Lessons relearned
by David Addison, Thermal Chemistry Ltd
Although the mechanism of flow-accelerated corrosion in gas-turbine-based combined-cycle and cogeneration plants generally has been understood for decades, FAC remains one of the major safety issues for plant management and personnel. It can occur across the feedwater system, from the condensate pump to the economizers and LP evaporator sections of heat-recovery steam generators. It is equally dangerous in both single- and two-phase flow regions.
FAC is the leading cause of availability loss in HRSGs and is the major damage mechanism in air-cooled condensers, which have been specified for many new combined cycles in the arid West.
In virtually all of these systems, cycle chemistry influences and, in some cases, controls FAC. Clearly, FAC should not be considered just a failure mechanism. It also is a major cause of cycle corrosion, contributing to higher levels of transported corrosion products. These corrosion products, in turn, act as the centers for many other failure and damage mechanisms.
The bottom line: Recognition, control, and alleviation of FAC should be one of the most important management-supported aspects of operating combined-cycle and cogeneration plants powered by gas turbines.
Powerplant owner/operators had the opportunity to participate last summer in the first international conference on FAC in fossil and combined-cycle plants, organized by Dr Barry Dooley, Kevin Shields, and Steve Shulder of Structural Integrity Associates Inc and a blue-ribbon panel of advisors (sidebar). It was conducted to provide users broad and expert experience in all aspects of FAC.
More than 175 participants represented about 100 organizations from 21 countries—including utilities, research organizations, universities, manufacturers, suppliers, and consultants. The high level of expertise that permeated the group was conducive to lively interaction, robust debate, and productive networking discussions. The technical program consisted of 40 papers presented by researchers, plant operators, and service organizations.
The goal of the meeting was to review, document, and transfer technology on the most recent developments in understanding (1) the mechanisms and root causes of FAC, (2) the management tools and approaches to mitigate its effects, (3) predictive processes, (4) cycle chemistry, (5) nondestructive examination (NDE) techniques and assessment technologies, and (5) the application of permanent solutions. By design, the conference was linked with FAC2010, a meeting focusing on FAC in nuclear power stations organized and conducted by the French utility EdF.
The latter was held in Lyon in May, a month before its fossil/combined-cycle counterpart in Washington, DC. Attendees participating in both events helped to connect the knowledge from the fossil and nuclear areas. The second international conference on FAC in fossil and combined-cycle plants is planned by Dooley and his Structural Integrity colleagues for early spring 2013, perhaps a month or two before the nuclear FAC meeting scheduled again for May in France. Write bdooley@structint.com to be placed on the mailing list for meeting updates as they become available.
FAC management
Issues related to flow-accelerated corrosion are in evidence globally and affect nuclear, conventional fossil-fired plants, and combined-cycle generating facilities. Think of FAC as a two-stage problem: initial component failure and the consequential damage from the generation, transport, and deposition of the resulting corrosion products in the higher-pressure stages of the Rankine cycle.
The physical location of FAC makes the affected pressure part susceptible to failure (Figs 1, 2). This Is caused by internal wall thinning of low-chromium-content carbon steel, which occurs because the magnetite layer dissolves when exposed to the temperature, velocity, chemical, and geometric factors associated with FAC.
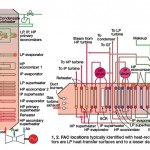
Failure of pressure parts results in water/steam leaks, personnel risks, damage to adjacent plant equipment, and the financial losses associated with a plant shutdown. Secondary to the actual FAC related failures is the longer-term issue of corrosion-product transport, which often is overlooked by power producers. Iron removed primarily by dissolution during the FAC process is transported into the higher-pressure and higher-temperature sections of the HRSG—typically from the preheater to the HP economizer and HP evaporator.
The higher temperatures and pressures of the HP sections cause the iron to precipitate and deposit as a porousoxide (magnetite) on heat-transfer surfaces. The oxide layer enables the concentration of corrodents and contaminants—such as chloride—which can enter the steam/water cycle via condenser tube leaks, demineralizer upsets, etc. If corrodents enter the cycle, the porous oxide layer allows under-deposit corrosion mechanisms to proceed rapidly. Pressure-part failures are a likely result.
Management of FAC risks is a life-of-plant issue and not a one-time problem that can be fixed and then forgotten about. As conference attendees learned, the top utilities worldwide typically rely on several key actions that when conducted together result in effective FAC management.
They include the following:
- Prepare a best-practices project/HRSG technical specification to mitigate FAC risk at the design stage.
- Implement a best practices program for cycle chemistry at plants under construction and in operation. It should specify such things as (1) avoiding use of reducing agents/oxygen scavengers for all-ferrous plants,(2) correct pH levels for operations and lay-up, (3) appropriate instrumentation, etc.
- Have in place a documented, methodical, and robust inspection program to detect early signs of FAC and to allow remedial action before failures occur. This should include repeatable and thorough corrosion-product sampling.
- All aspects of FAC monitoring and control should be documented, signed-off by senior management, and managed by accountable, technically competent staff personnel with sufficient budgetary support.
The science of FAC
Structural Integrity’s Dooley, the first speaker, set the tone for the conference. He opened the meeting with a clear and authoritative state-of-the-current-science address which summarized what is known about FAC and the issues it still presents to conventional and combined-cycle powerplant owners and operators.
One of Dooley’s key points, summarized in the previous section, was that FAC is a two-stage problem: material loss leads to pressure-part failures and the corrosion products produced migrate to and deposit in HP sections of the steam/water cycle. LP sections of HRSGs, and to a lesser degree the IP stages, are susceptible to FAC damage because of their relatively low operating temperatures and conventional carbon-steel construction (Figs 3-5).
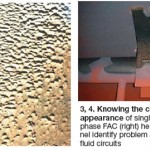
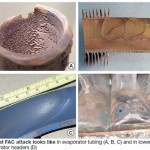
While industry knowledge regarding FAC has grown and some generating companies are effectively minimizing its adverse impacts, Dooley said, others continue to repeat past mistakes. Proof: More than 70% of the fossil-fired plants worldwide are still reporting failures caused by FAC.
He urged attendees to meet the challenges of FAC head on by conducting a root cause analysis and then making appropriate changes to water treatment programs and O&M procedures at afflicted plants. In his concluding remarks, Dooley suggested that a global FAC working group be established to “extend the science” and bring together related work in the nuclear, conventional fossil, and combined-cycle sectors of the industry.
Prof Derek Lister’s (Univ of New Brunswick) “Reflections on FAC Mechanisms” provided a wealth of knowledge and experience on the chemical and physical mechanisms of FAC, based on research conducted at the university and by the Japan Atomic Energy Agency. Relevant parallels to thermal plants were covered. Two key takeaways from Lister’s work are the significant and rapid inhibiting effects that the chromium content of pressure-part materials and slightly elevated dissolved-oxygen levels in condensate/feedwater have on FAC attack.
Stan Walker’s (EPRI) “The NDE Options for FAC” made the following key points regarding the value of nondestructive examination (NDE) for identifying and quantifying FAC damage:
- Detects FAC before a failure occurs.
- Helps assess remaining component and plant life.n Assists with plant risk-based assessments.
- Helps determine other potential FAC locations.
Next, Walker described the following technologies commercially available to inspect for FAC:
Ultrasonic thickness (UT) is the most common NDE technique for pipes of 2 in. diam and larger. Plant must be shut down and insulation removed to conduct UT; plus, inspection grid lines should be painted on the pipe parallel and perpendicular to flow. Repeatability from inspection to inspection is important to assure accurate trending of wall loss.
Radiography often is the choice for inspecting pipes smaller than 2 in., although sometimes it is used for pipe up to 6 in. diam. Advantages over UT: Can be used through insulation and close to welds; scaffolding typically is not needed. However, personnel must clear the area before radiographs are taken and this can be inconvenient during outages. Digital radiography is increasingly being used for FAC assessments.
Pulsed eddy current is an excellent screening tool for piping because it can be used through insulation and while the unit is in service. However, it may underestimate wall loses and usually is not used to determine FAC rates.
Ultrasonic long-range guided waves is another rapid and inexpensive screening technology. But it requires insulation removal.
Overall, Walker concluded, there is no single “best” NDE technique for detecting and assessing FAC damage. Some techniques are for long-range screening to verify that failure is not imminent; others, geared for sensitivity, are used to determine the exact size, location, and nature of damage. The optimal option is determined after considering available time and funding, access restrictions, technician skills, etc. Most important for accurate results are the use of proficient technicians and a thorough understanding of the of the limitations of the alternative inspection techniques.
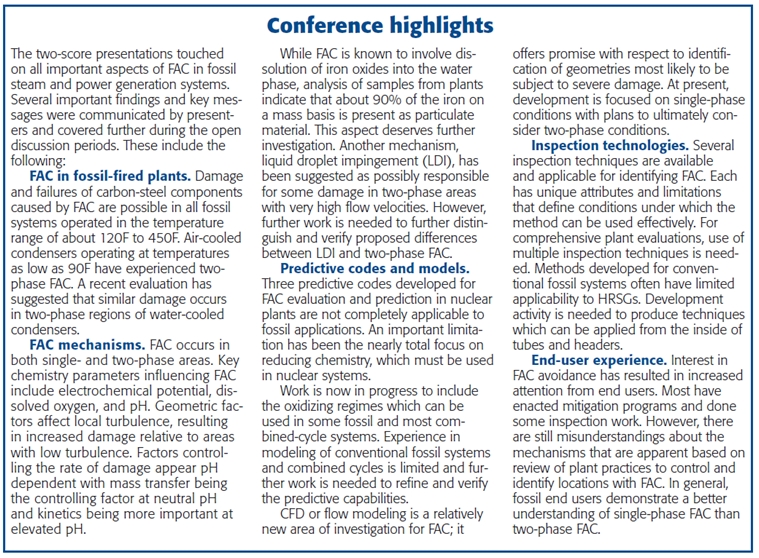
Fossil plant experience
Four sessions at the Arlington (Va) meeting focused on FAC experiences and programs at conventional fossil-fired steam plants and combined cycles. One of the first speakers was Des McInnes, Tarong Power Station, Queensland, Australia, who summarized two decades of FAC experience at the conventional coal-fired plant.
Highlights included the following: (1) significant FAC problems detected early in life, (2) LP heater replacements to remove copper alloys, (3) cycle chemistry changes to oxygenated treatment, (4) ongoing corrosion-product monitoring, and (5) plant inspections. McInnes suggested inspecting components whenever accessible during maintenance activities.
Gary Rogles presented the details of AmerenUE’s FAC inspection program from 1996 onward. Initially, the program was limited in scope, but in 2006 it was updated, expanded, and formalized because of increased FAC awareness. Units were ranked in order of FAC risk and re-inspected in priority order.
Rogles discussed the successful use of pulsed eddy current inspections of large-bore piping while plants were operating, and UT on smaller-bore pipes with the units offline, to assess loss of wall thickness. He also mentioned the use of handheld x-ray fluorescence (XRF) analysis to determine the chromium content of pipe materials.
Paul Waldrop described the development and implementation of PacifiCorp’s high-energy-piping (HEP) management and inspection program, including FAC management, across the utility’s fleet of conventional steam and combined-cycle units. The program, backed by senior management, provides clear directions to responsible individuals.Further, development of a central database of documents and inspection results, and use of standard NDE inspection terms, assures comparable results across all sites and contractors.
Waldrop said the program helps plant managers understand and identify HEP and FAC issues and to secure the necessary funding to correct deficiencies—thereby improving safety and reliability, and reducing plant risk profiles. Last lowers insurance premiums.
The AmerenUE program identified many thinned components, allowing their replacement before failures occurred. Key problem areas were feedwater-heater drains and dump piping, and reheater and superheater spray-valve stations.
“AEP’s Approach to FAC,” presented by Jeff Anderson, covered the utility’s experiences with FAC management issues across its coal and gas fleets. The company’s FAC program is managed at the corporate level by a three-person team: AEP’s head chemist, a program engineer, and a piping engineer.
The team identifies specific locations that it wants inspected while empowering plant staffs to go beyond those based on risk assessments. AEP has inspected more than 3500 locations on 63 units in the last five years, 30% of which had indications of FAC. Lessons learned include the following:
- Inspect at least two pipe diameters downstream of any fitting.
- “Identical” systems do not often have identical FAC.
- Seldom-used drain and bypass lines can have FAC.
- FAC can occur in straight pipe away from fittings.
- FAC may not occur at a constant rate.
- Younger plants may have more FAC than older plants.
- FAC temperature range is greater than most people might expect.
- Spot UT checks do not equal an inspection.
Anderson stressed the importance of a reporting system to reach inspection goals and to provide clear, effective communication with senior management. He added that the empowerment of plant staff to choose inspection locations within a structure framework provides dividends of improved site understanding of FAC and allows for identification of plant-specific issues.
Annual training is conducted to maintain FAC program awareness. Anderson recommended that this activity include discussion of “near miss” incidents to improve learning and understanding; also, that the issues identified by near misses be incorporated into the FAC management plan.
Constellation Energy’s Albert Olszewski described a program to gather baseline FAC data on a combined-cycle plant placed in layup in 2003 (85% complete); construction was restarted in 2008 after a change in ownership. UT thickness checks and XRF composition analysis provided a baseline for future FAC inspections.
System chemistry was optimized during the layup period as well, to minimize FAC risk. Originally, an AVT(R) water treatment program was planned. But that was switched to AVT(O) and the oxygen scavenger eliminated. The feedwater pH setpoint was raised up to pH 10-10.2 using ammonia and iron testing was conducted.
Bud McArthur Jr and Tom Gilchrist discussed the history of FAC at Tri-State G&T Assn Inc over the last two decades. The utility’s first FAC failure occurred in an economizer header stub at its coal-fired Craig Generating Station 20 years ago. The key conclusion from that experience was that while FAC was a proactive activity, unexpected failures made it necessary to initiate an optimized reactive approach involving materials upgrades (higher chromium content) and cycle chemistry improvements.
Perhaps the key take-away from all the presentations on utility FAC programs was the importance of effective data management and reporting to the executive corps. The best systems allow for automatic report generation. Specifically, databases should retain plant-specific data and inspection results in an easily searchable format that permits the trending and tracking of information.
The consensus view was that management reports should be concise, identify work undertaken, and provide a risk-based analysis with follow-up actions clearly identified. Color coding to identify the various levels of risk was considered particularly beneficial. Keep in mind that without plant management sign-off, remedial-action budgets can not be developed and approved and plant FAC risks will remain.
Air-cooled condensers
Increased reliance on air-cooled condensers (ACCs) to conserve water raises the profile of FAC at many new plants. So much so, that an entire session was devoted to FAC in ACCs. Recall that FAC-susceptible carbon steel is the primary material of construction for ACCs, and the fluid conditions—two-phase flow and the low pH of the liquid phase—are conducive to metal wastage.
The very large heat-transfer surface area of an ACC means significant quantities of iron can be removed from the condenser tubes and headers and transported to, and deposited in, the boiler absent an effective cycle chemistry program. Deposition in conventional boilers and heat-recovery steam generators increases the risk of under-deposit corrosion and subsequent failure of pressure parts.
“Capital Power ACC FAC Study,” presented by Bill Stroman, shared the independent power producer’s FAC experiences at several ACC-equipped plants in Canada. These facilities were commissioned and operated with a morpholine/hydrazine AVT(R) cycle chemistry program until they were sold in 2006. ACC inspections could not be confirmed and water-chemistry records were poor.
After the asset sale, Capital Power switched the plants to an AVT(O) program relying on ammonia to maintain a target pH of 9.2 to 9.3—this to optimize condensate polisher operation. A cycle-chemistry monitoring program also was implemented. In 2008-2009, rigorous inspections of the ACCs were conducted and significant two-phase FAC attack was identified.
Stroman then outlined the actions taken since 2009 to address the FAC observed. The primary initiative was a change from the ammonia-only feedwater treatment program to a blend of about 20% ammonia and 4% monoethanolamine (MEA).
The reason: MEA’s different volatility profile than ammonia allows it to increase the pH of the liquid phase of the two-phase turbine exhaust flow and provide additional protection against FAC. Early results have been encouraging and use of the blend has been extended to other plants. Assessment of the blend is ongoing.
Presentations on FAC in ACCs also were made by Li Zhigang from China’s Thermal Power Research Institute and Gary Joy from Australia’s CS Energy. Joy discussed the issues associated with significant two-phase FAC in the ACC for the 750-MW Kogan Creek supercritical coal-fired plant.
Kogan Creek minimized the amount of iron being removed from its ACC by increasing feedwater pH to more than 9.8. This was possible because the plant was commissioned with a condensate polisher capable of ammonia-cycle operation. The benefit of the ammonia cycle is its extended regeneration interval compared to polishers capable of hydrogen-cycle operation only.
Joy strongly recommended the use of condensate filters for all ACC-equipped plants to prevent transport of iron released by FAC into the boiler. The optimal filter, he said, is a pleated design capable of being backwashed and rated 5 microns absolute. When specifying an ACC for a new project, several attendees suggested that consideration be given to opting for carbon steel containing sufficient chromium to resist FAC attack.
HRSG experience
The session of particular interest to attendees involved in the planning and design of new combined-cycle facilities featured presentations by engineers who described their efforts at “designing-out” FAC from heat-recovery steam generators. Others on the program discussed ways to mitigate FAC issues in operating power generation facilities.
Amy Sieben, PE, HRST Inc, Eden Prairie, Minn, profiled five FAC-afflicted HRSGs that she and her colleagues had investigated. Most problems were severe and failure of pressure parts occurred in some cases only three or four years after commissioning (Fig 6, 7).
All of these were using oxygen scavengers, contrary to advice by the industry’s leading water chemists. Sieben discussed some of the repairs made to correct deficiencies—including the replacement of nozzles and headers with P11 and P22 (Figs 8, 9). Recall that these materials contain 1% and 2% chromium, respectively, which resists FAC attack. The chromium-rich oxide layer that forms on these materials in boiler service has a very low solubility compared to magnetite in the FAC temperature range.
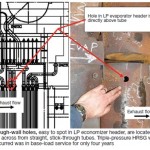
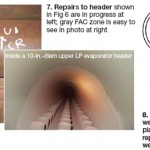
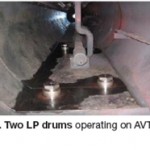
Other repairs included header replacements to decrease fluid velocities and the use of flow orifices to decrease fluid velocities and flow orifices to balance evaporator flows after design analyses revealed that the orifices had not been installed as planned during construction.
Paul Honcoop, NEM bv, Netherlands, suggested that better collaboration between HRSG manufacturers and owner/operators is needed to avoid repeating design practices conducive to FAC and other issues. The statement raised some eyebrows in the room but should not have.Power generators typically have opted for a low-first-cost model that relies most often on an EPC (engineer/procure/construct) contractor to interface with vendors and build and commission a plant to the owner’s specification. If the owner, or its engineer, does not have access to current operating experience, past omissions and errors in judgment can be repeated in the current specification.
Further, business practices involving layers of contractors and warranties that limit the ability to access and inspect the HRSG during the early operation/warranty period, and to interface directly with OEM, are not conducive to expeditious problem identification and resolution.What all this means is that meetings such as the International Conference on FAC provide an important service to the industry by bringing together the OEMs and owner/operators in a collaborative open forum to discuss problems, where they exist, and how to prevent them from recurring.
Honcoop described the constraints HRSG designers have regarding FAC mitigation. Temperatures can’t be changed, he said, and there’s only so much that can be done to limit the effects of turbulence and fluid velocities given today’s operating regimes (daily starts, fast ramps, etc). That essentially leaves materials of construction and cycle chemistry as the only practical ways to minimize FAC.
NEM provides cycle chemistry guidelines specific to the needs of each plant it supplies an HRSG for and that document is incorporated into the O&M manual. The company does not recommend the use of oxygen scavengers, in line with current EPRI guidelines.
Structural Integrity’s Dooley returned to the podium to present “Flow-Accelerated Corrosion in HRSGs,” a paper he developed with Bob Anderson of Florida-based Competitive Power Resources, which summarized FAC assessments the pair made on 19 boilers worldwide. These assessments provide a clear picture of exactly where the weaknesses are in addressing FAC.
Dooley pointed out that the assessments prove FAC and under-deposit corrosion are global generic HRSG issues. He made the following recommendations for the control of FAC in heat-recovery steam generators:
- Specify AVT(O) to control single-phase FAC in the feed system. The use of oxidizing environments to control single-phase FAC is well established and understood in the industry (Fig 10).
- Elevate pH to control two-phase FAC in evaporator tube bundles. The recommended level is 9.8 or higher. Single-phase FAC must be controlled first, with two-phase FAC held in check by addition of sodium hydroxide or tri-sodium phosphate to provide solid alkalization to the evaporators.
However, in HRSGs where the LP evaporator is used to supply attemperation water or feedwater to the IP and HP circuits, solid alkalis are not an option for increasing pH.
- Robust and reliable monitoring of total iron is required to ensure iron levels of less than 2 ppb in the feedwater and less than 5 ppb in the evaporators.
- A formal FAC management plan must be developed and implemented.Get the important details of Dooley’s presentation at www.ccj-online.com by clicking “Archives” on the tool bar near the top of the home page, clicking 1Q/2009 on the archives page, and clicking “HRSG assessments identify trends. . .” on the cover of the issue.
Joe Schroeder, Nooter/Eriksen Inc, Fenton, Mo, presented on how OEMs design HRSGs to minimize FAC issues over the lives of the units provided they are operated correctly. He began by saying that N/E’s design process is one of continual improvement. A key FAC-related design change he discussed was the use of T11 tubes in the LP evaporator (Fig 11).
Since 2007, Schroeder said, all N/E HRSGs have been built with T11 tubes in these bundles and the risers are straight-run up to the LP drum. Other design changes include the following:
- Use of diffusers in the LP drum, instead of the cyclone separators typically installed, to decrease velocities (Fig 12).
- Use of a low-velocity economizer bottom-header design.
- Relocation of downcomer orifices to reduce turbulence.
- More inspection plugs to allow easer inspection of risers with borescopes.
In addition to the mechanical design aspects of FAC mitigation, Schroeder discussed the role of N/E’s cycle chemistry recommendations, which include no oxygen scavengers and elevated pH—in line with currently understood FAC mechanisms. The importance of periodic boiler inspections also was mentioned.
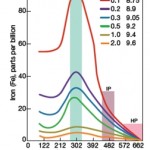
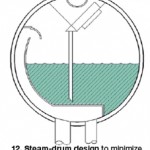
Other areas
Sessions addressed several other FAC-related areas, including discussions around FAC predictive codes of which several were discussed. Key point from this exchange: Predictive codes are only one part of a complete FAC management plan and should not be relied on in isolation; physical plant inspections also are required.
The consensus view regarding cycle chemistry of HRSGs is that for systems of all-ferrous construction (that is, no copper-bearing alloys) oxygen scavengers (reducing agents) should not be used. Reason: They increase the area affected by FAC, aswell as the corrosion rate, by increasingthe solubility of the protectivemagnetite layer in the HRSG.
The optimal water chemistry for HRSGs can be found in EPRI’s guidelines,available on the research organization’swebsite at www.epri.com.Also consult the guidelines offered bythe International Assn for the Properties of Water and Steam (www.iapws.org). The latter is unique inthat it is the only document thatspecifically addresses FAC issues related to two-phase flow.
Key points in the guidelines arethe following:
- Do not use an oxygen scavenger under any circumstances in aplant of all-ferrous construction.
- Operate with a feedwater pH of9.2 to 9.8, or higher.
- Maintain feedwater dissolved oxygencontent at less than 10 ppb(but not zero).
- Depending on plant design, ensure an evaporator pH of 9.2 to 9.8. This may require the use of solid alkali dosing with either tri-sodium phosphate or sodium hydroxide.
Regarding the development of specifications for new projects to design-out FAC risk—or in the word of Dooley, “design out future failures”—consider the following guidelines:
- Separate HRSG drum and desuperheating systems—that is, do not allow the LP evaporator tosupply attemperation water.
- Separate HRSG blowdown systems; do not cascade drains.
- Outfit all evaporators with a solid alkali dosing and control system for use with either sodium hydroxideor tri-sodium phosphate.n Ensure all-ferrous condenser(could be titanium or stainless steel) and HRSG construction.
- Eliminate use of oxygen scavengers and require implementationof a high-pH AVT(O) cooling-towerbased treatment program. Specify the use of 1.25% (P11) or 2% (P22) chrome materials in the HRSG at locations where there is a high risk of single- and/or two phase FAC.
- Increase the number of sampling locations in accordance with IAPWS guidelines. Include the ability to sample from all preheater and economizer sections.n
- Ensure that all sampling and analysis systems easily allow use of corrosion-product samplers with suitable sample flow and that primary coolers are close to the extraction point.
- Finally, you may also consider installing a full-flow condensate polisher capable of ammonia-cycle operation—especially for seawater-cooled plants.
Experts’ panel, discussion
The day after the formal program concluded, a half-day Experts’ Panel and Roundtable was convened for follow-on discussion. Seven attendees with expertise in various aspects of FAC opened the forum with assessments of the formal presentations made during the three previous days. There were about 50 participants on the fourth day, attesting to the meeting’s value and importance.
The discussion was robust and continued at a brisk pace until the end of the time allocated. Group consensus was that, although there is an excellent technical understanding of FAC in fossil-fired and combined-cycle plants, there continue to be unusual and unexpected observations in working plants. Additional research is needed to explain these observations and to improve and expand FAC prediction and inspection capabilities. Also, continued transfer of FAC technical knowledge to end users is needed.
Important discussion points included the following:
- The best FAC programs are supported by management and clearly define policy, roles, responsibilities, and resources.
- Communication and clearly defined specifications are critical to success of FAC- resistant designs and to the inspection of components for FAC damage.
- FAC rates are variable and depend on many factors. A conservative approach must be taken when considering repair/replacement of damaged components.
- In-kind replacement of damaged components will lead to additional FAC; modified geometries can increase the damage rate. Use of steel containing 0.1% or more chromium eliminates FAC susceptibility.
- Alternative chemistry control practices should be considered for mitigating two-phase FAC. Approaches mentioned included use of neutralizing amines—possibly blended with ammonia for pH control—and filming amines.
- In units with oxidizing chemistry, closure of deaerator and feedwater heater vents can reduce two-phase FAC damage. Many plants that can operate with vents closed do not.n Use of commercially available robotics technology appears to offer the greatest possibility for improved inspection of HRSGs.
- Alloy analyzers are less commonly used in fossil plants than they are in nuclear plants.
- Iron monitoring, while generally accepted as a means of evaluating FAC control, is subject to several sampling and analysis concerns. Use of particle monitors to provide an indirect indication of corrosion product transport is now being evaluated in several plants, including some with ACCs.
- End users indicate additional FAC awareness and training is needed in many cases.
End note
A disappointing aspect of the conference, in the author’s view, was the lack of participation by the chemical supply companies. They provide advice and services to many plants worldwide and often recommend chemical treatment programs out of alignment with current best practices.
The meeting offered an excellent opportunity for them to present their alternative viewpoints regarding FAC control so they could be discussed in an open forum to the benefit of all participants. Perhaps more chemical suppliers will participate in the 2013 conference. ccj