AIG tuning, catalyst for life forecasting
by TD Martz, LJ Muzio, and RA Smith, Fossil Energy Research Corp (FERCo)
Many gas-turbine “bubble” units installed between 2000 and 2004 are operating with their original charge of SCR catalyst. These units have outlived the original catalyst warranty (typically three years) and have benefitted from a combination of conservative design and good luck.
However, as these systems reach the decade mark, the design margins have diminished because of gradual (and inevitable) deactivation of the catalyst with age. As the catalyst nears its end of life, ammonia slip begins to increase exponentially. This catches many operators by surprise. They realize much too late that they are close to exceeding their ammonia slip limit and in danger of a costly forced outage.
There are practical steps operators can take to avoid this scenario, including these:
- Check and optimize the NH3/NOx distribution regularly. Improving distribution by tuning the ammonia injection grid (AIG) can reduce ammonia slip, thereby extending catalyst life.
- Forecast the life of your catalyst by regularly monitoring both its activity and ammonia slip. As the catalyst ages, the frequency of these measurements may need to increase.
- Implement a catalyst replacement plan so you are prepared to act before the slip limit is exceeded. Catalyst life forecasting is an important part of this plan. It is also helpful to clarify expectations regarding replacement-catalyst lead time, storage, and installation well in advance of placing an order.
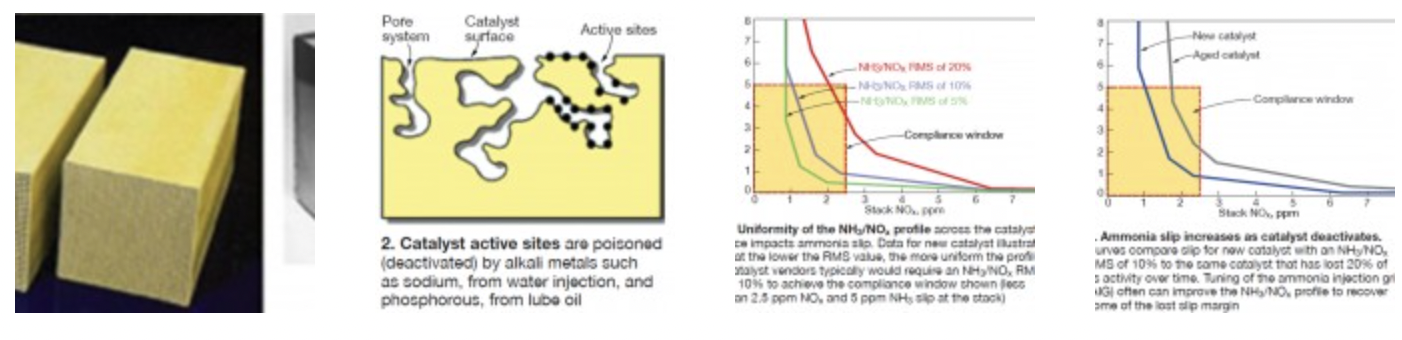
SCR fundamentals
There are two primary types of SCR catalyst used today for stationary gas-turbine (GT) applications: extruded ceramic honeycomb and corrugated mat (Fig 1). Both are homogeneous, meaning the catalytic material is distributed uniformly within the catalyst substrate material.
The catalytic material, similar in both types of catalyst, consists of vanadium pentoxide, titanium dioxide, molybdenum, and tungsten. Catalyst pitch sizes (technically speaking, cell hydraulic diameter) can be as small as 1/16 to 1/8 in. for gas-fired systems because there is no ash in the flue gas. Manufacturers of extruded ceramic honeycomb catalyst include Cormetech Inc, Ceram Environmental Inc, and Johnson Matthey plc; corrugated mat catalyst is manufactured by Haldor Topsoe A/S and Hitachi Zosen Corp.
Some early GTs came equipped with a heterogeneous “washcoat” SCR catalyst, which has a thin coat of catalyst material layered on top of extruded ceramic substrate. Washcoat catalyst by nature has less catalytic material per pound than homogeneous catalyst and is prone to premature deactivation. Most GT operators have replaced their washcoat catalyst with a homogeneous product.
Catalytic mechanism. In the presence of oxygen, the selective reaction of ammonia and NOx will happen on its own at temperatures around 1750F. This technology is called selective non-catalytic reduction of NOx, or SNCR, and is often used in fossil-fired boilers at the furnace exit to provide modest NOx reduction (20% to 30%). To promote this reaction at temperatures below 1000F, a catalyst is required; hence the term selective catalytic reduction, or SCR.
The primary SCR reactions are represented by the following equations:
- 4NH3 + 4NO + O2 ? 4N2 + 6H2O
- 6NO2 + 8NH3 ? 7N2 + 12H2O.
These reactions occur on the catalyst surface, so a large surface area is desired to minimize the catalyst volume. The substrates used for SCR catalyst have an inherent system of pores to provide the surface area required. Note that catalyst material is not consumed during the reaction. Operating the SCR system at a lower or higher NOx reduction level will not increase or decrease catalyst life. In gas-fired applications, life is determined primarily by the amount of catalyst poisons there is in the flue gas.
Deactivation. Active catalyst sites (Fig 2) are poisoned by alkali metals such as sodium (from water injection) and phosphorous (from lube oil). The rate of catalyst deactivation depends on the concentration of these poisons in the flue gas. For GT applications, the levels are low, generally resulting in deactivation rates of less than 5% per 10,000 hours of operation. This enables a new catalyst charge to perform effectively well beyond the typical three-year warranty period.
The NH3/NOx ratio is the molar ratio of the injected ammonia over the NOx at the catalyst inlet. The equations above show that the primary SCR reactions require only one mole of NH3 to remove one mole of NO, and about 1.33 moles of NH3 to remove one mole of NO2. Depending on the fraction of NO2 in the overall NOx concentration (typically about 20% for a gas turbine system), no more than about 1.1 moles of NH3 are needed per mole of NOx to make these reactions happen.
If the concentration of NH3 is higher in localized regions on the catalyst, then the excess ammonia will “slip” through the catalyst in these regions and move on to the stack. Thus the uniformity of the NH3/NOx profile across the catalyst face is critical to the SCR process.
Uniformity of the NH3/NOx profile is quantified by performing measurements on a grid of points that are on equal areas (to the extent possible). The standard deviation of the measured points is taken and normalized to the average. The result is defined as the RMS value, and is expressed as a percentage of the mean. Note that the NH3/NOx profile is more uniform at lower RMS values than at higher ones.
Fig 3 illustrates the dependence of ammonia slip on the NH3/NOx profile uniformity when 90% NOx removal is required. The FERCo SCR process simulation model was used to generate these curves for a system assuming 25 ppm NOx at the SCR inlet, 2.5 ppm NOx at the stack, and an ammonia slip limit of 5 ppm.
For a given stack NOx value, ammonia slip increases as the NH3/NOx RMS value increases. As a frame of reference, catalyst vendors typically require 10% NH3/NOx RMS for a system with these performance goals. The ammonia slip barely falls within the 5- ppm limit as the RMS approaches 20%, leaving no operational margin.
The curves in Fig 3 are based on a new catalyst charge. But what happens to these curves as the catalyst ages and deactivates? The impact of catalyst deactivation is similar to the impact of a higher NH3/NOx RMS value. Fig 4 demonstrates how the ammonia-slip margin diminishes as the catalyst deactivates by a nominal 20%. AIG tuning can improve the NH3/NOx profile, and recover lost ammonia-slip margin attributed to catalyst deactivation.
Another important consideration is the impact of the NH3/NOx distribution on the stack- NOx profile. If the NH3/NOx distribution at the catalyst inlet is stratified, the NOx profile at the catalyst outlet will be stratified as well (assuming a uniform inlet NOx profile). If the distance between the SCR catalyst outlet and the stack CEMS probe is short, this stratified NOx profile may not “mix out” and could adversely impact the CEMS RATA (Relative Accuracy Test Audit) test.
SCR optimization
Improving the NH3/NOx distribution by tuning the AIG can help reduce ammonia slip, thereby extending catalyst life. It is important to tune the AIG when a new SCR system is commissioned or when old catalyst is replaced by a new charge, to provide a benchmark for future tests. AIG tuning is also important after changes are made to the gas turbine or duct burners that may impact the SCR inlet NOx distribution.
Here are several questions you should know the answers to before planning an AIG tuning program:
- What are the adjustment options on the AIG? How many vertical adjustment zones? How many horizontal adjustment zones?
- A zone is defined as the injection area covered by one adjustment valve. In many cases, an AIG is designed with only one-dimensional adjustment capability—vertical or horizontal. Best practice: Specify an AIG with two-dimensional adjustability—vertical and horizontal.
- Was the AIG tuned when the SCR system was first commissioned? If not, was a flow model performed during the design stage to evaluate AIG performance?
This information will provide a valuable benchmark for AIG performance.
- How many access ports are available at the SCR catalyst outlet to measure a grid of points? Are they on both sides of the duct? How do the sample ports align with the AIG tuning zones?
- AIG tuning can be performed with a grid of sample points at the catalyst exit; sample points at the catalyst inlet are not required. AIG tuning is an iterative process, so accurate feedback is critical. The placement and number of measurement points at the catalyst exit depends on the placement and number of AIG adjustment zones. Ideally, the measurement points will be in the same streamline path as the upstream AIG adjustment zones. This will allow the test engineer to see changes in the catalyst outlet NOx levels resulting from AIG valve adjustments.
- Is it more cost effective to have a test contractor probe each port from a man lift or to install permanent sample probes for testing purposes?
The former method, also called the “point-by-point” approach, is a slow, labor- intensive process. For example, if a typical test grid has 50 points and it takes nominally five minutes per point to get a measurement, one test will require more than four hours.
But since AIG tuning is an iterative process, multiple tests usually are required. Thus the point-by-point approach may require having the test contractor at the plant for several days. Additionally, on large combined cycles, where the SCR duct is 35 ft wide, or more, the point-by-point approach may not even be feasible because the required sample probe would be too long to handle safely.
The preferred approach is to install a set of permanent sample probes at the catalyst outlet that can be used for tuning purposes throughout the life of the plant. The initial capital cost of installing the probes will be returned in the form of reduced test-contractor costs. The permanent probes and line extensions are typically routed down to grade level, so the contractor does not need a man lift or scaffolding.
An example of a permanent probe grid is shown in Fig 5. With this arrangement, FERCo employs a multipoint analyzer system that is able to perform a 50-point NOx traverse in less than 45 minutes. Typically, an AIG system can be tuned in less than one day.
- What considerations are necessary to measure the inlet NOx profile?
The uniformity of the NH3/NOx profile depends on the NH3 distribution as well as on the NOx distribution at the catalyst inlet. In most situations, it is safe to assume the inlet NOx profile is reasonably uniform. However, there are some arrangements—such as systems with duct burners—where the inlet NOx profile can be significantly stratified and must be measured.
This measurement can be made at the catalyst exit probes by turning off the ammonia during the first test (that is, no NOx reduction through the catalyst). However, turning off the ammonia will impact the hourly NOx average, and may require a variance from the local regulatory agency.
Fig 6 shows an example of NH3/NOx distribution results before and after AIG tuning. In this case, the AIG had only one-dimensional (vertical) adjustment capability. The vertical gradients were addressed by valve adjustments, but the horizontal (left-to-right) gradients could not be eliminated. This further illustrates that AIG design has a major impact on the ability to tune the ammonia distribution. Overall, the improvement in the profile was still significant, reducing the RMS from 22% to 13%.
Forecasting catalyst life
Catalyst life forecasting allows the SCR operator to predict and plan for the most cost-effective time to replace catalyst. Keep in mind that if catalyst is replaced too soon, money is lost in the form of wasted catalyst potential. If catalyst is replaced too late, money is lost in the form of a forced outage or fines triggered by high ammonia slip.
Monitoring catalyst activity (or deactivation) is a key component of catalyst life forecasting. Catalyst activity often is reported as a relative activity, which is the ratio of the current activity, K, to the “new” catalyst activity, K0. When catalyst is purchased, catalyst vendors are able to provide the K/K0 value at which the catalyst will no longer be effective—that is, end of life.
But it is the operator’s responsibility to monitor catalyst deactivation over time and forecast when the catalyst actually will reach end of life. Also, it is the operator’s responsibility to retain a new catalyst sample, either with the vendor or at the plant, to serve as a benchmark (K0) for comparison purposes.
To illustrate how catalyst activity data can be used to forecast catalyst life, a theoretical deactivation curve was developed using FERCo’s SCR process simulation model. Fig 7 shows an example of a system designed for 25 ppm SCR inlet NOx, 2.5 ppm stack NOx (90% NOx removal), and an ammonia slip limit of 5 ppm.
For this example, the relative activity (K/K0) at the end of catalyst life was 0.5. In other words, the 5-ppm ammonia-slip limit was reached when K/K0 decreased to 0.5. The deactivation rate for this theoretical case was 7% per 10,000 hours. At this rate, assuming 18 months were needed to get bids for new catalyst, order the catalyst, and coordinate the installation with a scheduled outage, the time to take action was when the catalyst reached K/K0 = 0.55. Important: This is a theoretical example; actual deactivation rates will vary, depending on the concentration of catalyst poisons in the flue gas.
By measuring actual activity data regularly, you can develop a similar curve for your plant’s catalyst as it ages. Your curve then can be used to forecast catalyst life based on the vendor’s end of life K/K0 value. Ammonia slip also can be used as an indicator of remaining catalyst life. But as Fig 7 indicates, this is more difficult because slip increases exponentially as the catalyst deactivates.
Monitoring catalyst activity
Catalyst activity typically is checked annually by removing a sample during an outage and sending it to a laboratory for an activity analysis. This provides only one activity data point per year, and often requires several weeks before the lab is able to provide the results. For faster and more accurate life forecasting, FERCo has developed an in-situ approach for monitoring catalyst activity called CatalysTrak™ that does not require a unit outage.
To measure K in a laboratory, the test contractor (catalyst vendor or third party) removes a sample of catalyst during an outage and tests it in a lab-scale reactor. The catalyst sample can be a complete test block designed as such by the catalyst vendor, or it can be a “core” sample which is drilled out of a catalyst block. Samples are usually obtained from the inlet side and outlet side of the catalyst bed. Obtaining multiple samples across the catalyst bed may be warranted if activity stratification is suspected.
The size of the lab reactor and the test conditions vary from vendor to vendor. As a result, it is not possible to compare the measured K value from different vendors. Rather, the relative activity, K/K0, must be used as the basis of comparison. As mentioned before, it is important to retain a new catalyst sample, either with the vendor or at the plant, to serve as a benchmark for comparison purposes.
In conducting the lab activity test, a specified volume of catalyst is exposed to a known gas flow rate. The gas can be actual or simulated flue gas at a given temperature and inlet NOx level. Ammonia is then injected at the sample inlet at a high NH3/NOx level to provide excess ammonia at the catalyst surface. The NOx reduction is measured across the catalyst sample, and the activity K is determined from a simple formula based on the NOx reduction and the flue-gas velocity through the catalyst.
In addition to an activity analysis, chemical and physical analyses can be performed on a catalyst sample to determine the cause of deactivation. For example, the accumulation of catalyst poisons such as sodium can be identified in the laboratory. Catalyst surface area, pore size distribution, and pore volume also can be checked.
Primary disadvantages of testing catalyst samples in a lab are the following:
- Samples can be obtained only during an outage.
- Turnaround time for sample analysis typically is several weeks.
For a base-load combined cycle, scheduled outages typically are conducted annually. It is difficult for an operator to develop an accurate catalyst life forecast and replacement plan based on one activity data point per year. Chances are good the operator will lose money by changing out the catalyst either too early or too late.
In-situ measurements. To improve the speed and accuracy of catalyst life forecasting, FERCo developed and patented an in-situ activity measurement method called CatalysTrak™. This method can be employed at any time while the gas turbine is operational, and does not interfere with plant operations or CEMS measurements.
Fig 8 provides a description of the CatalysTrak™ approach. Similar to the laboratory method, NOx reduction is measured across a small cross section (“test section”) of the catalyst bed. A small, supplemental AIG is permanently mounted upstream of the test section to increase the NH3/NOx level and provide excess ammonia across the catalyst test section. The activity calculation then is based on the maximum NOx removal measured across the test section.
The hardware requirements for CatalysTrak™ are simple, and can be easily installed by plant technicians in a few hours during an outage. This is a one-time installation, which is then good for the life of the plant. The activity tests also are simple, and require only a few hours to complete while the gas turbine is running at normal full-load conditions. A continuous NOx analyzer is required to perform CatalysTrak™ tests. Testing can be coordinated using a trusted local stack test contractor along with a FERCo engineer to oversee the tests and calculate the activity results.
The CatalysTrak™ method is not intended to replace laboratory catalyst activity tests. Rather, it provides operators the ability to obtain more catalyst activity data points for the purpose of forecasting catalyst life. When the catalyst is new, it may only be necessary to measure the activity annually. However, after the catalyst has aged several years, semi-annual or quarterly activity measurements may be needed.
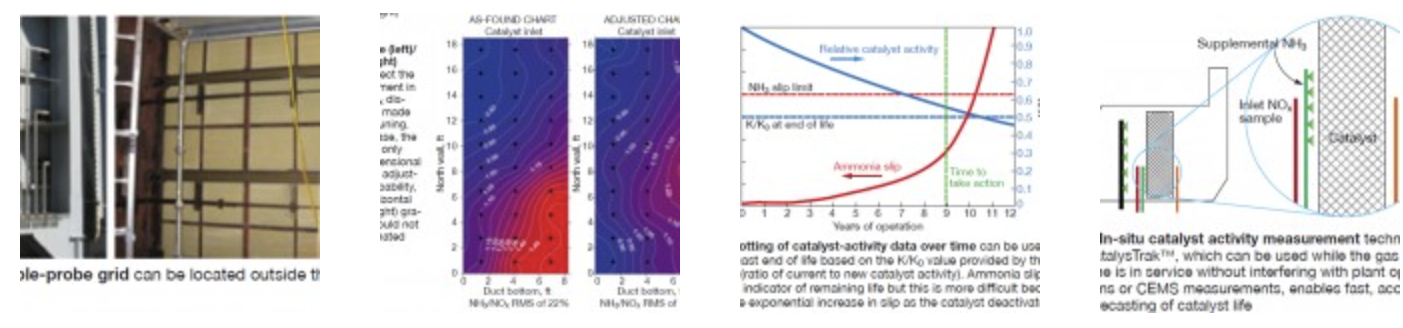
Monitoring ammonia slip. In addition measuring catalyst activity, ammonia slip can be used as an indicator of catalyst deactivation. However, the success of this approach depends on how often ammonia is measured. As catalyst deactivates over time, the corresponding increase in ammonia slip is not linear. The rate of increase in ammonia slip will jump significantly as the catalyst nears end of life. Therefore, if ammonia slip is only measured annually during the compliance test, it may not provide enough early warning that the catalyst requires replacement.
Example: Fig 7 shows the ammonia slip increased from 0 to 2.5 ppm over the first nine years of operation. However, it took less than two years to go from 2.5 to 5 ppm slip. In this case, semi-annual (or more often) ammonia measurements would be required to provide adequate warning that catalyst replacement was needed.
Ammonia-slip measurements can be performed by stack test contractors. Alternatively, tunable diode laser (TDL) ammonia analyzers are rugged and sufficiently accurate for this purpose. These continuous analyzers also can be used for system control purposes. Combining stack ammonia slip measurements with CatalysTrak™ testing on a regular basis will provide invaluable information for catalyst life forecasting.
Catalyst replacement plan
It is important for operators to develop and implement operational procedures based on the foregoing suggestions. This will ensure smooth and cost-effective catalyst replacement events throughout the life of the plant. To summarize, a list of procedures might include the following:
- Obtain from the manufacturer of your catalyst, the relative activity (K/K0) that represents the end of catalyst life.
- Put in place a methodology for tracking and accurately forecasting catalyst life—for example, laboratory activity, CatalysTrak™ in-situ, and ammonia-slip measurements. Perform AIG tuning to maximize catalyst life.
- Negotiate new or regenerated catalyst pricing, delivery, storage, and old catalyst disposal well in advance of placing the order.
- Consider if the AIG, catalyst housing, and/or seals require upgrade or modification when the catalyst is replaced.
- Obtain a sample of the new catalyst before it is installed and test for activity. This will be the basis of future K/K0 tests. CCJ