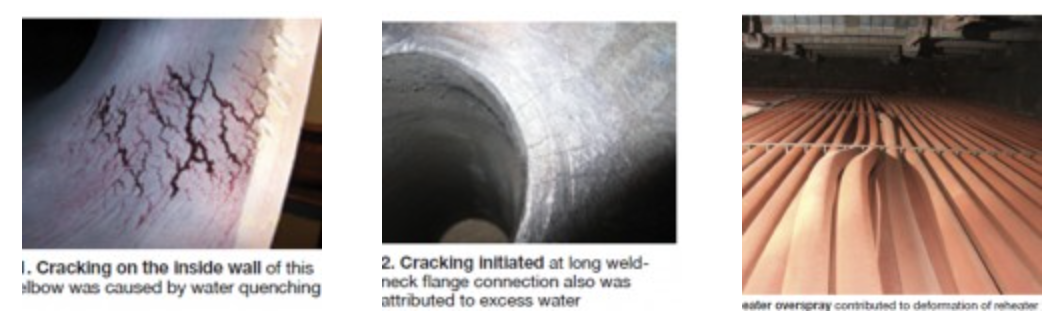
One way to reduce the demands placed on desuperheaters, especially those having to deal with the 1200F isotherm characteristic of 7FAs at part load, is to consider installation of an air attemperation system (Protect HRSGs against damage at low loads). It uses fresh air to reduce the temperature of GT exhaust gas as it enters the HRSG (Fig 4).
2. Desuperheater control during startup can be problematic, particularly if overspray also is occurring. Some arrangements require repeated oscillation of flow to maintain a given final steam temperature set-point. This phenomenon, known as desuperheater hunting, can lead to thermal fatigue of the spray nozzle assembly in probe-style attemperators (Fig 5).
Some arrangements have poor placement of thermocouples for control purposes; others have improperly sized hardware for cyclic and part-load operation. Keep in mind that if cycling damage—such as plugging or breaking—occurs to desuperheater components, control of steam temperature borders on the impossible and subsequent damage is likely.
3. Drum-temperature ramp rates. Thick components joined together often heat and cool at different rates. The difference in temperature between the components creates a thermal gradient at the joint which imposes a thermal stress. In most HRSGs, the thickest joints are in the HP drum—such as the downcomer-to-shell connections (Fig 6). Evaporator risers and steam outlets also can be at-risk for thermal fatigue.
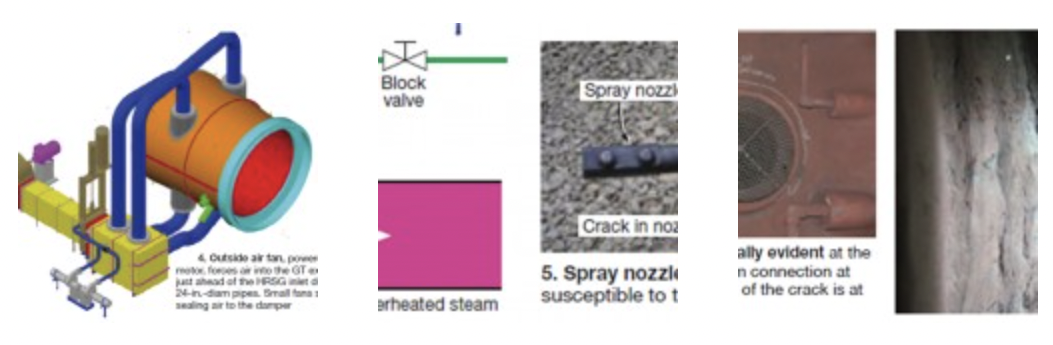
The thermal gradient across a given joint depends on the thicknesses of the components, connection type (refer back to p 46), weld details, and process conditions. Most of these parameters are difficult to change (specifically, weld details and process conditions), so operation must be addressed to maintain safe levels of thermal stress.
While most OEMs provide, and plants follow, startup curves based on pressure, the rate-of-change in saturation temperature really is the driving factor for thermal fatigue in steam-drum nozzle welds.
4. Economizer risks. Cycling economizers are a fatigue risk from thermal shock, which occurs when feedwater flow is initiated in a hot economizer. This can occur offline when drums are topped-off, as well as when feedwater begins to flow during a warm or hot start. In a panelized economizer, inlet tubes are put in tension as they try to contract when “cool” water enters the unit; subsequent passes in the same panel are still warm and restrain the headers (Fig 7).
Return-bend economizers may experience stress at the upper return bends as the inlet pass lifts off its supports. Upper return bends also may flatten when load is redistributed after the event. In addition, lower flow rates during startup and low-load operation mean lower economizer velocities, which may not be sufficient to overcome buoyant forces in down-flow passes and flow may stagnate or vapor lock in some down-flow tubes. This results in (1) thermal stress when flow increases and water begins moving through the tubes again, and (2) a decrease in thermal performance.
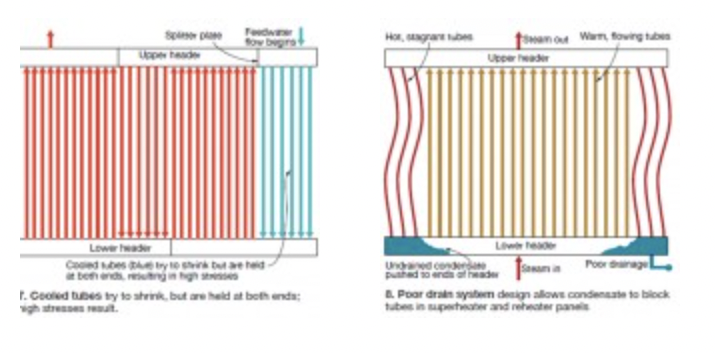
5. Superheater drainage. During the gas-turbine purge on a hot or warm start, superheaters become condensers as cooler air from the turbine is pushed across that heat-transfer surface. Steam inside the superheater panel cools until it reaches the saturation temperature and begins condensing.
Condensate collects in lower headers, interconnecting piping, and, if not drained properly, in the tubes themselves. Once the unit begins firing, undrained condensate may block tubes, thereby creating local cool areas and preventing steam flow. Result is higher average tube temperatures in the blocked tubes relatively to neighboring tubes. Bowed tubes at the end of the headers (near sidewalls and center gas baffles) usually are caused by poor condensate management (Fig 8).
The drain system for each superheater and reheater panel should be evaluated for condensate production and drain capacity used. While a hot start produces the most condensate, a warm start may use a higher percentage of the drain capacity because less pressure is available to blow out the condensate.
Additionally, elevated blowdown tanks and ganged drain manifolds (HP superheater and reheater discharging to one manifold) present additional challenges which should be analyzed thoroughly. Drain connection points to headers and piping also are critical, to prevent condensate from collecting in the downstream ends of superheater headers.
6. Control room philosophy. Observing a couple of starts from the control room provides solutions providers valuable insights. HRSG experts have the opportunity to follow operations in action and question operational decisions as they are made.
Example: Some board operators mistakenly believe they are protecting their equipment by entering a final-steam-temperature set point that is lower than design. This actually increases the amount of water being sprayed by the interstage desuperheaters, thereby increasing fatigue risk.
Other examples can include sitting at a damaging low load for extended periods before turn-over to AGC (or dispatched load). Finally, there are tradeoffs among connected pieces of equipment. Maintaining steam-turbine stresses at acceptable levels is critical to reliable operation, but there is a tradeoff with HRSG component stresses. Control-room observations can illuminate such tradeoffs.
End notes. Performing a cycling evaluation of your HRSGs is prudent, as such an assessment helps to identify risk areas specific to your plant’s arrangement and operation. These “watch” areas can be addressed through focused nondestructive examination, operational changes, and/or planned future capital improvements. Cycling a combined-cycle plant designed for base-load service without being fully aware of its idiosyncrasies can lead to forced outages and equipment damage that might have been avoided. CCJ