The 2020 conference of the 501F Users Group marked GE’s fourth year of participation in this event, coordinated by Said El-Nahas, 501F product manager, and Ben Myers, service engineering manager. The program began with an introduction to GE Gas Power, a new organizational structure combining the company’s new-unit and services operations under a single business entity focused on advancing sustainable gas-plant technology.
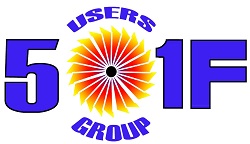
The steering committee requested presentations from the OEM on its exhaust frame and HRSG cleaning solutions, plus an update on hex-chrome findings. The session concluded with a refresher on GE technology adoption for 501F engines—including cooling/seals, coatings, materials technology, (such as dense vertically cracked TBC), and patterned abradable ring segments to extend the repair interval.
GE reported on the success of its performance upgrades at the 2 × 1 Tuxpan and Norte-Durango combined cycles, owned by Naturgy Mexico SA de CV. The former is powered by Mitsubishi 501F3s, the latter by Siemens 501FD3s. Both plants are covered by GE performance LTSAs and include planned and unplanned maintenance for gas and steam turbines and auxiliaries, generators and auxiliaries, main-steam valves and actuators, and control systems. Here’s what the speakers said:
-
- Maintenance intervals were extended to 32k hours/1250 starts.
- Output was increased by up to 9.2%.
- Heat rate was reduced by as much as 2.9%.
Regarding the exhaust frame, the speakers reported the following findings:
-
- Severe liner cracking.
- Strut creep affecting rotor position.
- Bearing damage.
- Baffle seal plate cracking.
GE’s objective was to mitigate these issues by developing repair solutions that could be implemented during a major inspection without schedule impact. Engineers developed an upgraded two-piece exhaust cylinder, made improvements to the saddle and strut shield, and upgraded baffle seals (new material and replaceable during an outage). Specialized repair processes also were developed for field implementation.
HRSG cleaning technology was covered next—specifically GE’s PressureWave Plus system. It was said to be superior to standard dry-ice cleaning, deep-clean dry-ice cleaning, and water washing regarding the following: no scaffolding required, reduced risk of fugitive emissions during startup after cleaning, reduction in cleaning time, depth of cleaning of at least 3 ft, and of no risk to pressure parts.
Hex-chrome concerns, probable causes, and containment/corrective actions were equal or similar to those presented at other user meetings in the last couple of years. Attendees were referred to GE’s PSSB 20180709A/B document and any subsequent update.