IAPWS helps plants control cycle chemistry
One of the benefits of attending last fall’s Air-Cooled Condenser Users Group meeting in Las Vegas was a review of guidelines for the operation of steam/water circuits in combined-cycle plants available through the International Association for the Properties of Water and Steam. Owner/operators worldwide can benefit from learning more about how this international non-profit association of national organizations can help them extract top performance from their Rankine cycles.
Dr Barry Dooley, a senior associate at Structural Integrity Associates Inc, and the executive secretary for IAPWS, brought attendees up to date on the IAPWS Technical Guidance Documents that can be downloaded from www.iapws.org at no charge; consider reviewing the following at your earliest convenience:
- “Procedures for the measurement of carryover of boiler water and steam,” to help prevent steam turbine damage.
- “Instrumentation for monitoring and control of cycle chemistry for the steam-water circuits of fossil-fired and combined-cycle power plants” provides guidance on the minimum level of key instrumentation required for managing water chemistry.
- “Volatile treatments for the steam-water circuits of fossil and combined-cycle/HRSG power plants” includes the basis for AVT and OT for all plants. The key recommendation: Only use oxidizing treatments in combined-cycle/HRSG plants.
- “Phosphate and NaOH treatments for the steam-water circuits of fossil and combined-cycle/HRSG power plants” includes the basis for selecting the optimum boiler/HRSG evaporator water treatment for all drum plants.
- “Steam purity for turbine operation” covers a wide range of failure mechanisms identified with steam turbines.
- “Corrosion product sampling and analysis,” to be published in December 2013, covers the optimum procedures for iron and copper sampling and analysis.
The foregoing documents represent the consensus opinions of the world’s top chemists. National organizations from 21 countries provide the foundation for IAPWS, which makes its standards on cycle chemistry for fossil-fired steam and combined-cycle plants available to all at no cost.
IAPWS, founded in 1929, does much more than develop cycle chemistry standards. It also is the developer of IF-97, which forms the basis for every steam table in the world. Plus, the organization is responsible for all the formulations of water, steam, heavy water, ice, and seawater, as well as all the thermophysical properties of water and steam (density, viscosity, etc).
Dooley also is a member of the ACC Users Group steering committee. Learn more about this organization at www.acc-usersgroup.org.
CCUG recognizes four engineers for their contributions to the industry
The Combined Cycle Users Group recognized four power-industry professionals—Clyde V Maughan, Patrick C Myers, Peter So, and William Wimperis—with its 2013 Individual Achievement Award at the organization’s annual meeting, held last September in Phoenix.
Individual Achievement recognition is earned by industry professionals who have demonstrated excellence throughout their careers in the design, construction, management, operation, and/or maintenance of generating facilities powered by gas turbines. The four outstanding individuals honored in 2013 were selected by the CCUG’s Awards Committee, chaired by Andy Donaldson, VP projects for WorleyParsons. Nominations for the 2014 awards are now being accepted (see sidebar on p 34 of this issue).
The career accomplishments of the 2013 recipients are outlined below:
Clyde V Maughan
President, Maughan Engineering Consultants
Maughan, who turned 87 two months ago, spent the first 36 years of his career after graduation from the Univ of Idaho (BSEE, 1950) at the General Electric Co as an engineer and manager in generator and turbine engineering design/service/development/manufacturing and a variety of other positions. Since retiring from GE, Maughan has been in private practice.
Along the way, he has been directly involved in 250 or so repair projects on generators from 2 to 1400 MW supplied by virtually all of the world’s major manufacturers. This work has included several dozen root-cause investigations of complex failures on stator and field components.
Plus, Maughan has served on several IEEE and IEC committees and working groups; managed a couple of major projects for EPRI; written or coauthored more than two-score major technical papers; published a handbook of more than 200 pages on generator repair and conducted nearly three dozen seminars (total of more than 1000 attendees) worldwide based on that work; and still had time to get an MS in Mechanical Engineering from Union College.
Most recently, Maughan has focused on disseminating to engineers worldwide the volumes of information he has compiled over the years. Much of this effort has been facilitated by the International Generator Technical Community™, an online forum that he helped to create. The IGTC library contains most of his technical documents. CCJ-online.com hosts the articles Maughan has published in the Combined Cycle Journal, as well as a series of webinars he conducted for CCJ ONscreen.
Patrick C Myers Sr
Plant Manager, Ceredo Generating Station, AEP
Pat Myers’ career contributions to American Electric Power and the Ceredo Generating Station that he manages are believed “immeasurable” by colleagues. Like many in the industry, Myers is a mechanical engineer who got his start at the General Electric Co as a field engineer. Later, he spent a couple of decades with the Columbia Gas Transmission Co before transitioning to AEP.
Following a series of relatively recent natural-gas explosions that caused deaths and considerable loss of property, Myers was appointed chair of an AEP internal team that designed and implemented venting and purging procedures for that fuel. This work earned Myers industry recognition and speaking assignments and his company a top Best Practices Award from the Combined Cycle Journal.
Myers has been the de facto leader of the 7EA Users Group steering committee for several years. This organization, which covers 7B-E models, as well as 7EAs, has benefitted considerably from his willingness to share knowledge and experience.
Peter So
Project Development Manager, Calpine Corp
Peter So has been involved in the development of several leading-edge technologies in his more than two decades of work on gas turbines in simple- and combined-cycle service. Currently, So manages the development of new projects and major plant modifications for Calpine in the West—including those involving fast starting, fast loading, and reduced startup emissions.
Over the years he has been awarded patents in the following areas:
• Inlet bleed heat and power augmentation.
• A method for providing off-gas to a combustion system.
• GT engine controls for minimizing combustion dynamics and emissions.
The former GE DLN specialist and startup engineer previously served Calpine as a senior performance engineer and as manager of turbine controls. Among his many accomplishments, So led the software development of the first PSM LEC III retrofit on a 501D5. Plus, he was the lead controls engineer for the company’s Humid Air Injection Project.
So also has been a long-term active member of the steering committee for the 7F Users Group, contributing significantly to the organization’s growth. A former co-chairman of the 7F Users, he currently serves as treasurer.
William Wimperis
Director of Project Management (retired), Constellation Energy
Bill Wimperis is one of the electric power industry’s pioneers in the formation, organization, and development of user groups for sharing technical information on gas turbines. He served more than two decades as a member of the steering committees for the 7F, 501F, and 501G User Groups.
One of the founding members of the 7F Users Group, Wimperis was chairman of that organization for several years. His comprehensive notes from the early meetings are legendary. After 10 years on the 7F steering committee, Wimperis moved over to the 501F Users Group from 2000 to 2007 as his company’s fleet diversified. Most recently, he served the 501G Users Group from 2008 to 2012, in lock-step with Constellation’s purchase and completion of the 2 x 1 Hillabee Power Plant.
Wimperis managed several combined-cycle projects for Constellation during his 30 years with the company. His last position prior to retirement at the end of 2012 was director of project management. Responsibilities included overall technical management and leadership, for all matters involving both engineering and development of new gas-fired generation.
Wood Group, Siemens update industry on joint venture
At a press conference conducted during Power-Gen International, Mark Dobler, CEO Wood Group GTS, Neil Sigmund, CEO TurboCare, and Chris Watson, CFO Wood Group GTS, updated the electric power industry on developments surrounding the recently announced joint venture between Wood Group GTS (51%) and Siemens’ TurboCare business (49%).
Dobler, Sigmund, and Watson comprise the senior leadership team for the JV, which has yet to be named. Final approvals on the joint venture are expected in the first quarter of 2014. The business will have about 4500 employees worldwide and generate approximately $1 billion in annual revenue.
All of Wood Group’s maintenance and power solutions businesses—except for its Rolls Wood Group, TransCanada Turbines, and Sulzer Wood JVs—are incorporated in the new entity along with TurboCare’s aftermarket gas turbine, steam turbine, and generator design, repair, and manufacturing services.
Dobler described the new business this way: “The JV will bring together Wood Group’s capabilities in the areas of asset operations, maintenance, risk management, and life-cycle optimization, with the aftermarket design, repair, and manufacturing capabilities of TurboCare to deliver greater flexibility, greater market reach, and an expanded footprint to service customers. The JV will be a significant integrated rotating-equipment service provider to the global power generation, oil and gas, and industrial sectors.”
How the joint venture will benefit powerplant owner/operators is evident in the details presented below for each of the new entity’s four primary business activities:
- OEM. The JV will be the OEM provider of parts, components, and associated overhaul and repair services for the generally more mature Fiat and Westinghouse (up to W501D4) turbines, and through Wood Group Pratt & Whitney, the P&W FT4 and GG4 products.
- Authorized service provider to OEMs. The JV will be an authorized provider of certain maintenance, supply-chain, and construction services to OEMs—including Siemens—for gas turbines, steam turbines, generators, and other rotating equipment.
- Independent aftermarket service provider. The JV will provide a broad independent aftermarket capability for gas turbines, steam turbines, and generators across a range of OEM equipment—including GE and Solar Turbines. This capability will include parts, components, and associated overhaul and repair services.
- O&M and EPC service provider. The JV will provide O&M and EPC services for powerplants in cogeneration, combined cycle, and simple-cycle gas-turbine configurations.
Develop a robust preservation program to protect plant equipment during lay-ups
Inactive powerplant equipment can suffer rapid and oftentimes irreversible damage when left unprotected and exposed to the natural environment. Such exposure can occur before the plant has been completed (Fig 1), as well as after commissioning.
Prior to commercial operation, preservation procedures should be implemented and sustained from the time equipment is manufactured until the plant for which it is intended is declared operational. During this period, warranties, insurance, and other considerations typically dictate that the OEM’s and EPC contractor’s procedures be followed.

Recall that construction on several combined cycles was halted in the early 2000s when the gas-turbine ordering boom went bust and equipment was put in storage, both indoors and outdoors, (Fig 2) as well as in partially completed plants. Following proper lay-up, equipment monitoring programs were put in place under the watchful eyes of preservation professionals to assure degradation mechanisms were being suppressed as intended. A great deal that was learned about equipment preservation during the bust—at plants such as Lenzie, Hillabee, and Dell—is of value for post-commissioning lay-ups.
After COD, the owner generally controls decision-making regarding preservation procedures—except possibly in cases where the maintenance of major equipment is governed by long-term service agreements. A big difference between preservation activities before and after commercial operation is that for the former, procedures are specific to individual pieces of equipment; for the latter, a more holistic approach is likely. Example: One plan for the steam side of the heat-recovery steam generator (HRSG) also may cover HP and reheat steam piping and valves, and the steam turbine.
There are many reasons a plant might be laid up for anywhere from a month to several months—possibly longer. A typical retrofit project—even a major inspection—might require an outage of from four to six weeks; a good snow-pack might keep fossil-fired plants out of service for an entire spring to maximize hydro generation; legal issues could keep a unit from operating for years after completion.
An effective preservation program requires careful planning and diligent management. The fundamentals of these activities recently were compiled into a guidelines document by the engineers and scientists at European Technology Development Ltd, “Preservation Guidelines for CCGT and Conventional Power Plants during Short- and Long-Term Shutdowns,” prepared by ETD’s W Moore, J Ford, T Callagy, and Dr D G Robertson. The guidelines for both wet and dry preservation are based on the practical experiences of industry experts at power producers in both North America and Europe. Write Eur Ing David Slater for more information on contents and price of the 69-page ETD Report 1274-gsp-188.
In a telephone interview with the editors, ETD’s Dr Ahmed Shibli said the major issue with long periods of inactivity is prevention of corrosion and its associated damage, which would adversely impact the plant’s reliability during re-commissioning and subsequent service. He said ETD found information available on powerplant lay-up procedures fragmented, dividing the issues between chemistry and engineering considerations. Some information also was subjective, often linked to the use of a company’s products. The objective of the EDT guidelines, Shibli continued, is to provide a broad view of the options together with the pros and cons.
The guidelines cover storage procedures to accommodate the type of plant, its history, outage time, locally available facilities, materials of construction, etc. Most plant shutdowns are planned, the metallurgist said, giving advanced notice that lay-up procedures will be required. However, there are generating facilities—combined cycles in particular—that need procedures ready for immediate application to accommodate the vagaries of the markets they serve.
Shibli stressed that owner/operators consider the entire plant when developing their lay-up procedures, not just the major equipment. Here’s a checklist of components/systems, among others, he recommended they include: HRSG water and gas sides, lube oil, steam turbine, condenser, generators, condensate/feedwater, water treatment plant, cooling water, transformers, switchgear, etc.
A few of the takeaways from report follow:
- Lay-up procedures depend to a large degree on the materials specified for plant equipment and systems. Example: If austenitic steels are present, then there will be a preference for all-volatile storage solutions (ammonia, for example) and chlorides should be limited to 0.3 ppm to minimize the risk of stress corrosion attack. Take care, Shibli said, to exclude solid alkalis, such as tri-sodium phosphate. The preferred storage method for plants containing copper alloys (condenser tubes, for example) is dry storage. If wet storage is unavoidable, bear in mind that high-pH ammonia-based procedures are not suitable—particularly under aerated conditions.
- The length of the lay-up period and the local environment significantly influence lay-up procedures. In general, wet lay-up is preferred for short shutdowns, dry lay-up for longer periods. However, today’s world is not so straight forward. Grid demands may make it impossible to determine just how long a lay-up will be at the planning stage; sometimes generating units are recalled to service with little notice. Alternatively, if a wet lay-up is prolonged, it is necessary to have a circulation system installed to keep water chemistry balanced throughout the HRSG and to assist in the mixing of any additional chemicals that may be required for the duration of the outage.
- Whether storage is wet or dry, routine checks are required to assure that the preservation plan is working correctly and that the optimal lay-up environment is being maintained (Figs 3, 4) In general, equipment should be checked daily until the storage team is satisfied that the preservation program is stable and reliable. At that point, the frequency of monitoring typically can be relaxed to twice weekly.
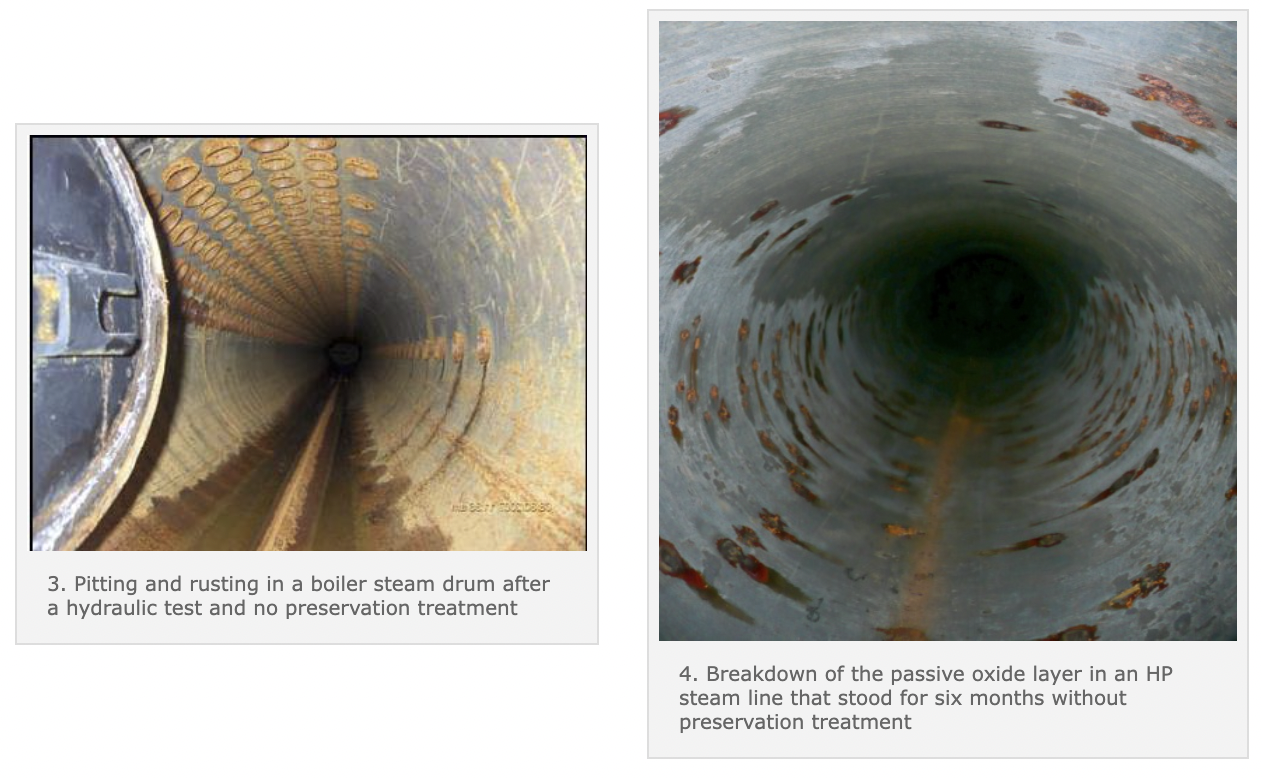
- Some plant modifications likely will be required to implement either wet or dry lay-up. The guidelines summarize available storage procedures and provide an overview of required modifications for each. If the planned storage is expected to be of limited duration, temporary solutions may be satisfactory. But if you expect to put a unit in storage regularly (such as each spring to maximize hydro production), well-designed permanent facilities should be considered. A series of logic diagrams is provided in the guidelines to assist in the development of suitable storage procedures.
Global forum for gas turbines launched to serve owner/operators, other interested parties
A global technical forum for gas-turbine owner/operators and others with interest in this equipment has been established at www.powerplanttechnicalforum.org. This site also serves the highly successful Generator Technical Forum, and the Steam Turbine Forum announced at Power-Gen only a few weeks ago. Most subscribers to CCJ ONsite and the print CCJ are familiar with the generator forum, now completing its fourth year of service to the industry; it is expected to have 2000 registered members (nearly 90 countries) by the end of 2013.
The Gas Turbine Forum is an online network connecting industry professionals worldwide. Like the Generator and Steam Turbine Forums, it is managed and conducted by industry volunteers with financial support from National Electric Coil. The forum’s mission is to facilitate access by electric-power professionals to technical information on gas turbines.
Here’s a list of the moderators for the Gas Turbine Forum, their company affiliations, and the forum subject matter that is their responsibility:
- Forum Master: Justin Voss, AES.
- Overhaul Best Practices: Jeff Fassett, PE, IEM Energy Consultants Inc.
- Component Life Cycle Management: Dr Maxine Watson, Quest Integrity Group (NZ).
- Maintenance Issues: Sal Paolucci, GT Accent Services.
- Control Systems and Monitoring: Joseph Clappis, MD&A.
- Efficiency: Rodger Anderson, PE, DRS Power Technology Inc.
- Governing Protection and Control: John Downing, Turbine Controls & Excitation Group Inc.
- Auxiliary Systems Reliability: Scott Cavendish, PE, Independent Turbine Consulting.
- Aeroderivatives: Bill Torrance, C Eng, Independent Consultant (UK).
- High Impact/Low Probability: Sep van der Linden, Brulin Associates.
Important for users to understand is that this new forum does not replace any forums already existing within the gas-turbine community, it complements them by focusing on engine technology as it is applied to all types of gas turbines the world over. There are many valuable forums addressing specific engine models, several of which are hosted by users groups on their websites—such as the Western Turbine Users Inc, 501D5-D5A Users, 7F Users Group, and CTOTF™. Other forums—such as those for the 7EA, 501F, and 501G Users Groups—are hosted at www.users-groups.com.
Bridging the gap between raw talent and experience
Power-industry executives are often heard lamenting about the ageing industry workforce and the difficulty they have finding new and capable employees for their businesses. Two thoughts:
- Turnover is not always a bad thing. It creates space for the innovative thinking needed to drive the organization forward.
- The responsibility for developing the talent needed to advance the business is yours, not a university’s, the military’s, or any other organization’s.
Many generating companies, and manufacturers and services firms associated with the electric power industry, provide financial support for training programs, internships, and university courses to help develop future talent. That’s the “right thing” to do and commendable. Cutsforth Inc took its involvement in the development of future engineers to the next level by working directly with students from the Univ of Minnesota who needed help manufacturing custom wheels for their entry, Daedalus, in the 2013 World Solar Challenge (Fig 5).
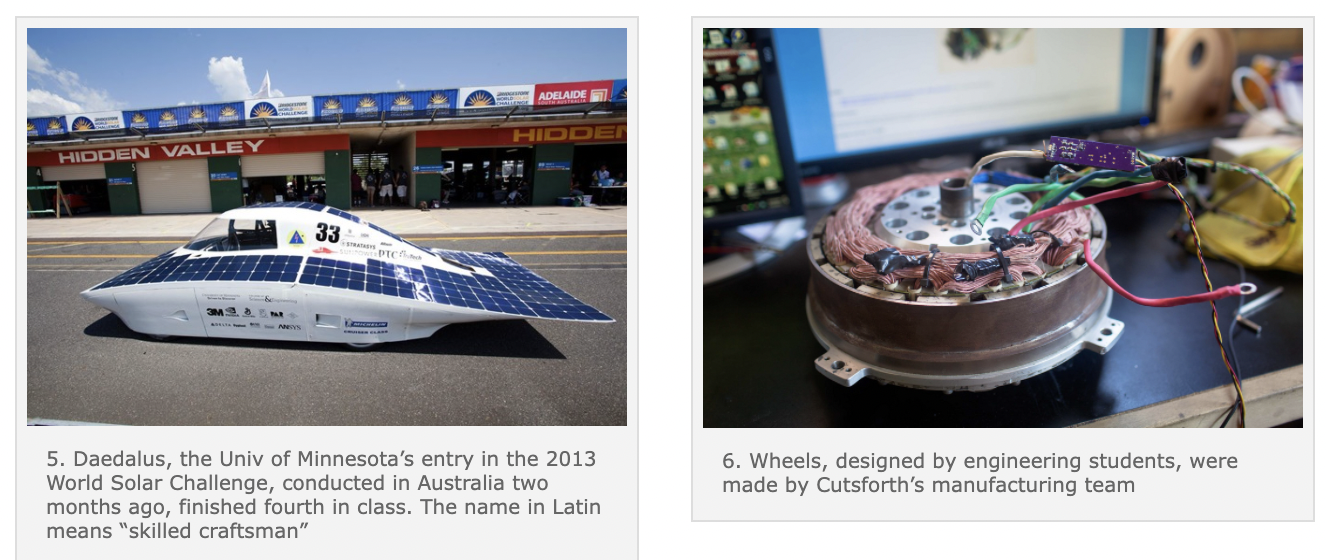
The wheels for the ultra-light solar vehicle were designed by the engineering students; Cutsforth’s manufacturing team CNC-machined them from solid blocks of aluminum to a tolerance under 0.003 in., thereby eliminating the need to balance the wheels after the tires were mounted. In an innovative approach to space and weight savings, portions of the electric motors were designed to be housed inside the wheels themselves. Cutsforth’s manufacturing team helped to make this goal a reality (Fig 6). More than 80 hours of programming and CNC machining time went into wheel production. All labor and materials needed to make the four wheels were donated by Cutsforth.
The World Solar Challenge, held every two years in Australia, runs north to south from Darwin to Adelaide, a distance of nearly 1900 miles. The Univ of Minnesota team finished the grueling race, placing fourth in the Cruiser Class.
Summing up Cutsforth’s involvement in the innovative project, GM Benjamin Warums said, “The electric power industry is where we work and this project allowed us to help the students working toward the advancement of alternative forms of energy. We were honored to be approached by the Univ of Minnesota and take great pride in our manufacturing team’s ability to hold tight tolerances. Helping future innovators was a natural fit for Cutsforth. We congratulate the university’s solar car team for its creative work and for finishing the race.”
Peaker produces 180 MW in 12 minutes, holds emissions within California limits
Over the last couple of years, Siemens Energy Inc and Mitsubishi Power Systems Americas Inc have strengthened their positions among the technology leaders for frame gas turbines. Siemens’ successes include H-class and fast-start/fast-ramp combined cycles, Mitsubishi’s include 501GAC-powered combined cycles and its giant J-class gas turbine.
Power producers evidently have been impressed, judging from the two-to-one advantage the two companies held over perennial market leader GE Energy in sales of frames for US electric generation in 2012 (capacity basis).
More recently, Siemens and Mitsubishi collaborated to assure the success of NRG Energy Inc’s four-unit, nominal 720-MW Marsh Landing Generating Station, a simple-cycle facility in Antioch, Calif, about 40 miles northeast of San Francisco. It began commercial operation May 1, 2013. Siemens supplied four SGT6-5000F (501FD4) gas turbines equipped with ULN (ultra low NOx) combustion systems, four SGen-1000A generators, the SPPA-T3000 control system, and balance-of-plant equipment, as well as technical support for installation and commissioning.
Mitsubishi provided a leading-edge dilution SCR system for each engine to reduce the 9 ppm NOx/4 ppm CO in turbine exhaust to 2.5 ppm/2 ppm out the stack. Ammonia slip is restricted to 10 ppm. Cormetech Inc and Johnson Matthey supplied state-of-the-art SCR and CO catalyst formulations, respectively, to guarantee emissions conformance.
Siemens partnered with NRG to implement an integrated control technology that allows the plant to maintain low emissions while navigating fast, intermittent load ramps. All four units demonstrated ramp rates of up to 32 MW/min, reaching base load in 12 minutes while holding emissions within permit limits. Siemens refers to this as its Clean-Ramp™ technology.
Mitsubishi’s scope included CFD and physical flow modeling to guide the design and supply of all equipment from the gas-turbine expansion joint to the stack, including the following:
- SCR catalyst modules and drop-in CO catalyst panels.
- Inlet and outlet transition ducts and all expansion joints.
- A 2 x 100% tempering-air/purge-air skid complete with accessories and interconnecting ductwork from the fans, including tempering-air distribution devices within the SCR system casing.
- Ammonia forwarding skid, vaporization skid, and injection grid with balancing manifold.
- PLC-based SCR emissions controls and control logic interface to the DCS.
- Exhaust stack with advanced silencing systems.
Marsh Landing, located on a 27-acre brownfield site in a challenging seismic zone, complies with some of the nation’s most strict limits for NOx, CO, VOCs, and particulates. The facility sits adjacent to the Contra Costa Power Plant, a nominal 680-MW station with two 1960s gas/oil-fired steam units; it was retired the day the new facility began commercial operation.
Marsh Landing relies on water and wastewater infrastructure owned by the city of Antioch and the Delta Diablo Sanitation District. Its planned water consumption of 50 acre-ft/yr is a 99.99% decrease from what Contra Costa required. The old steam plant had a once-through cooling system.
NRG has a 10-yr power purchase agreement with PG&E for the entire output of the facility. Electricity is delivered to the utility’s existing switchyard adjacent to Marsh Landing via 230-kV lines. Natural gas is supplied via a new pipeline that connects to PG&E’s interstate gas transmission line 400 about ¼ mile from the plant.
Hill to succeed Fusco as Calpine’s CEO next May; company has a good third quarter
Calpine Corp’s board of directors has selected Thad Hill, the company’s president/COO, to succeed Jack Fusco as CEO when the latter assumes the role of executive chairman of the board in May 2014. The change is part of a planned leadership transition. Hill joined Calpine in September 2008 from NRG Texas where he served as president in 2007-2008.
Calpine Corp is said to generate more electricity than any other independent power producer in America. Its fleet of 93 powerplants totals 28 GW of nameplate capacity in operation or under construction. The company reported an increase in third-quarter operating revenue of 18.3%, year over year; net income increased by more than 11%.
Beyond the financials, Calpine plant and central engineering personnel contributed to the company’s success in the third quarter by:
- Producing more than 30 million MWh.
- Achieving a record-low year-to-date fleet-wide forced outage factor of 1.4%.
- Delivering record-high year-to-date fleet-wide starting reliability of 98.8%.
- Reducing year-to-date plant operating expenses by about 7%.
- Maintaining top-quartile safety metrics: 0.85 total recordable incident rate year-to-date.
Significant plant developments in the third quarter include the following:
- Russell City Energy Center commenced commercial operation in August. The facility, which produces 429 MW of base-load and 464 MW of peak capacity, is under contract to deliver its full output to PG&E for 10 years.
- Los Esteros Critical Energy Facility was recommissioned as a combined-cycle plant and resumed delivering power to the grid in August. The facility began life in 2003 as a four-unit LM6000 peaking facility with a rated output of 188 MW. Conversion to combined cycle increased generating capability to 309 MW while increasing efficiency and environmental performance.
- Osprey Energy Center achieved 100% starting reliability and 0% forced-outage factor.
Products/services
Camfil Farr Power Systems’ lab-on-wheels (the Camlab) allows gas-turbine users to evaluate, in real time under the actual operating conditions at their sites, alternative filtration solutions simultaneously with no risk to operating equipment.
Clark-Reliance Corp announces Safe View™, a shield for use on armored-glass liquid-level gauges to protect operators from high-pressure leaks, a rare but potentially dangerous situation. The shields are easily retrofitted on C-R Jerguson® gauges as well as on similar gauges made by others.
Company news
Wood Group GTS is awarded a six-year contract to provide maintenance services for a GE 7EA at a manufacturing facility in Texas. This includes all major maintenance services—including parts, repairs, field services, and the installation of M&D technology for predictive performance management. . . .A southeastern power producer selects the company to supply ECOMAX™ combustion tuning and dynamics monitoring systems for a fleet of 7FA gas turbines.
International Generator Technical Community (http://www.generatortechnicalforum.org) announced its highly successful discussion forum for generator professionals now has 1900 members in 88 countries. Also, that it has expanded into steam turbines. Bios for the steam-turbine discussion moderators, volunteers all, and their areas of expertise are posted on the website.
ABB announced it had established a new Turbine Automation Center of Competence for steam- and gas-turbine applications, based in Natrona Heights, Pa. Focal point of the effort is the development of products specific to turbine automation for the company’s Symphony Plus control system.
Mistras Group reported is acquisition of Carmgen Engineering Inc, a professional engineering consulting and technical training services provider, capable of helping clients shorten the duration of their outages and extend the interval between shutdowns without compromising safety and reliability.
Chromalloy acquires Trac Group, which provides design, engineering, and manufacturing of complex HP and LP turbine components—including blades, segments, and vanes. The company also appoints Jason Humphries business development director to lead new component repair developments for turbine engine manufacturers and operators for the company’s Carson City (Nev) and Mexicali operations.
Metso and Turbine Services Ltd agree to use the Metso DNA turbine automation system on all future projects where TSL supplies turbine components and other materials.
NRG Energy Inc enters into an agreement to acquire Edison Mission Energy’s 8-GW portfolio of powerplants.
Portersville Valve Co LLC and PRD Technologies LLC, both suppliers of pressure-relief systems for powerplants, agree to merge.
Hamon Deltak Inc opens an office in Denver.
People
NAES Corp opens a new facility for its Industrial Services Div in Sulphur, La. . . .hires Tom French, most recently self-employed, as VP Quality Assurance. . . .hires Kevin Taylor, former president of MasTec Inc, as senior VP of engineering and construction.
Victory Energy hires Vijay Patel to help lead the company’s business expansion efforts in the power and utility markets.
ProEnergy announces the addition of Charlie Athanasia as COO and Craig Kingsley as VP turbine services. Athanasia was VP of Alstom’s thermal services business in North America; Kingsley has more than 20 years of operations and general management experience in the heavy industrial turbine market with Dresser-Rand, TGM, Sulzer, and GE.
Plant news
Burbank Water & Power, Magnolia Power Plant. Bill Hutchings, a long-term CCJ supporter, reports that the project team for the award-winning 1 x 1 Magnolia combined cycle recently celebrated the 10th anniversary of the project’s groundbreaking (Fig 7). Located in downtown Burbank, the unit incorporates the world’s first GE HEAT™ (high-efficiency advanced technology) steam turbine, operates solely on reclaimed water, and includes an advanced zero-liquid-discharge system.
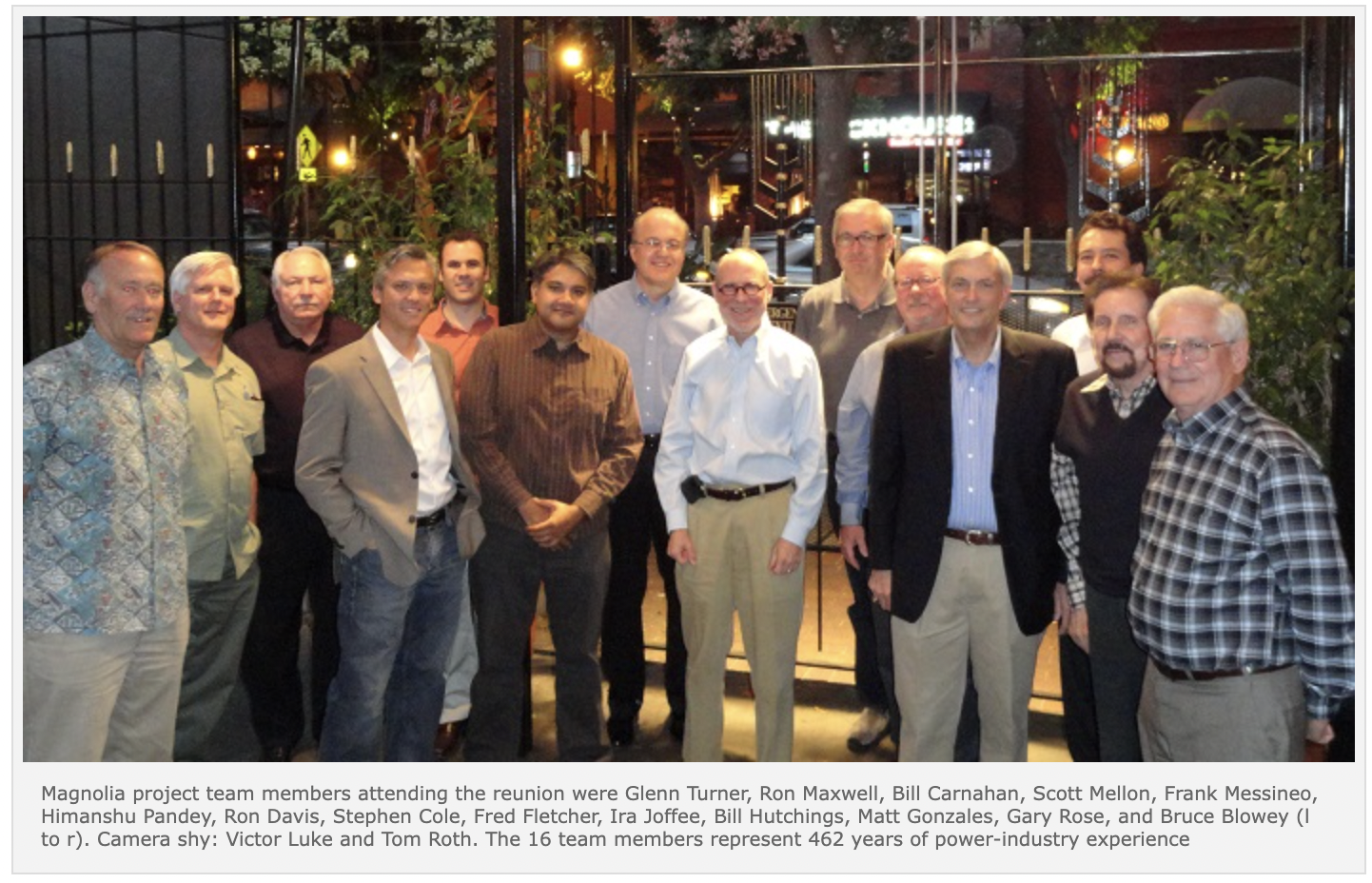
Ameren Missouri’s Maryland Heights Renewable Energy Center receives CCJ’s 2013 Pacesetter Plant Award for advancing the state-of-the-art for the electric power industry in the use of renewable fuels for carbon management, the combustion of challenging fuels in advanced gas turbines, and the integration of automation, monitoring, remote capability, digital intelligence within PLC architecture (Fig 8).
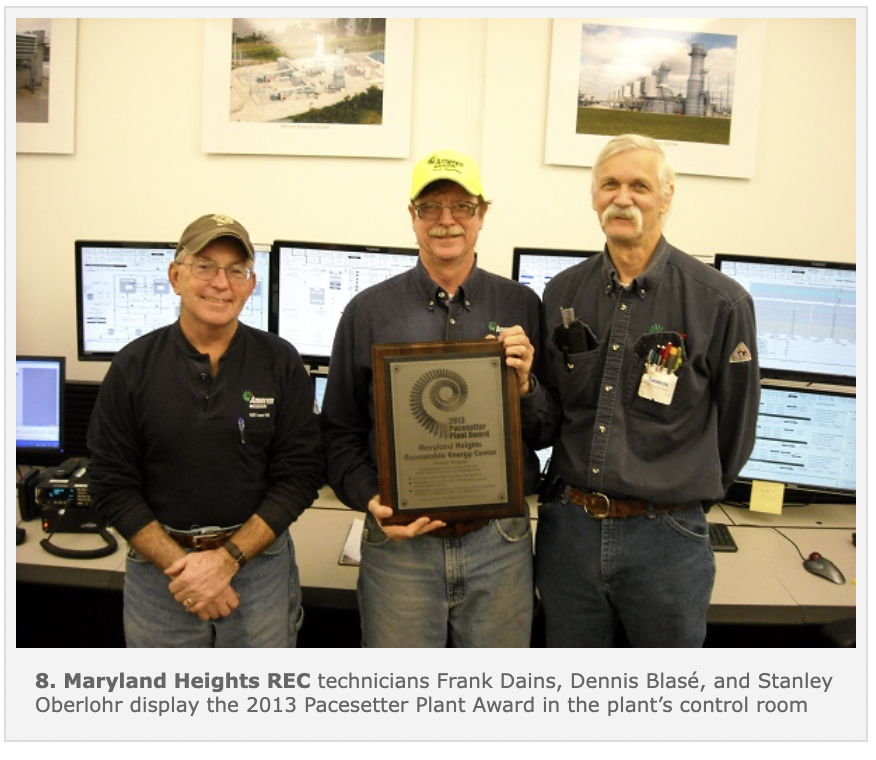
Patriot CCPP, Clinton Twp, Pa, orders two H-class gas turbines from Siemens Energy Inc. The 829-MW facility is expected to begin operation in 2016. These are the 26th and 27th H-class GTs sold by Siemens worldwide.
Lakewood Cogeneration Plant, owned by Essential Power™, commissions a Symphony Plus control upgrade supplied by ABB.