Expansion joint failure mitigation
Wolf Hollow 1
Owned by Stark Investments, Managed by Insight Energy LLC
Operated by NAES Corp
730-MW, gas-fired, two-unit, 1 × 1combined cycle located in Granbury, TX
Plant manager: Kelly Fleetwood
Key project participants: Adam Jackson, plant engineer; Shane Maples, maintenance supervisor; Ryan Sachetti, project engineer, Industrial Air Flow Dynamics Inc
Challenge.
Maintaining the integrity of expansion joints between the gas turbine and heat-recovery steam generator (HRSG) at plants powered by G-class engines has been an industry-wide challenge. Expansion-joint failures have adversely impacted the reliability, availability, and profitabilityof these plants—particularly those cycling daily. In addition to the expense associated with availability loss, expansion joints—ranging in size from 15 to 23ft in diameter—can cost thousands of dollars to repair and upwards of a million, or more, to replace (Fig 82).
Actual repair and replacement costs depend on the nature of the failure, required work, and market conditions. Some of the issues experienced at Wolf Hollow I, which averages over 200 start/stop cycles annually, include the following:
- Failure of metal mesh designed to retain the layers of insulation within the expansion joint.
- Failure and/or liberation of liner plates installed to cover the space on the exhaust-gas side of the joint between sections of exhaust ductwork. These failures result in insulation being pulled into the exhaust stream and fouling the SCR catalyst. Such fouling can limit unit output because of increased turbine back pressure and/or reduced catalyst performance; in the extreme, a unit trip is possible.
- Failure of the weld joining the exhaust duct and expansion-joint frame, resulting in leakage of hot gas which causes efficiency loss and may damage electrical conduit, wiring, and/or instrumentation. Personnel safety is another concern.
- Failure of the outer “belt” covering of the joint as a result of insulation loss within the expansion joint and/or compression/tension fatigue stresses, both allowing leakage of hot gas and contributing to the issues described in the previous bullet point.
Historically, the plant had operated only 60 to 90 days between repairs to one or more of its six expansion joints (three per unit). Repairs ranged from installing a “patch” on the outer belt to complete joint replacement. The financial impact to Wolf Hollow has been significant; repair/replacement costs have exceeded $5 million since first commercial operation in 2003.
Solution.
Wolf Hollow performed detailed failure analyses for its expansion joints—including failure mechanisms, failure rates, collateral damage, repairs, and cost impact. The first expansion joint immediately downstream of the turbine case (EE00) was the worst in terms of repair frequency and cost, followed by the third joint (EE02) located between the transition from the cylindrical exhaust duct to the rectangular entrance to the HRSG. The second joint (EE01) had the most favorable frequency-of-repair record.
Review revealed EE00 was part of the turbine supplier’s scope of supply and Wolf Hollow engaged the OEM to support a detailed evaluation of the failures, determine the causes of the failures, and recommend options to prevent failures in the future.
The plant also elected to partner with Industrial Air Flow Dynamics Inc, Glastonbury, Conn, to perform an independent analysis of each of the three expansion joints. This decision was based on IAFD’s (1) commitment to gather actual operating data, (2) its willingness to conduct a comprehensive historical review of events at Wolf Hollow and other facilities IAFD had performed work for, (3) design capabilities, and (4) commitment to customer needs.
The failure mechanism for the EE00 joint was insufficient clearance (gap) between the faces of the expansion-joint frame (Fig 83). The clearance provided did not allow the outer belt to flex within design tolerances. The clearance varies as the unit cycles because of the thermal growth/contraction of the exhaust duct. The stiffness of the outer belt is determined by design requirements and materials necessary to meet the operating conditions. When the outer belt is compressed or stretched beyond its material limits, the belt material breaks down and failure occurs.
Once there is a flow path for exhaust gas, the rate of belt deterioration increases because of the extreme heat and the material becomes brittle. Frequent cycling exacerbates the problem. Contact with high-temperature gas also causes the insulation to crystallize. The resulting powder is entrained in the exhaust flow and deposited on the catalyst surface.
Proposals to correct problem were received from two vendors. Both specified changes to the frame and joint materials to eliminate the failure mechanism and allow high-cycle operation. Each proposal included modifications to increase the clearance between the frame faces. One vendor proposed complete replacement of the frame and improvements in the insulation and wire mesh within the joint. Frame replacement would also require reducing the length of the exhaust duct between the EE00 and EE01 expansion joints.
The estimated cost and outage duration to implement this proposed modification was $1.5-2.2 million and 30 days. This proposal was not accepted. The second vendor proposed modifying the existing frame to achieve the necessary outer belt width and making improvements in the insulation and wire mesh within the joint (Fig 84). The estimated cost to implement was between $150,000 and$175,000; outage time, between three and five days.
The failure mechanism for the EE01 joint was insufficient structural support of the frame’s flange at the frame-to-duct interface (Fig 85). During operation, as the duct sections expanded/contracted and moved differentially, the stiffness of the outer belt material caused the flange to flex and the weld connecting the joint frame to the exhaust duct to fail. A secondary failure mechanism: The outer belt material was not adequate for the operating conditions in this location because of the exhaust duct design.
The proposed modification included (1) addition of gussets to increase the structural strength of the joint frame and flange, thereby preventing flexing at the duct-to-frame weld (Fig 86); (2) replacement of the outer belt with one fabricated from a material suited for the operating conditions; (3) improvements in insulation and wire mesh within the joint similar to those proposed for EE00. The estimated cost and outage duration to implement was $90,000 to $105,000 and three to four days.
The primary failure mechanism for the EE02 joint was insufficient outer belt width (Fig 87). The actual thermal growth of the duct causes the flange face-to-face clearance to increase at the 12 o’clock position and decrease at 6 o’clock. This resulted in the outer belt being stretched and pulling free from the frame, thereby creating an exhaust-gas flow path. In addition, the internal liner plates covering the gap on the exhaust-gas side of the expansion joint were not sufficiently long in the axial direction to cover the gap throughout the range of thermal expansion.
A new frame to include modified and additional pins to attach a liner plate of new design was proposed (Fig 88). The proposal also recommended an increase in outer belt width to accommodate the actual duct movement, as well as improvements to the insulation and wire mesh within the joint (Fig 89). The estimated cost and outage duration to implement was $90,000 to $105,000 and six to seven days.
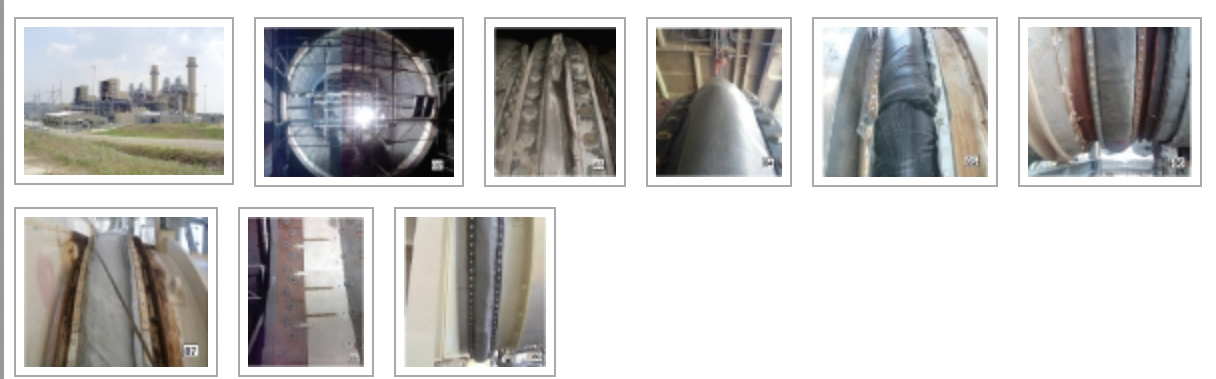
Results.
Wolf Hollow implemented the proposal for the EE02 expansion joints and completed this installation on both units in November 2009. In January 2010, Unit 2 experienced a failure of the liner plate at the 12 o’clock position. The failure was reviewed and the design of the liner plate was modified.
In April 2010, the new liner plates were installed on both units. As of the end of November 2010, there had been no further issues with the EE02 expansion joints. Each unit recorded 195 cycles between EE02 installation in November 2009 and the end of November 2010. Wolf Hollow implemented the proposals summarized above for the EE00 and EE01 in April 2010. There had been no issues with these joints between installation in April and the end of last November; there were 135 cycles on each unit during that period.
Wolf Hollow has monitored quarterly both the condition of the expansion joints via infrared thermography and the differential pressure across the catalyst. This project began in early 2009 with the goal to eliminate outages, capacity impacts, collateral damage, and reduce the costs caused by expansion-joint failures. The investment in the newly designed expansion joints is on pace to provide a return on investment in less than two years based on historical costs. The new expansion joints have not been associated with availability loss or decrease in catalyst performance since their installation.