That’s not your father’s gage glass
Drum-level gage glasses have been reliably protecting deck-plates personnel and the public at large against boiler failures since well before the industry’s oldest operator was born. But while today’s direct- and indirect-reading drum-level instruments may look like those installed on your ageing heat-recovery steam generator (HRSG), improvements have been ongoing.
Jim Kolbus, product manager, Clark-Reliance, Strongsville, Ohio (Sidebar), speaking at the 20th annual meeting of the HRSG User’s Group, held earlier this year in Houston, brought owner/operators up to date on this vital safety equipment. He began by reviewing the different types of gage glasses.
The only direct-reading drum-level gage is a glass gage, Kolbus said, and there are four types of these, as shown in Fig 1: tubular, prismatic (also known as reflex), flat glass (transparent), and bicolor (ported). Note that the last operates on the principle of light refraction: Light refracts through water differently (green) than it does through steam (red). The gage must be equipped with an illuminator to comply with Section I of the ASME Boiler & Pressure Vessel Code (Code).
The instrument expert stressed that the tubular glass option was not recommended as a permanent installation because it offers the least protection for plant personnel. It’s fine for boil-out and chemical cleaning purposes, he said. Prismatic gages typically do not require any illumination accessories, Kolbus continued. They are easily viewed in areas with sufficient ambient lighting.
Flat-glass gages should have illumination accessories. The instruments are designed with inner mica shields, which reduce an observer’s ability to read the level accurately when installed without back-lighting. Bicolor gages generally are the only option above 2000 psig; however, they are used as well in low-pressure applications because it’s easy to see the water level.
Indirect-reading water-level indication systems may be any combination of the following types: (1) differential pressure, (2) guided-wave radar, (3) conductivity probe-type systems with a control unit and remote display, and (4) magnetic level-indication systems designed with a float in a stainless steel chamber. However, the use of magnetic level-indication systems is limited by the Code to 900 psig.
The first two indirect-reading gages must be installed and programmed in accordance with the manufacturers’ instructions to prevent indication errors. Also, Kolbus recommended that users take precautions to prevent adverse effects of freezing conditions on level-sensing components.
Code requirements
The ASME Code mandates that one direct-reading gage remain in service at all times on applications up to 400 psig. The logic is that boilers in this pressure range generally are specified for hospitals, universities, district heating systems, etc, and are close to large numbers of people. Having the most obvious and accurate water-level instrument in continuous service contributes to a high level of safety.
For boilers operating at pressures in excess of 400 psig there are two options: Two direct-reading gages or two indirect indicators on continuous display for the operator and one direct-reading gage. Last may be isolated but must be maintained in serviceable condition.
Fig 2 is important because it illustrates Code rules for locating a water gage glass with respect to the piping between the drum and the water column. Goal of the arrangement is to assure installation of a gage with unimpaired visibility that fills to the top of the required visible range and can be drained completely.
Some attendees seemed surprised to learn that the gage-cock connections found on water columns of older installations to provide positive verification of water level, if necessary, are no longer required by ASME Section I—and haven’t been for 20 years.
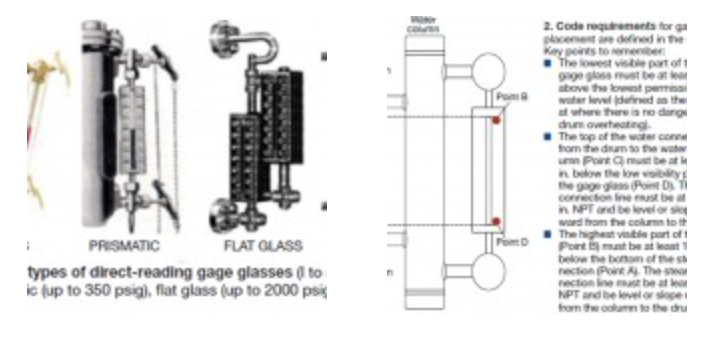
That meeting began Monday, February 10, with the group’s annual safety roundtable, followed by live presentations from about 30 third-party suppliers of products and services for the 501F. A vendor fair closed out the first day’s program.
Presentations by users; roundtable discussion forums on the rotor, inlet and exhaust sections, compressor, combustor, hot-gas, and auxiliaries; and special closed sessions for the five OEMs serving this user community (Doosan, GE, Mitsubishi Power, PSM, and Siemens Energy) were sprinkled throughout the three remaining days of the conference.
Clark-Reliance in your plant
Clark-Reliance, founded in 1884 as the Reliance Gauge Column Co, is the industry’s leading supplier of gage glasses and other mostly “invisible” plant equipment—such as transmitters, level switches, liquid separators, sight windows, flow indicators, steam traps, small valves, hydraulic-oil filters, etc. The company’s brands that may be familiar to you include Jerguson, Magne-Sonics, Jacoby-Tarbox, Clark Steam Specialties, National Filtration Systems, Anderson Separator, Hycoa, and Oil Filtration Systems.
One control must be set to activate ahead of the other one. A manual reset function may be applied to the lower of the two controls, this to assure that the operator confirms there’s a safe water level in the gage before activating the reset. Additionally, the cutout circuit may incorporate a time delay not to exceed 90 seconds, thereby allowing the operator a little more time to regain a safe water level in the boiler without initiating a shutdown.
Piping recommendations. Best practices regarding level-instrument piping include the following:
- All piping from the drum to water-level instruments must be insulated to (1) protect personnel against burns, (2) assure accuracy of level measurement, (3) minimize condensate formation. Keep in mind that condensate contributes to erosion of the mica shield in the gage glass: The less condensate, the less wear.
- Any piping slope should be downhill on the steam line and uphill on the water line from the drum (Fig 2).
- Regarding piping runs from the drum to level instruments, less is more. The shorter the run the less temperature loss; plus, the likelihood of more accurate level indication.
Common Code violations, concerns. Kolbus noted that he finds too many of the violations listed below in plants visited and stressed that users review Code requirements to assure the highest levels of plant and personnel safety. Violations and concerns include these:
- Isolated, inoperable water gages.
- Missing water gage glasses.
- Missing illumination from ported-type gages.
- Inadequate display of remote level indicators in the control room combined with isolated gages.
- Contaminated water gage glasses that prevent viewing the actual level (meniscus line). Confusion can result when a contaminated water gage causes a stain at the water-level line—especially on neglected tubular glass applications. On higher-pressure gage glasses, a white color on the inside of the glass may occur when the mica shield has deteriorated. In both cases, immediate maintenance/replacement are required.
- Multiple-section flat glasses without the Code-required overlap.
- Poor maintenance practices.
Inspection results compiled by the National Board of Boiler & Pressure Vessel Inspectors in its Annual Violation Tracking Report reveal boiler controls (including gage glasses) leading in “number of violations.” In 2010, the last year for which complete data were available when Kolbus prepared his presentation, boiler controls accounted for 29% (21,158) of the 71,816 violations found during 688,963 inspections.
His conclusion was that the stats would improve significantly if operators had access to proper training and support. Since the beginning of this year, inspectors have been detailing the causes for boiler-controls violations. This will permit extraction from the data of those violations attributed to water level gages, cutouts, etc.
Case histories. Fig 3 illustrates both the good and the bad in one gage glass installation. The good: Chains on water gage isolation valves are properly installed as is the drain piping on the water gage valves and water column. The bad: Drain piping on the lower right side of the drum should not have a trap. The low point must have a valve. This Code violation was corrected by the plant owner.
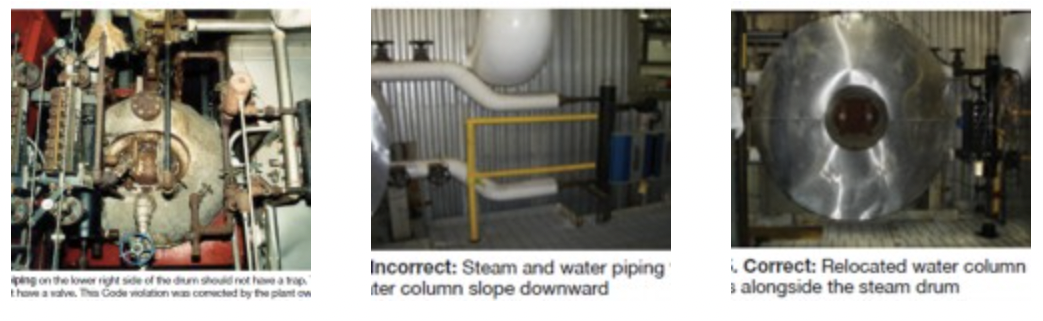
Fig 4 illustrates a water column installed incorrectly, with steam and water inlet piping sloping downward. This dangerous installation never was placed in operation. The low-water alarm and low-water cutout probes would have indicated trapped water in the piping and the gage glass would have responded similarly. Corrective action is shown in Fig 5. Water column was relocated near the drum and the gage glass and conductivity probes in the water column are in the correct position relative to the drum. CCJ