Re-engineering, new surface boost reliability, efficiency, operational flexibility
Experience teaches that after heat-recovery steam generators (HRSGs) operate for about 15-20 years, major work is required for one or more of the following reasons:
- Normal wear and tear has taken a physical toll.
- Forced outages are increasing and availability is decreasing.
- Equipment performance is off design values by a significant amount.
- New emissions regulations.
- New operating paradigm (for example, was base load, now cycling).
- Spare parts (control systems, in particular) are difficult to obtain and no longer supported by the OEM.
Upgrade of ageing equipment, rather than simply replacement-in-kind, can offer owner/operators many benefits, Zahi Youwakim told his colleagues at the recent Frame 6 Users Group meeting in Scottsdale, Ariz. He offered his experience at Texas-based Huntsman Petrochemical Corp as a case in point. Youwakim, a member of the user group’s steering committee, is the utility plant engineer at that facility.
Huntsman purchased the Port Neches (Tex) assets of Texaco Chemical Co in 1994. The acquisition included cogeneration units CG-9 and CG-10, each consisting of a Frame 6B gas turbine and HRSG. Youwakim, a 1980PennStategrad, knows this equipment well, having been a Texaco employee at Port Neches during its installation.
He began by reminding the mixed group of utility- and process-plant asset management and O&M personnel that steam system reliability is more important to a chemical plant than reliability of power production. Reason is that any interruption in steam supply adversely impacts product output; electric power, by contrast, can be purchased from others.
HRSGs. The single-pressure (600 psig) HRSGs for CG-9 and CG-10 had been problematic since first operation in 1991. Youwakim recalled that “from Day One, the boilers suffered from a high delta p across the economizer and it was not possible to deliver rated feedwater flow to the steam drum.”
In addition, the circulation rate was too low and superheater gas temperature too high. Overheating of superheater tubes damaged fins and caused tube failures (Figs 1, 2).
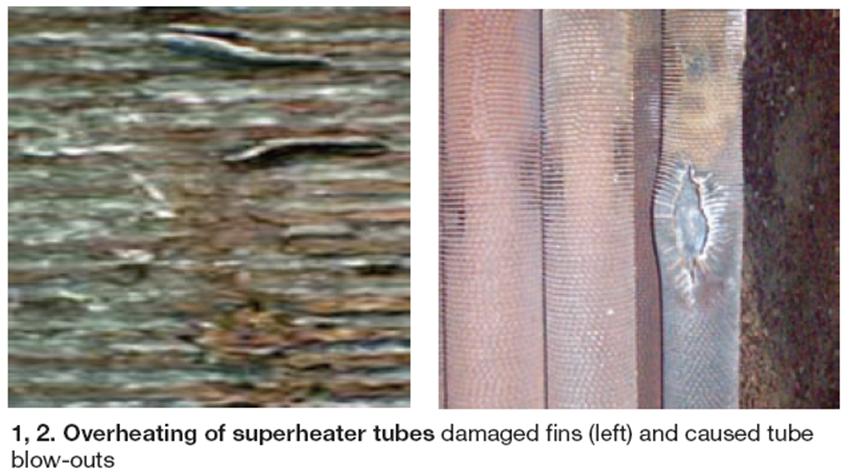
The HRSGs were supplied by Houston-based Energy Technology Inc (best known by the acryonym Entec), which closed its doors the same year Huntsman purchased the Texaco facility. The units were designed to produce up to 325,000 lb/hr under the most favorable ambient conditions; stack temperature was 365F (Fig 3).
Huntsman needed more steam from its boilers and had to address other design deficiencies as well to achieve the 35-yr lifetime expected of these units. One goal was to boost boiler efficiency by reducing stack temperature to 300F-325F, another to achieve 750F steam temperature [plus over minus] 25F for the entire range of ambient conditions—100F at 100% RH in summer to the rare 20F winter day—with normal operation of medium supplemental firing and the full 750F under the most demanding conditions at maximum fire.
The chemical company selected six vendors to bid the redesign/rebuild project, requesting cost and outage time to achieve the following alternative solutions:
- Rebuild as is.
- Re-engineer and reconstruct the units to (1) eliminate economizer restrictions on feedwater flow, (2) increase the circulation rate, and (3) eliminate superheater problems.
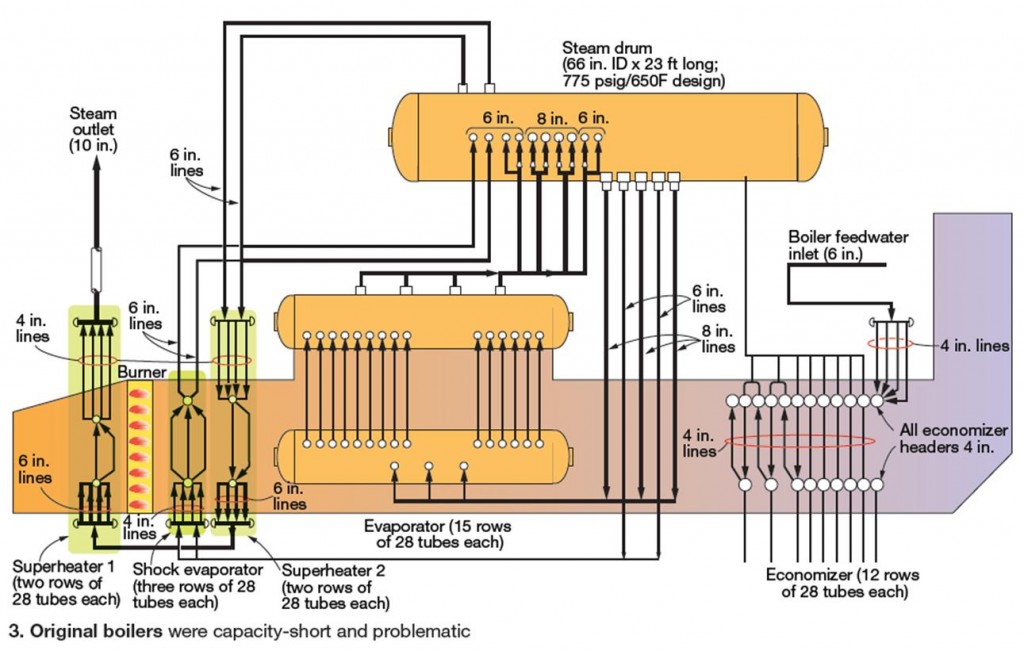
Youwakim said Huntsman told the bidders that it really was not interested in an as-is rebuild. It wanted a re-engineered, reliable HRSG capable of covering the plant’s wide operating range. Further, the successful bidder would have to explain to the chemical producer’s satisfaction how it would address the three major deficiencies noted in the bullet point immediately above.
Downtime to complete the project was another major consideration, as was safety. This dictated maximum prefabrication and working onsite 24-7 to completion.
Rentech Boiler Services Inc, Abilene, was the successful bidder. The company’s Lee King told the editors that Rentech seldom does in-kind replacement work. He said the company’s engineers generally can get higher efficiency and lower emissions through re-engineering and are comfortable offering process guarantees on improvements.
Youwakim told Frame 6 attendees that Rentech increased boiler output from 300,000 to 325,000 lb/hr to 350,000 to 375,000 and decreased stack temperature to 320F to 330F, 35 to 45 deg F lower than previously. He said a 25-deg-F drop in stack temperature reduces heat input by 8-million Btu/hr.
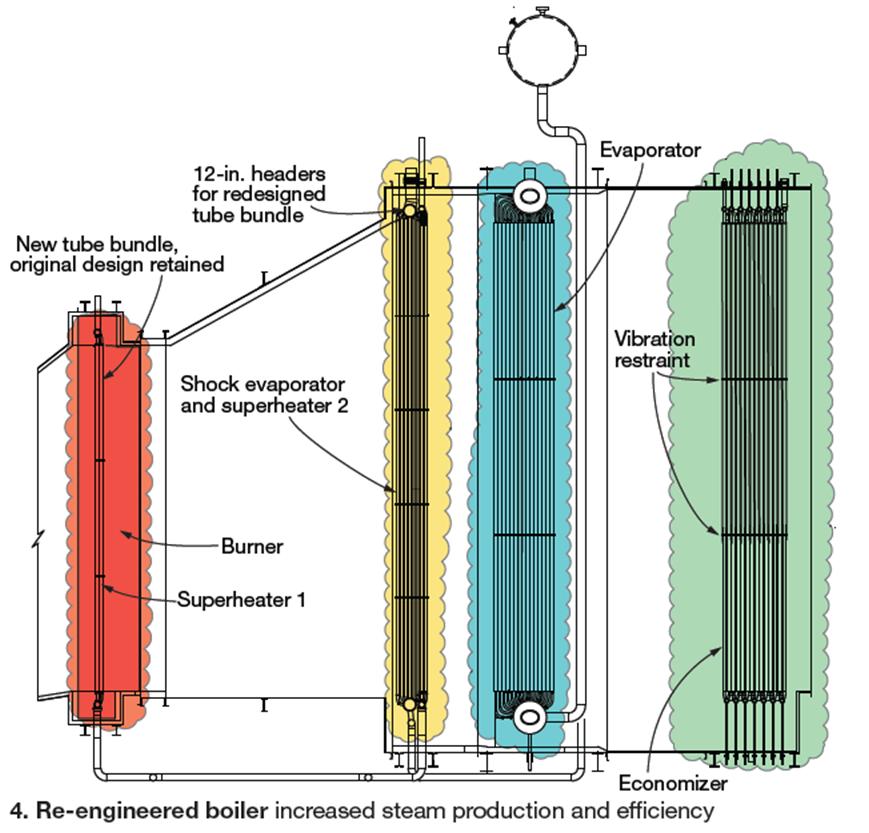
Recirculation rate, formerly 7.5:1 to 8.7:1 depending on ambient conditions, was increased to a minimum 10:1 on the coldest winter day and to 14:1 in summer.
King said that Huntsman’s objectives were met within both budget and the planned 45-day outage (per HRSG), and without a lost-time accident, by making the following modifications to the boilers (refer to Fig 4):
- Double the heat-transfer surface of the shock evaporator by adding three rows of 28 tubes for a total of six rows x 28 tubes, and changing the size of upper and lower headers to 12 in. from 8 in.
- Riser piping from the upper headers to the steam drum was increased to 10 in. and 10 x 6 in. reducers were installed to accommodate the 6 in. existing drum nozzles. The 6-in. drum feeders to the lower shock-evaporator headers were retained.
- Minimum wall thickness for tubes in the second superheater was increased from 0.120 in. to 0.150.
- Casing liner in the area of the shock evaporator was changed to Type 310 stainless steel. Baffles and tube vibration restraints throughout the unit were swapped out with Type 310.
- Riser piping for the evaporator section was increased to 12 in. from the original 8 or 10, to improve circulation. Keep in mind that these were not arbitrary changes (Fig 5). They resulted from detailed engineering calculations required by the ASME Boiler and Pressure Vessel Code.
- Fabric expansion joints were replaced with stainless-steel bellows type.
- Fin material for new tubing in heat-transfer sections is Type 409 stainless steel. It can handle gas temperatures up to 1250F, or 350 deg F above the recommended limit for carbon steel. The better material is
expected to virtually eliminate fin wastage. - The economizer was reconfigured to reduce the water-side pressure loss and heat- transfer surface was increased by 16% (addition of two rows) to reduce the exhaust-gas temperature (Fig 6).
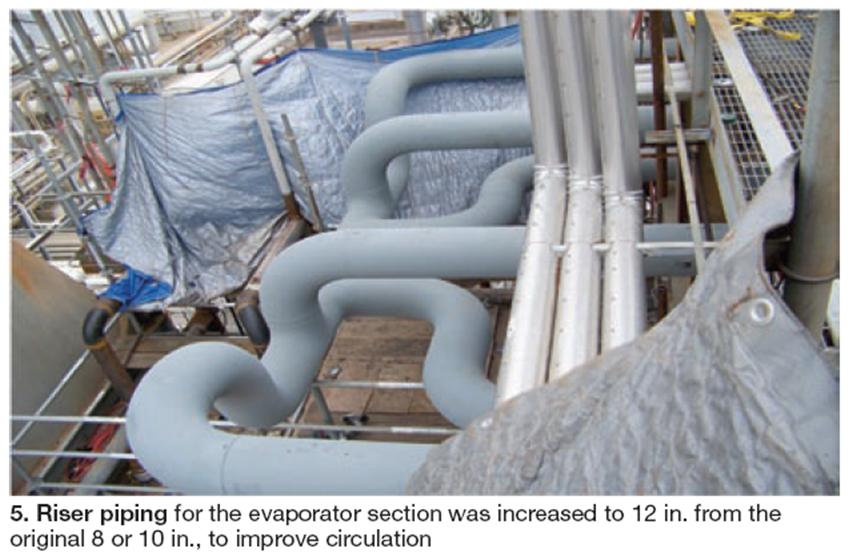
The most successful projects generally are characterized by a collaborative project team consisting of vendor and owner experts from engineering, fabrication, and field-execution disciplines, Youwakim continued. The team must be committed to meeting the contract goals, schedule, and budget. The highest level of cooperation is necessary to adjust seamlessly to changes in weather, supply-chain upsets, etc.
Youwakim’s final thoughts: Think safe, think smart, work safe, work smart. CCJ
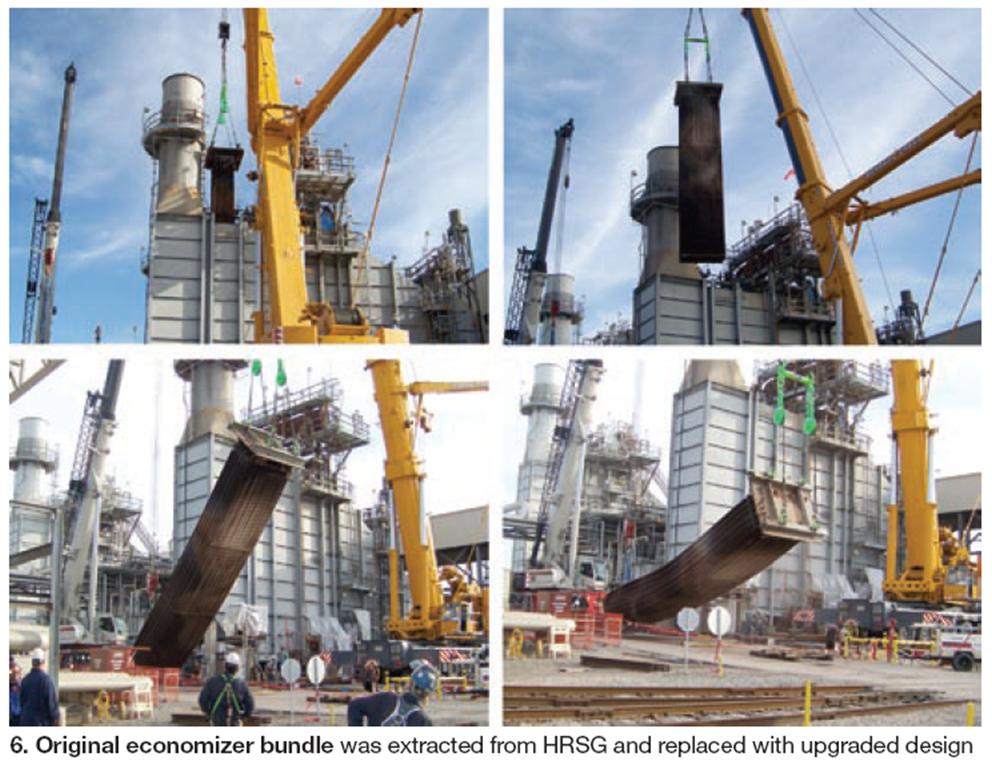