Demin-water recirc mod yields big savings
Mill Creek Combustion Turbine Station
Duke Energy Corp
640-MW, dual-fuel, simple-cycle peaking facility located in Blacksburg, SC
Plant manager: Randy Spencer
Key project participants: Joe Costello, CT tech III, lead chemistry technician Kristi McCall, fleet engineer
Challenge.
Raw water for the plant’s eight GE 7EA gas turbines is purchased from the city and stored in the large makeup water tank shown in Fig 90. First processing step is RO, then deionization. Storage of product water is in the demin tank behind the makeup tank in the photo. Makeup water is inherently dirty and RO-system prefilters and membranes are susceptible to rapid clogging and require frequent replacement.
Demineralized water is used only when the units are firing oil, which is infrequently. Thus demin water typically sits in the tanks for long periods with no circulation or usage. The organisms that thrive in the stagnant water can cause rapid clogging of the unit filters critical to unit operation when burning oil. Clogging can be detrimental to starting reliability and availability.
Solution.
Plant personnel determined that circulating water from the demin tanks back through the RO system would be of great benefit. After planning and siting the project, excavation to access and modify the existing piping system began. The supply line from the makeup tank to the RO system and the supply line from demin tanks to the turbines were tied together, and a valve placed between the two (Figs 91, 92).
A check valve was placed upstream of the tie on the demin-to-GT line, to prevent contaminating the water in the demineralized tanks. A valve was already in place on the makeup-to-RO line, upstream of the tie. With this one tie, it was made possible to pull from the demineralized tanks, cross into the makeup water line, supply the RO, and then discharge the newly circulated and cleaned water back into the demin tanks.
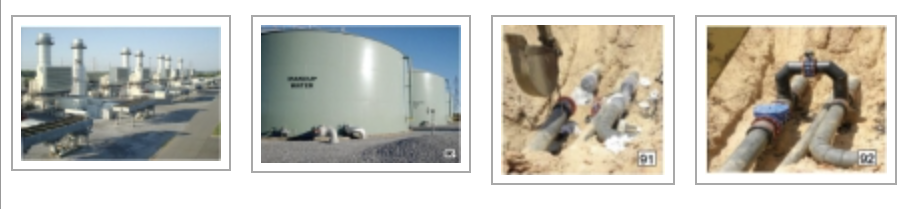
Results.
With the recirculation option, demineralized water is the primary water going through the RO system. This helps keep the water in the tanks from stagnating and prevents clogging of unit filters. Additionally, since clean water is now primarily used in the RO system, the membranes and prefilters will remain clean and last longer.
This modification dramatically reduces the costs of annual filter and membrane replacement as well as increasing unit starting reliability and availability. It also reduces the amount of water purchased from the city for makeup.
From 2008 to 2010, we replaced over 570 prefilters in the RO system at a cost of more than $25,750. We expect that recirculation will reduce the need to replace the prefilters in the RO by 90%. The cost for a full replacement of the membranes in the RO system is around $119,000. By using demineralized water in the RO, we expect the life of the membranes to nearly double. Over a 10-yr period, this would save almost $60,000. Finally, use of demin water in the RO system dramatically reduces the need for, and cost of, makeup water.