Capitalizing on work presented by Xcel Energy at meetings of the HRSG Forum with Bob Anderson, ETD’s Dr Ahmed Shibli and William Moore produced an extensive report for the consultancy’s Group Sponsored Project on drones and robots for powerplant inspection. The highlights of this work were discussed at European Technology Development Ltd’s International Conference on Power Plant Operation and Flexibility, London, July 2018.
The exploratory phase (just completed) of this project was directed at determining suitability of drones and robots for visual and UT inspection, as well as a review of R&D activities. The upcoming phase is the design and development of the most suitable and economic automated devices in three types:
1. Drones for visual inspection and data analysis of remote, out-of-view and at-height components.
2. Robots for polishing and UT inspection of components including crack sizing.
3. Small or mini-robotic devices for polishing and UT inspection requiring access through narrow spaces—such as between HRSG tubes.
Various organizations and experts are involved and more are invited to participate.
Drones. One development point is the oil and gas industry, currently using drones for UT inspection by attaching them to pipes (Fig 1). However, drones are not yet stable enough for complete UT inspection.
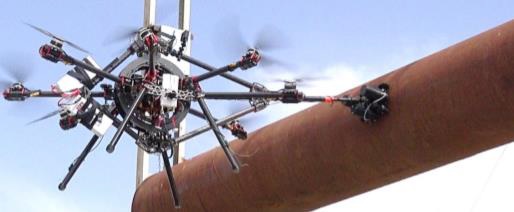
Some significant points were made:
1. Photos taken by modern commercial surveillance drones can be enlarged on a computer screen by factors greater than 20× before pixilation creeps in.
2. Such detail can help diagnose the cause of failures. In the case of a burst evaporator tube, for example, a thick edge can indicate impure feed or boiler water; a thin edge can indicate overheating, fireside wastage, etc.
3. This valuable information is available as soon as the boiler has cooled sufficiently for access.
In emergency shutdowns, a drone is a frontrunner for immediate access to the failure location. Quick access is especially beneficial if there is a need to procure materials or services. It also enhances the placing of scaffolding in the correct, precise location. Plus, drones can check surrounding areas before a chain of failures occurs and capture a permanent record.
For thermal surveys, drones are particularly adept at carrying thermal imaging cameras and reaching correct positions. This can identify the areas of heat leak or damage to insulation.
Powering the drones carries two options: internal combustion engines, or electrical power. Electric became the choice with lithium batteries, but carrying loads for long time periods is difficult. The group sponsored project is investigating this further.
Robots. For this project, a robot is defined as “a surface crawler that carries out visual/NDE inspection and sends inspection data to a remote-control unit.”
Robots can reach inaccessible areas, or those where scaffolding is required. There is a range of proven technologies for robots, robotic machines, and intelligent flexible arms, but further development is needed for the powerplant environment—for example, polishing heads and UT probes for wall-thickness measurements.
Current development recognizes the challenges. Robots are not suitable for climbing tubes with thick deposits. Closely-spaced wall tubes can limit access, and plants have wide variations in tube diameters and tube-to-tube gaps.
A look ahead. Robotic arm development, especially for access through narrow spaces, shows promise. Stated Shibli, “a highly flexible and long robotic arm of about 0.4 in. diameter is needed that can pass between tubes in an HRSG, has multiple axes of rotation, and can carry out visual examination, surface polishing, initial inspection, and assessment.”
The next phase of this ongoing group sponsored project is development of “a novel drone-robot hybrid device.”
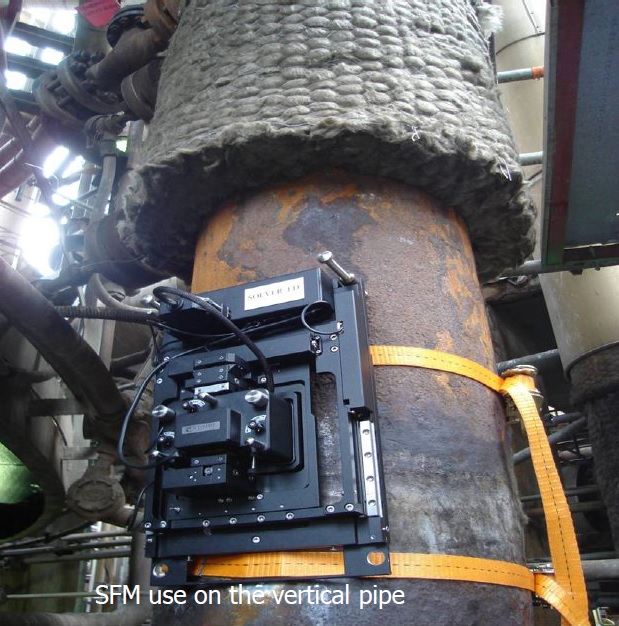
Other inspection techniques discussed at the meeting included Obikou, a pipe strengthening mechanism for creep damage and/or steam welded pipes (ETD); a portable scanning force microscope (Fig 2) for early-stage creep and fatigue damage detection and life assessment (ETD); electrical discharge sampling equipment for removal of samples from pressure vessels and turbine rotors for quality checks and life/crack assessment (ETD/SGS, UK); portable magnetic measurement equipment for onsite creep damage detection (Univ of Manchester, UK); and shop welding interruptions of P91 components (PPC, Greece).